Another major part of the shuttle propulsion system was the external tank (ET), the only major nonreusable portion of the launch vehicle. It was the largest (and, when loaded, the heaviest part of the Space Shuttle), at about 154 feet in length and 27.5 feet in diameter. NASA issued a request for proposals for design and construction to Chrysler, McDonnell Douglas, Boeing, and Martin Marietta on April 2, 1973. All four bidders submitted their proposals on May 17. The source selection board gave the highest technical ratings to 214 Martin Marietta and McDonnell Douglas. Martin argued that it Chapter 5 alone among the bidders had relevant experience, with the Titan III core vehicle being situated between two large solid-rocket motors. Martin’s costs were by far the lowest of the four, although the board recognized that it was bidding below true expected costs—“buying in" as it was called. But as NASA deputy administrator George Low said, “We nevertheless strongly felt that in the end Martin Marietta costs would, indeed, be lower than those of any of the other contenders." Consequently, on August 16, 1973, NASA selected Martin Marietta (Denver Division) to negotiate a contract for the design, development, and testing of the external tank, a selection that, this time, the other competitors did not protest. NASA required assembly of the structure at the Marshall-managed Michoud facility near New Orleans.92
The external tank seemed to some to pose few technological demands. James Kingsbury, head of Marshall’s Science and Engineering Directorate, stated, “There was nothing really challenging technologically in the Tank. . . . The challenge was to drive down the cost." Similarly, Larry Mulloy, who was Marshall’s project manager for the solid-rocket booster but also worked on the tank, stated, “There was no technological challenge in the building of the External Tank. The only challenge was building it to sustain the very large loads that it has to carry, and the thermal environment that it is exposed to during ascent" and do so within a weight limit of about 75,000 pounds. As it turned out, however, there was in fact
a major challenge, only fully appreciated after loss of Space Shuttle Columbia on February 1, 2003, to a “breach in the Thermal Protection System on the leading edge of the left wing" resulting from its being struck by “a piece of insulating foam" from an area of the external tank known as the bipod ramp. During reentry into the atmosphere, this breach allowed aerodynamic superheating of the wing’s aluminum structure, melting, and the subsequent breakup of the orbiter under increasing aerodynamic forces.93
The external tank had to carry the cryogenic liquid-hydrogen and liquid-oxygen propellants for the three shuttle main engines. It also served as the “structural backbone" for the shuttle stack and had to withstand substantial heating as the shuttle accelerated to supersonic speeds through the lower atmosphere, where dynamic pressures were high. This heating was much more complex than on a launch vehicle like the Saturn V. At the top, the tank needed only to withstand the effects of high-speed airflow. But further down, the tank’s insulation had to encounter complex shock waves as it passed through the transonic speed range (roughly Mach 0.8 to 1.2). As the airflow became supersonic, shock waves came from the nose of the orbiter, the boosters, and the structural attachments connecting the tank, boosters, and orbiter. As the waves impinged on the sides of the external tank, they created heating rates up to 40 British thermal units per square foot per second. This was much smaller than the heating of a nose cone reentering the atmosphere, but it was substantial for the thin aluminum sheeting of which the external tank was formed to reduce weight.94
As designers examined the requirements for the external tank, they found that not even the arrangement of the hydrogen and oxygen tanks involved a simple application of lessons from the Centaur and Saturn. In both, the liquid-hydrogen tank was above the liquid – oxygen tank. Since liquid oxygen was 6 times as heavy as liquid hydrogen, this arrangement made it unnecessary to strengthen the hydrogen tank to support the heavier oxygen during liftoff. Also, with the lighter hydrogen on top, the inertial forces necessary to change the attitude of the vehicle were lower than would have been the case had the reverse arrangement prevailed. For the shuttle, however, the engines were not directly under the tanks, as was the case for the Saturn upper stages and Centaur. Instead, they were off to one side. With the heavy oxygen tank on the bottom of the external tank, its weight would have created an inertial force difficult to overcome by gimballing of the SSMEs and the SRB nozzles. Especially after the separation of the solid boosters, the weight of the oxygen tank would have tended to cause the orbiter to spin around
FIG. 5.5
Technical drawing of the Space Shuttle vehicle showing its component parts, including the external tank. (Photo courtesy of NASA)
|
|
|
 |
|
 |
 |
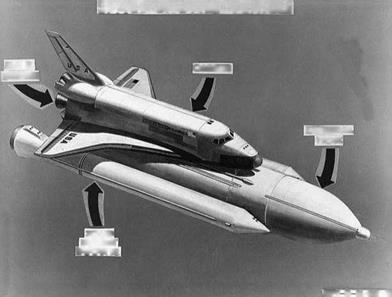

MS F C 7F> SA 4106—2C
the tank’s center of gravity. Placing the oxygen tank on top moved the shuttle stack’s center of gravity well forward, making steering much more feasible. But it also forced designers to make the liquid – hydrogen tank (and also an intertank structure between it and the oxygen tank) much sturdier than had been necessary on the Saturn upper stages.95
