The Centurion, which was built in 1998 by AeroVironment, represented third-generation advancement on the technology developed in the Pathfinder and Pathfinder Plus UAVs. The Centurion, however, was still
considered to be a prototype demonstrator for future solar-powered vehicles that could stay airborne for long periods of time. Prior to construction of the full-scale Centurion UAV, a quarter-scale model was constructed to verify design predictions. The Centurion had a five-section wingspan of 206 feet, which was more than twice the wingspan of Pathfinder; incorporated a redesigned airfoil; and had a length of 12 feet and an aspect ratio of 26 to 1. The aircraft, which had 14 direct-current electric motors, was to be powered by bifacial solar cells that covered 80 percent of the upper wing surface and had a maximum output of 31 kilowatts. The Centurion
 |
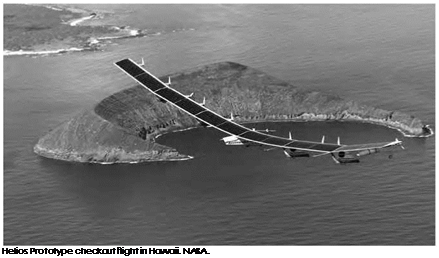 |
had a cruising speed of between 17 and 21 mph and could carry a payload of approximately 100 pounds to an altitude of 100,000 feet, or 600 pounds to 80,000 feet. The primary building material consisted of carbon fiber and graphite epoxy composite structure, Kevlar, Styrofoam leading edge, and plastic film covering. Centurion flew three low-altitude developmental test flights on battery power at NASA Dryden, verifying handling qualities, performance, and structural integrity. The primary mission of the Centurion was to verify the handling and performance characteristics of an ultra-lightweight all-wing UAV with a wingspan of over 200 feet.[1551]
Helios Prototype-Fourth-Generation and Last ERAST Unmanned Aerial Vehicle
The Helios Prototype, which resulted from modifications of the Centurion and renaming of the aircraft to Helios, was a proof-of-concept flying wing that because of budget limitations had two different configurations: a high-altitude configuration designated the HP-01 (1998-2002) and a long-endurance configuration designated the HP-03 (2003).[1552] The two primary objectives for the Helios Prototypes were to demonstrate sustained flight at an altitude of 100,000 feet and the ability to fly nonstop
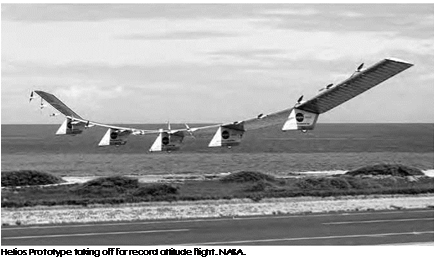 |
 |
for at least 24 hours, including at least 14 hours above 50,000 feet. Initial low-altitude test flights were conducted under battery power at Edwards Air Force Base in 1999. Afterward, Helios was equipped with high – efficiency photovoltaic solar cells and underwent high-altitude flighttesting in the summer of 2001 at the U. S. Navy Pacific Missile Range Facility in Hawaii. On August 13, 2001, following further upgrading of systems, the high-altitude configuration (HP-01) reached an altitude of 96,863 feet, setting a world record for sustained horizontal flight by a winged aircraft and effectively satisfying the first Helios objective of high – altitude performance. The previous record was held by the Air Force’s SR-71A. The plan for the long-endurance configuration was to use solar cells to power the electric motors and subsystems during daylight hours and a modified hydrogen-air fuel cell system during the night. The vehicle also was equipped with backup lithium batteries and was battery – powered for its first six low-altitude test flights at Dryden.
Helios used wing dihedral (wing upsweep), engine power, elevator control surfaces, and a stability augmentation and control system to provide aerodynamic stability and control. Helios added a sixth wing panel to the Centurion, giving the remotely powered aircraft a wingspan of 247 feet, which was longer than the wingspans of either the U. S. Air Force C-5 transport or the Boeing 747 commercial airliner. The aircraft had a length of 12 feet, a wing chord of 8 feet, an empty weight of 1,322 pounds, an aspect ratio of 31 to 1, and wing loading of 0.835 pounds
per square foot. The craft, which had 14 (only 10 on long-endurance HPO3 version) brushless direct-current electric motors each rated at 2 horsepower (1.5 kW) that each drove a lightweight, 79-inch-diameter propeller, was powered by 62,120 bifacial solar cells covering the upper wing surface. Bifacial solar cells enabled Helios to convert solar energy into electricity when illuminated from either above or below, which enabled the vehicle to absorb reflected energy when flying above cloud cover. The Helios had a cruising speed of between 19 and 27 mph and could carry a payload of up to 726 pounds, including ballast, instruments, experiments, and a supplemental energy system. Helios was designed to operate at up to 100,000 feet, which is above 99 percent of the Earth’s atmosphere, with a typical endurance mission at 50,000 to 70,000 feet. Like the Centurion, the Helios Prototype was constructed mostly of composite material, including carbon fiber, graphite epoxy, Kevlar, Styrofoam, and a thin transparent plastic film. The main tubular wing spar, which was made of carbon fiber and also wrapped with Nomex and Kevlar, was thicker on the top and bottom to absorb the constant bending motions that occurred during flight. Under-wing pods were attached to carry the landing gear, battery backup system, fuel cells, flight control computers, and data instruments. The Helios flight control surfaces consisted of 72 trailing-edge elevators that provided pitch control. The fixed landing gear consisted of two wheels on each pod.[1553]
At an October 13, 1999, flight demonstration at the Dryden Flight Center, Ray Morgan—vice president of AeroVironment, which developed the Helios—noted that the ultimate intention is for Helios-type UAVs to "stay in the stratosphere for months at a time and act as an 11-mile-high tower.” Morgan added that the Helios had a "very unique, slow, and stable flight characteristic. . . that means we can fly in fairly tight circles and be, essentially, a geo-stationary platform in the sky— and that has lots of potential application.”[1554] Some of commercial tasks envisioned for future solar-powered HALE aircraft to follow the Helios Prototype were storm tracking studies, atmospheric sampling, spectral imaging for agricultural and natural resource purposes, pipeline mon-
itoring, and telecommunications platforms. Morgan further noted that reliability of the Helios was obtained in two ways: simplicity, because the UAV is simply a flying wing, and redundancy. Each motor pylon turned 2 horsepower into 10 pounds of thrust. There was only one moving part in each pylon. There were no brushes, gearboxes, or mechanism for variation in the pitch required to operate the UAV.[1555] Furthermore, while the Helios had 72 elevators, the UAV could use differential thrust to turn the aircraft without use of the elevators.
The Helios HP03 long-endurance configuration, which included a hydrogen-air fuel cell pod, made its first high-altitude flight June 7, 2003. The test objectives of this flight were: (1) to demonstrate the readiness of the aircraft systems, flight support equipment and instrumentation, and flight procedures; (2) to validate the handling and aeroelastic stability of the aircraft; (3) to demonstrate the operation of the fuel cell system and gaseous hydrogen storage tanks; and (4) to provide training for personnel to staff future multiday flights. The flight was planned to be a 30-hour endurance flight, but because of leakage in the coolant and compressed air line, the flight had to be aborted after 15 hours. Flight data, however, verified that the vehicle was aeroelastically stable under the flight conditions expected for the long-endurance flight demonstration.
On its second test flight, on June 26, 2003, following further modifications based on the first flight, the Helios prototype crashed on the Navy’s Pacific Missile Range Facility in Hawaii. This flight was intended to evaluate the vehicle’s hydrogen fuel cell system designed to power the UAV during periods of darkness, which would be necessary for long – duration flights. Approximately 30 minutes into its flight and at an altitude of only 2,800 feet, the aircraft encountered turbulence and morphed into a high dihedral (wings upswept) configuration that, over time, took on an increasingly alarming U-like appearance. This caused Helios to become unstable in pitch, and the big UAV began to nose up and down. During one descending swoop, the big UAV exceeded its maximum permissible airspeed, causing the wing’s leading edge secondary structure on the outer panels to fail and the solar cells and skin on the upper surface to rip off. Shedding bits and pieces of structure, the Helios progressively disintegrated as it plunged downward, being destroyed when it impacted the ocean.[1556]
The Mishap Investigation Board (MIB) concluded that: "In summary, there was no evidence that suggests that there was prior structural failure(s) that would have contributed to the vehicle developing the higher-than-normal dihedral deflections [wing upsweep] that caused the unstable pitch oscillation and subsequent failure of the vehicle.”[1557] The report, in noting the lessons learned, identified both the proximate and root causes of the loss of Helios. The proximate cause of the crash was determined to be the "high dynamic pressure reached by the aircraft during the last cycle of the unstable pitch oscillation leading to failure of the vehicle’s secondary structure.” Two root causes, however, that contributed to or created the proximate cause of the accident were: (1) the lack of adequate analysis methods, which led to an inaccurate risk assessment of the effects of the configuration change from the HPO1 (high altitude) to the HPO3 (long endurance) version of the Helios and (2) configuration changes to the aircraft, which altered the Helios from a spanloader to a highly point-loaded mass distribution on the same structure, significantly reducing design robustness and margins of safety.[1558]
The report noted that the Helios UAV represented "a nonlinear stability and control problem involving complex interactions among the flexible structure, unsteady aerodynamics, flight control system, propulsion system, the environmental conditions, and vehicle flight dynamics.” As a result of the investigation, the MIB made a number of key recommendations for future UAV development. These included:
1. Develop more advanced, multidisciplinary "time – domain” analysis methods appropriate to highly flexible, "morphing” vehicles;
2. Develop ground-test procedures and techniques appropriate to UAV class vehicles to validate new analysis methods and predictions;
3. Improve the technical insight for highly complex projects, using the expertise available from all NASA Research Centers;
4. Develop multidisciplinary models, which can describe the nonlinear dynamic behavior of aircraft modifications or perform incremental flight-testing; and
5. Provide adequate resources to future programs for more incremental flight-testing when large configuration changes significantly deviate from the initial design concept.
As already noted, because of budget constraints, the NASA-industry team basically had to use one prototype vehicle for two tests: high altitude and long endurance. Adding to this factor, as noted in the MIB report, the switch from a regenerative fuel cell to a hydrogen-air fuel cell, which was necessitated by technical problems with the RFCS, combined with project time and budget deadlines, caused a critical change in the load factor on the wing structure. The hydrogen-air fuel cell system was more point loaded because of having to use a third pod at the centerline of the vehicle to hold the 520-pound primary hydrogen-air fuel cell. The originally planned for regenerative fuel cell system would have required only two pods, each one-third of the distance from the vehicle’s centerline to the wingtip.[1559]
Even with the loss of the Helios Prototype, the MIB noted both the success and the challenge of the solar UAV program, as reflected in the following statement from the Mishap report:
During the course of this investigation the MIB discovered that the AV [AeroVironment]/NASA technical team had created most of the world’s knowledge in the area of High Altitude – Long Endurance (HALE) aircraft design, development, and test. This has placed the United States in a position of world leadership in this class of vehicle, which has significant strategic implications for the nation. The capability afforded by such vehicles is real and unique, and can enable the use of the stratosphere for many government and commercial applications. The MIB also found that this class of vehicle is orders of magnitude more complex than it appears but that the AV/ NASA technical team had identified and solved the toughest technical problems. Although more knowledge can and should be pursued as recommended in this report, an adequate knowledge base now exists to design, develop, and deploy operational HALE systems.[1560]
ERAST Program Overview and Accomplishments
The ERAST program, which started in 1994 and ended in 2003, following the loss of the Helios Prototype, accomplished almost all of its primary objectives, including development of a solar-powered UAV capable of flying at very high altitudes; demonstrating payload capabilities and sensors for atmospheric research; resolving solar-powered UAV operational issues; and demonstrating UAV’s usefulness to scientific, Government, and civil customers. The ERAST program also demonstrated that the unique joint NASA-industry ERAST alliance under a Joint Sponsored Research Agreement worked well and that good cooperation under this agreement led to efficient use of resources and expedited reaching the project milestones required to satisfy the program’s budget and time constraints. In regard to the alliance partner manufacturing the solar cells for the four generations of solar-powered UAV s, SunPower Corporation was able to make significant increases in efficiency and lower the cost of its commercial solar cells, which led to its successful mass-produced series A-300 solar cells. The one primary objective that remained unfulfilled at the close of the ERAST NASA-industry program was obtaining the long-endurance capability to fly for multiple days or longer. As with the earlier solar UAV program in the 1980s, a backup power system that would enable solar UAVs to fly in periods of darkness remained the critical problem to be solved. Significant progress in this area, however, was made and work continued at NASA Glenn under the Low Emissions Alternative Power (LEAP) program on the goal of perfecting a lightweight regenerative fuel cell system. NASA Glenn made its first closed-loop (system completely sealed) regenerative fuel cell demonstration in September 2003 and demonstrated five contiguous back-to-back charge-discharge cycles at full power under semiautonomous control in July 2005.[1561]
[1] Peter W. Brooks, The Modern Airliner: Its Origins and Development (London: Putnam & Co., Ltd., 1961), pp. 91-111. Brooks uses the term to describe a category of large airliner and transport aircraft defined by common shared design characteristics, including circular cross-section constant-diameter fuselages, four-engines, tricycle landing gear, and propeller-driven (piston and turbo-propeller), from the DC-4 through the Bristol Britannia, and predominant in the time period 1942 through 1958. Though some historians have quibbled with this, I find Brooks’s reasoning convincing and his concept of such a "generation’ both historically valid and of enduring value.
[2] Quoted in Roy A. Grossnick, et al., United States Naval Aviation 1910-1995 (Washington: U. S. Navy, 1997), p. 15; Gordon Swanborough and Peter M. Bowers, United States Navy Aircraft Since 1911 (New York: Funk & Wagnalls, 1968), p. 394.
[3] Alexander Lippisch, "Recent Tests of Tailless Airplanes," NACA TM-564 (1930), a NACA translation of his article "Les nouveaux essays d’avions sans queue," l’Aerophile (Feb. 1-15, 1930), pp. 35-39.
[4] For Volta, see Theodore von Karman and Lee Edson, The Wind and Beyond: Theodore von Kdrmdn, Pioneer in Aviation and Pathfinder in Space (Boston: Little, Brown and Co., 1967), pp. 216-217, 221-222; Adolf Busemann, "Compressible Flow in the Thirties," Annual Review of Fluid Mechanics, vol. 3 (1971), pp. 6-1 1; Carlo Ferrari, "Recalling the Vth Volta Congress: High Speeds in Aviation," Annual Review of Fluid Mechanics, vol. 28 (1996), pp. 1-9; Hans-Ulrich Meier, "Histo – rischer Ruckblick zur Entwicklung der Hochgeschwindigkeitsaerodynamik," in H.-U. Meier, ed., Die Pfeilflugelentwicklung in Deutschland bis 1945 (Bonn: Bernard & Graefe Verlag, 2006), pp. 16-36; and Michael Eckert, The Dawn of Fluid Dynamics: A Discipline Between
Science and Technology (Weinheim: WileyVCH Verlag, 2006), pp. 228-231.
[5] Adolf Busemann, "Aerodynamische Auftrieb bei Uberschallgeschwindigkeit," Luflfahrlforschung, vol. 1 2, No. 6 (Oct. 3, 1935), pp. 210-220, esp. Abb. 4-5 (Figures 4-5).
[6] Theodore von Karman, Aerodynamics (New York: McGraw-Hill Book Company, Inc., 1963 ed.), p. 1 33.
[7] Ministero dell’Aeronautica, 1 ° Divisione, Sezione Aerodinamica Resultati di Esperienze (Rome: Guidonia, 1936); the swept "double-ender" wind tunnel study (anticipating the layout of Dornier’s Do 335 Pfeil ["Arrow"] of the late wartime years) was designated the J-1 0; its drawing is dated March 7, 1936. I thank Professor Claudio Bruno of the Universita degli Studi di Roma "La Sapi – enza"; and Brigadier General Marcello di Lauro and Lieutenant Colonel Massimiliano Barlattani of the Stato Maggiore dell’Aeronautica Militare (SMdAM), Rome, for their very great assistance in enabling me to examine this study at the Ufficio Storico of the SMdAM in June 2009.
