It was not until the mid-1940s that it became apparent to aerodynamic researchers in the United States that it might be possible to build a flight vehicle capable of hypersonic speeds. Until that time, propulsion systems capable of generating the thrust required for such vehicles had simply not been considered technically feasible. The large rocket engines that had been developed in Germany during World War II allowed concept studies to be initiated with some hope of success.
Nevertheless, in the immediate post-war period, most researchers believed that hypersonic flight was a domain for unmanned missiles. When an English translation of a technical paper by German scientists Eugen Sanger and Irene Bredt was provided by the U. S. Navy’s Bureau of Aeronautics (BuAer) in 1946, this preconception began to change. Expanding upon ideas conceived as early as 1928, Singer and Bredt had concluded during 1944 that a rocket-powered hypersonic aircraft could be built with only minor advances in technology. The concept of manned aircraft flying at hypersonic speeds was highly stimulating to researchers at the National Advisory Committee for Aeronautics (NACA).’ But although there were numerous paper studies exploring variations of the Sanger and Bredt proposal in the late 1940s, none bore fruit and no hardware construction was undertaken at that time. It was from this background, however, that the concept for a hypersonic research airplane would emerge.2
At the time, there was no established need for a hypersonic aircraft, and it was assumed by many that no operational military3 or civil requirement for hypersonic vehicles would be forthcoming in the foreseeable future. The need for hypersonic research was not overwhelming, but there was a growing body of opinion that it should be undertaken.
The first substantial official support for hypersonic research came on 24 June 1952 when the NACA Committee on Aerodynamics passed a resolution to “… increase its program dealing with the problems of unmanned and manned flight in the upper stratosphere at altitudes between 12 and 50 miles,4 and at Mach numbers between 4 and 10.” This resolution was ratified by the NACA Executive Committee when it met the following month. A study group consisting of Clinton E. Brown (chairman), William J. O’Sullivan, Jr., and Charles H. Zimmerman was formed on 8 September 1952 at the Langley5 Aeronautical Laboratory. This group endorsed the feasibility of hypersonic flight and identified structural heating as the single most important technological problem remaining to be solved.
An October 1953 meeting of the Air Force’s Scientific Advisory Board (SAB) Aircraft Panel provided additional support for hypersonic research. Chairman Clarke Millikan released a statement declaring that the feasibility of an advanced manned research aircraft “should be looked into.” The panel member from Langley, Robert R. Gilruth, played an important role in coordinating a consensus of opinion between the SAB and the NACA.
Contrary to Sanger’s conclusions, by 1954 it was generally agreed within the NACA and industry that the potential of hypersonic flight could not be realized without major advances in technology. In particular, the unprecedented problems of aerodynamic heating and high-temperature structures appeared to be so formidable that they were viewed as “barriers” to sustained hypersonic flight.
Fortunately, the successes enjoyed by the second generation X-ls and other high-speed research programs had increased political and philosophical support for a more advanced research aircraft program. The large rocket engines being developed by the long-range missile (ICBM) programs were seen as a way to provide power for a hypersonic research vehicle. It was now agreed that manned hypersonic flight was feasible. Fortunately, at the time there was less emphasis than now on establishing operational requirements prior to conducting basic research, and perhaps even more fortunately, there were no large manned space programs with which to compete for funding. The time was finally right for launching a hypersonic flight research program. s
The specific origins of the hypersonic research program occurred during a meeting of the NACA inter-laboratory Research Airplane Panel held in Washington, DC, on 45 February 1954. The panel chairman, Hartley A. Soule, had directed NACA research aircraft activities in the cooperative USAF – NACA program since 1946 and was well versed in the politics and personalities involved. The panel concluded that a wholly new manned research vehicle was needed, and recommended that NACA Headquarters request detailed goals and requirements for such a vehicle from the research laboratories.
