n October 6, 1973, a terrorist’s bomb shattered the solemn spiritual calm of Yom Kippur. the most sacred of holy days on the Hebrew calendar. A grenade, thrown by someone whom American newspapers referred to as an “Arab guerilla," wounded a soldier and two policemen in Israeli-occupied Gaza City.[32] This was the opening salvo of a massive. coordinated surprise attack on Israel by Egypt and Syria, whose forces crossed the Suez Canal in retaliation for the loss of their land in the Sinai and the Golan I leights during 1967’s Six Day War. Israel quickly mobilized for war. Prime Minister Golda Meir proclaimed the attack an “act of madness.” Her Defense Minister. Moshe Dayan, spoke in starker terms, calling for "all out war" and with a promise that “We will annihilate them."2
Meanwhile, Israel observed this holiest of days as a nation; its citizens spent the day fasting and praying, not listening to the radio or reading newspapers. Many had no idea the attack had occurred until they gathered for Yom Kippur services later that evening. At synagogues throughout the country, rabbis read aloud the names of those being summoned immediately to fight. In one crowded synagogue, a reservist soldier stood as his name was read, and as he turned to leave, his weeping father held him in a tight embrace, refusing to let him go. The rabbi intervened, saying, “His place is not here today.” The rabbi blessed the soldier as his father released him. The Yom Kippur War (or as some called it the October War) had begun.
Over the next 3 weeks, the world witnessed combat whose intensity rivaled that of World War II. With Americans helping to arm Israel and the Soviet Union stockpiling weapons in the Arab nations, some speculated that the next world war was imminent. This did not happen, but the events
of that day affected the lives of all Americans, because of a devastating economic—not military — weapon. The Arab nations retaliated against the West with an oil embargo, dramatically raising the price of oil and reducing the supply. It revealed a significant weakness of the United States, one that demonstrated how closely its economy was aligned with the accessibility of oil. Many believe this 1973 confrontation to be the genesis of the 1970s energy crisis. Although it played a major role, the crisis was actually rooted in earlier events.
The New York Times first used of the term “energy crisis’” in relationship to the United States in 1971. In a three-part series titled “Nation’s Energy Crisis,” reporter John Noble Wilford recounted the effects of a Faustian bargain reaching back to the dawn of the Industrial Revolution. Dr. Faust, of German legend, was an astrologer and alchemist who sought forbidden knowledge and ultimately sold his soul to the devil. Mephistopheles, to attain it. The story has been used as a symbol for Western civilization’s constant pursuit of power and knowledge.’ Wilford used it to describe America’s situation in 1971. Symbolically, the 19 century’s bucolic environment was sacrificed for “modern man to command. . . and to harness in the Saturn 5 moon rocket the power of 900,000 horses.”[33] [34] This energy – dependent society had struck the Faustian energy bargain, and. Wilford argued, it resulted in the energy crisis of the 1970s.
Aside from the environmental damage wrought by industrial society, there was also the problem of how to sustain its momentum. The power to drive modern American society is derived in large part from natural resources not within its control. At the time of Wilford’s article, petroleum represented 43 percent of all domestic energy usage. With more than 90 percent of all the oil consumed in the eastern half of the United States coming from sources abroad. Wilford argued. “This gives a number of foreign governments a major voice in the price and How of American fuel.”[35] And more than prices were under their control. As one geologist wrote in 1976, “Whoever controls the energy systems can dominate the society.”[36] As the United States became a superpower in the 20th century, the American engine became increasingly powered by a fuel not of its own making. The effects of external control became evident with the onset of the Arab oil embargo.
In 1973. 2 years after the suggestion that the United States was suffering from or had an energy crisis, the Arab world began using “oil as a weapon.”[37] [38] [39] The statistical results of the Yom Kippur War included the loss of more than 3,000 lives, as well as billions of dollars expended in military equipment. But for the first time, a new weapon emerged that had the power to destabilize all industrial nations —oil. Because of American support of Israel, Saudi Arabia announced a 10-percent reduction in the flow of oil to the United States and its allies, with the threat of an additional 5-percent reduction each month unless the West stopped sending arms to Israel. Saudi Arabia was at the time producing 8!^ million barrels of oil a day. and it represented the third largest oil exporter to America, roughly 400.000 barrels per day.* Similar threats came from other members of the oil cartel, known as the Organization of the Petroleum Exporting Countries (OPEC). Oil was the lifeblood of the United States, and a shortage or a threat to its access quickly revealed it to be the Nation’s Achilles’ heel.