[8] Raymond F. Anderson, "Determination of the Characteristics of Tapered Wings," NACA Report No. 572 (1936); see in particular Figs. 15 and 16, p. 11.
[9] For an example of such work, see Dr. Richard Lehnert, "Bericht uber Dreikomponentenmessungen mit den Gleitermodellen A4 V12/a und A4 V1 2/c," Archiv Nr 66/34 (Peenemunde: Heeres – Versuchsstelle, Nov. 27, 1940), pp. 6-10, Box 674, "C10/V-2/History" file, archives of the National Museum of the United States Air Force, Dayton, OH. Re: German research deficiencies, see Adolf Baeumker, Ein Beitrag zur Geschichte der Fuhrung der deutschen Luftfahrttechnik im ersten halben Jahrhun dert, 1900-1950 (Bad Godesberg: Deutschen Forschungs – und Versuchsanstalt fur Luft – und Raumfahrt e. V., 1971), pp. 61-74; Col. Leslie E. Simon, German Scientific Establishments (Washington: Office of Technical Services, Department of Commerce, 1947), pp. 7-9; Helmuth Trischler, "Self-Mobilization or Resistance? Aeronautical Research and National Socialism," and Ulrich Albrecht, "Military Technology and National Socialist Ideology," in Monika Renneberg and Mark Walker, eds., Science, Technology, and National Socialism (Cambridge: Cambridge University Press, 1994), pp. 72-1 25. For science and the Third Reich more generally, see Alan D. Beyerchen, Scientists Under Hitler: Politics and the Physics Community in the Third Reich (New Haven: Yale University Press, 1977); and Kristie Macrakis, Surviving the Swastika: Scientific Research in Nazi Germany (New York: Oxford University Press, 1993).
[10] USAAF, "German Aircraft, New and Projected Types" (1946), Box 568, "A-1A/Germ/1945 file, NMUSAF Archives; and J. McMasters and D. Muncy, "The Early Development of Jet Propelled Aircraft," AIAA Paper 2007-0151, Pts. 1-2 (2007).
1 1 . See Richard P. Hallion, "Lippisch Gluhareff, and Jones: The Emergence of the Delta Planform and the Origins of the Sweptwing in the United States," Aerospace Historian, vol. 26, no. 1 (Mar. 1979), pp. 1-10.
[12] Memo, Michael Gluhareff to 1.1. Sikorsky, July 1941, copy in the Gluhareff Dart accession file, National Air and Space Museum, Smithsonian Institution, Washington, DC. Gluhareff’s Dart appeared contemporaneously with a remarkably similar (though with a tractor propeller) Soviet design by Alexandr Sergeevich Moskalev. Though unclear, it seems Gluhareff first conceived the planform. It is possible that an informal interchange of information between the two occurred, as Soviet aeronautics and espionage authorities kept close track of American developments and the activities of the emigree Russian community in America.
1 3. Griswold is best known as coinventor (with Hugh De Haven) of the three-point seat restraint, which formed the basis for the modern automotive seat belt; Saab then advanced further, building upon their work. See "Three-Point Safety Belt is American, not Swedish, Invention,’ Status Report, vol. 35, no. 9 (Oct. 21, 2000), p. 7.
[14] Vought-Sikorsky, "Aerodynamic Characteristics of the Preliminary Design of a 1/20 Scale Model of the Dart Fighter,’ Vought-Sikorsky Wind Tunnel Report No. 192 (Nov. 1 8, 1942), copy in the Gluhareff Dart accession file, National Air and Space Museum, Smithsonian Institution, Washington, DC.
[15] Letter, Roger W. Griswold to Maj. Donald R. Eastman, Oct. 22, 1 946, Gluhareff Dart accession file, NASM.
[16] M. E. Gluhareff, "Tailless Airplane,’ U. S. patent No. 2,51 1,502, issued June 1 3, 1950; "Sikorsky Envisions Supersonic Airliner,” Aviation Week (May 4, 1959), pp. 67-68; M. E. Gluhareff, "Aircraft with Retractable Auxiliary Airfoil,’ U. S. patent No. 2,941,752, issued June 21, 1960.
[17] See William Sears’s biographical introduction to the "Collected Works of Robert T. Jones,’ NASA TM-X-3334 (1976), pp. vii-ix; and Walter G. Vincenti, "Robert Thomas Jones,’ in Biographical Memoirs, vol. 86 (Washington: National Academy of Sciences, 2005), pp. 3-21.
1 8. Transcript of interview of R. T. Jones by Walter Bonney, Sept. 24, 1 974, p. 5, in Jones biographical file, No. 001 147, Archives of the NASA Historical Division, National Aeronautics and Space Administration, Washington, DC.
[19] Transcript of Jones-Bonney interview, p. 5; Hallion conversation with Dr. Robert T. Jones at NASA Ames Research Center, Sunnyvale, CA, July 14, 1977; Max M. Munk, "The Aerodynamic Forces on Airship Hills, NACA Report No. 1 84 (1923); Max M. Munk, "Note on the Relative Effect of the Dihedral and the Sweep Back of Airplane Wings," NACA TN-177 (1924); H. S. Tsien, "Supersonic Flow Over an Inclined Body of Revolution," Journal of the Aeronautical Sciences, vol. 5, no. 2 (Oct. 1938), pp. 480-483.
[20] Note that although Lippisch called his tailless aircraft "deltas’ as early as 1 930, in fact they were generally broad high aspect ratio wings with pronounced leading edge taper, akin to the wing planform of America’s classic DC-1/2/3 airliners. During the Second World War, Lippisch did develop some concepts for sharply swept deltas (though of very thick and impracticable wing section). Taken all together, Lippisch’s deltas, whether of high or low aspect ratio planform, were not comparable to the thin slender and sharply swept (over 60 degrees) deltas of Jones, and Gluhareff before him, or Dietrich Kuchemann at the Royal Aircraft Establishment afterwards, which were more akin to high-supersonic and hypersonic shapes of the 1950s-1960s.
[21] For DM-1 and extrapolative tests, see Herbert A. Wilson, Jr., and J. Calvin Lowell, "Full-Scale Investigation of the Maximum Lift and Flow Characteristics of an Airplane Having Approximately Triangular Plan Form,’ NACA RM-L6K20 (1947); J. Calvin Lovell and Herbert A. Wilson, Jr., "Langley Full-Scale-Tunnel Investigation of Maximum Lift and Stability Characteristics of an Airplane Having Approximately Triangular Plan Form (DM-1 Glider),’ NACA RM-L7F16 (1947); and Edward F. Whittle, Jr., and J. Calvin Lovell, "Full-Scale Investigation of an Equilateral Triangular Wing Having 10-Percent-Thick Biconvex Airfoil Sections,’ NACA RM-L8G05 (1948).
[22] In 1944, Kotcher had conceived a rocket-powered "Mach 0.999" transonic research airplane (a humorous reference to the widely accepted notion of an "impenetrable" sonic "barrier") that subsequently inspired the Bell Aircraft Corporation to undertake design of the XS-1, the world’s first supersonic manned airplane.
[23] Kantrowitz would pioneer high-Mach research facilities design, and Soule would serve the NACA as research airplane projects leader, supervising the Agency’s Research Airplane Projects Panel (RAPP), a high-level steering group coordinating the NACA’s X-series experimental aircraft programs.
[24] Memo, Jones to Lewis, Mar. 5, 1945; see also ltr., Jones to Ernest O. Pearson, Jr., Feb. 2, 1960, and Navy/NACA Record of Invention Sheet, Apr. 10, 1946, Jones biographical file, NASA.
[25] Robert T. Jones, "Properties of Low-Aspect-Ratio Pointed Wings at Speeds Below and Above the Speed of Sound," NACA TN-1032 (1946), p. 1 1 [first issued at NACA LMAL on May 11, 1945].
[26] For Millikan visit to Germany, see Millikan Diary 6, Box 35, Papers of Clark B. Millikan, Archives, California Institute of Technology, Pasadena, CA; Alexander Lippisch, ltr. to editor, Aviation Week and Space Technology (Jan. 6, 1975); in 1977, while curator of science and technology
at the National Air and Space Museum, the author persuaded Jones to donate his historic delta test model to the museum; he had been using it for years as a letter opener!
[27] Jones noted afterward that at Volta, Busemann "didn’t have the idea of getting the wing inside the Mach cone so you got subsonic flow. The real key to [the swept wing] was to get subsonic flow at supersonic speed by getting the wing inside the Mach cone. . . the development of what I would say [was] the really correct sweep theory for supersonic speeds occurred in Germany in ’43 or ’44, and with me in 1945.’ (See transcript of Jones-Bonney interview, p. 6). But German researchers had mastered it earlier, as evident in a series of papers and presentations in a then-"Geheim" ("Secret”) conference report by
the Lilienthal-Gesellschaft fur Luftfahrtforschung, Allgemeine Stromungsforschung: Bericht uber die Sitzung Hochgeschwindigkeitsfragen am 29 und 30 Oktober 1942 in Berlin (Berlin: LGF, 1942).
[28] For his report, see Robert T. Jones, "Wing Planforms for High-Speed Flight,’ NACA TN-1033 (1946) [first issued at LMAL on June 23, 1945, as Confidential Memorandum Report L5F21 ]. Jones’s tortuous path to publication is related in James R. Hansen’s Engineer in Charge: A History of the Langley Aeronautical Laboratory, 1917-1958, SP-4305 (Washington: NASA, 1987), pp. 284-285.
[29] Jones, "Wing Planforms for High-Speed Flight," NACA TN-1033, p. 1.
[30] For the United States, this meant that Soviet intelligence collectors increasingly focused on American high-speed research. Bell Aircraft Corporation, manufacturer of the first American jet airplane, the first supersonic airplane, and advanced swept wing testbeds (the X-2 and X-5), figured prominently as a Soviet collection target as did the NACA. NACA engineer William Perl (born Mutterperl), a member of the Rosenberg spy ring who passed information on aviation and jet engines to Soviet intelligence, worked as a postwar research assistant for Caltech’s Theodore von Karman, director of the Guggenheim Aeronautical Laboratory of the California Institute of Technology (GALCIT), the Nation’s premier academic aero research facility. He cultivated a close bond with TvK’s sister Josephine ("Pipa") and TvK himself. Perl had almost unique access to the highest-level NACA and GALCIT reports on high-speed flight, and the state of advanced research and facilities planning for them and the U. S. Air Force. He associated as well with NACA notables, including Arthur Kantrowitz, Eastman Jacobs, and Robert T. Jones. So closely was he associated with von Karman that he once helpfully reminded him where to find the combination to an office safe! He helped screen sensitive NACA data for a presentation TvK was making on high-speed stability and control, and TvK recommended Perl for consultation on tunnel development at the proposed new Arnold Engineering Development Center (AEDC) in Tennessee. Perl was unmasked by the Venona signals intelligence decryption program, interrogated on his associations with known Communists, and subsequently arrested and convicted of perjury. (He had falsely denied knowing the Rosenbergs.) More serious espionage charges were not brought, lest court proceedings compromise the ongoing Venona collection effort. The Papers of Theodore von Karman, Box 31, Folder 31.38, Archives of the California Institute of Technology, and the Federal Bureau of Investigations’ extensive Perl documentation contain much revealing correspondence on Perl and his associates. I thank Ernest Porter and the FBI historical office for arranging access to FBI material. See also Katherine A. S. Sibley, Red Spies in America: Stolen Secrets and the Dawn of the Cold War (Lawrence: University Press of Kansas, 2004); and John Earl Haynes and Harvey Klehr’s Early Cold War Spies: The Espionage Trials that Shaped American Politics (Cambridge: Cambridge University Press, 2006) for further details on the Perl case.
[31] . George W. Gray, Frontiers of Flight: The Story of NACA Research (New York: Knopf, 1 948), p. 348.
[32] Re: German high-speed influence in the U. S., Britain, and Russia, see H. S. Tsien, "Reports on the Recent Aeronautical Developments of Several Selected Fields in Germany and Switzerland,’ in Theodore von Karman, ed., Where We Stand: First Report to General of the Army H. H. Arnold on Long Range Research Problems of the Air Forces with a Review of German Plans and Developments (Washington: HQ AAF, Aug. 22, 1945), Microfilm Reel 194, Papers of Gen. Henry H. Arnold, Manuscript Division, U. S. Library of Congress, Washington, DC; Ronald Smelt, "A Critical Review of German Research on High-Speed Airflow,’ Journal of the Royal Aeronautical Society, vol. 50,
No. 432 (Dec. 1946), pp. 899-934; Andrew Nahum, "I Believe the Americans Have Not Yet Taken Them All!’ in Helmuth Trischler, Stefan Zeilinger, Robert Bud, and Bernard Finn, eds., Tackling Transport (London: Science Museum, 2003), pp. 99-1 38; Matthew Uttley, "Operation ‘Sturgeon’ and Britain’s Post-War Exploitation of Nazi German Aeronautics,’ Intelligence and National Security, vol. 17, no. 2 (Sum. 2002), pp. 1-26; M. I. Gurevich, "O Pod’emnoi Sile Strelovidnogo Kryla v Sverkhzvukovom Potoke,’ Prikladnaya Matematika i Mekhanika, vol. 10 (1946), translated by the NACA as "Lift Force of an Arrow-Shaped Wing,’ NACA TM-1 245 (1949). Gurevich, cofounder of the MiG bureau (he is the "G" in "MiG’) was subsequently principal aerodynamicist of the MiG – 15, the Soviet Union’s swept wing equivalent to the American F-86. For a detailed examination
of F-86 wing development and the influence of German work (particularly Gothert’s) upon it, see Morgan M. Blair, "Evolution of the F-86,’ AIAA Paper 80-3039 (1980).
[33] Pitch-up was of such significance that it is discussed subsequently in greater detail within this essay.
[34] First comprehensively analyzed by Max M. Munk in his "Note on the Relative Effect of the Dihedral and the Sweep Back of Airplane Wings,’ NACA TN-177 (1924).
[35] See John E. Steiner, "Transcontinental Rapid Transit: The 367-80 and a Transport Revolution — The 1953-1978 Quarter Century," AIAA Paper 78-3009 (1978), p. 93; John E. Steiner, "Jet Aviation Development: A Company Perspective," in Walter J. Boyne and Donald H. Lopez, eds., The Jet Age: Forty Years of Jet Aviation (Washington: Smithsonian Institution Press, 1979), pp. 145-148; and William H. Cook, The Road to the 707: The Inside Story of Designing the 707 (Bellevue, WA: TYC Publishing Co., 1991), pp. 145-205.
[36] See, for example, Richard T. Whitcomb, "An Investigation of the Effects of Sweep on the Characteristics of a High-Aspect-Ratio Wing in the Langley 8-Ft. High Speed Tunnel,’ NACA RM-L6J01 a (1947), conclusion 4, p. 19; Stephen Silverman, "The Next 25 Years of Fighter Aircraft,’ AIAA Paper No. 78-301 3 (1978); Glen Spacht, "X-29 Integrated Technology Demonstrator and ATF,’ AIAA Paper No. 83-1058 (1983).
[37] A. M. "Tex’ Johnston with Charles Barton, Tex Johnston: Jet-Age Test Pilot (Washington: Smithsonian Institution Press, 1991), p. 1 05. The designation "L-39” could be taken to imply that the swept wing testbeds were modifications of Bell’s earlier and smaller P-39 Airacobra. In fact, it was coincidence; the L-39s were P-63 conversions, as is evident from examining photographs of the
two L-39 aircraft.
[38] Corwin H. Meyer, Corky Meyer’s Flight Journal: A Test Pilot’s Tales of Dodging Disasters—Just in Time (North Branch, MN: Specialty Press, 2006), p. 193.