In responding to the NACA Headquarters, all of the NACA laboratories set up small ad hoc study groups during March 1954. Langley had been an island of hypersonic study since the end of the war and chose to deal with the problem in more depth than the other laboratories. After the new 11-inch hypersonic wind tunnel at Langley became operational in 1947, a research group headed by Charles H. McLellan was formed to conduct limited hypersonic research.7 This group, which reported to the Chief of the Langley Aero – Physics Division, John V. Becker, provided verification of newly developed hypersonic theories while investigating such important phenomena as hypersonic shock-boundary – layer interaction. The 11-inch tunnel later served to test preliminary design configurations that led to the final hypersonic aircraft configuration. Langley also organized a parallel exploratory program into materials and structures optimized for hypersonic flight.
Given this, it was not surprising that a team at Langley was largely responsible for defining the early requirements for the new research airplane. The members of the Langley team included Maxim A. Faget in propulsion; Thomas A. Toll in configuration, stability, and control; Norris F. Dow in structures and materials; and James B. Whitten in piloting. All four fell under the direction of Becker. Besides the almost mandatory elements of stability, control, and piloting, a fourth objective was outlined that would come to dominate virtually every other aspect of the aircraft’s design— it would be optimized for research into the related fields of high-temperature aerodynamics and high-temperature structures. Thus it would become the first aircraft in which aero – thermo-structural considerations constituted the primary research problem, as well as the primary research objective.
The preliminary specifications for the research aircraft were surprisingly brief: only four pages of requirements, plus six additional pages of supporting data. A new sense of urgency was present: “As the need for the exploratory data is acute because of the rapid advance of the performance of service aircraft, the minimum practical and reliable airplane is required in order that the development and construction time be kept to a minimum."* In other versions of the requirements this was made even more specific: “It shall be possible to design and construct the airplane within 3 years.”9 As John Becker subsequently observed, "… it was obviously impossible that the proposed aircraft be in any sense an optimum hypersonic configuration.”
In developing the general requirements, the team developed a conceptual research aircraft that served as a model for the eventual X-15. The aircraft they conceived was “… not proposed as a prototype of any of the particular
The first Bell X-2 (46-674) made its initial unpowered glide flight on 5 August 1954. This aircraft made a total of 17 flights before it was lost on 27 September 1956. Its pilot, Air Force Captain Milburn Apt had flown to a record speed 2,094 mph, thereby becoming the first person to exceed Mach 3.
(NASA/DFRC)
concepts in vogue in 1954 … [but] rather as a general tool for manned hypersonic flight research, able to penetrate the new regime briefly, safely, and without the burdens, restrictions, and delays imposed by operational requirements other than research.” The merits of this approach had been convincingly demonstrated by the successes of the X-l and other dedicated research aircraft of the late 1940s and early 1950s.10
Assuming that the new vehicle would be air launched like the X-l and X-2, Langley established an aircraft size that could conveniently be carried by a Convair B-36, the largest suitable aircraft available in the inventory. This translated to a gross weight of approximately
30.0 pounds, including 18,000 pounds of fuel and instrumentation.11 A maximum speed of 4,600 mph and an altitude potential of
400.0 feet were envisioned, with the pilot subjected to approximately 4.5g (an acceleration equal to 4.5 times the force of gravity) at engine burnout.12
The proposed maximum speed was more than double that achieved by the X-2, and placed the aircraft in a region where heating was the
primary problem associated with structural design, and where very little background information existed. Hypersonic aerodynamics was in its infancy in 1954. The few small hypersonic wind tunnels then in existence had been used almost exclusively for fluid mechanics studies, and they were unable to simulate either the high temperatures or the high Reynolds numbers of actual flight. It was generally believed that these wind tunnels did not produce valid results when applied to a full-scale aircraft. The proposed hypersonic research airplane, it was assumed, would provide a bridge over the huge technological gap that appeared to exist between laboratory experimentation and actual flight.12
One aspect of the Langley proposal caused considerable controversy. The Langley team called for two distinct research flight profiles. The first consisted of a variety of constant angle-of-attack, constant altitude, and maneuvering flights to investigate the aerodynamic and thermodynamic characteristics and limitations of then-available technology. These were the essential hypersonic research flights. But the second flight profile was designed to explore some of the problems of manned
space flight by making "… long leaps out of the sensible atmosphere.” This included investigations into high-lift and low-L/D (lift over drag; commonly called a drag coefficient) during the reentry pull-up maneuver” which was recognized as a prime problem for manned space flight from both a heating and piloting perspective.14
This brought other concerns: “.., As the speed increases, an increasingly large portion of the aircraft’s weight is borne by centrifugal force until, at satellite velocity, no aerodynamic lift is needed and the aircraft may be operated completely out of the atmosphere. At these speeds the pilot must be able to function for long periods in a weightless condition, which is of considerable concern from the aeromed – ical standpoint.” By employing a high altitude ballistic trajectory to approximately 250,000 feet, the Langley group expected the pilot would operate in an essentially weightless condition for approximately two minutes. Attitude control was another problem, since traditional aerodynamic control surfaces would be useless at the altitudes proposed for the new aircraft; the dynamic pressure would be less than 1 pound per square foot (psf). The
use of small hydrogen-peroxide thrusters for attitude control was proposed.