This, in turn, compounded a problem with the ET’s weight. The initial empty weight allowance had been 78,000 pounds, but in 1974, the Johnson Space Center in Houston (renamed from the Manned Spacecraft Center in 1973) reduced the goal to 75,000 pounds. Moreover, NASA asked Martin Marietta if it could not only reduce the weight but do so at no additional cost. In fact, the space agency suggested that it would be helpful actually to reduce the cost. Even though Marshall lowered the safety factor for the ET, the initial tank used on shuttle flights 1-5 and 7 weighed some 77,100 pounds. But through concerted efforts, Martin Marietta was able to achieve a 10,300-pound weight reduction for the lightweight tanks first used on flight 6 of the shuttle. The firm attained the weight reduction through a variety of design changes, including eliminating some portions of longitudinal structural stiffeners in the hydrogen tank, using fewer circumferential stiffeners, milling some portions of the tank to a lower thickness, using a different type of aluminum that was stronger and thus allowed thinner sections, and redesigning anti-slosh baffling.96
The resultant external tank included a liquid-hydrogen tank that constituted 96.66 feet of the ET’s roughly 154 feet in length. It had semi-monocoque design with fusion-welded barrel sections, forward and aft domes, and five ring frames. It operated at a pressure range of 32 to 34 pounds per square inch and contained an anti-vortex baffle but no elaborate anti-slosh baffles, because the lightness of the liquid hydrogen made its sloshing less significant than that of liquid oxygen. The feed line from the tank allowed a maximum flow rate of 48,724 gallons per minute from its 385,265- gallon (237,641-pound) capacity. The intertank structure was much shorter at 22.5 feet. Made of both steel and aluminum, it, too, was semi-monocoque in structure with a thrust beam, skin, stringers, and panels. It contained instrumentation and a device called an umbilical plate for supply of purge gas, detection of hazardous gas escaping from the tanks, and boil-off of hydrogen gas while on the ground. The intertank also had a purge system that removed the highly combustible propellants if they escaped from their tanks or plumbing fixtures.
Above the intertank was the liquid-oxygen tank. Its 49.33 feet of length, combined with those of the intertank and the liquid – hydrogen tank, exceeded the total length of the ET because it and its liquid-hydrogen counterpart extended into the intertank. The liquid-oxygen tank was an aluminum monocoque structure operating with a pressure range of 20-22 pounds per square inch. It allowed a maximum of 2,787 pounds (19,017 gallons) of liquid oxygen to flow to the main engines when they were operating at 104 percent of their rated thrust. Containing both anti-slosh and antivortex mechanisms, the tank had a capacity of 143,351 gallons, or 1,391,936 pounds, of oxidizer.97
The thermal-protection system for the external tank had to withstand the complex aerodynamic heating generated by the shuttle structure and keep the cryogenic propellants from boiling. The tank was coated with an inch of foam similar to that used on the Saturn S-II. Unlike the S-II insulation, however, which had to protect only against boil-off and not against the formation of ice on the foam from the liquid hydrogen and the liquid oxygen, that on the ET could not permit ice formation, because if ice came off the tank during launch, it could easily damage the critical and delicate thermal-protection system on the orbiter. Thus, the external tank’s insulation had to be thicker than that on the S-II. It was in fact so effective that despite the extreme temperatures inside the tanks, the surface of the insulation felt “only slightly cool to the touch." For the first two shuttle flights, there was a white, fire-retardant
latex coating on top of the foam, but thereafter, following testing to determine that the foam alone provided sufficient protection during ascent, the shuttle team dispensed with this coating, saving 595 pounds and leaving the orange foam to add its distinctive color to the white of the orbiter and solid-rocket boosters at launch.98
Like the main engines, the external tank underwent extensive testing before the first shuttle launch. The entire propulsion system was, of course, designed under Marshall oversight, with Center Director Lucas continuing von Braun’s practice of using weekly notes for overall communication and systems engineering. In view of this, the Columbia Accident Investigation Board was perhaps unfairly critical in 2003 when it wrote:
In the 1970s, engineers often developed particular facets of a design (structural, thermal, and so on) one after another and in relative isolation from other engineers working on different facets. Today, engineers usually work together on all aspects of a design as an integrated team. The bipod fitting [in the area where foam separated on 218 Columbia’s last flight] was designed from a structural standpoint,
Chapter 5 and the application process for foam (to prevent ice formation) and
Super Lightweight Ablator (to protect from high heating) were developed separately.