[39] NACA’s L-39 trials are covered in three reports by S. A. Sjoberg and J. P. Reeder: "Flight Measurements of the Lateral and Directional Stability and Control Characteristics of an Airplane Having a 35° Sweptback Wing with 40-Percent-Span slots and a Comparison with Wind-Tunnel Data,’ NACA TN-151 1 (1948); "Flight Measurements of the Longitudinal Stability, Stalling, and Lift Characteristics of an Airplane Having a 35° Sweptback Wing Without Slots and With 40-Percent-Span Slots and a Comparison with Wind-Tunnel Data,’ NACA TN-1679 (1948); and "Flight Measurements of the Stability, Control, and Stalling Characteristics of an Airplane Having a 35° Sweptback Wing Without Slots and With 80-Percent-Span Slots and a Comparison with Wind-Tunnel Data,’ NACA TN-1743 (1948). The American L-39s were matched by foreign equivalents, most notably in Sweden, where the Saab company flew a subscale swept wing variant of its conventional Safir light aircraft, designated the Saab 201, to support development of its J29 fighter, Western Europe’s first production swept wing jet, which first flew in Sept. 1948. Like both the F-86 and MiG-15, it owed its design largely to German inspiration. Saab researchers were so impressed with what they had learned from the 201 that they subsequently flew another modified Safir, the Saab 202, with
a more sharply swept wing planform intended for the company’s next jet fighter, the J32 Lansen (Lance). See Hans G. Andersson, Saab Aircraft Since 1937 (Washington: Smithsonian Institution Press, 1989), pp. 106, 117.
[40] XP-86 test report, May 21, 1948, reprinted in Roland Beamont, Testing Early Jets: Compressibility and the Supersonic Era (Shrewsbury: Airlife, 1 990), p. 36. Beamont’s achievement remained largely secret; the first British pilot to fly through the speed of sound in a British airplane was John Derry, who did so in Sept. 1948.
41 . Quote from Nigel Walpole, Swift Justice: The Full Story of the Supermarine Swift (Barnsley, UK: Pen & Sword Books, 2004), p. 38.
[42] Charles Burnet, Three Centuries to Concorde (London: Mechanical Engineering Publications Ltd., 1979), pp. 121, 123.
[43] Michael Collins, Carrying the Fire: An Astronaut’s Journeys (New York: Farrar, Straus, and Giroux, 1 974), p. 9. Another Sabre veteran who went through Nellis at the same time recalled to the author how he once took off on a training sortie with ominous columns of lingering smoke from three earlier Sabre accidents.
[44] For development of control boost, artificial feel, and control limiting, see Robert G. Mungall, "Flight Investigation of a Combined Geared Unbalancing-Tab and Servotab Control System as Used with an All-Movable Horizontal Tail,’ NACA TN-1 763 (1 948); William H. Phillips, "Theoretical Analysis of Some Simple Types of Acceleration Restrictors,’ NACA TN-2574 (1951); R. Porter Brown, Robert G. Chilton, and James B. Whitten, "Flight Investigation of a Mechanical Feel Device in an Irreversible Elevator Control System of a Large Airplane,’ NACA Report No. 1 101 (1952); James J. Adams and James B. Whitten, "Tests of a Centering Spring Used as an Artificial Feel Device on the Elevator of a Fighter Airplane,’ NACA RM-L52G16; and Marvin Abramovitz, Stanley F. Schmidt, and Rudolph D. Van Dyke, Jr., "Investigation of the Use of a Stick Force Proportional to Pitching Acceleration for Normal-Acceleration Warning,’ NACA RM-A53E21 (1953).
[45] George E. Cooper and Robert C. Innis, "Effect of Area-Suction-Type Boundary-Layer Control on the Landing-Approach Characteristics of a 35° Swept-Wing Fighter,’ NACA RM-A55K14 (1957), p. 11. Other relevant Ames F-86 studies are: George A. Rathert, Jr., L. Stewart Rolls, Lee Wino – grad, and George E. Cooper, "Preliminary Flight Investigation of the Wing-Dropping Tendency and Lateral-Control Characteristics of a 35° Swept-Wing Airplane at Transonic Mach Numbers,’ NACA RM-A50H03 (1950); and George A. Rathert, Jr., Howard L. Ziff, and George E. Cooper, "Preliminary Flight Investigation of the Maneuvering Accelerations and Buffet Boundary of a 35° Swept-Wing Airplane at High Altitude and Transonic Speeds,’ NACA RM-A50L04 (1951).
[46] Edwin P. Hartman, Adventures in Research: A History of the Ames Research Center, 19401965, SP-4302 (Washington: NASA 1970), p. 252.
[47] A. Scott Crossfield with Clay Blair, Always Another Dawn: The Story of a Rocket Test Pilot (Cleveland: World Publishing Co., 1960), pp. 193-194. See also W. C. Williams and A. S. Crossfield, "Handling Qualities of High-Speed Airplanes,’ NACA RM-L52A08 (1952), p. 3; Melvin Sadoff, John D. Stewart, and George E. Cooper, "Analytical Study of the Comparative Pitch-Up Behavior of Several Airplanes and Correlation with Pilot Opinion,’ NACA RM-A57D04 (1957).
[48] Sadoff, Stewart, and Cooper, "Analytical Study of Comparative Pitch-Up Behavior,’ p. 1 2.
[49] S. A. Mikoyan, Stepan Anastasovich Mikoyan: An Autobiography (Shrewsbury: Airlife, 1999), p. 289.
[50] Maj. Gen. H. E. "Tom’ Collins, USAF (ret.), "Testing the Russian MiG,’ in Ken Chilstrom, ed., Testing at Old Wright Field (Omaha: Westchester House Publishers, 1991), p. 46.
51 . Two not so taken with the swept tailless configuration were Douglas aerodynamicist L. Eugene Root and former Focke-Wulf aerodynamicist Hans Multhopp. After an inspection trip to Messerschmitt in August 1945, Root wrote "a tailless design suffers a disadvantage of small allowable center of gravity travel. . . . Although equally good flying qualities can be obtained in either [tailless or conventional] case, the tailless design is considered more dangerous at very high speeds. For example, the Me 262 has been taken to a Mach number of 0.86 without serious difficulty, whereas the Me 163 could not exceed M = 0.82. For the Me 163 . . . it was not considered possible fundamentally to control the airplane longitudinally past M = 0.82 in view of a sudden diving moment and complete loss of elevator effectiveness.’ See L. E. Root, "Information of Messerschmitt Aircraft Design,’ Item Nos. 5, 25, File No. XXXII-37, Copy 079 (Aug. 1945), p. 3, Catalog D52.1Messerschmitt/144, in the Wright Field Microfilm Collection, National Air and Space Museum Archives, Paul E. Garber Restoration Facility, Silver Hill, MD. Focke-Wulf’s Hans Multhopp, designer of the influential T-tail sweptwing Ta 183, was even more dismissive. After the war, while working at the Royal Aircraft Establishment, he remarked that it constituted an "awful fashion;’ see Nahum, "I Believe. . .,’ in Trischler, et al., ed., Tackling Transport, p. 118. Multhopp later came to America, joining Martin and designing the SV-5 reentry shape that spawned the SV-5D PRIME, the X-24A, and the X-38.
[52] Burnet, Three Centuries to Concorde, p. 102.
[53] Crossfield with Blair, Always Another Dawn, p. 39; Melvin Sadoff and Thomas R. Sisk, "Longitudinal-Stability Characteristics of the Northrop X-4 Airplane (USAF No. 46-677)," NACA RM-A50D27 (1950); and Williams and Crossfield, "Handling Qualities of High-Speed Airplanes."
[54] Quote from Walpole, Swift Justice, pp. 58, 66. Walpole, a former Swift pilot, writes affectionately but frankly of its strengths and shortcomings. See also Burnet, Three Centuries to Concorde, pp. 1 27-1 28. Burnet was involved in analyzing Swift performance, and his book is an excellent review of Supermarine and other British efforts at this time.
[55] For the origins of the D-558 program, see Richard P. Hallion, Supersonic Flight: Breaking the Sound Barrier and Beyond—The Story of the Bell X-1 and Douglas D-558 (New York: The Macmillan Co. in association with the Smithsonian Institution, 1972).
[56] Particularly Bernard Gothert’s "Hochgeschwindigkeitmessungen an einem Pfeilflugel (Pfeilwin – kel ф = 35°),’ in the previously cited Lilienthal-Gesellschaft, Allgemeine Stromungsforschung, pp. 30-40, subsequently translated and issued by the NACA as "High-Speed Measurements on a Swept-Back [sic] Wing (Sweepback Angle ф = 35°),’ NACA TM-1 102 (1947), which directly influenced design of the 35-degree swept wings employed on the F-86, the B-47, and the D-558-2. Gothert, incidentally, used NACA airfoil sections for his studies, another example of the Agency’s pervasive international influence. At war’s end he was in Berlin; when ordered to report to Russian authorities, he instead fled the city, making his way back to Gottingen, where he met Douglas engineer Apollo M. O. Smith, with the Naval Technical Mission to Europe. Smith arranged for him to immigrate to the United States, where he had a long and influential career, rising to Chief Scientist of Air Force Systems Command, a position he held from 1964 to 1966. See Tuncer Cebeci, ed., Legacy of a Gentle Genius: The Life of A. M.O. Smith (Long Beach: Horizons Publishing, Inc.,
1999), p. 32. I acknowledge with grateful appreciation notes and correspondence received from members of the D-558 design team in 1971-1972, including the late Edward Heinemann,
L. Eugene Root, A. M.O. Smith, Kermit Van Every, and Leo Devlin, illuminating the origins of the Skystreak and Skyrocket programs.
[57] Hallion, Supersonic Flight, pp. 151-152, based upon D-558 biweekly progress reports. As well, I thank the late Robert Champine for his assistance to my research. See also S. A. Sjoberg and R. A. Champine, "Preliminary Flight Measurements of the Static Longitudinal Stability and Stalling Characteristics of the Douglas D-558-II Research Airplane (BuAero No. 37974),’ NACA RM – L9H31a (1949); W. H. Stillwell, J. V. Wilmerding, and R. A. Champine, "Flight Measurements with the Douglas D-558-II (BuAero No. 37974) Research Airplane Low-Speed Stalling and Lift Characteristics,’ NACA RM-L50G10 (1950).
[58] Jack Fischel and Jack Nugent, "Flight Determination of the Longitudinal Stability in Accelerated Maneuvers at Transonic Speeds for the Douglas D-558-II Research Airplane Including the Effects of an Outboard Wing Fence," NACA RM-L53A16 (1953); Jack Fischel, "Effect of Wing Slats and Inboard Wing Fences on the Longitudinal Stability Characteristics of the Douglas D-558-II Research Airplane in Accelerated Maneuvers at Subsonic and Transonic Speeds," NACA RM-L53L16 (1954); Jack Fischel and Cyril D. Brunn, "Longitudinal Stability Characteristics in Accelerated Maneuvers at Subsonic and Transonic Speeds of the Douglas D-558-II Research Airplane Equipped with a Leading-Edge Wing Chord-Extension," NACA RM-H54H16 (1954); M. J. Queijo, Byron M. Jaquet, and Walter D. Wolmart, "Wind-Tunnel Investigation at Low Speed of the Effects of Chord – wise Wing Fences and Horizontal-Tail Position on the Static Longitudinal Stability Characteristics of an Airplane Model with a 35° Sweptback Wing," NACA Report 1 203 (1954); Jack Fischel and Donald Reisert, "Effect of Several Wing Modifications on the Subsonic and Transonic Longitudinal Handling Qualities of the Douglas D-558-II Research Airplane," NACA RM-H56C30 (1956).
[59] Robert O. Rahn, "XF4D Skyray Development: Now It Can Be Told,’ 22nd Symposium, Society of Experimental Test Pilots, Beverly Hills, CA, Sept. 30, 1978; and Edward H. Heinemann and Rosario Rausa, Ed Heinemann: Combat Aircraft Designer (Annapolis: Naval Institute Press, 1980), p. 192. Years later, another Skyray pilot at the Naval Air Test Center experienced a similar mishap, likewise making a near-miraculous recovery; the plane was so badly stressed that it never flew again.
[60] Meyer, Flight Journal, pp. 1 96-198; he was nearly killed on one low-altitude low-speed pitch-up that ended in a near-fatal spin. The Cougar’s approach behavior resulted in a Langley research program flown using a F9F-7 variant, which highlighted the need for more powerful, responsive, and controllable aircraft, such as the later McDonnell F4H-1 Phantom II. See Lindsay J. Lina, Garland J. Morris, and Robert A. Champine, "Flight Investigation of Factors Affecting the Choice of Minimum Approach Speed for Carrier-Type Landings of a Swept-Wing Jet Fighter Airplane,’ NACA RM-L57F1 3 (1957).
61 . Robert C. Little, "Voodoo! Testing McAir’s Formidable F-101,’ Air Power History, vol. 41, no.
1 (spring 1 994), pp. 6-7. In Britain, designer George Edwards likewise added anhedral (though more modest than the Phantom’s) to the Supermarine Scimitar, another pitch-up plagued swept wing fighter. See Robert Gardner, From Bouncing Bombs to Concorde: the Authorised Biography of Aviation Pioneer Sir George Edwards OM (Stroud, UK: Sutton Publishing, 2006), p. 125. Though not per se a swept wing aircraft, the Lockheed F-104 Starfighter, another T-tail design, likewise experienced tail-blanketing and consequent pitch-up, necessitating installation of a stick-kicker and imposing of limitations on high angle-of-attack maneuvering. At the time of its design, the benefits of a low-placed tail were already recognized, and it is surprising that Clarence "Kelly’ Johnson, Lockheed’s legendary designer, did not incorporate one. Certainly afterward, he recognized its value, for when, in 1971, he proposed a lineal derivative of the F-104, the CL-1 200 Lancer (subsequently designated the X-27 but never built and flown), as a lightweight NATO export fighter, it featured a low, not high, all-moving horizontal tail. For X-27 see Jay Miller, The X-Planes: X-1 to X-45 (Hinckley, UK: Midland Publishing, 2001), pp. 284-289.
[62] See Joseph Weil, Paul Comisarow, and Kenneth W. Goodson, "Longitudinal Stability and Control Characteristics of an Airplane Model Having a 42.8° Sweptback Circular-Arc Wing with Aspect Ratio 4.00, Taper Ratio 0.60, and Sweptback Tail Surfaces,’ NACA RM-L7G28 (1947). Considerable debate likewise existed on whether the XS-2 should have a shoulder-mounted wing with anhedral, a midwing (like the XS-1) without any dihedral or anhedral, or a low wing with or without dihedral. Bell opted for a low wing with slight dihedral.
[63] Harold F. Kleckner, "Preliminary Flight Research on an All-Movable Horizontal Tail as a Longitudinal Control for Flight at High Mach Numbers,’ NACA ARR-L5C08 (Mar. 1945), p. 1.
[64] Harold F. Kleckner, "Flight Tests of an All-Movable Horizontal Tail with Geared Unbalancing Tabs on the Curtiss XP-42 Airplane,’ NACA TN-1 1 39 (1946).
[65] Hubert M. Drake and John R. Carden, "Elevator-Stabilizer Effectiveness and Trim of the X-1 Airplane to a Mach Number of 1.06,’ NACA RM-L50G20 (1950). Despite the 1950 publication date, this report covers the results of XS-1 testing from Oct. 1946 through the first supersonic flight to M = 1 .06 on Oct. 14, 1 947. European designers recognized the value of such a tail layout as well. The Miles M.52, a jet-powered supersonic research airplane intemperately canceled by the British Labour government, would have incorporated similar surfaces; "This unfortunate decision,’
Sir Roy Fedden wrote a decade later, "cost us at least ten years in aeronautical progress.’ See
his Britain’s Air Survival: An Appraisement and Strategy for Success (London: Cassell & Co., Ltd., 1957), p. 20.
[66] Jack D. Brewer and Jacob H. Lichtenstein, "Effect of Horizontal Tail on Low-Speed Static Lateral Stability Characteristics of a Model Having 45° Sweptback Wing and Tail Surfaces,’ NACA TN – 2010 (1950); and Jacob H. Lichtenstein, "Experimental Determination of the Effect of Horizontal-Tail Size, Tail Length, and Vertical Location on Low-Speed Static Longitudinal Stability and Damping in Pitch of a Model Having 45° Sweptback Wing and Tail Surfaces,’ NACA Report 1 096 (1952).
[67] William J. Alford, Jr., and Thomas B. Pasteur, Jr., "The Effects of Changes in Aspect Ratio and Tail Height on the Longitudinal Stability Characteristics at High Subsonic Speeds of a Model with a Wing Having 32.6° Sweepback,’ NACA RM-L53L09 (1953), p. 1.