While the hypersonic research aspect of the Langley proposal enjoyed virtually unanimous support, it is interesting to note that the space flight aspect was viewed in 1954 with what can best be described as cautious tolerance. There were few who believed that any space flight was imminent, and most believed that manned space flight in particular was many decades in the future, probably not until the 21st century. Several researchers recommended that the space flight research was premature and should be removed from the рто – gram. Fortunately, it remained.15
Hypersonic stability was the first problem of really major proportion encountered in the study. Serious instability had already been encountered with the X-l and X-2 at Mach numbers substantially lower than those expected with the proposed hypersonic research aircraft, and it was considered a major challenge to create a solution that would permit stable flight at Mach 7.
Researchers at Langley discovered through
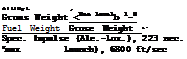
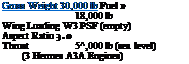
The notional research airplane designed by John V. Becker’s group at Langley shows the basis for the eventual X-15. Note the bulletshaped fuselage (similar to the X-1) and the configuration of the empennage. This was the shape most of the early wind tunnel and analytical studies were performed against. (NASA)
wind tunnel testing and evaluating high speed data from earlier X-planes that an extremely large vertical stabilizer was required if the thin sections then in vogue for supersonic aircraft were used. This was largely because of a rapid loss in the lift-curve slope of thin sections as the Mach number increased. The solution devised by McLellan, based on theoretical considerations of the influence of airfoil shape on normal force characteristics, was to replace the thin supersonic-airfoil section of the vertical stabilizer with a 10 degree wedge shape. Further, a variable-wedge vertical stabilizer was proposed as a means of restoring the lift-curve slope at high speeds, thus permitting much smaller surfaces, which were easier to design structurally and imposed a smaller drag penalty on the airframe. McLellan’s calculations indicated that this wedge shape should eliminate the disastrous directional stability decay encountered by the X-l and X-2.
edge, very similar to the one eventually used on the Space Shuttle orbiters. Both the braking effect and the stability derivatives could be varied through wide ranges by variable deflection of the wedge surfaces. The flexibility made possible by variable wedge deflection was thought to be of great value because a primary use of the airplane would be to study stability, control, and handling characteristics through a wide range of speeds and altitudes. lfi
Two basic structural design approaches had been debated since the initiation of the study—first, a conventional low-temperature design of aluminum or stainless steel protected from the high-temperature environment by a layer of assumed insulation; and second, an exposed hot-structure in which no attempt would be made to provide protection, but in which the metal used and the design approach would permit high structural temperatures.17
Becker’s group also included speed brakes as part of the vertical stabilizers to reduce the Mach number and heating during reentry. Interestingly, the speed brakes originally proposed by Langley consisted of a split trailing
It was found from analysis of the heating projections for various trajectories that the airplane would need to accommodate temperatures of over 2,000 degrees Fahrenheit on the lower surface of the wing. At the time, there
This chart was used by Becker to demonstrate the relative differences between the nominal recovery temperature, compared to the temperatures expected to be sustained by an insulated structure and an appropriately designed heat-sink skin (hot-structure). Inconel X was the material of choice very early in the study.