Although a cease-fire was negotiated by October 22, just weeks after lighting began, the conflict caused an economic ripple effect that spread throughout the world. Neither Israel nor the Arab nations officially won. but the conflict became an important symbol of national identity and strength in the Muslim world. It marked the first time Egyptian soldiers inflicted losses against Israel and won substantial territorial gains. “Crossing the Suez Canal" became a slogan that contributed to a new Arab unity and pride. M The conflict was significant outside the Middle East as well. Superpower patrons had come to the support of both sides, threatening to engulf the world in conflict, and it all but destroyed the detente negotiated by President Richard M. Nixon and Leonid Brezhnev. For the first time, both superpowers had a direct confrontation in the Middle East, and it served to heighten the Cold War’s intensity, renewing the United States’ perceived urgency to match and surpass all Soviet military capabilities.[40] [41]
While the United States was confident it could maintain its pace in the arms race, its leaders recognized a more significant threat in its vulnerability to the “oil weapon." In response, just 1 month after the Yom Kippur War, President Nixon signed the Alaska pipeline bill, allocating S4.5 billion to open the most significant oil reserves in the United States.11 Soon, the Nation’s speed limit would be reduced to 55 miles per hour. But oil from Alaska and slower driving would not solve the immediate crisis. A reporter from the Washington Post called the oil embargo the “biggest, most painful single problem ever met by the U. S. in peacetime.” And many speculated that the stakes could not be higher: “The political and strategic independence of the United States” was being threatened by “oil blackmail.”[42] [43]
By March 1974, OPEC had decreased oil exports by 15 percent (a reduction of 1.5 million barrels a day to the United States) and dramatically increased prices. On March 17. the embargo essentially ended, but the impact continued to be felt. One reporter noted that the “oil weapon (which looks more like a shotgun than a rifle) has hit its target.” America suffered worsening inflation, decreasing growth, and continued high oil prices. Many predicted that the “United States economy—and indeed the world economy-will never again be the same as in the pre-embargo days."11
The embargo itself was not responsible for the energy crisis, and its end did not make the country less vulnerable. Thomas Rees, a Democratic Congressman from California, stated that the end of the embargo would mean little security for the United States. “I laving the right to buy Arab oil is having the right to go bankrupt.” Me continued his warning, saying,“It’s not the lack of oil that will ruin the world—it’s the price of oil.”[44]
The price of a barrel of oil in the past year alone had increased 450 percent, from $2.59 to $11.65. The price of a gallon of gasoline increased from 38.5 cents in May 1973 to 55.1 cents in June 1974. There seemed to be only one immediate answer to the problem—conservation.
Many oil industry experts thought that the United States could “get by without the Arab oil imports primarily by reducing American consumption.”[45] As early as 1973, vocal proponents called for “strong conversation measures,” including new technologies, which would reduce America’s energy dependence and lessen the effectiveness of the Arabnations’ oil weapon in ’“political and economic warfare”[46] [47] A conservation strategy became the primary means to counter the effects of the energy crisis. Despite the urgency, it would be nearly 2 years after the oil embargo before American politicians began to pursue actively a solution to the problem.