[68] Norman M. McFadden and Donovan R. Heinle, "Flight Investigation of the Effects of Horizontal-Tail Height, Moment of Inertia, and Control Effectiveness on the Pitch-up Characteristics of a 35° Swept-Wing Fighter Airplane at High Subsonic Speeds,’ NACA RM-A54F21 (1955).
[69] W. Hewitt Phillips, Journey in Aeronautical Research: A Career at NASA Langley Research Center, No. 1 2 in the Monographs in Aerospace History Series (Washington: NASA, 1 998), p. 70; for an excellent survey, see Richard E. Day, Coupling Dynamics in Aircraft: A Historical Perspective, SP-532 (Washington: NASA, 1997).
[70] Phillips, Journey in Aeronautical Research, p. 72.
71 . William H. Phillips, "Effect of Steady Rolling on Longitudinal and Directional Stability,’ NACA TN-1627 (1948), pp. 1-2.
[72] William H. Phillips, "Appreciation and Prediction of Flying Qualities," NACA Report No. 927 (1949), p. 32.
[73] James H. Parks, "Experimental Evidence of Sustained Coupled Longitudinal and Lateral Oscillations from a Rocket-Propelled Model of a 35° Swept Wing Airplane Configuration,’ NACA RM-L54D15 (1 954). For more on Wallops testing, see Joseph A. Shortal, A New Dimension: Wallops Island Flight Test Range: The First Fifteen Years, RP-1 028 (Washington: NASA, 1978), pp. 256-257. For the record, the wingspan-to-fuselage ratio of the model was 0.59, significantly lower than the XS-1.
[74] It is worth noting that the advanced X-1A (and X-1 B and X-1 D) had a wingspan-to-fuselage length ratio of 0.79, compared to the 0.90 XS-1, the drop model of which first encountered inertial coupling. Their longer fuselage forebody likewise contributed even further to their tendency toward lateral-directional instability.
[75] Yeager pilot report and attached transcript, Dec. 23, 1953; J. L. Powell, Jr., "X-1A Airplane Contract W33-038-ac-20062, Flight Test Progress Report No. 15, Period From 9 December through 20 December 1953,’ Bell Aircraft Corporation Report No. 58-980-019 (Feb. 3, 1954), both from AFFTC History Office archives. I thank the staff of the AFFTC History Office and the NASA DFRC Library and Archives for locating these and other documents.
[76] Hubert M. Drake and Wendell H. Stillwell, "Behavior of the Bell X-1A Research Airplane During Exploratory Flights at Mach Numbers Near 2.0 and at Extreme Altitude,’ NACA RM-H55G25 (1955), p. 10.
[77] Alfred D. Phillips and Lt. Col. Frank K. Everest, USAF, "Phase II Flight Test of the North American YF-100 Airplane USAF No. 52-5754,’ AFFTC TR-53-33 (1953), Appendix I, p. 8. For the difference between fighter pilots and test pilots in regarding the F-1 00, see Brig. Gen. Frank. K. Everest, Jr., with John Guenther, The Fastest Man Alive (New York: Bantam, 1 990 ed.), pp. 6, 11-1 3.
[78] James R. Peele, "Memorandum for Research Airplane Projects Leader [Hartley A. Soule, hereafter RAPL]: Results of Flights 2, 3, and 4 of the F-100A (52-5778) airplane’ (Nov. 19, 1954), DFRC Archives.
[79] Ronald-Bel Stiffler, The History of the Air Force Flight Test Center: 1 January 1954-30June 1954 (Edwards AFB: AFFTC, July 13, 1955), vol. 1, pp. 66-67, copy in AFFTC History Office archives.
[80] NACA High-Speed Flight Station, "Flight Experience with Two High-Speed Airplanes Having Violent Lateral-Longitudinal Coupling in Aileron Rolls,’ NACA RM-H55A1 3 (1955), p. 4.
81 . Joseph Weil, "Memo to RAPL: Visit of HSFS personnel to North American Aviation, Inc. on Nov. 8, 1954′ (Nov. 19, 1954), DFRC Archives.
[82] Peele memo to RAPL, Nov. 19, 1954; for Langley REAC studies, see Charles J. Donlan [NACA LRC], "Memo for Associate Director [Floyd Thompson]: Industry-Service-NACA Conference on F-100, Dec. 16, 1954′ (Dec. 28. 1954), DFRC Archives.
[83] Joseph Weil and Walter C. Williams, "Memo for RAPL: Meeting of NACA and Air Force personnel at North American Aviation, Inc on Monday, Nov. 22, 1 954, to discuss means of expediting solution of stability and control problems on the F-100A airplane’ (Nov. 26, 1954), DFRC Archives; Thomas W. Finch, "Memo for RAPL: Progress report for the F-1 00A (52-5778) airplane for the period Nov. 1 to Nov. 30, 1954′ (Dec. 20, 1954), DFRC Archives; Hubert M. Drake, Thomas W. Finch, and James R. Peele, "Flight Measurements of Directional Stability to a Mach Number of 1 .48 for an Airplane Tested with Three Different Vertical Tail Configurations,’ NACA RM-H55G26 (1955); Marion H. Yancey, Jr., and Maj. Stuart R. Childs, USAF, "Phase IV Stability Tests of the F-100A Aircraft, USAF S/N 52-5767,’ AFFTC TR-55-9 (1955); 1 st Lt. David C. Leisy, USAF, and Capt. Hugh P. Hunerwadel, USAF, "ARDC F-100D Category II Performance Stability and Control Tests,’ AFFTC TR-58-27 (1958).
[84] See, for example, Robert G. Hoey and Capt. Iven C. Kincheloe, USAF, "ARDC F-104A Stability and Control,’ AFFTC TR-58-14 (1958); and Capt. Slayton L. Johns, USAF, and Capt. James W. Wood, USAF, "ARDC F-104A Stability and Control with External Stores,’ AFFTC TR-58-14, Addendum 1 (July 1959).
[85] For example, Thomas R. Sisk and William H. Andrews, "Flight Experience with a Delta-Wing Airplane Having Violent Lateral-Longitudinal Coupling in Aileron Rolls,’ NACA RM-H55H03 (1955).
[86] William H. Phillips [NACA LRC], "Memo for Associate Director: Flight program for F-100A airplane’ (Aug. 10, 1953), DFRC Archives. Even odder, it was Phillips who had identified inertial coupling in TN-1627 in 1948!
[87] The best known was Capt. Milburn "Mel’ Apt, who died in late 1956. His Bell X-2 went out of control as he turned back to Edwards after having attained Mach 3.2, possibly because of lagging instrumentation readings leading him to conclude he was flying at a slower speed. Undoubtedly the nearly decade-old design of the X-2 contributed to its violent coupling tendencies. It is sobering that in 1 947 NACA had evaluated some design options (tail location, vertical fin design) that, had Bell incorporated them on the X-2, might have turned Apt’s accident into an incident. See Ronald Bel Stiffler, The Bell X-2 Rocket Research Aircraft: The Flight Test Program (Edwards AFB: Air Force Flight Test Center, 1957); and Richard E. Day and Donald Reisert, "Flight Behavior of the X-2 Research Airplane to a Mach Number of 3.20 and a Geometric Altitude of 1 26,200 Feet,’ NACA TM-X – 137 (1959).
[88] Keneth Owen, Concorde: Story of a Supersonic Pioneer (London: Science Museum, 2001), pp. 21-60; Andrew Nahum, "The Royal Aircraft Establishment from 1945 to Concorde,’ in Robert Bud and Philip Gummett, eds., Cold War, Hot Science: Applied Research in Britain’s Defence Laboratories, 1945-1990 (London: Science Museum, 1999), pp. 29-58; and Andersson, Saab Aircraft, pp. 1 24-1 29.
[89] Even the official Air Force history of the service’s postwar fighter development repeats the canard, though it does acknowledge that "low-aspect-ratio wing forms were also studied by the U. S. National Advisory Committee for Aeronautics.’ See Marcelle Size Knaack, Post-World War II Fighters 1945-1973, vol. 1 of Encyclopedia of U. S. Air Force Aircraft and Missile Systems (Washington: Office of Air Force History, 1978), p. 159, no. 1.
[90] Letter, Adolph Burstein to Richard P. Hallion, Jan. 25, 1972. Despite his "Germanic’ name, Burstein, one of the XF-92A’s designers, was not a German scientist or engineer who came to America after 1945. Rather, he was a Russian emigree from St. Petersburg who had come to the United States in 1925.
91 . See Hallion, "Lippisch Gluhareff, and Jones,’ and R. P. Hallion, "Convair’s Delta Alpha,’ Air Enthusiast Quarterly, No. 2 (1976).
[92] Edward H. Heinemann, "Design of High-Speed Aircraft,’ a paper presented at the Fifth International Aeronautical Conference, Royal Aeronautical Society-Institute of the Aeronautical Sciences, Los Angeles, CA, June 20-24, 1955, p. 3. Copy from the Boeing-McDonnell Douglas Archives.
[93] Ltr., Maj. Howard C. Goodell, USAF, to Paul E. Garber, "DM-1 Glider Disposal,’ Nov. 28,
1949, in Gluhareff Dart accession file, National Air and Space Museum.
[94] For Langley’s progressive evaluation and modification of the DM-1, see two reports by Herbert A. Wilson, Jr., and J. Calvin Lovell, "Full Scale Investigation of the Maximum Lift and Flow Characteristics of an Airplane Having Approximately Triangular Plan Form,’ NACA RM-L6K20 (1947); and "Langley Full-Scale Tunnel Investigation of Maximum Lift and Stability Characteristics of an Airplane Having Approximately Triangular Plan Form (DM-1 Glider), NACA RM-L7F16 (1947). Changes are detailed in RM L7F16, Fig. 4. The closest expression of Germanic delta philosophy in America was not a Convair delta, but a Douglas one: the Navy-Marine F4D-1 Skyray fighter. Its design was greatly influenced by German tailless and swept wing reports Douglas engineers L. Eugene Root and Apollo M. O. Smith had discovered while assigned to an Allied technical intelligence team examining the Messerschmitt advanced projects office at Oberammergau and interviewing its senior personnel, particularly chief designer Woldemar Voigt; I wish to acknowledge with gratitude notes on their experiences received in 1972 from both the late L. Eugene Root and A. M.O. Smith. See also Cebeci, ed., Legacy of a Gentle Genius, pp. 30-36.
[95] R. M. Cross, "Characteristics of a Triangular-Winged Aircraft: 2: Stability and Control,’ in NACA, Conference on Aerodynamic Problems of Transonic Airplane Design (1 947), pp. 163-1 86, and Figs. 6 and 1 2. See also Edward F. Whittle, Jr., and J. Calvin Lovell, "Full-Scale Investigation of an Equilateral Triangular Wing Having 10-percent-Thick Biconvex Airfoil Sections, NACA RM-L8G05 (1948), Fig. 2.
[96] Crossfield with Blair, Always Another Dawn, p. 167; Thomas R. Sisk and Duane O. Muhle – man, "Longitudinal Stability Characteristics in Maneuvering Flight of the Convair XF-92A Delta-Wing Airplane Including the Effects of Wing Fences," NACA RM-H4J27 (1955).
[97] Everest with Guenther, Fastest Man Alive, p. 109.
[98] R. T. Jones, "Characteristics of a Configuration with a Large Angle of Sweepback," in NACA, Conference on Aerodynamic Problems of Transonic Airplane Design (1947), pp. 165-168, Figs. 1 -6.
[99] Charles F. Hall and John C. Heitmeyer, "Aerodynamic Study of a Wing-Fuselage Combination Employing a Wing Swept Back 63°—Characteristics at Supersonic Speeds of a Model with the Wing Twisted and Cambered for Uniform Load," NACA RM-A9J24 (1950).
[100] Though no transport or military aircraft ever flew with such a slender swept wing, just such a configuration was subsequently employed on the largest swept wing tailless vehicle ever flown, the Northrop Snark intercontinental cruise missile. Though the Snark did not enter operational service for a variety of other reasons, it did demonstrate that, aerodynamically, such a wing configuration was eminently suitable for long-range transonic cruising flight.
[101] Charles F. Hall, "Lift, Drag, and Pitching Moment of Low-Aspect Ratio Wings at Subsonic and Supersonic Speeds," NACA RM-A53A30 (1953). For the views of an Ames onlooker, see Hartman, Adventures in Research, pp. 202-207.
[102] Quoted in William E. Andrews, Thomas R. Sisk, and Robert W. Darville, "Longitudinal Stability Characteristics of the Convair YF-102 Airplane Determined from Flight Tests,’ NACA RM-H56117 (1956), p. 1; see also Edwin J. Saltzman, Donald R. Bellman, and Norman T. Musialowski, "Flight-Determined Transonic Lift and Drag Characteristics of the YF-1 02 Airplane With Two Wing Configurations,’ NACA RM-H56E08 (1956).
[103] Although it still experienced some troubled sailing: like most of the Century series fighters, the F-1 02 had other, more tortuous acquisition and program management problems unrelated to its aerodynamics that contributed to its delayed service entry. See Thomas A. Marschak, The Role of Project Histories in the Study of R&D, Rand report P-2850 (Santa Monica: The Rand Corporation, 1965), pp. 66-81; and Knaack, Fighters, pp. 163-167.
[104] H. Julian Allen and A. J. Eggers, Jr., "A Study of the Motion and Aerodynamic Heating of Ballistic Missiles Entering the Earth’s Atmosphere at High Supersonic Speeds,’ NACA TR-1 381 (1 953); Hartman, Adventures in Research, pp. 215-21 8.
[105] A. J. Eggers, Jr., and Clarence A. Syvertson, "Aircraft Configurations Developing High Lift-Drag Ratios at High Supersonic Speeds,’ NACA RM-A55L05 (1956), p. 1.
[106] Ames staff, "Preliminary Investigation of a New Research Airplane for Exploring the Problems of Efficient Hypersonic Flight,’ (Jan. 18, 1957), copy in the archives of the Historical Office, NASA Johnson Space Center, Houston, TX. Drawings and more data on this concept can be found in Richard P. Hallion, ed., From Max Valier to Project PRIME (1924-1967), vol. 1 of The Hypersonic Revolution: Case Studies in the History of Hypersonic Technology (Washington: USAF, 1998), pp. II – vi-II-x. Round One, in NACA parlance, was the original X-1 and D-558 programs. Round Two was the X-1 5. Round Three was what eventually emerged as the X-20 Dyna-Soar development effort.
[107] See John V. Becker, "The Development of Winged Reentry Vehicles, 1952-1963,’ in Hallion, ed., Hypersonic Revolution, vol. 1, pp. 379-448. It is worth noting that one significant aircraft project did use the Eggers-Syvertson wing but in a modified form: the massive North American XB-70A Valkyrie Mach 3+ experimental bomber. The XB-70 had its six engines, landing gear, and weapons bays located under the wing in a large wedge-shaped centerbody. The long, cobralike nose ran forward from the wing and featured canard control surfaces. Its sharply swept delta wing had outer wing panels that could entrap the lateral momentum off the ventral centerbody and transfer it downward to furnish compression lift.
[108] For further detail, see R. Dale Reed with Darlene Lister, Wingless Flight: The Lifting Body Story, SP-4220 (Washington: NASA 1997); Milton O. Thompson and Curtis Peebles, Flying Without Wings: NASA Lifting Bodies and The Birth of the Space Shuttle (Washington: Smithsonian Institution Press, 1 999); and Johnny G. Armstrong, "Flight Planning and Conduct of the X-24B Research Aircraft Flight Test Program,’ Air Force Flight Test Center TR-76-1 1 (1977).