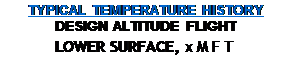
(NASA)
was no known insulating technique that could meet this requirement. The Bell “doublewall” concept where a non Toad-bearing metal sandwich acted as the basic insulator, would later undergo extensive development, but in 1954, it was in an embryonic state and not applicable to the critical nose and leading edge regions. Furthermore, it required a heavy and space-consuming supplemental liquid cooling system. However, the study group felt that the possibility of local failure of any insulation scheme constituted a serious hazard. Finally, the problem of accurately measuring heat-transfer rates—one of the prime objectives of the new research aircraft program— would be substantially more difficult to accomplish with an insulated structure.
At the start of the study it was by no means obvious that the hot-structure approach would prove practical either. The permissible design temperature for the best available material was about 1,200 degrees Fahrenheit, which was far below the estimated equilibrium temperature peak of about 2,000 degrees Fahrenheit. It was clear that some form of heat dissipation would have to be employed—either direct internal cooling or heat absorption into the structure
itself. It was felt that either solution would bring a heavy weight penalty.
The availability of Inconel Xі* and its exceptional strength at extremely high temperatures, made it, almost by default, the structural material preferred by Langley for a hot-structure design. During mid-1954, an analysis of an Inconel X structure was begun by Becker’s group; concurrently, a detailed thermal analysis was conducted. A subsequent stress study indicated that the wing skin thickness should range from 0.05 to 0.10 inches—about the same values found necessary for heat absorption in the thermal analysis.
Thus it was possible to solve the structural problem for the transient conditions of a Mach 7 aircraft with no serious weight penalty for heat absorption. This was an unexpected plus for the hot-structure. Together with the fact that none of the perceived difficulties of an insulated-type structure were present, the study group decided in favor of an uninsulated hot-structure design.
Unfortunately, it later proved that the hot – structure had problems of its own, particularly
Inconel X was easily the best high-temperature alloy available during the 1950s. It possessed a rare combination of high tensile strength and the ability to withstand high temperatures. Although it proved somewhat difficult to work with, it did not impose some of the problems encountered with titanium on other high-speed aircraft projects. (NASA)
in the area of nonuniform temperature distribution. Detailed thermal analyses revealed that large temperature differences would develop between the upper and lower wing skin during the pull-up portions of certain trajectories. This unequal heating would result in intolerable thermal stresses in a conventional structural design. To solve this new problem, wing shear members were devised which did not offer any resistance to unequal expansion of the wing skins. The wing thus was essentially free to deform both spanwise and chord – wise with asymmetrical heating. Although this technique solved the problem of the gross thermal stresses, localized thermal-stress problems still existed in the vicinity of the stringer attachments. The study indicated, however, that proper selection of stringer proportions and spacing would produce an acceptable design free from thermal buckling.
During the Langley studies, it was discovered that differential heating of the wing leading edge produced changes in the natural torsional frequency of the wing unless some sort of flexible expansion joint was incorporated in its design. The hot leading edge expanded faster than the remaining structure, introducing a compression that destabilized the section as a whole and reduced its torsional stiffness, To negate this phenomenon, the leading edge was segmented and flexibly mounted in an attempt to reduce thermally induced buckling and bending.
With its research objectives and structure now essentially determined, the Langley team turned its attention to the questions of propulsion by examining various existing rocket propulsion systems. The most promising configuration was found to be a grouping of four General Electric A1 or A3 Hermes rocket engines, due primarily to the “thrust stepping” (a crude method of modulating, or throttling, the thrust output) option this configuration provided.
The studies prompted the NACA to adopt the official policy that the construction of a manned hypersonic research airplane was feasible. In June 1954, Dr. Hugh L. Dryden sent a letter to Lieutenant General Donald Putt at Air Force Headquarters stating that the NACA was interested in the creation of a new manned research aircraft program that would explore hypersonic speeds and altitudes well in excess of those presently being achieved. The letter also recommended that a meeting between the NACA, Air Force Headquarters, and the Air Force SAB be arranged to discuss the project. Putt responded favorably, and also recommended that the Navy be invited to participate.