To bring attention to this negligence, on January 29. 1975, a group of American scientists that included 11 Nobel Prize winners published a dire warning: the U. S. was facing “the most serious situation since World War II.” The threat was the “energy crisis," and the group believed that the country was “courting energy disaster” through its lethargy, ignorance, and confusion.1 Nobel laureate Hans A. Bethe, a Cornell University physicist, drafted the report. He and his colleagues warned that “our whole mode of life may come to an end unless we find a solution.”[48] [49] In agreement with Bethe’s analysis, some reporters chastised the U. S. Government for “fiddling while the energy runs out.”14
While President Gerald R. Ford had recently devised an energy program that included a $l-per-barrel excise tax on foreign oil, most believed his modest research initiatives would be ineffective. Even Ford was critical of the U. S. Congress and its lack of action on this increasingly important issue. He thought his excise tax proposal would in a sense, be “putting a gun to Congress’s head,” to try to motivate it to propose a plan to solve

President Gerald R. Ford meets with Soviet and American space leaders to examine the Soviet Soyuz spacecraft model from a model set depicting the 1975 Apollo Soyuz Test Project, an Earth orbital docking and rendezvous mission with crewmen from the U. S. and U. S.S. R. (September 7.1974). (NASA Johnson Space Center [NASA JSC].)
|
the crisis. On January 31,1975. a New York Times reporter wrote that “the country may well be hastened into action.”[50] That same day, most likely unknown to the press, to Bethe, or even to President Ford, two prominent U. S. Senators—Frank E. Moss, a Democratic Senator from Utah, and Barry Goldwater, a Republican Senator from Arizona—sent a letter to the NASA’s Administrator, James C. Fletcher. They thought the Government Agency that had most recently held the Nation’s attention with its successes on the surface of the Moon might have the technological capability to coordinate a major conservation initiative on Earth. This letter, dated January 31, 1975. was the genesis of what became one of the largest coordinated environmental programs ever attempted in the United States. NASA refocused its sights from the heavens to Earth.
From the Moon to Earth
In December 1972, the last two astronauts to walk the surface of the Moon left their desolate surroundings and returned to Earth. Apollo 17 brought to an end a dramatic era at NASA that began with Kennedy’s famous proclamation promising to send a man to the Moon. During the Apollo years. NASA enjoyed the world’s praise as the pinnacle of humanity’s technological excellence. But Apollo 17’s return marked a new era. Its return signified the beginnings of a fundamental transformation in the Agency’s vision, away from space and lunar exploration and toward Earth and low-Earth orbit. Astronauts would venture no further than the low’-Earth destinations of the Space Shuttle, and more pressing national concerns took the focus and initiative away from long-term dreams in space. Furthermore, space initiatives had become the prime focus of NASA during the Apollo era. to the detriment of its work in aeronautics. Basic research in aeronautics was an area that many believed had been neglected for too long. A 1976 Senate Committee on Aeronautical and Space Sciences report stated “We are concerned that the nation’s aeronautical research and technology base in aeronautics has in fact eroded significantly over the last several years.’’[51]
One of the practical earthly problems that entered NASA’s new aeronautical consciousness was the energy crisis. The crisis threatened to shake the foundations of commercial flight. Prior to 1972, fuel represented one – quarter of the operating costs of a typical airline organization.[52] [53] After 1972, foreign petroleum dependency increased, and fuel doubled its revenue drain, resulting in the reduction of flights, grounding of aircraft, and layoffs of thousands employees.2-‘ The situation appeared to grow1 worse by the day.
Because of NASA’s expertise in aeronautics, the United States Congress looked to it to lead a new conservation initiative. It began with the letter that Senators Moss and Goldwater wrote January 31, 1975, to James C. Fletcher, the NASA Administrator. Although the letter came from the Senators, its origins were actually in NASA
John Klineberg spent 25 years working at NASA. He was the Director of both the Goddard Space Flight Center and Lewis (now Glenn) Research Center. 1 le served as Deputy Associate Administrator for Aeronautics and Space Technology at Headquarters and was a research scientist at the Ames Research Center. (NASA Glenn Research Center (NASA GRC).) itself. John Klineberg, who served NASA in a variety of leadership positions, such as head of Lewis Research Center, recently recalled “Moss, of course, wrote us a letter that justified it… [but] 1 wrote that letter.”[54]
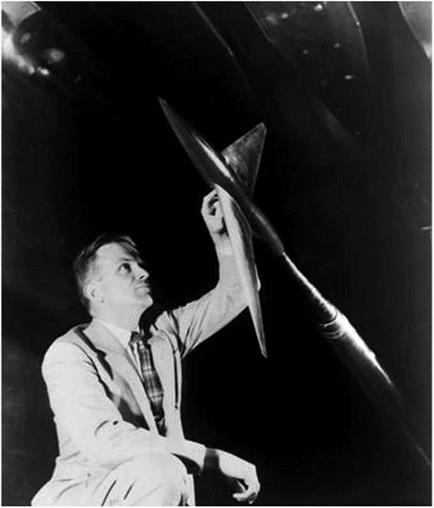
Richard T. Whitcomb examines a model incorporating his famous transonic area rule in the 8-foot High-Speed Tunnel in April 1954. (NASA Langley Research Center [NASA LaRCJ.)