[109] Spacecraft Design Division, Summary of MSC Shuttle Configurations External HO Tanks! (Houston: Manned Spacecraft Center, June 30, 1972, rev. ed.), passim. I thank the late Dr. Edward C. Ezell for making a copy of this document available for my research. The range of configurations and wind tunnel testing done in support of Shuttle development is in A. Miles Whitnah and Ernest R. Hillje, "Space Shuttle Wind Tunnel Testing Summary,’ NASA Reference Publication 1 1 25 (1984), esp. pp. 5-7. See also Alfred C. Draper, Melvin L. Buck, and William H. Goesch, "A Delta Shuttle Orbiter.’ Astronautics & Aeronautics, vol. 9, No. 1 (Jan. 1971), pp. 26-35 (I acknowledge with gratitude the assistance and advice of the late Al Draper, while we both worked at Aeronautical Systems Division, Wright-Patterson AFB, in 1986-1987); Joseph Weil and Bruce G. Powers, "Correlation of Predicted and Flight Derived Stability and Control Derivatives with Particular Application to Tailless Delta Wing Configurations,’
NASA TM-81 361 (July 1981); and J. P. Loftus, Jr., et al. "The Evolution of the Space Shuttle Design,’ a reference paper prepared for the Rogers Commission, 1986 (copy in NASA JSC History Office archives). The evolution of Shuttle configuration evolution is examined more broadly in Richard P. Hallion and James O. Young, "Space Shuttle: Fulfillment of a Dream,’ in Hallion, ed., From Scramjet to the National Aero-Space Plane (1964-1986), vol. 2 of The Hypersonic Revolution: Case Studies in the History of Hypersonic Technology (Washington: USAF, 1998) pp. 947-1173.
1 1 0. The best survey of v-g origins remains Robert L. Perry’s Innovation and Military Requirements: A Comparative Study, Rand Report RM-51 82PR (Santa Monica: The Rand Corporation, 1967), upon which this account is based.
[111] The history of the X-5 is examined minutely in Warren E. Green’s The Bell X-5 Research Airplane (Wright-Patterson AFB: Wright Air Development Center, March 1954). For NACA work, see LRC staff, "Summary of NACA/NASA Variable-Sweep Research and Development Leading to the F-1 1 1 (TFX)," Langley Working Paper LWP-285 (Dec. 22, 1966).
1 1 2. Corwin H. Meyer, "Wild, Wild Cat: The XF10F," 20th Symposium, The Society of Experimental Test Pilots, Beverly Hills, CA, Sept. 15, 1976.
1 1 3. For meeting, see LRC staff, "Summary of NACA/NASA Variable-Sweep Research and Development,’ p. 8; and J. E. Morpurgo, Barnes Wallis: a Biography (Harmondsworth, UK: Penguin Books, 1973), p. 423. NASA Langley Photograph L58-771a, dated Nov. 1 3, 1958, documents the Stack-Wallis meeting; it is also catalogued as NASA LaRC image EL-2008-00001.
1 14. LRC, "Summary of NACA/NASA Variable-Sweep Research;" see also William J. Alford, Jr., and William P. Henderson, "An Exploratory Investigation of Variable-Wing-Sweep Airplane Configurations," NASA TM-X-142 (1959); William J. Alford, Jr., Arvo A. Luoma, and William P. Henderson, "Wind – Tunnel Studies at Subsonic and Transonic Speeds of a Multiple-Mission Variable-Wing-Sweep Airplane Configuration," NASA TM-X-206 (1959); and Gerald V. Foster and Odell A. Morris, "Aerodynamic Characteristics in Pitch at a Mach Number of 1.97 of Two Variable-Wing-Sweep V/STOL Configurations with Outboard Wing Panels Swept Back 75°," NASA TM-X-322 (1960).
1 15. Morpurgo, Wallis, p. 422, and Derek Wood, Project Cancelled: British Aircraft that Never Flew (Indianapolis: The Bobbs-Merrill Company, Inc., 1975), pp. 1 82-195. After the Nov. 1958 meeting, NASA tunnel tests revealed very great deficiencies attending his tailless concept that Stack and others reported back to Vickers in June 1959. In short, the outboard pivot was but one element necessary for making a successful v-g aircraft. Others were provision for a conventional tail and design of a practicable airframe. In short, Wallis had an idea, but it took Alford and Polhamus and other NASA researchers to refine it and render it achievable.
1 1 6. NASA F-111 tunnel research, analysis, and support is detailed in Testimony of Edward C. Pol – hamus, in U. S. Senate, TFX Contract Investigation (Second Series): Hearings Before the Permanent Subcommittee on Investigations of the Committee on Government Operations, United States Senate, 91st Congress, 2nd Session, Part 2 (Washington: GPO, 1970), pp. 339-363; for the F-1 1 1 in Desert Storm, see Tom Clancy with Gen. Chuck Horner (New York: G. P. Putnam’s Sons, 1999), pp. 318, 417, 424, and 450.
1 17. See Joseph R. Chambers, Partners in Freedom: Contributions of the Langley Research Center to U. S. Military Aircraft of the 1990s, SP-20004519 (Washington; NASA, 2000), which treats these and other programs in great and authoritative detail.
1 1 8. Robert W. Kress, "Variable Sweep Wing Design," AIAA Paper No. 83-1051 (1983) is an excellent survey. The Su-24 was clearly F-1 1 1 inspired, and the Tu-1 60 was embarrassingly similar in configuration to the American B-1.
1 19. John P. Campbell and Hubert M. Drake, "Investigation of Stability and Control Characteristics of an Airplane Model with Skewed Wing in the Langley Free-Flight Tunnel,’ NACA TN-1 208 (May 1947), p. 10.
1 20. Richard P. Hallion and Michael H. Gorn, On the Frontier: Experimental Flight at NASA Dryden (Washington: Smithsonian Books, 2002), pp. 256-260, and personal recollections of the program from the time.
[121] De E. Beeler, Donald R. Bellman, and John H. Griffith, "Flight Determination of the Effects of Wing Vortex Generators on the Aerodynamic Characteristics of the Douglas D-558-I Airplane,’ NACA RM-L51A23 (1951).
1 22. All three bore the imprint of Richard Whitcomb and thus, in this survey, are not examined in detail, since his work is more thoroughly treated in a companion essay by Jeremy Kinney.
1 23. LRC staff, "The Supersonic Transport—A Technical Summary,’ NASA TN-D-423 (1960), p. 93; this was the summary report of the briefings presented the previous fall to Quesada. NASA research on supersonic cruise is the subject of a companion essay in this study, by William Flanagan, and Whitcomb’s work is detailed in the previously cited Kinney study in this volume.
1 24. In FY 1 968, NASA expended $10.8 million in then-year dollars on SST research at Langley, Ames, and Lewis, against a total aeronautics research expenditure of $42.9 million at those Centers. See Testimony of James E. Webb in U. S. Senate, Aeronautical Research and Development Policy: Hearings Before the Committee on Aeronautical and Space Sciences, United States Senate, 90th Congress, 1st Session (Washington: GPO, 1967), p. 39.
1 25. Lyndon B. Johnson, "President’s Message on Transportation,’ Mar. 2, 1 966, reprinted in Legislative Reference Service of the Library of Congress, Policy Planning for Aeronautical Research and Development: Staff Report Prepared for Use of the Committee on Aeronautical and Space Sciences United States Senate by the Legislative Reference Service Library of Congress, Document No. 90, U. S. Senate, 89th Congress, 2nd Session (Washington: GPO, 1 966), pp. 50-51 .
1 26. For various perspectives on Anglo-French-Soviet-American SST development, see Kenneth Owen, Concorde: Story of a Supersonic Pioneer (London: Science Museum, 2001); Howard Moon, Soviet SST: The Technopolitics of the Tupolev Tu-144 (New York: Orion Books, 1989); R. E.G. Davies, Supersonic (Airliner) Non-Sense: A Case Study in Applied Market Research (McLean, VA: Paladwr Press,
1998); Mel Horwitch, Clipped Wings: The American SST Conflict (Cambridge: The MIT Press, 1982); and Eric M. Conway, High-Speed Dreams: NASA and the Technopolitics of Supersonic Transportation, 1945-1999 (Baltimore: The Johns Hopkins Press, 2005).
1 27. Deep stall is a dangerous condition wherein an airplane pitches to a high angle of attack, stalls, and then descends in a stabilized stalled attitude, impervious to corrective control inputs. It is more typically encountered by swept wing T-tail aircraft, and one infamous British accident, to a BAC 1-1 1 airliner, claimed the life of a crack flight-test crew captained by the legendary Mike Lithgow, an early supersonic and sweptwing pioneer.
1 28. Langley’s SCAT studies are summarized in David A. Anderton, Sixty Years of Aeronautical Research, 1917-1977, EP-145 (Washington: NASA, 1978), pp. 54-58. Relevant reports on specific configurations and predecessors include: Donald D. Baals, Thomas A. Toll, and Owen G. Morris, "Airplane Configurations for Cruise at a Mach Number of 3,” NACA RM-L58E 14a (1958); Odell A. Morris and A. Warner Robins, "Aerodynamic Characteristics at Mach Number 2.01 of an Airplane Configuration Having a Cambered and Twisted Arrow Wing Designed for a Mach Number of 3.0,’ NASA TM-X-1 15 (1959); Cornelius Driver, M. Leroy Spearman, and William A. Corlett, "Aerodynamic Characteristics at Mach Numbers From 1.61 to 2.86 of a Supersonic Transport Model With a Blended Wing-Body, Variable-Sweep Auxiliary Wing Panels, Outboard Tail Surfaces, and a Design Mach Number of 2.2,’ NASA TM-X-817 (1963); Odell A. Morris and James C. Patterson, Jr., "Transonic Aerodynamic Characteristics of Supersonic Transport Model With a Fixed, Warped Wing Having 74° Sweep,’ NASA TM-X-1 167 (1965); Odell A. Morris, and Roger H. Fournier, "Aerodynamic Characteristics at Mach Numbers 2.30, 2.60, and 2.96 of a Supersonic Transport Model Having Fixed, Warped Wing,’ NASA TM-X-1 115 (1965); A. Warner Robins, Odell A. Morris, and Roy V. Harris, Jr., "Recent Research Results in the Aerodynamics of Supersonic Vehicles,’ AIAA Paper 65-717 (1965); Donald D. Baals, A. Warner Robins, and Roy V. Harris, Jr., "Aerodynamic Design Integration of Supersonic Aircraft,’ AIAA Paper 68-101 8 (1968); Odell A. Morris, Dennis E. Fuller, and Carolyn B. Watson, "Aerodynamic Characteristics of a Fixed Arrow-Wing Supersonic Cruise Aircraft at Mach Numbers of 2.30, 2.70, and 2.95,’ NASA TM-78706 (1978); and John P. Decker and Peter F. Jacobs, "Stability and Performance Characteristics of a Fixed Arrow Wing Supersonic Transport Configuration (SCAT 15F-9898) at Mach Numbers from 0.60 to 1.20,’ NASA TM-78726 (1978).
1 29. Harry J. Hillaker, "The F-16: A Technology Demonstrator, a Prototype, and a Flight Demonstrator,’ AIAA Paper No. 83-1063 (1983). The "XL’ designation for the cranked-arrow F-16 reflected Harry Hillakers passionate interest in golf, for it echoed the name of a particularly popular longdistance golf ball, the Top Flite XL. See also Chambers, Innovation in Flight, pp. 42, 48, 58-59.
1 30. For Junkers, see Hugo Junkers, Gleiflieger mit zur Aufnahme von nicht Auftrieg erzeugen Teilen dienenden Hohlkorpen, Patentschrift Nr. 253788, Klasse 77h, Gruppe 5 (Berlin: Reichspatentamt, Nov. 14, 191 2). For Liebeck, see Robert H. Liebeck, Mark A. Page, Blaine K. Rawdon, Paul W. Scott, and Robert A. Wright, "Concepts for Advanced Subsonic Transports,’ NASA CR-4624 (1994); Robert H. Liebeck, "Design of the Blended Wing Body Subsonic Transport,’ Journal of Aircraft, vol. 41, no. 1 (Jan.-Feb. 2004). pp. 10-25; and Chambers, Innovation in Flight, pp. 86-92.
[131] These included heavy-lift cargo, air-refueling, and other military missions rather than use as a civil airliner. See NASA LRC, "The Blended-Wing-Body: Super Jumbo Jet Concept Would Carry 800 Passengers," NASA Facts, FS-1997-07-24-LaRC July 1997); and NASA LRC, "The Blended Wing Body: A Revolutionary Concept in Aircraft Design," NASA Facts, FS-2001-04-24-LaRC (Apr. 2001). For an early appreciation of the military value of BWB designs, see Gene H. McCall, et al., Aircraft & Propulsion, a volume in the New World Vistas: Air and Space Power for the 21st Century series (Washington: HQ USAF Scientific Advisory Board, 1995), p. 6.
1 32. Robert H. Liebeck, Mark A. Page and Blaine K. Rawdon, "Blended-Wing-Body Subsonic Commercial Transport," AIAA Paper 98-0438 (1998); Sean Wakayama, "Multidisciplinary Design Optimization of the Blended-Wing-Body," AIAA Paper 98-4938 (1998); Dino Roman, J. B. Allen, and Robert H. Liebeck, "Aerodynamic Design Challenges of the Blended-Wing-Body Subsonic Transport," AIAA Paper 2000-4335 (2000). Fuel economy figure from Dryden Flight Research Center, "X-24B Blended Wing-Body" (Apr. 2, 2009).
1 33. DFRC, "X-24B Blended Wing-Body" (Apr. 2, 2009).
[134] David A. Anderton, "NACA Formula Eases Supersonic Flight,’ Aviation Week vol. 63 (Sept. 1 2, 1955): p. 1 5; Marvin Miles, "New Fighter Jet Gets Test,’ Los Angeles Times, Mar. 10, 1971, p. 26; "Boeing’s 747-400 Jet Makes Maiden Flight,’ Wall Street Journal, May 2, 1988, p. 8.
[135] Whitcomb’s story has been interpreted from the viewpoint of the NACA and NASA’s overall contributions to aeronautics by several historians and engineers. This chapter depends heavily on the work of James Hansen, Richard Hallion, Michael Gorn, Lane Wallace, John Becker, Donald Baals, and William Corliss.
[136] Clay Blair, Jr., "The Man Who Put the Squeeze on Aircraft Design,’ Air Force Magazine, vol. 39 (Jan. 1956): p. 50.
[137] "Richard Travis Whitcomb: Distinguished Research Associate,’ NASA Langley Research Center, Apr. 1983, File CW-463000-01, National Air and Space Museum Archives.
[138] Richard Witkin, "Air Scientist Got His Start When 1 2," New York Times, Oct. 3, 1955, p. 20 (quote); Ray Bert, "Winged Victory: Meet Richard Whitcomb," Transformations (fall 2002), http://www. wpi. edu/News/Transformations/2002Fall/whitcomb. html (Accessed Feb. 14, 2009); "Jet Pioneers—Richard T. Whitcomb," n. d., File CW-463000-01, National Air and Space Museum Archives.
[139] Barbara Rowes, "When You Ride Tomorrow’s Airplanes, You’ll Thank Dick Whitcomb," Washington Post-Times Herald, Aug. 31, 1969, p. 165.
[140] Bert, "Winged Victory"; Witkin, "Air Scientist Got His Start When 1 2"; Brian Welch, "Whitcomb: Aeronautical Research and the Better Shape," Langley Researcher (Mar. 21, 1 980): p. 4.
[141] John Becker, The High Speed Frontier: Case Histories of Four NACA Programs 1920-1950, NASA SP-445 (Washington, DC: U. S. Government Printing Office, 1980), p. 61.
[142] Becker, High Speed Frontier, p. 61; Lane E. Wallace, "The Whitcomb Area Rule: NACA Aerodynamics Research and Innovation,’ in Pam E. Mack, ed., From Engineering Science to Big Science: The NACA and NASA Collier Trophy Research Project Winners, (Washington, DC: National Aeronautics and Space Administration, 1998), p. 137.
[143] John D. Anderson, Jr., A History of Aerodynamics and its Impact on Flying Machines (New York: Cambridge University Press, 1997), pp. 419, 424-425.
1 1 . Becker, High Speed Frontier, p. 61.
1 2. James R. Hansen, Engineer in Charge: A History of the Langley Aeronautical Laboratory, 1917-1958, NASA SP-4305 (Washington, DC: NASA, 1987), pp. 331-332.
[146] Ibid., p. 332.
[147] Hansen, Engineer in Charge, p. 341. As James R. Hansen has suggested, these were certainly antecedents to Whitcomb’s area rule, but it was his highly intuitive visual mind that resulted in something original.
[148] Ibid., p. 332.