However, the board went on to note in all fairness:
It was—and still is—impossible to conduct a ground-based, simultaneous, full-scale simulation of the combination of loads, airflows, temperatures, pressures, vibration, and acoustics the External Tank experiences during launch and ascent. Therefore, the qualification testing did not truly reflect the combination of factors the bipod would experience during flight. Engineers and designers used the best methods available at the time: test the bipod and foam under as many severe combinations as could be simulated and then interpolate the results. Various analyses determined stresses, thermal gradients, air loads, and other conditions that could not be obtained through testing.99
Design requirements specified that the Space Shuttle system not shed any debris, but on the first shuttle flight, the external tank produced a shower of particles, causing engineers to say they would have been hard-pressed to clear Columbia for flight if they had known this would happen. When the bipod ramp lost foam on shuttle flight 7, wind-tunnel testing showed that the ramp area was
designed with an aerodynamically too steep angle, and designers changed the ramp angle from 45 degrees to a shallower 22 to 30 degrees. However, this and a later “slight modification to the ramp impingement profile" failed to prevent the destruction of Space Shuttle Columbia on February 1, 2003. It is beyond the scope of this history to discuss the Columbia accident further, but despite advances in analytical capabilities until 2003, the board was unable to pinpoint the “precise reasons why the left bipod foam ramp was lost."100
This was so even though the board included a staff of more than 120 people aided by about 400 NASA engineers in a lengthy and extensive investigation lasting months. The reasons a definitive explanation was impossible included the fact that foam did not “have the same properties in all directions" or the “same composition at every point." It was “extremely difficult to model analytically or to characterize physically. . . in even relatively static conditions, much less during the launch and ascent of the Shuttle." Factors that may have caused the foam to separate and damage the wing included “aerodynamic loads, thermal and vacuum effects, vibrations, stress in the External Tank structure, and myriad other conditions" including “wind shear, associated Solid Rocket Booster and Space Shuttle Main Engine responses, and liquid oxygen sloshing in the External Tank." Even in 2003, “Non-destructive evaluation techniques for determining External Tank foam strength have not been perfected or qualified." 101
With statements such as, “In our view, the NASA organizational culture had as much to do with this accident as the foam," the accident investigation board clearly implicated more than technology in the causes of the Columbia accident. But a major cause was NASA and contractor engineers’ failure to understand the reasons for and full implications of foam shedding from the external tank. As well-known space commentator John Pike said, “The more they study the foam, the less they understand it." And as a newspaper article stated, “Getting every ounce of the foam to stick to the external tank has bedeviled NASA engineers for 22 years. . . . Why foam falls off any area of the tank remains a scientific mystery." In the more sober language of the CAIB report, “Although engineers have made numerous changes in foam design and application in the 25 years the External Tank has been in production, the problem of foam-shedding has not been solved." 102
Whatever the larger causes of the accident, from the perspective of this book, this was but one more instance in which engineers did not have the design, development, and operation of rockets “down
to a science." Despite countless billions of dollars spent on researching, developing, and operating a large number of missiles and rockets; despite a great deal of effort on NASA’s and contractors’ parts to understand and correct this particular problem, there were aspects of rocketry (including this one) that eluded the understanding of engineers and even scientists such as investigation board member Douglas D. Osheroff, a Nobel Prize-winning physicist from Stanford University. Osheroff had conducted some simple experiments with foam that helped him understand the “basic physical properties of the foam itself" but also demonstrated “the difficulty of understanding why foam falls off the external tank." As he said, “Attempts to understand [the] complex behavior and failure modes" of the components of the shuttle stack were “hampered by their strong interactions with other systems in the stack."103