|
In the letter. Moss and Goldwater said it was their desire, as leaders of the Committee on Aeronautical and Space Sciences, that NASA devise a plan to develop new technologies to lessen the effects of the energy crisis.
The plan was needed for the “preservation of the role of the United States as a leader in aeronautical science and technology” They envisioned a program led by NASA that would result in significant technology transfers to industry. NASA was to research a new generation of fuel-efficient aircraft that would cost roughly the same as current aircraft, have the same performance capabilities, meet the same safety and environmental requirements, offer significant fuel savings, and be able to take to the skies in the 1980s. Moss and Goldwater ended their letter by stating, “It is our hope that the goal you establish will be one that is both feasible and challenging.”25 Risk and the acceptance of challenge were approved and encouraged components of the daring project from the start.
NASA responded quickly to the request, in part because the Agency had already been investigating some fuel-efficient technologies as part of its base R&D activities. One of the first was the “supercritical wing,” a project led by Langley’s Richard Whitcomb in the mid-1960s, which delayed the formation of a shock wave until the aircraft attained a faster speed.2*’
The result was a significant cruise performance improvement and an increase in fuel efficiency. In mid-1970. NASA established the Advanced Transport Technology office to take advantage of the aerodynamic potential of the supercritical wing for flight efficiency. Other fuel-efficient technology programs were soon added. This included an Active Controls program. which used computers to control airplane surfaces to reduce drag and increase efficiency. Composite materials were also studied because of the light weight and strength of polymers compared with existing aluminum and metal airplane components.
With the oil embargo in 1973 and the resulting energy crisis, NASA intensified its explorations into this area. It established the Energy Trends and Alternative Fuels (ETAF) program in April 1973 to search for more efficient uses of petroleum and also for alternative energy sources such as hydrogen and electric power. By the end of the year, a NASA manager wrote, “The relevance and urgency of this study has grown dramatically since spring.”2 In 1973, NASA also collaborated with Hamilton Standard in a program called Reducing the Energy Consumption of Commercial Air Transportation (RECAT). Over the next 2 years, NASA, in collaboration with General Electric, Pratt & Whitney, Hamilton Standard, and [55] [56] [57]
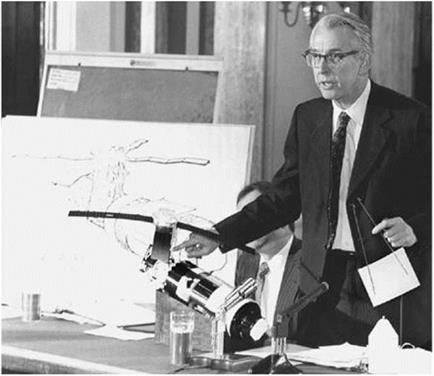
Dr. James Fletcher appearing before the U. S. Senate Committee on Aeronautical and Space Sciences to discuss Skylab (May 23. 1973). As NASA Administrator. Fletcher gained the approval of the Nixon Administration to develop the Space Shuttle as a follow-on human space llight effort. (NASA Headquarters —Greatest Images of NASA (NASA HQ GRIN|.)
|
American Airlines, would explore several opportunities for achieving more energy-efficient aircraft. When the two Senators challenged NASA’s leaders in January 1975 to come up with a solution for the crisis threatening American aviation, they drew their inspiration from these programs.2*
NASA’s Administrator, James Fletcher, assigned overall responsibility for a new airline fuel efficiency program to Alan M. Lovelace, NASA’s Associate Administrator for Aeronautics and Space Technology.
