The Grumman X-29 research aircraft played a very interesting role in the evolution of modern fly-by-wire flight control systems. Exotic in appearance, with its forward-swept wings and large movable canard control surfaces, the X-29 was highly unstable about the longitudinal axis with a static stability margin of -35 percent. This level of instability probably indicates that the X-29 represents the most unstable piloted aircraft that has ever been successfully flown. Not only did it fly, but it also demonstrated good controllability at very high angles of attack. This degree of success was only possible through the use of a very advanced fly-by-wire flight control system that employed a combination of both digital computers in the primary system and analog computers in the backup system. The program began in 1977, with the Defense Advanced Research Projects Agency (DARPA) and the Air Force Flight Dynamics Laboratory jointly soliciting industry proposals for a research aircraft designed to investigate the forward-swept wing concept in a high-performance aircraft application. In December 1981, Grumman Aircraft
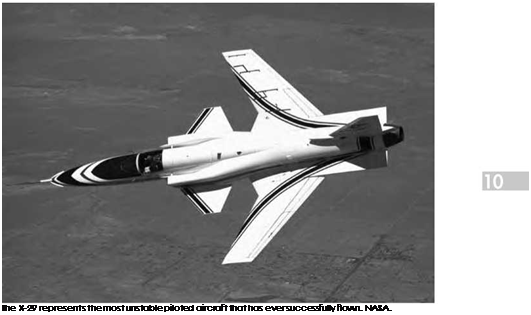
was selected to build two aircraft, which were designated X-29. The most unique and visually obvious aspect of the design was the forward – swept wings that incorporated a thin supercritical airfoil, but there were many other areas of the X-29 design that embodied advanced technology. The aircraft used advanced composite materials and unusual construction approaches. Its control system made use of variable camber wing surfaces, aft fuselage-mounted strake flaps, fully movable canards mounted on the sides of the engine inlets, and a computerized fly-by-wire flight control system to maintain control of the otherwise highly unstable aircraft.[1221]
In constructing the X-29s, Grumman used the forward fuselage and nose landing gear from two Northrop F-5A fighters. Control surface actuators and the main landing gear came from the F-16. The unique aspect of the X-29 airframe, its forward-swept wing, was developed by Grumman. Because of the major differences between the X-29s and the F-5As, the modified aircraft were assigned new USAF serial numbers, becoming 82-0003 and 82-0049. The main difference between the two
X-29s was the emergency spin parachute system mounted at the base of the rudder on the second aircraft. The X-29 flight research program was conducted by the NASA Dryden Flight Research Center in two phases and included participation by the Air Force Flight Test Center and the Grumman Corporation.[1222] The joint NASA-Air Force portion of the X-29 test program extended from 1984 to 1991; the Air Force conducted a follow-on investigation of vortex flow control (VFC) that lasted into 1992.
The X-29’s thin supercritical forward-swept wing presented significant design challenges. The typical stall pattern of an aft-swept wing, from wingtip to root, is reversed for a forward-swept wing, which stalls from the root to the tip. The aerodynamic lift forces on the outer portions of a forward-swept wing produce a twisting moment that tends to force the leading edge further upward. This increases the angle of attack at the wingtips, causing even further twisting that, if uncontrolled, can lead to structural failure of the wing, a phenomenon known as aero – elastic divergence. To deal with this problem, Grumman made use of state-of-the-art composite materials in designing the wing external skin, which it laminated in a way that produced an inherent coupling between wing bending and torsion loads, a concept known as aeroelastic tailoring. At increasing angles of attack (higher lift), the structural characteristics incorporated into composite laminates were designed to ensure that the wing twisted to counter the upward twist produced by aerodynamic loads. The key to the design was balancing the aerodynamic aspects of the wing’s configuration with the structural characteristics of the composite laminate to control potential aeroelastic divergence. The wing substructure and the basic airframe itself were made of aluminum and titanium.[1223]
The X-29 featured an unusual combination of flight control surfaces. These consisted of forward-mounted canards that contributed positive lift and provided primary control about the pitch axis. Wing flaperons (combination flaps and ailerons) could change the camber of the wing and also functioned as ailerons for roll control. The actuators used to control wing camber were mounted externally in streamlined fairings at the trailing edge of the wing because of the thinness of the supercritical airfoil. The strake flaps on each side of aft fuselage augmented the canards, proving additional pitch control. The control surfaces were electronically linked to a triple-redundant digital fly-by-wire
