In January 2006, NASA Headquarters announced its restructured aeronautics mission. As explained by Associate Administrator for Aeronautics Lisa J. Porter, "NASA is returning to long-term investments
in cutting-edge fundamental research in traditional aeronautical disciplines. . . appropriate to NASA’s unique capabilities.” One of the four new program areas announced was Fundamental Aeronautics (which included supersonic research), with Rich Wlezien as acting director.[524]
During May, NASA released more details on Fundamental Aeronautics, including plans for what was called the Supersonics Project, managed by Mary Jo Long-Davis with Peter Coen as its principal investigator. One of the project’s major technical challenges was to accurately model the propagation of sonic booms from aircraft to the ground incorporating all relevant physical phenomena. These included realistic atmospheric conditions and the effects of vibrations on structures and the people inside (for which most existing research involved military firing ranges and explosives). "The research goal is to model sonic boom impact as perceived both indoors and outdoors.” Developing the propagation models would involve exploitation of existing databases and additional flight tests as necessary to validate the effects of molecular relaxation, rise time, and turbulence on the loudness of sonic booms.[525]
As the Supersonics Project evolved, it added aircraft concepts more challenging than an SSBJ to serve as longer-range targets on which to focus advanced research and technologies. These were a medium-sized (100-200 passenger) Mach 1.6—1.8 supersonic airliner that could have an acceptable sonic boom by about 2020 and an efficient multi-Mach aircraft that might have an acceptably low boom when flying at a speed somewhat below Mach 2 by the years 2030—2035. NASA awarded advanced concept studies for these in October 2008.[526] NASA
also began working with Japan’s Aerospace Exploration Agency (JAXA) on supersonic research, including sonic boom modeling.[527] Although NASA was not ready as yet to develop a new low-boom supersonic research airplane, it supported an application by Gulfstream to the Air Force that reserved the designation X-54A just in case this would be done in the future.[528]
Meanwhile, existing aircraft had continued to prove their value for sonic boom research. During 2005, the Dryden Center began applying a creative new flight technique called low-boom/no-boom to produce controlled booms. Ed Haering used PCBoom4 modeling in developing this concept, which Jim Smolka then refined into a fly- able maneuver with flight tests over an extensive array of pressure sensors and microphones. The new technique allowed F-18s to generate shaped ("low boom”) signatures as well as the evanescent sound waves ("no-boom”) that remain after the refraction and absorption of shock waves generated allow Mach speeds (known as the Mach cutoff) before they reach the surface.
The basic low-boom/no-boom technique requires cruising just below Mach 1 at about 50,000 feet, rolling into an inverted position, diving at a 53-degree angle, keeping the aircraft’s speed at Mach 1.1 during a portion of the dive, and pulling out to recover at about 32,000 feet. This flight profile took advantage of four attributes that contribute to reduced overpressures: a long propagation distance (the relatively high altitude of the dive), the weaker shock waves generated from the top of an aircraft (by diving while upside down), low airframe weight and volume (the relatively small size of an F-18), and a low Mach number. This technique allowed Dryden’s F-18s, which normally generate overpressures of 1.5 psf in level flight, to produce overpressures under 0.1 psf. Using these maneuvers, Dryden’s skilled test pilots could precisely place these focused quiet booms on specific locations, such as those with observers and sensors. Not only were the overpressures low, they had a slower rise time than the typical N-shaped sonic
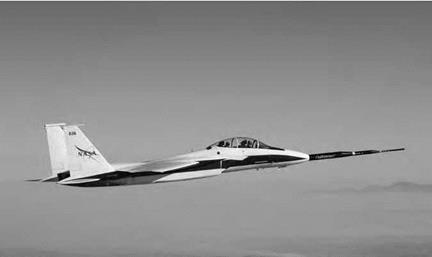
|

NASA F-15B No. 836 in flight with Quiet Spike, September 2006. NASA.
|
signature. The technique also resulted in systematic recordings of evanescent waves—the kind that sound merely like distant thunder.[529]
Dryden researchers used this technique in July 2007 during a test called House Variable Intensity Boom Effect on Structures (House VIBES). Following up on a similar test from the year before with an old (early 1960s) Edwards AFB house slated for demolition,[530] Langley engineers installed 112 sensors (a mix of accelerometers and microphones) inside the unoccupied half of a modern (late 1990s) duplex house. Other sensors were placed outside the house and on a nearby 35-foot tower. These measured pressures and vibrations from 12 normal intensity N-shaped booms (up to 2.2 psf) created by F-18s in steady and level flight at Mach 1.25 and 32,000 feet as well as 31 shaped booms (registering only 0.1 to 0.7 psf) from F-18s using the Low Boom/No Boom flight profile. The latter booms were similar to those that would
be expected from an acceptable supersonic business jet. The specially instrumented F-15B No. 852 performed six flights, and an F-18A did one flight. Above the surface boundary layer, an instrumented L-23 sailplane from the Air Force Test Pilot School recorded shock waves at precise locations in the path of the focused booms to account for atmospheric effects. The data from the house sensors confirmed fewer vibrations and noise levels in the modern house than had been the case with the older house. At the same time, data gathered by the outdoor sensors added greatly to NASA’s variable intensity sonic boom database, which was expected to help program and validate sonic boom propagation codes for years to come, including more advanced three-dimensional versions of PCBoom.[531]
With the awakening of interest in an SSBJ, NASA Langley acoustics specialists including Brenda Sullivan and Kevin Shepherd had resumed an active program of studies and experiments on human and structural response to sonic booms. They upgraded the HSR-era simulator booth with an improved computer-controlled playback system, new loudspeakers, and other equipment to more accurately replicate the sound of various boom signatures, such as those recorded at Edwards. In 2005, they also added predicted boom shapes from several low-boom aircraft designs.[532] At the same time, Gulfstream created a new mobile sonic boom simulator to help demonstrate the difference between traditional and shaped sonic booms to a wider audience. Although Gulfstream’s folded horn design could not reproduce the very low frequencies of Langley’s simulator booth, it created a "traveling” pressure wave that moved past the listener and resonated with postboom noises, features that were judged more realistic than other simulators.