With a goal of conservation before him, in a month’s time, Lovelace had established the Aircraft Fuel Conservation Technology Task Force. James J. Kramer, from the Office of Aeronautics and Space Technology [58]
(OAST), directed the 15-member task force, which came to be called the Kramer Committee.-‘4 For the next 2 months, the Committee members worked together to develop a technology plan to satisfy the Government’s request. To evaluate their results, NASA on April 17 established an advisory board chaired by Raymond L. Bisplinghoff from the University of Missouri.[59] [60] [61] The Kramer Committee included a remarkably diverse and knowledgeable group of members representing universities (MIT), industry (American Airlines, Pan American, Douglas Aircraft. Boeing), Government (NASA, the Federal Aviation Administration fFAAJ, the Department of Transportation, the Department of Defense), and engine manufacturers (Pratt & Whitney, Lockheed, General Electric). They named the new conservation effort the Aircraft Energy Efficiency (ACEE) program.
John Klineberg. one of the key members of the task force, recalled how closely it listened to the needs of industry. As part of the process, task force members went directly to industry leaders. They then reported areas of concern and need back to the task force. They discussedissues with the various NASA Centers in the same way. The information was then turned into briefings, and the task force communicated the results back to industry and NASA. This was the process by which ACEE took shape.3′
In May and June 1975. the advisory board met to review and revise the initial recommendations of the Kramer Committee. The group members initially started with a long list of initiatives that would potentially lessen the effects of the energy crisis. They then worked to reduce the options to a manageable number and divided them into specific technology sections. Although some projects might be ready for short-term implementation, most required a projected 10 years of research and development before aircraft fuel consumption would be reduced. The ultimate goal, according to Kramer, was “achieving a technology readiness by 1985 for a 50 percent reduction in fuel consumption for new civil transports.”1- There were two unbreakable ground rules for attaining these goals. The first wras that fuel would not be saved at the expense of the environment. The second wfas that fuel savings techniques would not compromise aircraft safety in any way. Ultimately, the Kramer Committee identified six technology plans it believed would achieve the stated fuel reduction goal, without violating safety or environmental criteria.
The Kramer Committee’s six conservation technologies addressed the three ways to improve fuel efficiency in an airplane, as expressed in the Breguet range equation: decreasing the fuel consumption by an engine, decreasing the aircraft drag by improving its aerodynamics, and decreasing the weight of the airplane. The Committee’s six conservation technologies addressed all of these areas. The Engine Component Improvement project would identify minor ways to improve existing engines to make them more fuel efficient. At an estimated cost of S40 million, the cumulative effects could have a 5-percent increase in fuel savings. The Energy Efficient Engine (or “E3,’’ as it came to be known) project would go beyond modifications to existing engines by creating an entirely new’ model to be ready for airplanes built in 1990. This was a planned 7-year, $175- million project, with a potential 10-percent fuel savings. The final propulsion project was considered the most radical of the all, a return to propellers, or “turboprops.” Though the riskiest proposal in terms of success, it also provided one of the greatest rewards, a potential 15- to 30-percent fuel savings compared with existing jet aircraft. The turboprops w’ere a 9-year, $ 125-million program.
In addition to the three propulsion projects, the Kramer Committee also identified two main airframe aerodynamics performance initiatives. [62]
Janies Kramer. Associate Administrator for Aeronautics, visiting Langley in 1978. Joseph Chambers, at right, briefs him on stall/spin research for general aviation airplanes. Kramer is holding a spin tunnel model of the American Yankee airplane shown in tlie background. Courtesy of Joseph Chambers.
Dr. Hans Mark (1929- ) speaks Moffett Field Officer s Club (November 9. 1976). Mark became NASA Deputy Administrator in July 1981. He had served as Secretary of the Air Force and as Undersecretary of the Air Force. Mark has also served as Director of NASA’s Ames Research Center. Mountain View. CA. (NASA Ames Research Center (NASA ARC|.)