NACA representatives met with members of the Air Force and Navy research and development groups on 9 July 1954 to present the proposal for a hypersonic research aircraft as an extension of the existing cooperative research airplane program. It was soon discovered that the Air Force SAB had been making similar proposals to Air Force Headquarters, and that the Office of Naval Research had already contracted with the Douglas Aircraft Company to determine the feasibility of constructing a manned aircraft capable of achieving 1,000,000 feet altitude. Douglas had concluded that 700,000 foot altitudes would be possible from the reentry deceleration standpoint, but that the thermostructural problem had not been thoroughly analyzed. It was agreed that a cooperative program would be more cost effective and likely lead to better research data at an earlier time.19
The Navy and Air Force representatives viewed the NACA proposal with favor, although each had some reservations. At the close of the meeting, however, there was agreement that both services would further study the details of the NACA proposal, and that the NACA would take the initiative to secure project approval from the Department of Defense.2"
Less than a month later, the Air Force identified the principal shortcoming of the original Langley proposal—the apparent lack of a suitable rocket engine. In early August the Power Plant Laboratory at the Wright Air Development Center (WADC) pointed out
that “no current rocket engines” entirely satisfied the NACA requirements, and emphasized that the Hermes engine was not designed to be operated in close proximity to humans—that it usually was fired only when shielded by concrete walls. Other major objections to the Hermes engine centered around its relatively early state of development, its limited design life (intended for missile use, it was not required to operate successfully more than once), and the apparent difficulty of incorporating the ability to throttle it during flight.21 WADC technical personnel who visited Langley on 9 August drew a firm distinction between engines intended for piloted aircraft and those designed for missiles; the NACA immediately recognized the problem, but concluded that although program costs would increase, the initial feasibility estimates would not be affected.22
WADC’s official reaction to the NACA proposal was submitted to the Air Research and Development Command (ARDC) on 13 August.2’ Colonel V. R. Haugen reported “unanimous” agreement among WADC participants that the proposal was technically feasible; excepting the engine situation, there was no occasion for adverse comment. The evaluation forwarded by Haugen also contained a cost estimate of $12,200,000 “distributed over three to four fiscal years" for two research aircraft and necessary government – furnished equipment. Estimated costs included: $1,500,000 for design work; $9,500,000 for construction and development, including flight test demonstration; $650,000 for government furnished equipment, including engines, $300,000 for design studies and specifications; and $250,000 for modification of a carrier aircraft.24 Somewhat prophetically, one WADC official commented informally: “Remember the X-3, the X-5, [and] the X-2 overran 200 percent. This project won’t get started for $12,000,000.”"
On 13 September, the ARDC issued an endorsement of the NACA proposal, and recommended that the Air Force “… initiate a project to design, construct, and operate a new research aircraft similar to that suggested by NACA without delay.” The aircraft, emphasized ARDC, should be considered a pure research vehicle and should not be programmed as a weapon system prototype. On 4 October 1954, Brigadier General Benjamin S. Kelsey, Deputy Director of Research and Development at Air Force Headquarters, stated that the project would be a joint Navy – NACA-USAF effort managed by the Air Force and guided by a joint steering committee. Air Force Headquarters further pointed out the necessity for funding a special flight test range as part of the project:4′
The NACA Committee on Aeronautics met on 5 October 1954 to consider the hypersonic research aircraft. During the meeting, historic and technical data were reviewed by various committee members including Walter C. Williams, De E. Beeler, and research pilot A. Scott Crossfield from the High-Speed Flight Station (HSFS). Williams’ support was crucial. Crossfield would later describe Williams as.. the man of the 20th Century who made more U. S. advanced aeronautical and space programs succeed than all the others together. … He had no peer. None. He was a very strong influence in getting the X-15 program launched in the right direction.”27
Although one Committee member expressed opposition to the proposed hypersonic research aircraft as an extension to the ongoing test programs, the rest of the Committee supported the project. The Committee formally adopted a resolution to build a Mach 7 research airplane (attached as an appendix to this monograph).2*