[149] The NACA referred to the facility as the 8-foot Transonic Tunnel after Oct. 1950, but for the purposes of clarity and to avoid confusion with the follow-on 8-foot Transonic Pressure Tunnel, the original designation 8-foot High Speed Tunnel is used in this text. Hansen, Engineer in Charge, pp. 327-328, 454; Steven T. Corneliussen, "The Transonic Wind Tunnel and the NACA Technical Culture,’ in Pam E. Mack, ed., From Engineering Science to Big Science: The NACA and NASA Collier Trophy Research Project Winners (Washington, DC: NASA, 1998), p. 133.
[150] Hansen, Engineer in Charge, pp. 329, 330-331.
1 8. Richard T. Whitcomb and Thomas C. Kelly, "A Study of the Flow Over a 45-degree Sweptback Wing-Fuselage Combination at Transonic Mach Numbers," NACA RM-L52DO1 (June 25, 1952), p. 1; Hansen, Engineer in Charge, p. 333.
[152] Ibid., p. 333.
[153] Ibid., p. 334.
[154] Ibid., p. 334.
[155] Roger D. Launius, quoted in James Schultz, Crafting Flight: Aircraft Pioneers and the Contributions of the Men and Women of NASA Langley Research Center (Washington, DC: NASA, 2003), p. 1 83.
[156] Eugene S. Ferguson, Engineering and the Minds Eye (Boston: MIT Press, 1994), p. 41; Hansen, Engineer in Charge, p. 328.
[157] Whitcomb quoted in Welch, "Whitcomb,’ p. 5.
[158] Richard T. Whitcomb, "A Study of the Zero-Lift Drag-Rise Characteristics of Wing-Body Combinations Near the Speed of Sound,’ NACA TR-1 273 (1956), pp. 519, 538-539; Engineer in Charge, pp. 334-335.
[159] Donald D. Baals and William R. Corliss, Wind Tunnels of NASA (Washington, DC: Scientific and Technical Information Branch, National Aeronautics and Space Administration, 1981), p. 63.
[160] Hansen, Engineer in Charge, p. 336.
[161] Quoted in Richard P. Hallion, Designers and Test Pilots (Alexandria, VA: Time-Life Books, 1983), p. 143.
[162] Michael Gorn, Expanding the Envelope: Flight Research at NACA and NASA (Lexington: University Press of Kentucky, 2001), p. 329.
[163] Richard T. Whitcomb, "A Study of the Zero-Lift Drag-Rise Characteristics of Wing-Body Combinations Near the Speed of Sound,’ NACA RM-L52H08 (Sept. 3, 1952). RM-L52H08 was superseded by TR-1 273 (see note 23) when the document became unclassified in 1956.
31 . Anderton, "NACA Formula Eases Supersonic Flight,’ pp. 1 3-14.
[165] Gordon Swanborough, United States Military Aircraft Since 1909 (London: Putnam, 1963), pp. 151, 153.
[166] Hansen, Engineer in Charge, p. 337.
[167] Baals and Corliss, Wind Tunnels of NASA, p. 62; Hansen, Engineer in Charge, p. 337.
[168] Hansen, Engineer in Charge, p. 337.
[169] Hansen, Engineer in Charge, pp. 337-338; Richard P. Hallion, On the Frontier: Flight Research at Dryden, 1946-198 1 (Washington, DC: NASA, 1984), p. 90; Baals and Corliss, Wind Tunnels of NASA, p. 63.
[170] Hansen, Engineer in Charge, 338; Swanborough, United States Military Aircraft Since 1909, p. 152; Hallion, On the Frontier, pp. 90, 144 [quote]; Baals and Corliss, Wind Tunnels of NASA, p. 63.
[171] Swanborough, United States Military Aircraft Since 1909, pp. 152, 154-155; Richard Wit – kin, "Supersonic Jets Will Defend City,’ New York Times, Jan 3, 1957, p. 1 2.
[172] Swanborough, United States Military Aircraft Since 1909, pp. 152, 154-155.
[173] Hallion, On the Frontier, p. 57.
[174] Ibid., p. 96.
[175] Gordon Swanborough and Peter M. Bowers, United States Navy Aircraft Since 1911 (Annapolis: Naval Institute Press, 1990), pp. 456, 459; Barrett Tillman, MiG Master: The Story of the F-8 Crusader (Annapolis: Naval Institute Press, 2007), pp. 55-60.
[176] Anderton, "NACA Formula Eases Supersonic Flight,’ 15; Hansen, Engineer in Charge, p. 339
[177] Rene J. Francillon, Grumman Aircraft Since 1929 (Naval Institute Press, 1989), p. 377; Swan – borough and Bowers, United States Navy Aircraft Since 1911, pp. 256-257.
[178] Rene J. Francillon, Lockheed Aircraft Since 1913 (Annapolis: Naval Institute Press, 1987), pp. 329, 331, 342.
[179] Richard T. Whitcomb and Thomas L. Fischetti, "Development of a Supersonic Area Rule and an Application to the Design of a Wing-Body Combination Having High Lift-to-Drag Ratios,’ NACA RM-L53H31A (Aug. 1 8, 1 953); and Richard T. Whitcomb, "Some Considerations Regarding the Application of the Supersonic Area Rule to the Design of Airplane Fuselages,’ NACA RM-L56E23a (July 3, 1956).
[180] Richard Witkin, "Aviation: 2,600 M. P.H.," New York Times, Oct. 20, 1957, p. X33.
[181] "Aero News Digest," Aero Digest (Sept. 1 955): p. 5. Aero Digest released the story without permission because publisher Fred Hamlin learned that the NACA had arranged, without his knowledge, to make the announcement in the rival journal, Aviation Week, on Sept. 19. "New Design Increasing Airplane Speeds Hailed," Los Angeles Times, Sept. 1 2, 1955, p. 10; Alvin Shuster, "’Pinch-Waist’ Plane Lifts Supersonic Speed 25%," New York Times, Sept. 1 2, 1 955, p. 15.
[182] Quoted in Alvin Shuster, "’Pinch-Waist’ Plane Lifts Supersonic Speed 25%," New York Times, Sept. 12, 1955, p. 15.
[183] Commentary by Robert Hotz, "The Area-Rule Breakthrough," Aviation Week (Sept. 1 2, 1955), p. 152.
51 . "New Plane Shape Increases Speed,’ The Washington Post-Times Herald, Sept. 1 2, 1 955, p. 1 8; "New Design Increasing Airplane Speeds Hailed,” Los Angeles Times, Sept. 1 2, 1 955, p. 10; "Radial Shift in Air Design Bared by U. S.,’ Christian Science Monitor, Sept. 1 2, 1955, p. 1 .
[185] "Area Rule and Coke Bottle,’ Aviation Week (Sept. 1 2, 1955): p. 1 3. This source appeared as a sidebar in Anderton, "NACA Formula Eases Supersonic Flight.’
[186] Richard Witkin, "The ‘Wasp-Waist’ Plane,’ New York Times, Oct. 2, 1955, p. 20.
[187] Maurice A. Garbell, "Transonic Planes Cut Drag with ‘Wasp Waist,” Christian Science Monitor, Oct. 14, 1955, p. 5.
[188] James J. Hagerty, Jr., "The Collier Trophy Winner,’ Collier’s (Dec. 9, 1 955): n. p.
[189] "Designer to Be Honored For Pinched-Waist Plane,’ New York Times, Nov. 23, 1955, p. 48.
[190] Neal Stanford, "Wing Design Seeks Speed,’ Christian Science Monitor, Feb. 17, 1970, p. 5.
[191] "Whitcomb Receives NACA’s First DSM,’ U. S. Air Services (Oct. 1956): p. 20.
[192] Rowes, "When You Ride Tomorrow’s Airplanes, You’ll Thank Dick Whitcomb."
[193] Joseph R. Chambers, Innovation in Flight: Research of the NASA Langley Research Center on Revolutionary Advanced Concepts for Aeronautics, NASA SP-2005-4539 (Washington, DC: NASA, 2005), p. 18.
61 . Whitcomb also rejected the committee’s emphasis on variable-geometry wings as too heavy, which led to his ejection from the design committee by Stack. Eric M. Conway, High Speed Dreams: NASA and the Technopolitics of Supersonic Transportation, 1945-1999 (Baltimore: Johns Hopkins University Press, 2005), pp. 54-55; Becker, High Speed Frontier, pp. 55-56.
[195] Conway, High Speed Dreams, p. 55; Gorn, Expanding the Envelope, p. 56; Quote from Chambers, Innovation in Flight, p. 28.
[196] Gorn, Expanding the Envelope, p. 331.
[197] For more information on the history of airfoils and their theorists and designers, see Anderson, A History of Aerodynamics.
[198] Rowes, "When You Ride Tomorrow’s Airplanes, You’ll Thank Dick Whitcomb,’ p. 165.
[199] Thomas Grubisich, "Fuel-Saver in Wings,’ The Washington Post, July 11, 1 974, p. C1.
[200] Gorn, Expanding the Envelope, p. 331.
[201] Grubisich, "Fuel-Saver in Wings."
[202] Gorn, Expanding the Envelope, p. 331.
[203] Welch, "Whitcomb," p. 5.
71 . Richard T. Whitcomb and Larry L. Clark, "An Airfoil Shape for Efficient Flight at Supercritical Mach Numbers," NASA TM-X-1 109 (Apr. 20, 1965).
[205] For a first-person account of the development of the supercritical wing, see Richard T. Whitcomb, "Research Associated with the Langley 8-Foot Tunnels Branch: Lecture at Ames Research Center, October 21, 1970," NASA TM-108686 (1970).
[206] Richard T. Whitcomb, "The State of Technology Before the F-8 Supercritical Wing," in Proceedings of the F-8 Digital Fly-By-Wire and Supercritical Wing First Flights 20th Anniversary, May 27,
1992, NASA CP-3256, vol. 1 (Washington, DC: NASA, 1996), p. 81; Gorn, Expanding the Envelope, pp. 331-332.
[207] Gorn, Expanding the Envelope, pp. 332, 394, 401.
[208] Welch, "Whitcomb," p. 5.
71 . Richard T. Whitcomb and Larry L. Clark, "An Airfoil Shape for Efficient Flight at Supercritical Mach Numbers," NASA TM-X-1 109 (Apr. 20, 1965).
[210] For a first-person account of the development of the supercritical wing, see Richard T. Whitcomb, "Research Associated with the Langley 8-Foot Tunnels Branch: Lecture at Ames Research Center, October 21, 1970," NASA TM-108686 (1970).
[211] Richard T. Whitcomb, "The State of Technology Before the F-8 Supercritical Wing," in Proceedings of the F-8 Digital Fly-By-Wire and Supercritical Wing First Flights 20th Anniversary, May 27,
1992, NASA CP-3256, vol. 1 (Washington, DC: NASA, 1996), p. 81; Gorn, Expanding the Envelope, pp. 331-332.
[212] Gorn, Expanding the Envelope, pp. 332, 394, 401.
[213] Thomas C. Kelly and Richard T. Whitcomb, "Evolution of the F-8 Supercritical Wing Configuration,’ in Supercritical Wing Technology—A Progress Report on Flight Evaluations, NASA SP-301 (1972), p. 35; Gorn, Expanding the Envelope, pp. 332-333.
[214] Kelly and Whitcomb, "Evolution of the F-8 Supercritical Wing Configuration,’ in Supercritical Wing Technology, p. 35; Gorn, Expanding the Envelope, pp. 333-334.
[215] Neal Stanford, "Wing Design Seeks Speed,’ Christian Science Monitor, Feb. 17, 1970, p. 5.
[216] Thomas C. McMurtry, Neil W. Matheny, and Donald H. Gatlin, "Piloting and Operational Aspects of the F-8 Supercritical Wing Airplane,’ in Supercritical Wing Technology—A Progress Report on Flight Evaluations. NASA SP-301, (Washington, DC, NASA, 1972), p. 102; Gorn, Expanding the Envelope, pp. 335, 337.
[217] Joseph Well, "Summary and Future Plans,’ in Supercritical Wing Technology, pp. 127-128.
[218] See Jon S. Pyle and Louis L. Steers, "Flight-Determined Lift and Drag Characteristics of an F-8 Airplane Modified with a Supercritical Wing with Comparisons to Wind Tunnel Results,’ NASA TM-X-3250 (Jan. 16, 1975); and Lawrence C. Montoya and Richard D. Banner, "F-8 Supercritical Wing Flight Pressure, Boundary-Layer, and Wake Measurements and Comparisons with Wind Tunnel Data,’ NASA TM-X-3544 June 1977).
81 . Becker, High Speed Frontier, p. 59.
[220] Grubisich, "Fuel-Saver in Wings."
[221] Stacy V. Jones, "New Aircraft Wing Invented," New York Times, May 1, 1976, p. 46.
[222] Grubisich, "Fuel-Saver in Wings."
[223] Richard Witkin, "McDonnell Douglas Unveils New Cargo Jet," New York Times, Aug. 6, 1975, p. 65.
[224] Chambers, Innovation in Flight, p. 1 83; Hallion, On the Frontier, p. 204.
[225] Hallion, On the Frontier, pp. 206-207.
[226] Ibid., p. 172.
[227] For an overview of NASA development of supercritical airfoils up to 1 990, see Charles D. Harris, "NASA Supercritical Airfoils—A Matrix of Family-Related Airfoils," NASA TP-2969 (1990).
[228] Blackwell, "Influence on Today’s Aircraft,’ p. 114.
[229] "Dr. Whitcomb to Receive $25,000 Award from NASA,’ NASA Release No. 74-148 (June 4, 1974): pp. 1, 3, File CW-463000-01, National Air and Space Museum Archives; Gorn, Expanding the Envelope, p. 337.
[230] Grubisich, "Fuel-Saver in Wings.’
[231] "Richard Travis Whitcomb: Distinguished Research Associate,’ NASA Langley Research Center, Apr. 1983.
[232] Welch, "Whitcomb,” p. 5.
[233] Joseph R. Chambers, Concept to Reality: Contributions of the Langley Research Center to U. S. Civil Aircraft of the 1990s (Washington, DC: NASA, 2003), p. 35.
[234] Ibid., p. 35.
[235] George Larson, "Winglets,’ Air & Space Magazine (Sept. 01,2001), http://www. airspacemag. com/flight-today/wing. html (Accessed Feb. 20, 2009).
[236] See F. Nagel, Wings With End Plates. Memo. Rep. 1 30, Eng. Div., McCook Field, Nov. 4,
1924; W. Mangler, "The Lift Distribution of Wings With End Plates," NACA TM-856 (1938); J. Weber, Theoretical Load Distribution on a Wing with Vertical Plates. R. & M. No. 2960, British A. R.C., 1956.
[237] Richard T. Whitcomb, "A Design Approach and Selected Wind-Tunnel Results at High Subsonic Speeds for Wing-Tip Mounted Winglets," NASA TN-D-8260 (July 1976), p. 1; Chambers, Concept to Reality, p. 35.
[238] Whitcomb, "A Design Approach and Selected Wind-Tunnel Results at High Subsonic Speeds for Wing-Tip Mounted Winglets," NASA TN-D-8260 (July 1976), pp. 1 3-14.
[239] Ibid., pp. 1-2, 5, 1 3-14. Whitcomb also suggested consultation of the following two references regarding winglet design: John E. Lamar, "A Vortex-Lattice Method for the Mean Camber Shapes of Trimmed Noncoplanar Platforms with Minimum Vortex Drag," NASA TN-D-8090 (1976) and M. I. Goldhammer, "A Lifting Surface Theory for the Analysis of Nonplanar Lifting Systems," AIAA Paper No. 76-16 (Jan. 1976).
[240] Stuart G. Flechner, Peter F. Jacobs, and Richard T. Whitcomb, "A High Subsonic Wind Tunnel Investigation of Winglets on a Representative Second-Generation Jet Transport Wing," NASA TN – 8264 (July 1976), pp. 1, 13.
[241] Larson, "Winglets."
[242] See also Stuart G. Flechner and Peter F. Jacobs, "Experimental Results of Winglets on First, Second, and Third Generation Jet Transports," NASA TM-72674 (1978).
[243] For these articles, see Conventional Take-off and Landing (CTOL| Transport Technology 1978: Proceedings of a Conference Held at Langley Research Center, Hampton, VA, Feb. 28-Mar. 3, 1978, NASA CP-2036, Parts I and II (Washington, DC: NASA, 1978); Chambers, Concept to Reality, p. 38.