flight control system (with analog backup) that provided artificial stability necessary for controlling the inherently unstable forward-swept wing, close-coupled canard design used on the X-29. Each of the three digital flight control computers had an analog backup. If one of the digital computers failed, the remaining two took over. If two of the digital computers failed, the flight control system switched to the analog mode. If one of the analog computers failed, the two remaining analog computers took over.[1224]
Grumman chief test pilot Charles A. "Chuck” Sewell flew the first X-29 at Edwards AFB on December 14, 1984.[1225] During the Phase I research effort, X-29 aircraft No. 1 was used exclusively, flying 242 times. Its wingtips remained unstalled up to the 21-degree angle of attack allowed in Phase I testing. This limitation was due to the fact that an anti-spin parachute was not installed on the aircraft. The aeroelas – tic tailored wing prevented structural divergence of the wing, and the digital flight control system functioned safely and reliably. Flight control laws and control surface effectiveness combined to provide good pilot handling qualities during maneuvering flight. The aircraft’s supercritical airfoil contributed to enhanced cruise and maneuver performance in the transonic regime.[1226] However, overall drag reduction was not as great as had been predicted for the configuration. On December 13, 1985, with NASA test pilot Steve Ishmael at the controls, the X-29 became the first aircraft with a forward-swept wing to fly beyond the speed of sound, reaching Mach 1.03 in level flight.[1227] Other test pilots who flew the X-29 during Phase I of the joint test program were NASA test pilot Rogers Smith, Lt. Col. Theodore "Ted” Wierzbanowski and Maj. Harry Walker from the Air Force, and Navy Cdr. Ray Craig.
The second X-29 aircraft, modified to incorporate an anti-spin parachute and its deployment mechanism, was used during Phase II testing to investigate the aircraft’s high-angle-of-attack characteristics and the potential usefulness of the forward-swept wing and canard configuration on military fighter plane designs. First flown on May 23, 1989, it would eventually fly 120 research flights and demonstrate control and maneuvering qualities that were better in many cases than the predictions derived from computational methods and simulation models. NASA, Air Force, and Grumman project pilots reported that the X-29 had excellent control response up to angles of attack of 45 degrees, with limited controllability still available at up to 67 degrees angle of attack. Phase II flight-testing defined an allowable X-29 flight envelope that extended to Mach 1.48, an altitude of just over 50,000 feet, an angle of attack of up to 50 degrees at 1 g and 35 degrees at airspeeds up to 300 knots. Much of the X-29’s high-angle-of-attack capability was attributed to the quality of the flight control laws that were cooperatively developed by NASA and the Air Force. These had initially been developed using results obtained from extensive wind tunnel testing and predictions derived from radio-controlled flight tests of a 22-percent scale drop model at NASA Langley Research Center.[1228] Flight control system engineers at NASA Dryden and the Air Force Flight Test Center at Edwards used these as the basis for detailed flight control system design. This design used a combination of pitch rate and angle of attack in developing the longitudinal control laws. Selectable gain was included in the flight control system design, and this was used by the X-29 test pilots during flying qualities assessments and evaluations of the effects of control law gain changes at higher angles of attack. Prior to the start of flight-testing, wing rock was estimated to restrict the available angle of attack to less than about 35 degrees. However in flight-testing, wing rock amplitude was found to be less than half of what had been predicted, allowing the roll rate to aileron gain to be lowered to one-fourth of the value that had been derived from preflight data using the subscale free flight model. The available flight envelope was extended to 67 degrees angle of attack at 1 g. Maneuvering flight about all axes was cleared up to an angle of attack of 45 degrees in 1 g flight. The reduced wing rock that had been observed in flight was apparently due to higher roll
damping and increased aileron control power for large aileron deflections.[1229]