Because the anticipated cost of the project would require support from Department of Defense contingency funds as well as Air Force and Navy R&D funds, a formal Memorandum of Understanding (MoU) was drafted and sent around for signatures beginning in early November 1954. The MoU was originated by Trevor Gardner (Air Force Special Assistant for Research and Development), and was forwarded, respec-
tively, for the signatures of J. H. Smith Jr. H (Assistant Secretary of the Navy [Air]) and Hugh L. Dryden (Director of the NACA). Dryden signed the Moll on 23 December 1954, and returned executed copies to the Air Force and Navy.’0
The MoU (attached as an appendix to this monograph) provided that technical direction of the research project would be the responsibility of the NACA, acting.. with the advice and assistance of a Research Airplane Committee” composed of one representative each from the Air Force, Navy, and the NACA. Administration of the design and construction phases of the project was assigned to the Air Force. The NACA would conduct the flight research, with extensive support from the Air Force Flight Test Center. The Navy was essentially left paying 25 percent of the bills with little active roll in the project, although it would later supply biomedical expertise and a single pilot. The NACA and the Research Airplane Committee were charged with the responsibility for disseminating the research results to the military services and aircraft industry as appropriate based on various security aspects. The concluding statement on the MoU was: “Accomplishment of this project is a matter of national urgency.’’11
It should be noted that it was not unusual in the late 1940s and early 1950s for the military services to fund the development and construction of aircraft for the NACA to use in its flight test programs. This was how most of the testing on the X-l and others had been accomplished. The eventual X-l5 would be the fastest, highest-flying, and most expensive of these joint projects.12
After the signed copies of the MoU were returned to all participants, the Department of Defense authorized the Air Force to issue invitations to contractors having experience in the development of fighter-type aircraft to participate in the design competition. After the Christmas holidays, on 30 December, the Air Force sent invitation-to-bid letters to 12 prospective contractors; Bell, Boeing,
Chance-Vought, Consolidated (Convair), Douglas, Grumman, Lockheed, Martin, McDonnell, North American, Northrop, and Republic. The letter asked those interested in bidding to notify Wright Field by 10 January 1955, and to attend a bidder’s conference on 18 January 1955.”
Attached to the letter were a preliminary outline specification, an abstract of the Langley preliminary study, a discussion of possible engines, a list of data requirements, and a cost outline statement. Each bidder was required to satisfy various requirements set forth, except in the case of the NACA abstract which was presented as "… representative of possible solutions.”14
Grumman, Lockheed, and Martin expressed little interest in the competition and did not attend the bidder’s conference, leaving nine possible competitors. At the bidders’ conference, representatives from the contractors met with NACA and Air Force personnel to discuss the competition and the basic design requirements.
During the bidders’ conference, the airframe manufacturers were informed that one prime proposal and one alternate proposal (that might offer an unconventional but superior solution to the problems involved) would be accepted from each company. It also was noted that an engineering study, only, would be required for a modified aircraft where an observer could be substituted for the research instrumentation (a Navy requirement); that a weight allowance of 800 pounds, a volume of 40 cubic feet, and a power requirement of 2.25 kilowatts (kW) needed to be provided for research instrumentation; and that the winning design would have to be built in 30 months and be capable of attaining speeds of Mach 6 and altitudes of 250,000 feet. Following the preliminary statements concerning the bidding, NACA personnel briefed the various companies in attendance on new information that had resulted from late 1954 wind tunnel research that had taken place at Langley.
Subsequently, between the bidders’ conference and the 9 May submission deadline, Boeing, Chance-Vought, Convair, Grumman, McDonnell, and Northrop notified the Air Force that they did not intend to submit formal proposals. This left Bell, Douglas, North American, and Republic. During this period, representatives from these companies met with NACA personnel on numerous occasions and reviewed technical information on various aspects of the forthcoming research airplane. The NACA also provided these contractors with further information gained as a result of wind tunnel tests in the Ames 10-by – 14 inch supersonic tunnel and the Langley Mach 4 blowdown tunnel.
On 17 January 1955, NACA representatives met with Air Force personnel at Wright Field and were informed that the research airplane was identified as Air Force Project 1226 and would be officially designated X-15.