[244] Chambers, Concept to Reality, p. 41. During the takeoff for the world flight, one of Voyager’s winglets broke off, and pilot Dick Rutan had to severely maneuver the aircraft to break the other one off before the journey could continue.
[245] Ibid., pp. 41-43.
[246] Gulfstream, "The History of Gulfstream: 1958-2008," 2009, http://www. gulfstreami. com/history (Accessed Feb. 15, 2009).
[247] Chambers, Concept to Reality, p. 38.
1 1 0. KC-1935 Winglet Program Review: Proceedings of a Symposium Held At Dryden Flight Research Center, Sept. 16, 1981, NASA CP-221 1 (Washington, DC: NASA, 1982), pp. 1,
1 1-12; Chambers, Concept to Reality, pp. 38-39. In the end, the Air Force chose not to equip its KC-1 35 aerial tankers with winglets, opting for new engines instead.
[249] Staff of Douglas Aircraft Company, DC-10 Winglet Flight Evaluation, NASA CR-3704 (June 1983), pp. v, 1 15-1 16; Chambers, Concept to Reality, pp. 38, 39, 41,43.
1 1 2. Chambers, Concept to Reality, p. 43; "Winglets for the Airlines,’ n. p., n. d.; The Boeing Company, "Commercial Airplanes: MD-1 1 Family,’ 2009, http://www. boeing. com/commercial/ md-1 Ifamily/index. html (Accessed Mar. 1, 2009).
1 1 3. Chambers, Concept to Reality, pp. 38, 43.
1 14. Aviation Partners Boeing, "Winglets,’ 2006, http://www. aviationpartnersboeing. com (Accessed Mar. 27, 2009); Stephen O. Andersen and Durwood Zaelke, Industry Genius: Inventions and People Protecting the Climate and Fragile Ozone Layer (Sheffield, UK: Greenleaf Publishing, 2003), pp. 32-52; Aviation Partners Boeing, "Winglets Save Airlines Money: An Interview with Joe Clark and Jason Paur,’ 2006, http://www. aviationpartnersboeing. com/interview. html (Mar. 27, 2009).
1 15. Welch, "Whitcomb,” p. 5; Larson, "Winglets.”
1 1 6. David Devoss, "The Race to Recover the Cup,’ Los Angeles Times, Aug. 31, 1986, p. X9.
1 1 7. Chambers, Concept to Reality, p. 44.
1 1 8. Grubisich, "Fuel-Saver in Wings.’
1 19. Bert, "Winged Victory’; Welch, "Whitcomb,” p. 4.
1 20. Hallion, On the Frontier, p. 202.
[259] Bert, "Winged Victory"; NASA History Office, "Richard T. Whitcomb," 2008, htp://history. nasa. gov/naca/bio. html (Accessed Feb. 27, 2009); "Richard Travis Whitcomb: Distinguished Research Associate," NASA Langley Research Center, Apr. 1983.
1 22. James Blackwell, "Influence on Today’s Aircraft,’ in Proceedings of the F-8 Digital Fly-ByWire and Supercritical Wing First Flight’s 20th Anniversary, May 27, 1992, pp. 96-97, 1 00;
U. S. Air Force, "F-22 Raptor,’ Mar. 2009, http://www. af. mil/information/factsheets/factsheet. asp? fsD= 199 (May 21, 2009).
1 23. Hallion, On the Frontier, p. 206.
1 24. Langley Research Center, "NASA Contributions to the C-17 Globemaster III,’ FS-1996-05-06- LaRC (May 1996): p. 2.
1 25. Chambers, Innovation in Flight, p. 79.
1 26. The National Register also recognized two other important Langley wind tunnels: the Variable-Density Tunnel of 1922 and the Full-Scale Tunnel of 1931. National Park Service, "From Sand Dunes to Sonic Booms: List of Sites,’ n. d., http://www. nps. gov/nr/travel/aviation/sitelist. htm (Accessed Mar. 15, 2009); NASA, "Langley Research Center National Historic Landmarks,’
1992, http://www. nasa. gov/centers/langley/news/factsheets/Landmarks. html#8FT (Accessed Mar. 15, 2009).
1 27. National Park Service, "Eight-Foot High Speed Tunnel,’ n. d., http://www. nps. gov/nr/ travel/aviation/8ft. htm (Accessed Mar. 5, 2009); National Park Service, "National Historic Landmarks Program: Eight-Foot High Speed Tunnel,’ 2006, http://tps. crnps. gov/nhl/detail. cfm? ResourceId=1916&ResourceType=Structure, (Accessed Mar. 5, 2009).
[266] Welch, "Whitcomb,” p. 4; NASA, "Audit of Wind Tunnel Utilization,’ 2003, oig. nasa. gov/ audits/reports/FY03/pdfs/ig-03-027.pdf (Accessed Mar. 17, 2009).
1 29. Welch, "Whitcomb," p. 4.
[268] Russell E. Lee, "Famous Firsts in Helicopter History,’ in Walter J. Boyne and Donald S. Lopez, eds., Vertical Flight: The Age of the Helicopter (Washington: Smithsonian Institution Press, 1984), p. 248; Don Fertman, "The Helicopter History of Sikorsky Aircraft,’ Vertiflite, vol. 30, no. 4 (May/June 1984), p. 16; Mike Debraggio, "The American Helicopter Society—A Leader for 40 Years,’ Vertiflite, vol. 30, no. 4 (May/June 1984), p. 56.
[269] F. B. Gustafson, "A History of NACA Research on Rotating-Wing Aircraft,’ Journal of the American Helicopter Society, vol. 1, no. 1 (Jan. 1956), p. 16.
[270] Edgar C. Wood, "The Army Helicopter, Past, Present and Future,’ Journal of the American Helicopter Society, vol. 1, no. 1 (Jan. 1 956), pp 87-92; Lt. Gen. John J. Tolson, Airmobilily, 1961-1971, a volume in the U. S. Army Vietnam Studies series (Washington, DC: Army, 1973), pp. 1 6-24; and J. A. Stockfisch, The 1962 Howze Board and Army Combat Developments, Monograph Report MR-435-A (Santa Monica: The RAND Corporation, 1994).
[271] This case study has drawn upon two major sources covering the period 1930 through 1984 published in Vertiflite, the quarterly magazine of the American Helicopter Society: Frederic B. Gustafson, ‘History of NACA/NASA Rotating-Wing Aircraft Research, 1915-1970," Vertiflite, Reprint VF-70, (Apr. 1971), pp. 1 -27; and John Ward, "An Updated History of NACA/NASA Rotary-Wing Aircraft Research 1915-1984," Vertiflite, vol. 30, No. 4 (May/June 1984), pp. 108-1 17. The author (who wrote the second of those two) has extended the coverage beyond the original 1984 end date.
[272] J. B. Wheatley, "Lift and Drag Characteristics and Gliding Performance of an Autogiro as Determined In Flight," NACA Report No. 434 (1932).
[273] J. B. Wheatley, "A Aerodynamic Analysis of the Autogiro Rotor With Comparison Between Calculated and Experimental Results," NACA Report No. 487 (1934).
[274] Anon., "Proceedings of Rotating-Wing Aircraft Meeting of the Franklin Institute, Philadelphia, Pennsylvania, Oct. 20-29, 1938," Philadelphia Section, Institute of the Aeronautical Sciences (IAS); Anon., "Proceedings of the Second Annual Rotating-Wing Aircraft Meeting of the Franklin Institute, Philadelphia, Pennsylvania, Nov. 30-Dec. 1, 1939," Philadelphia Section, Institute of the Aeronautical Sciences (IAS).
[275] FJ. Bailey, Jr., "A Simplified Theoretical Method of Determining the Characteristics of a Lifting Rotor in Forward Flight," NACA Report No. 716 (1941).
[276] F. B. Gustafson, "Effects on Helicopter Performance of Modifications in Profile-Drag Characteristics of Rotor-Blade Airfoil Sections," NACA WR-L-26 [formerly NACA Advanced Confidential Report ACR L4H05] (1944).
[277] Alfred Gessow and Garry C. Myers, Jr., Aerodynamics of the Helicopter (New York: The Mac
millan Company, 1952; reissued by Frederick Ungar Publishing Co., 1967).
1 1. R. P. Coleman, "Theory of Self-Excited Mechanical Oscillations of Hinged Rotor Blades,’ NACA WR-L-308 [formerly NACA Advanced Restricted Report 3G29] (1943).
1 2. G. W. Brooks, "The Application of Models to Helicopter Vibration and Flutter Research,’ Proceedings of the ninth annual forum of the American Helicopter Society (May 1953).
1 3. George E. Cooper, "Understanding and Interpreting Pilot Opinion,’ Aeronautical Engineering Review, vol. 16, no. 3, (Mar. 1957), p. 47-51.
[281] S. Salmirs and R. J. Tapscott, "The Effects of Various Combinations of Damping and Control Power on Helicopter Handling Qualities During Both Instrument and Visual Flight,’ NASA TN-D – 58 (1959).
[282] G. E. Cooper and R. P. Harper, Jr., "The Use of Pilot Rating in the Evaluation of Aircraft Handling Qualities," NASA TN-D-5153 (1969).
1 6. Harry H. Heyson and S. Katzoff, "Induced Velocities Near a Lifting Rotor with Nonuniform Disk Loading," NACA Report 1319 (1957).
1 7. Edwin P. Hartman, Adventures in Research, A History of Ames Research Center, 1940-1965, NASA SP-4302 (Washington, DC: NASA, 1970), p. 411.
1 8. William Warmbrodt, Charles Smith, and Wayne Johnson, "Rotorcraft Research Testing in the National Full-Scale Aerodynamics Complex at NASA Ames Research Center,’ NASA TM-86687 (May 1985); J. Sheiman and L. H. Ludi, "Qualitative Evaluation of Effect of Helicopter Rotor Blade Tip Vortex on Blade Airloads,’ NASA TN-D-1637 (1963).
1 9. James Sheiman, "A Tabulation of Helicopter Rotor-Blade Differential Pressures, Stresses, and Motions As Measured In Flight," NASA TM-X-952 (1964).
[287] John F. Ward, "Helicopter Rotor Periodic Differential Pressures and Structural Response Measured in Transient and Steady-State Maneuvers," Journal of the American Helicopter Society, vol. 16, no. 1 (Jan. 1971).
[288] F. Garren, J. R. Kelly, and R. W. Summer, "VTOL Flight Investigation to Develop a Decelerating Instrument Approach Capability," Society of Automotive Engineers Paper No. 690693 (1969), presented at the Aeronautics and Space Engineering and Manufacturing Meeting, Los Angeles, CA, Oct. 6-10, 1969.
[289] Wilmer H. Reed, III, "Review of Propeller-Rotor Whirl Flutter," NASA TR-R-264 (1967).
[290] William T. Yeager, Jr., and Raymond G. Kvaternik, "A Historical Overview of Aeroelasticity Branch and Transonic Dynamics Tunnel Contributions to Rotorcraft Technology and Development, NASA TM-2001-211054 / ARL-TR-2564, (Aug. 2001).
[291] RJ. Huston, "An Exploratory Investigation of Factors Affecting the Handling Qualities of a Rudimentary Hingeless Rotor Helicopter," NASA TN-D-341 8 (May 1966).
[292] I. H. Culver and J. E. Rhodes, "Structural Coupling in the Blades of a Rotating Wing Aircraft, IAS Paper No. 62-33 (1962).
[293] J. R. Kelly, F. R. Niessen, JJ. Thibodeaux, K. R. Yenni, and J. F. Garren, Jr., "Flight Investigation of Manual and Automatic VTOL Decelerating Instrument Approaches and Landings,’ NASA TN-D-7524 (July 1974).
[294] R. G. Kvaternik and W. G. Walton, Jr., "A Formulation of Rotor-Airframe Coupling for the Design Analysis of Vibrations of Helicopter Airframes," NASA RP-1089 (June 1982).
[295] Karen Jackson, Richard L. Boitnott, Edwin L. Fasanella, Lisa E. Jones, and Karen H. Lyle, "A Summary of DOD-Sponsored Research Performed at NASA Langley’s Impact Dynamics Research Facility," Journal of the American Helicopter Society, vol. 51, no. 1 (June 2004).
[296] H. K. Edenborough, T. M. Gaffey, and J. A. Weiberg, "Analysis and Tests Confirm Design of Proprotor Aircraft," AIAA Paper No. 72-803 (1972).
[297] James R. Hansen, Spaceflight Revolution, Langley Research Center From Sputnik to Apollo, NASA SP-4308 (Washington, DC: NASA 1995), pp. 81-111.
[298] A. W. Linden and M. W. Hellyer, "The Rotor Systems Research Aircraft," AIAA Paper No. 741277 (1974).
[299] Jack N. Nielsen and James C. Biggers, "Recent Progress in Circulation Control Aerodynamics, AIAA Paper No. 87-0001 (1987).
[300] W. Warmbrodt and J. L. McCloud, II, "A Full-Scale Wind Tunnel Investigation of a Helicopter Bearingless Main Rotor,’ NASA TM-81 321 (1981).
[301] M. Mosher and R. L. Peterson, "Acoustic Measurements of a Full-Scale Coaxial Helicopter,’ AIAA Paper No. 83-0722 (1983).
[302] Robert C. Ball, "Summary Highlights of the Advanced Rotor Transmission (ART) Program,’ AIAA Paper No. 92-3362 (1992).
[303] Wayne Johnson, Helicopter Theory (Princeton: Princeton University Press, 1980).
[304] D. C. Dugan, R. G. Erhart, and L. G. Schroers, "The XV-15 Tilt Rotor Research Aircraft,’ NASA TM-81244 / AVRADCOM Technical Report 80A-15 (1980).
[305] Martin D. Maisel, Demo J. Giulianetti, and Daniel C. Dugan, The History of The XV-15 Tilt Rotor Research Aircraft From Concept to Flight, NASA SP-2000-4517 (Washington, DC: NASA, 2000).
[306] Brenda Forman, "The V-22 Tiltrotor ‘Osprey:’ The Program That Wouldn’t Die,’ Vertiflite, vol.
39, no. 6, (Nov./Dec. 1993), pp. 20-23.
[307] Jack G. McArdle, "Outdoor Test Stand Performance of a Convertible Engine with Variable Inlet Guide Vanes for Advanced Rotorcraft Propulsion,’ NASA TM-88939 (1986).
[308] Raymond G. Kvaternik, "The NASA/Industry Design Analysis Methods for Vibration (DAMVIBS) Program—A Government Overview," AIAA Paper No. 92-2200 (1992).
[309] B. P. Gupta, A. H. Logan, and E. R. Wood, "Higher Harmonic Control for Rotary Wing Aircraft," AIAA Paper No. 84-2484 (1984).
[310] Ruth M. Martin, "NASA/AHS Rotorcraft Noise Reduction Program: NASA Langley Acoustics Division Contributions," Vertiflite, vol. 35, no. 4, (May/June 1989), pp. 48-52.
[311] W. R. Mantay, W. T. Yeager, Jr., M. N. Hamouda, R. G. Cramer, Jr., and C. W. Langston, ‘Aeroelastic model Helicopter Testing in the Langley TDT," NASA TM-86440 / USAAVSCOM TM-85-8-5 (1985).
[312] Robert J. Huston, Robert A. Golub, and James C. Yu, "Noise Considerations for Tilt Rotor, AIAA Paper 89-2359 (1989).
[313] Glenn E. Bugos, Atmosphere of Freedom, Sixty Years at the Ames Research Center, NASA SP – 4314 (Washington, DC: NASA 2000), pp. 21 1-246.
[314] Maisel, et al., History of the XV-15 Tilt-Rotor, pp. 1 10-1 14.
[315] William J. Snyder, John Zuk, and Hans Mark, "Tilt Rotor Technology Takes Off," AIAA Paper 89-2359 (1989).
[316] Wayne Johnson, "Model for Vortex Ring State Influence on Rotorcraft Flight Dynamics," NASA TP-2005-213477 (2005).
[317] The Center for Rotorcraft Innovation (CRI) Web site is: http://www. irotor. org.
[318] David D. Few, "A Perspective on 15 Years of Proof-of-Concept Aircraft Development and Flight Research at Ames—Moffett by the Rotorcraft and Powered-Lift Flight Projects Division, 1 970-1985," NASA RP-1 1 87 (1987).