The first, the Energy Efficient Transport program, called for evolutionary improvements to optimize aircraft designs. Wind tunnel studies would help verify new designs that decreased drag and improved fuel efficiency. This was a 7-year, S50-million program, with estimated fuel savings of 10 to 15 percent. A second aerodynamics initiative. Laminar Flow Control, had an even greater potential drag reduction potential through a smooth (or laminar) flow over the wings and tail. Virtually all civil transports cruise with a turbulent flow that increases drag. With anywhere from 20 to 40 percent fuel savings, the 10-year, $ 100-million program was estimated to be flight-ready by 1990.
The final area the Kramer Committee identified involved using advanced materials to reduce the weight of aircraft. The Composite Primary Aircraft Structures program investigated composites containing boron or graphite filaments in polyimide, epoxy, or aluminum matrices that could potentially reduce aircraft weight by 25 percent. This was a $180-million, 8-year program with 10- to 15-percent fuel savings potential, with the new composite designs in service by 1985.
There were some concerns about the selection of these ACEE projects. Hans Mark, the Director of NASA’s Ames Research Center, wrote to Alan Lovelace in June 1975 saying that “Certainly there are many other aeronautical needs which must not be neglected.”3-‘ He understood that fuel conservation was in the national interest, but he cautioned against committing too much aeronautical funding to the development of civil aviation at the expense of military aircraft technology. He added that aeronautical priorities change quickly. The main issue in 1968 was airport congestion. In 1970. aircraft noise was the central problem. By 1974, it was fuel conservation. Mark wanted to ensure that NASA did not overreact to something that might turn out to be a short-term problem. Furthermore, he suggested that fuel efficiency could be improved by working with the airlines to develop more fuel-efficient flight trajectories.
Lovelace appreciated Mark’s concerns, but the ACEE plan went forward without any changes. In total, six recommendations made by the Kramer Committee cost a projected $670 million, with a 10-year timeframe for implementation. The percentage fuel savings for each project could not be added together because they did not all apply to the same type of aircraft. [63]
However, when combined, they did reach the stated goal of 50 percent in total fuel reduction. Raymond Bisplinghoff, the head of the advisory board for the Kramer Committee, officially presented these conclusions and an outline of the technology plan to Alan M. Lovelace on July 30, 1975*
The role of NASA itself was the one of the final areas of debate by the Kramer Committee. Since the Committee was made up of a cross section of individuals from different academic, industrial, and governmental organizations, there was a broad and vigorous discussion about NASA and the importance of Government-funded research. The Committee members realized that ACEE was unusual because it “in some instances goes further in the demonstration of civil technology improvements than has been NASA’s traditional role.” But the consensus was that this was necessary because of the “inability of industry to support these activities on their own.” Specifically, the Kramer Committee stated, individual technologies such as the turboprop or laminar How control would likely never be developed by industry because of their “high technical risks.”* The Committee published its final report. “Aircraft Fuel Conservation Technology,” in September 1975.
Concurrently with the publication of the report, a separate and independent study examined the costs and benefits of implementing these projects. NASA contracted with Ultrasystems, a California company that specialized in generating computerized economic models. Looking at a 10-year period. Ultrasystems used the Kramer Committee’s $670-million cost estimate and compared it with a forecast of commercial aircraft Heet fuel consumption. While Ultrasystems conceded that the airline industry was in a state of flux and was often unpredictable, it tried to use some baseline assumptions to predict the near-term future. To lessen errors. Ultrasystems used proprietary data given to NASA’s Ames Research Center from various aircraft manufacturers and the airline industry itself. It concluded that implementing the six ACEE programs advocated by the Kramer Committee would save the equivalent of 677.500 barrels of [64] [65] oil each day. The future price of a barrel of oil determined the ultimate potential return on this investment. Again. Ultrasystems made some educated assumptions but concluded that for each dollar spent on the program, there would be anywhere from a return of $7.50 to $26 on the investment. The final assessment examined whether funding for these programs should come from private industry or the Government, and it concluded. “It is extremely unlikely that private industry could meet the expected capital requirements of the NASA program and, consequently. Federal support is necessary.”56
The engineers had finished defining and laying out the program. The only other question to be answered was: Would Government approve the program and provide the funding for one of the largest coordinated fuel conservation projects ever attempted in the United States? To answer that question, the Senate held three hearings in fall 1975 and used the testimony to decide the program’s future.