The Power Plant Laboratory had originally listed the Aerojet XLR73, Bell XLR81, North American NA-5400 (an engine in early development, still lacking a military designation), and the Reaction Motors XLR10 (and its variants, including the XLR30) as engines that the airframe competitors could use in their designs. Early in January, the laboratory had become concerned that the builders of engines other than those listed might protest the exclusion of their products. Consequently there emerged an explanation and justification of the engine selection process. It appeared that the engineers had confidence in the ability of the XLR81 and XLR73 to meet airplane requirements, had doubts about the suitability of the XLR25 (a Curtiss-Wright product), and held the thrust potential of the XLR8 and XLR11 (similar engines) in low repute. For practical purposes, this exhausted the available Air Force-developed engines suitable for manned aircraft. The XLR10 and NA-5400 were the only Navy-developed engines viewed as acceptable in terms of the competition.35
Earlier, the engine manufacturers had been contacted for specific information about the engines originally listed as suitable for the X-15 program,36 and this information was distributed to all four prospective airframe contractors.37 Due to its early development status, there was little data available for the North American NA-5400, and the Reaction Motors XLR10 was “not recommended” at the suggestion of the engine manufacturer itself. On 4 February each of the prospective engine contractors (Aerojet, Bell, North American, and Reaction Motors) was asked to submit an engine development proposal.38 Based on this, the Air Force very slightly relaxed the rigid limitations on engine selection, instructing competitors that.. if… an engine not on the approved list offers sufficient advantage, the airframe company may, together with the engine manufacturer, present justification for approval…” to the Air Force.35
On 9 May 1955, Bell, Douglas, North American, and Republic submitted their proposals to the Air Force. Two days later the technical data was distributed to the evaluation groups with a request that results be returned by 22 June.40 The final evaluation meeting was scheduled for 25 July at Wright Field.41
Shortly thereafter, Hartley A. Soule, as Chairman of the NACA evaluation group, sent the evaluation rules and processes to the NACA laboratories. The evaluation would be based on the technical and manufacturing competency of each contractor, schedule and cost estimates, design approach, and the research utility of each design. In order to expedite the evaluation, each of the NACA laboratories was assigned specific items to consider with responses to be returned to Soule no later than 13 June.
The evaluation of the engine would be made at the same time, but would be conducted separate from that of the airframe contractor, with the possibility that the chosen engine might not be the one selected by the winning airframe contractor.
On 10 June the HSFS results were sent to Soule, based on the design approach and
research utility aspects of the airframe, flight control system, propulsion unit, crew provisions, handling and launching, and miscellaneous systems. The proposals were ranked:
(1) Douglas; (2) North American; (3) Bell; and (4) Republic. The proposals from Douglas and North American were considered almost equal on the basis of points.
The Ames final evaluation, on 13 June 1955, ranked the proposals: fl) North American;
(2) Douglas; (3) Bell; and (4) Republic. The North American structure was considered to be more representative of future aircraft and thus superior in terms of research utility. Douglas retained a simple and conventional magnesium structure, but in so doing avoided the very thermodynamic problems the research effort wished to explore.
The 14 June final evaluation from Langley ranked the proposals; (1) North American; (2) Douglas; (3) Republic; and (4) Bell. Langley felt that while the magnesium wing structure of Douglas was feasible, it was feared that local hot spots caused by irregular aerodynamic heating could weaken the structure and be subject to failure. North American’s use of Inconel X was believed to be an advantage.
The final order representing the overall NACA evaluation was (1) North American; (2) Douglas; (3) Bell; and (4) Republic. All of the laboratories involved in this portion of the evaluation considered both the North American and Douglas proposals to be much superior to those submitted by Bell and Republic.
As with the NACA evaluations, the Air Force found little difference between the Douglas and North American designs, point-wise, with both proposals significantly superior to those of Beil and Republic. The Navy evaluation found much the same thing, ranking the proposals: (1) Douglas; (2) North American; (3) Republic; and (4) Bell.
On 26-28 July, the Air Force, Navy, and NACA evaluation teams met to coordinate their separate results. The Air Force and the NACA concluded that the North American proposal best accommodated their requirements. Accordingly, the Navy decided not to. be put in the position of casting the dissenting vote and after short deliberation, agreed to go along with the decision of the Air Force and the NACA. A combined meeting of the Air Force, Navy, and the NACA was held at NACA Fleadquarters on 12 August for the final briefing on the evaluation. Later, the Research Airplane Committee met, accepted the findings of the evaluation groups, and agreed to present the recommendation to the Department of Defense.
