The ECS cools the electronic equipment in the IU and the forward third stage skirt. Sixteen cold plates are installed in each stage.
An antifreeze-like coolant, 60 per cent methanol and 40 per cent water, from a reservoir within the IU is circulated through the cold plates. Heat generated by the mounted components is transferred to the coolant by means of conduction.
Prior to liftoff a preflight heat exchanger serviced by ground support equipment transfers heat from the coolant. Approximately 163 seconds after liftoff, ECS’s sublimator-heat exchanger takes over the job of temperature control.
Some of the more complex components like the guidance computer, flight control computer, and the ST-124-M platform, have coolant fluid circulated through them to provide more efficient heat removal.
In the vacuum of space the warmed coolant, after leaving the cold plates, is routed through a device called a sublimator. Water, from an IU reservoir,
Structure Segments—Prior to splicing, mounting brackets for thermal conditioning panels can be seen on interior surface of segments. The exterior of the spring-loaded umbilical door and the access door are visible at right center.
Extremely accurate theodolites, similar to a surveyor’s transit, are used to align the segments in a circle prior to splicing. Metal splicing plates join the three segments, and the holes which permit the IU to be joined to mating surfaces of the launch vehicle are drilled at top and bottom edges of the structure for ease in handling. Protective rings are bolted to these edges to stiffen the structure. Vehicle antenna holes are cut after splices are bolted.
After structure fabrication is completed, module and component assembly operations begin. Temperature transducers are fastened to the inner skin, environmental control system (ECS) cold plates are mounted, and a cable tray is bolted to the top of the
7- 2
Splice Joint Operations—Final grinding of a splice joint ensures a smooth surface prior to splice plate assembly.
SATURN V NEWS
goes to the sublimator and is exposed through a porous plate to the low temperature and pressure of outer space where it freezes, blocking the pores in the plate. The heat from the coolant, transferred to the plate, is absorbed by the ice converting it directly into water vapor (a process called sublimation).
The system is self-regulating. The rate of heat dissipation varies with the amount of heat input, speeding up or slowing down as heat is generated. If the coolant temperature falls below a pre-set level, an
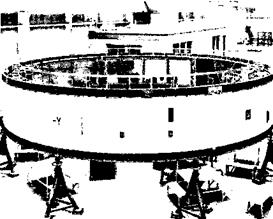
IBM-DR-19
|
Instrument Unit Assembly in IBM Manufacturing Area – Splicing operations and assembly of the tubular cable tray are complete, the cold plates have been installed, and installation of components is underway.
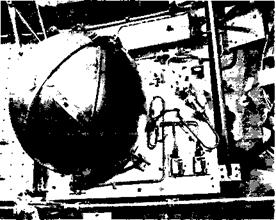
IBM-DR-21
|
Environment Control—A mobile clean room protects against contamination during assembly of environmental control system components. Gaseous nitrogen will be circulated from a ground supply through the duct partially assembled in the cable tray to purge the IU following vehicle fueling.
electronically controlled valve causes the coolant mixture to bypass the sublimator until the temperature rises sufficiently to require further cooling.
Nitrogen gas provides artificial pressure for both coolant solution and sublimator water reservoirs during orbit.
A coolant circulating pump along with the necessary valves and piping to control flow complete the environmental control equipment.
Guidance and Control
The IU’s guidance and flight control systems nav-
SATURN V NEWS
igate (determine vehicle position and velocity), guide (determine attitude correction signals), and control (determine and issue control commands to the engine actuators) the Saturn V vehicle.
Completely self-contained, these systems measure acceleration and vehicle attitude, determine velocity and position and their effect on the mission, calculate attitude correction signals, and determine
and issue control commands to the engine actuators.
All this is done to place the vehicle in a desired attitude to reach the required velocity and altitude for mission completion.
Major components are an inertial platform, the launch vehicle digital computer (LVDC), the launch vehicle data adapter (LVDA), an analog flight control computer, and control and rate gyros.
IBM-DR-4
ST-124-M Inertia! Platform System
Prior to liftoff, launch parameters go to the LVDC.
About five seconds before liftoff, the inertial guidance platform and the LVDC are released from ground control. As the vehicle ascends, the guidance platform senses and measures vehicle acceleration and attitude and sends these measurements to the LVDC via the LVDA.
The LVDC integrates these measurements with the time since launch to determine vehicle position relative to starting point and destination. It then computes the desired vehicle attitude, using data stored in its memory, and the difference between the desired attitude and the actual becomes the generated attitude correction signal.
This signal is sent to the analog flight control computer, where it is combined with information from rate gyros. Using this data, the flight control computer determines and issues the command to gimbal the engines and change the thrust direction.
Each mission has at least three phases: atmospheric – powered flight, boost period after initial entry into
7-4
REFERENCE
space, and the coasting period.
Atmospheric boost causes the greatest vehicle load because of atmospheric pressure. During this time the guidance system is primarily checking vehicle integrity and is programmed to minimize this pressure.
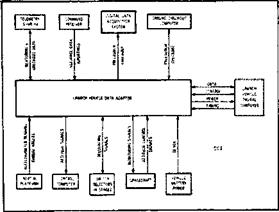
IBM-DR-6
|
Guidance and Control—The LVDC and LVDA portion of the guidance system is shown in this block diagram. The LVDC receives information from all parts of the vehicle via the LVDA, and in turn issues commands.
The vehicle maintains liftoff orientation long enough to clear the launch equipment, and then it performs a roll maneuver to get to the flight azimuth direction.
The time tilt program is applied after the roll maneuver. The pitch angle is regulated by the tilt program, and is independent of navigation measurements. However, navigation measurements and computations are performed throughout the flight, beginning at the time the platform is released (i. e., five seconds before liftoff). First stage engine cutoff and stage separation are commanded when the IU receives a signal that the tank’s fuel level has reached a predetermined point. During second stage powered flight the LVDC guides the vehicle via the best path to reach the mission objectives.
During orbit, navigation and guidance information in the LVDC can be updated by data transmission from ground stations through the IU radio command system.
Approximately once every two seconds, the LVDC, using iterative or "closed loop” guidance, figures vehicle position and vehicle conditions required at the end of powered flight (velocity, altitude, etc.) and generates the attitude correction signals to gimbal the engines so that the vehicle reaches its predetermined parking orbit.
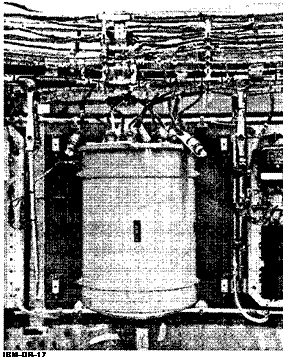
III Interior During Assembly—The large, cylindrical component simulates size and shape of the flight control computer and is used to check cable lengths and mounting arrangement.
Second stage engine cutoff comes when the IU is signaled that stage propellant has reached a predetermined level, and then the stage is separated. By this time, the vehicle has already reached its approximate orbital altitude, and the third stage burn merely gives it enough push to reach a circular parking orbit.