Preflight predictions of the X-29’s pitch capabilities matched flight – test results up through 40 degrees angle of attack. Differences in nose – up pitching moment above an angle of attack of 40 degrees were found to require more canard deflection than predicted. Large yaw asymmetries led to several instances in which the aircraft tended to stabilize at very high nose-up pitch angles during maneuvers at angles of attack above 50 degrees, with the aircraft at an aft center of gravity. Modifications to provide additional nose-down pitch authority were not possible because of physical limits on canard deflection. Maximum pitch rates were limited by the high level of static instability inherent in the X-29 design and control surface rate limits. New actuators with at least a 50-percent higher actuation rate would have been required to achieve pitch rates comparable to those of an operational fighter like the F/A-18. The full wingspan flaper – ons were found to provide good roll control that was not affected by the fact that the X-29 did not use wing leading-edge maneuvering flaps. Pilot – selectable variable gain capability was used during examination of airplane stability and maneuverability. Basic fighter maneuvers were flown, and roll and yaw gains were increased to improve roll performance. A gain that provided maximum rudder authority resulted in the best pilot comments. Roll coordination was better than anticipated, with rudder effectiveness also higher than preflight predictions at angles of attack between 20 and 40 degrees. Yaw asymmetries developed above 40 degrees angle of attack. Diminished aileron and rudder power was not sufficient to overpower these asymmetries. Increasing gain further produced rudder saturation, resulting in uncoordinated turns, a result that was disliked by test pilots, even though this actually resulted in better roll performance.[1230]
Flight-test data from Phase II, the high-angle-of-attack and military utility phase of the X-29 program, satisfied the program’s primary objective. The technologies demonstrated in the program had potential to improve future fighter aircraft mission performance, and the forward-swept wings/movable canard configuration provided excellent control response at up to 45 degrees angle of attack. Very importantly, the X-29A program provided a significant pool of knowledge that
was very useful background for fine-tuning ground-based predictive techniques for high-angle-of-attack aircraft.[1231] One significant potential safety issue with the flight control system, the danger of sensor selection thresholds being set too wide, was discovered during the X-29 test program. The flight control system used three sources of air data in its computations. These air data sources were the nose probe and two probes mounted one on each side of the forward fuselage. The selection algorithm in the flight control system used the data from the nose probe as the primary source, provided it was within some threshold of the data from both side probes. However, the data selection threshold was intentionally large to accommodate known data errors in certain flight modes because of the position of the side sensors in the airflow. Long after the start of flight-testing, ground simulation revealed that the nose probe could, in some circumstances, furnish erroneous information at very low flight speeds, causing the X-29 to go out of control. Although this fault was successfully identified through ground simulation, 162 flights had already been flown before it was detected and corrected.[1232]
In 1992, the Air Force began a follow-on program with X-29 No. 2 that investigated the use of vortex flow control as a means of providing increased aircraft control at very high angles of attack, at which normal rudder control is ineffective. Wind tunnel tests had showed that injection of air into the vortexes coming off the nose of the aircraft would change the direction of vortex flow. The forces created on the nose of the aircraft could be used to control directional (yaw) stability. The second X-29 aircraft was modified to incorporate two high-pressure nitrogen tanks, related control valves with two small nozzle jets on the forward upper portion of the nose. The nozzles injected air into the vortexes, which flowed off the nose of the aircraft at high angles of attack. From May to August 1992, 60 test flights were flown. Data from these flights were used to determine that VFC was more effective than expected in generating yaw forces, but it was less successful in providing control when sideslip was present, and it did little to decrease roll oscillations.[1233] The two X-29 aircraft flew a total of 436 flights, 254 by the first, and 182 by the second. The former is exhibited at the National Museum of the
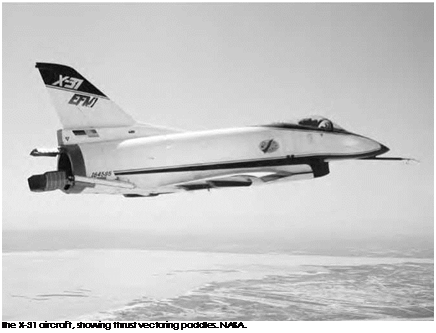 |
 |
United States Air Force, while the latter remained at Edwards and is on exhibit at the Dryden Flight Research Center.[1234]