Interestingly, the North American proposal was by far the most expensive. The estimated costs for three aircraft plus one static test article and supporting equipment were: Bell, $36.3 million; Douglas, $36.4 million; Republic, $47 million; and North American, $56.1 million.
Because the estimated costs submitted by North American were far – above the amount allocated for the project, the Research Airplane Committee included a recommendation for a funding increase that would need to be approved before the actual contract was signed. A further recommendation, one that would later take on greater importance, called for relaxing the proposed schedule by up to one-and-one-half years. These recommendations were sent to the Assistant Secretary of Defense for Research and Development.
Events took an unexpected twist on 23 August when the North American representative in Dayton verbally informed the Air Force that the company wished to withdraw its proposal. On 30 August, North American sent a letter to the Air Force formally requesting that the company be allowed to withdraw from consideration.43
The Vice President and Chief Engineer for North American, Raymond H. Rice, wrote to the Air Force on 23 September and explained that the company had decided to withdraw
from the competition because it had recently won new bomber and long range interceptor competitions and also had increased activity relating to its on-going F-107 fighter. Having undertaken these projects, North American said it would be unable to accommodate the fast engineering man-hours build-up that would be required to support the desired schedule. Rice went on that, “… due to the apparent interest that has subsequently been expressed in the North American design, the contractor [North American] wishes to extend two alternate courses which have been previously discussed with Air Force personnel: The engineering man-power work load schedule has been reviewed and the contractor wishes to point out that Project 1226 could be handled if it were permissible to extend the schedule… over an additional eight month period: in the event the above time extension is not acceptable and in the best interest of the project, the contractor is willing to release the proposal data to the Air Force at no cost.”43
As it turned out, the possibility of extending the schedule had already been approved on 12 August, allowing North American to withdraw its previous letter of retraction once it had been officially informed that it had won the contract.44 Accordingly, on 30 September 1955, the Air Force formally notified North American that its design had been selected as the winner. The other bidders were consequently notified of North American’s selection and thanked for their participation.45
By 11 October, the estimate from North American had been reduced from $56,000,000 to $45,000,000 and the maximum annual funds requirement from $26,000,000 to $15,000,000. Shortly thereafter, the Department of Defense released the funds needed to start work. More meetings between the Air Force, the NACA, and North American were held on 27-28 October, largely to define changes to the aircraft configuration. On 18 November, letter contract AF33(600)-31693 was sent to North American, and an executed copy was returned on 8 December 1955.46 The detailed design
and development of the hypersonic research airplane had been underway for just under a year at this point.47
On 1 December 1955, a series of actions48 began that resulted in letter contract AF33(600)-32248 being sent to Reaction Motors, effective on 14 February 1956. Its initial allocation of funds totaled $3,000,000, with an eventual expenditure of about $6,000,000 foreseen as necessary for the delivery of the first flight engine.49
A definitive contract for North American was completed on 11 June 1956, superseding the letter contract and two intervening amendments. At that time, $5,315,000 had been committed to North American. The definitive contract allowed the eventual expenditure of $40,263,709 plus a fee of $2,617,075. For this sum, the government was to receive three X-15 research aircraft, a high speed and a low speed wind tunnel model program, a free-spin model, a full-size mockup, propulsion system tests and stands, flight tests, modification of a B-36 carrier aircraft, a flight handbook, a maintenance handbook, technical data, periodic reports of several types, ground handling dollies, spare parts, and ground support equipment. Exclusive of contract costs were fuel and oil, special test site facilities, and expenses to operate the B-36. The delivery date for the X-15s was to be 31 October 1958. The quantity of aircraft had been determined by experience; it had been noted during earlier research aircraft programs that two aircraft were enough to handle the anticipated workload, but three assured that the test pace could be maintained even with one aircraft down.50 This lesson has been largely forgotten in our current budget-conscious era.
A final contract for the engine, the prime unit of government furnished equipment, was effective on 7 September 1956. Superseding the letter contract of February, it covered the expenditure of $10,160,030 plus a fee of $614,000.51 For this sum, Reaction Motors agreed to deliver one engine, a mockup, reports, drawings, and tools.