Under the aegis of the Supersonics Project, plans for additional simulation capabilities accelerated. Based on multiple studies that had long cited the more bothersome effects of booms experienced indoors, the
Langley Center began in the summer of 2008 to build one of the most sophisticated sonic boom simulation systems yet. Scheduled for completion in early 2009, it would consist of a carefully constructed 12- by 14-foot room with sound and pressure systems that would replicate all the noises and vibrations caused by various levels and types of sonic booms.[533] Such studies would be vital if most concepts for supersonic business jets were ever to be realized. When the FAA updated its policy on supersonic noise certification in October 2008, it acknowledged the promising results of recent experiments but cautioned that any future changes in the rules against supersonic flight would still depend on public acceptance.[534]
NASA’s Supersonics Project also put a new flight test on its agenda: the Lift and Nozzle Change Effects on Tail Shocks (LaNCETS). Both the SSBD and Quiet Spike experiments had only involved shock waves from the front of an aircraft. Yet shocks from the rear of an aircraft as well as jet engine exhaust plumes also contribute to sonic booms—especially the recompression phase of the typical N-wave signature—but have long been more difficult to control. NASA initiated the LaNCETS experiment to address this issue. As described in the Supersonic Project’s original planning document, one of the metrics for LaNCETS was to "investigate control of aft shock structure using nozzle and/or lift tailoring with the goal of a 20% reduction in near-field tail shock strength.”[535]
NASA Dryden had just the airplane with which to do this: F-15B No. 837. Originally built in 1973 as the Air Force’s first preproduction TF-15A two-seat trainer (soon redesignated as the F-15B), it had been extensively modified for various experiments over its long lifespan. These included the Short Takeoff and Landing Maneuvering Technology Demonstration, the High-Stability Engine Control project, the Advanced Control Technology for Integrated Vehicles Experiment (ACTIVE),
and Intelligent Flight Control Systems (IFCS). F-15B No. 837 had the following special features: digital fly-by-wire controls, canards ahead of the wings for changing longitudinal lift distribution, and thrust-vectoring variable area ratio nozzles on its twin jet engines that could (1) constrict and expand to change the shape the exhaust plumes and (2) change the pitch and yaw of the exhaust flow.[536] It was planned to use these capabilities for validating computational tools developed at Langley, Ames, and Dryden to predict the interactions between shocks from the tail and exhaust under various lift and plume conditions.
Tim Moes, one of the Supersonics Project’s associate managers, was the LaNCETS project manager at the Dryden Center. Jim Smolka, who had flown most of F-15B No. 837’s previous missions at Dryden, was its test pilot. He and Nils Larson in F-15B No. 836 conducted Phase I of the test program with three missions from June 17-19, 2008. They gathered baseline measurements with 29 probes, all at 40,000 feet and speeds of Mach 1.2, 1.4, and 1.6.[537]
Several months before Phase II of LaNCETS, NASA specialists and affiliated researchers in the Supersonics Project announced significant progress in near-field simulation tools using the latest in computational fluid dynamics. They even reported having success as far out as 10 body lengths (a mid-field distance). As seven of these researchers claimed in August 2008, "[It] is reasonable to expect the expeditious development of an efficient sonic boom prediction methodology that will eventually become compatible with an optimization environment.”[538] Of course, more data from flight-testing would increase the likelihood of this prediction.
LaNCETS Phase II began on November 24, 2008, with nine missions flown by December 11. After being interrupted by a freak snowstorm during the third week of December and then having to break for the holiday season, the LaNCETS team completed the project with flight
tests on January 12, 15, and 30, 2009. In all, Jim Smolka flew 13 missions in F-15B No. 837, 11 of which included in-flight shock wave measurements by No. 836 from distances of 100 to 500 feet. Nils Larson piloted the probing flights, with Jason Cudnik or Carrie Rhoades in the back seat. The aircrews tested the effects of both positive and negative canard trim at Mach 1.2, 1.4, and 1.6 as well as thrust vectoring at Mach 1.2 and 1.4. They also gathered supersonic data on plume effects with different nozzle areas and exit pressure ratios. Once again, GPS equipment recorded the exact locations of the two aircraft for each of the datasets. On January 30, 2009, with Jim Smolka at the controls for the last time, No. 837 made a final flight before its well-earned retirement.[539]
The large amount of data collected will be made available to industry and academia, in addition to NASA researchers at Langley, Ames, and Dryden. For the first time, analysts and engineers will be able to use actual flight test results to validate and improve CFD models on tail shocks and exhaust plumes—taking another step toward the design of a truly low-boom supersonic airplane.[540]