[319] Edwin W. Aiken, Robert A. Jacobson, Michelle M. Eshow, William S. Hindson, and Douglas H. Doane, "Preliminary Design Features of the RASCAL—A NASA/Army Rotorcraft In-Flight Simulator," AIAA Paper 92-4175 (1992); Robert T. N. Chen, William S. Hindson, and Arnold W. Mueller, "Acoustic Flight Tests of Rotorcraft Noise-Abatement Approaches Using Local Differential GPS Guidance," NASA TM-1 10370 (1995); Robert M. Kufeld and Paul C. Loschke, "UH-60 Airloads Program — Status and Plans," AIAA Paper 91-3142 (1991).
[320] In 2003, Congress authorized the Joint Planning and Development Office (JPDO) coordinating the activities of multiple Federal agencies in planning Next Generation Air Transportation System to implement the transformation of the national airspace system.
[321] Mark Liptak, "International Helicopter Study Team (IHST) Overview Briefing,’ presented at Helicopter Association International HELI EXPO Meeting, Houston, TX, Feb. 21-23, 2009 (see http://www. ihst. org).
[322] The author is grateful to Karl Bender of NASA’s Dryden Research Library for helping to gather source materials. For a concise introduction to sonic boom theory, see Kenneth J. Plotkin and Domenic J. Maglieri, "Sonic Boom Research: History and Future,’ American Institute of Aeronautics and Astronautics (AIAA), Paper 2003-3575, June 23, 2003.
[323] For its development and testing, see Richard P. Hallion, Supersonic Flight: Breaking the Sound Barrier and Beyond: The Story of the Bell X-1 and Douglas D-558 (New York: Macmillan, 1 977).
[324] Some of the personnel stationed at Muroc when Yeager broke the sound barrier later recalled hearing a sonic boom, but these may have been memories of subsequent flights at higher speeds. One of NASA’s top sonic boom experts has calculated that at Mach 1.06 and 41,000 feet above ground level, atmospheric refraction and absorption of the shock waves would almost certainly have dissipated the XS-1 ‘s sonic boom before it could reach the surface. E-mail, Edward A. Haering, Dryden Flight Research Center, to Lawrence R. Benson, Apr. 8, 2009.
[325] "Ernst Mach,’ Stanford Encyclopedia of Philosophy, Mar. 21, 2008, htp://plato. stanford. edu/entries/Ernst-mach; Jeff Scott, "Ernst Mach and Mach Number,’ Nov. 9, 2003, htp://www. aerospaceweb. org/question/history/q0149.shmtl.
[326] By the end of World War II, ballistic waves were well understood, e. g., J. W.M. Dumond, et al., "A Determination of the Wave Forms and Laws of Propagation and Dissipation of Ballistic Shock Waves,’ Journal of the Acoustical Society of America (hereinafter cited as JASA), vol. 1 8, no. 1 (Jan. 1946), pp. 97-118.
[327] David Darling: The Complete Book of Spaceflight: From Apollo 1 to Zero Gravity (Hoboken,
NJ: John Wiley and Sons, 2003), p. 457. See also "Airpower: Missiles and Rockets in Warfare,’ http://www. centennialofflight. gov/essay/Air_Power/Missiles/AP29.htm; and Bob Ward, Dr. Space: The Life of Wernher von Braun (Annapolis: Naval Institute, 2005), p. 43.
[328] The definitive biography, Van Braun: Dreamer of Space, Engineer of War, by Michael J. Neufeld (New York: Alfred A. Knopf, 2007), pp. 1 33-1 36, leaves open the question of whether the Germans at Peenemunde heard the first manmade sonic booms in 1942 when their A4 test rockets exceeded Mach 1 about 25 seconds after launch.
[329] For the authoritative history of the NACA/NASA mission at Edwards AFB, see Richard P. Hallion and Michael H. Gorn, On the Frontier: Experimental Flight at NASA Dryden (Washington, DC: Smithsonian, 2003).
[330] Plotkin and Maglieri, "Sonic Boom Research,’ pp. 1-2.
[331] Introduction to "The Battle of the Bangs,’ Flight and Aircraft Engineer, vol. 61, no. 2289 (Dec. 5, 1952), p. 696, http://www. flightgbbal. com/pdfarchive/view/1952/%203457.
[332] 1 . G. B. Whitham, "The Flow Pattern of a Supersonic Projectile,’ Communications on Pure and Applied Mathematics, vol. 5, no. 3 (1952), pp. 301-348 (available at http://www3. interscience. wiley. com/journal/l 13395160/issue) and "On the Propagation of Weak Shock Waves,’ Journal of Fluid Dynamics, vol. 1, No. 3 (Sept. 1956), pp. 290-31 8 (available at http://joumals. cambridge. org/action/displayjoumal? jid=JFM), and described in Larry J. Runyan, et al., Sonic Boom Literature Survey, vol. II, Capsule Summaries, (Seattle: Boeing Commercial Airplane Co. for the FAA), Sept. 1973, pp. 6-8, 59-60. Whitham later taught at both the Massachusetts and California Institutes of Technology.
12. Air Force Flight Test Center History Office, Ad Inexplorata: The Evolution of Flight Testing at Edwards Air Force Base (Edwards AFB: AFFTC, 1996), Appendix B, p. 55.
1 3. John G. Norris, "AF Says ‘Sonic Boom’ Can Peril Civilians,’ Washington Post and Times Herald (hereinafter cited as Washington Post), Nov. 9, 1954, pp. 1, 12.
[335] One of the first studies on focused booms was G. M. Lilley, et al., "Some Aspects of Noise from Supersonic Aircraft,’ Journal of the Royal Aeronautical Society, vol. 57 (June 1953), pp. 396-41 4, as described in Runyan, Sonic Boom Capsule Summaries, p. 54. AFFTC used F-100s to conduct the first in-flight boom measurements: Marshall E. Mullens, "A Flight Test Investigation of the Sonic Boom,’ AFFTC TN-56-20, May 1956.
[336] History of the 3201 Air Base Group, Eglin AFB, Jul.—Sept. 1951, Abstract from Information Retrieval and Indexing System (IRIS) No. 438908, Air Force Historical Research Center, Maxwell AFB, AL.
[337] F. Walkden, "The Shock Pattern of a Wing-Body Combination Far from the Flight Path,’ Aeronautical Quarterly, vol. 9, pt. 2 (May 1958), pp. 1 64-194; described in Runyan, Sonic Boom Capsule Summaries, 8-9. Both Walkden and Whitman did their pioneering studies at the University of Manchester.
[338] Fred Keefe and Grover Amen, "Boom,” The New Yorker, May 1 6, 1962, pp. 33-34.
1 8. Albion B. Hailey, "AF Expert Dodges Efforts to Detail ‘Sonic Boom’ Loss,’ Washington Post,
Aug. 25, 1960, p. A15.
[340] J. P. and E. G.R Taylor, "A Brief Legal History of the Sonic Boom in America,’ Aircraft Engine Noise and Sonic Boom (Neuilly Sur Seine, France: NATO Advisory Group for Aerospace Research and Development [AGARD], 1969), Conference Proceedings (CP) No. 42, Paris, May 1969, pp. 2-1-2-1 1.
20. "Warplanes Fill Skies Over U. S. and Canada,’ Los Angeles Times, Sept. 10, 1960, p. 4; Albion B. Halley and Warren Kornberg, "U. S. Tests Air Defenses in 3000-Plane ‘Battle,”’ Washington Post, Oct. 15, 1961, pp. A1, B1; Richard Witkin, "Civilian Planes Halted 1 2 Hours in Defense Test,’ New York Times, Oct. 15, 1961, pp. 1,46.
[342] . Marcelle S. Knaack, Post-World War II Bombers, 1945-1973 (Washington, DC: Government Printing Office (hereinafter cited as GPO) for Office of Air Force History, 1 988), pp. 394-395 (vol. 2, Encyclopedia of U. S. Air Force Aircraft and Missile Systems).
[343] "Jet Breaks 3 Records—and Many Windows,’ Los Angeles Times, Mar. 6, 1962, p. 1. In reality, most of the damage was done while accelerating after the refuelings.
[344] For the definitive account of political and economic aspects of the SST and subsequent programs (as well as many technical details), see Erik M. Conway, High-Speed Dreams: NASA and the Technopolitics of Supersonic Transportation, 1945-1999 (Baltimore: Johns Hopkins, 2005), pp. 27-45 cited here. For an earlier study by an insider, see F. Edward McLean, "Supersonic Cruise Technology/’ NASA Special Publication (SP) 472 (Washington, DC: GPO, 1985). For an account focused on its political aspects, see Mel Howitch, Clipped Wings: The American SST Conflict (Cambridge: MIT, 1982).
[345] McLean, Supersonic Cruise Technology, pp 35-46; Joseph R. Chambers, Innovation in Flight; "Research of the NASA Langley Research Center on Revolutionary Concepts for Aeronautics,’ NASA SP-2005-4539, pp. 25-28.
[346] FAA Historical Chronology, 1926-1996, http://ww. faa. gov/about/media/b-chron. pdf.
For Quesada’s role, see Stuart I. Rochester, Takeoff at Mid-Century: Federal Civil Aviation Policy in the Eisenhower Years, 1953-1961 (Washington, DC: GPO for FAA, 1976). For the activism of Halaby and the demise of the SST after his departure, see Richard J. Kent, Jr., Safe, Separated, and Soaring: A History of Civil Aviation Policy, 1961-1972 (Washington, DC: GPO for FAA, 1980).
[347] NASA’s HSFRC became the FRC in 1959. For an overall summary of Langley’s supersonic activities, see Chambers, Innovations in Flight, ch. 1, "Supersonic Civil Aircraft: The Need for Speed,’ pp. 7-70.
[348] Based on author’s review of Section 7.4, "Noise, Aircraft’ in volumes of the Index of NACA Technical Publications (Washington DC: NACA Division of Research Information) covering the years 1915-1957.
[349] Telephone interview, Domenic Maglieri by Lawrence Benson, Feb. 6, 2009.
[350] A. B. Fryer, et al., "Publications in Acoustics and Noise Control from the NASA Langley Research Center during 1940-1976,’ NASA TM-X-74042, July 1977. The following abbreviations are used for NASA publications cited in the notes: Conference Publication (CP), Contractor Report (CR), Reference Publication (RP), Special Publication (SP), Technical Memorandum (TM), formerly classified Tech Memo (TM-X), Technical Note (TN), Technical Paper (TP), and Technical Report (TR). Bibliographic data and often full text copies can be accessed through the NASA Technical Reports Server (NTRS), http://ntrs. nasa. gov/search. jsp.
30. For a chronological summary of selected projects during first decade, see Johnny M. Sands, "Sonic Boom Research (1958-1968),’ FAA, Nov. 1968, Defense Technical Information Center (DTIC) document AD 684806.
[352] . Domenic J. Maglieri, Harvey H. Hubbard, and Donald L. Lansing, "Ground Measurements of the Shock-Wave Noise from Airplanes in Level Flight at Mach Numbers to 1 .4 and Altitudes to
45.0 Feet,’ NASA TN-D-48, Sept. 1959; Lindsay J. Lina and Domenic J. Maglieri, "Ground Measurements of Airplane Shock-Wave Noise at Mach Numbers to 2.0 and at Altitudes to
60.0 Feet,’ NASA TN-D-235, Mar. 1960.
[353] Maglieri, Vera Huckel, and Tony L. Parrott, "Ground Measurements of Shock-Wave Pressure for Fighter Airplanes Flying at Very Low Altitudes. . .," NASA TN-D-3443, July 1966 (superseded classified TMX-611, 1961).
[354] Gareth H. Jordan, "Flight Measurements of Sonic Booms and Effects of Shock Waves on Aircraft," in Society of Experimental Test Pilots Quarterly Review, vol. 5, No. 1 (1961), pp. 117-131, presented at SETP Supersonic Symposium, Sept. 29, 1961.
[355] John O. Powers, J. M. Sands, and Maglieri, "Survey of United States Sonic Boom Overflight Experimentation," NASA TM-X-66339, May 1969, p. 5; USAF Fact Sheet, "Sonic Boom," Oct. 2005, http://www. af. mil/factsheets/fsID=184; Telephone interview, Maglieri by Benson, Mar. 19, 2009.
[356] Maglieri and Hubbard, "Ground Measurements of the Shock-Wave Noise from Supersonic Bomber Airplanes in the Altitude Range from 30,000 to 50,000 Feet," NASA TN-D-880, July 1961.
[357] Jordan, "Flight Measurements of Sonic Booms."
[358] Ibid.; Maglieri and Donald L. Lansing, "Sonic Booms from Aircraft in Maneuvers," NASA TN – D-2370, July 1 964; Hubbard, et al., "Ground Measurements of Sonic-Boom Measurements for the Altitude Range of 10,000 to 75,000 Feet," NASA TR-R-198, July 1964. (Both reports were based on the tests in 1961.)
[359] Harriet J. Smith, "Experimental and Calculated Flow Fields Produced by Airplanes Flying at Supersonic Speeds," NASA TN-D-621, Nov. 1960; J. F. Bryant, Maglieri, and V. S. Richie, "In-Flight Shock-Wave Measurements Above and Below a Bomber Airplane at Mach Numbers from 1.42 to 1.69," NASA TN-D-1968, Oct. 1963.
[360] NASA Flight Research Center, "X-15 Program" [monthly report], Sept. 1961, Dryden archive,
File LI-6-10A-1 3 (Peter Merlin assisted the author in finding this and other archival documents.); Karen S. Green and Terrill W. Putnam, "Measurements of Sonic Booms Generated by an Airplane Flying at Mach 3.5 and 4.8," NASA TM-X-31 26, Oct. 1974. (Since hypersonic speeds were not directly relevant for the SST, a formal report was delayed until NASA began planning reentry flights for the Space Shuttle.) For a history of the X-15 program, see Hallion and Gorn, On the Frontier, pp. 101-125.
40. Charles W. Nixon and Hubbard, "Results of the USAF-NASA-FAA Flight Program to Study Community Response to Sonic Booms in the Greater St. Louis Area,’ NASA TN-D-2705, May 1965; Clark, et al., "Studies of Sonic Boom Damage,’ NASA CR-227, May 1965.
[362] . Sands, "Sonic Boom Research (1958-1968),’ p. 3.
[363] Maglieri and Garland J. Morris, "Measurement of Response of Two Light Airplanes to Sonic Booms," NASA TN-D-1941, Aug. 1963.
[364] D. A. Hilton, Maglieri, and R. Steiner, "Sonic-Boom Exposures during FAA Community Response Studies over a 6-Month Period in the Oklahoma City Area," NASA TN-D-2539, Dec. 1964.
[365] Conway, High-Speed Dreams, pp. 121-1 22.
[366] Thomas H. Higgins, "Sonic Boom Research and Design Considerations in the Development of a Commercial Supersonic Transport,’ JASA, vol. 39, no. 5, pt. 2 (Nov. 1966), pp. 526-531.
[367] David. A. Hilton, Vera Huckel, and Maglieri, "Sonic Boom Measurements during Bomber Training Operations in the Chicago Area,’ NASA TN-D-3655, Oct. 1966.
[368] Histories of the 4700 Air Defense Wing, Jan.-Mar. and Apr.-June 1960, IRIS abstracts; History of the 84th Fighter Group, Jan.-Dec. 1961, IRIS abstract; Telephone interview, Maglieri by Benson, Mar. 1 3, 2009.
[369] William H. Andrews, "Summary of Preliminary Data Derived from the XB-70 Airplanes,’ NASA TM-X-1 240, June 1966, pp. 11-12. Despite being 3.5 times heavier than the B-58, the XB-70’s bow wave proved to be only slightly stronger.
[370] Maglieri, et al., "A Summary of XB-70 Sonic Boom Signature Data, Final Report,’ NASA CR-1 89630, Apr. 1992. Until this report, the 1965-1966 findings were filed away unpublished. The original oscillographs were also scanned and digitized at this time for use in the High-Speed Research Program.
[371] FRC, "NASA XB-70 Flight Research Program,’ Apr. 1966, Dryden archive, File L2-4-4D-3, p. 10 quoted. See also C. M. Plattner, "XB-70A Flight Research: Phase 2 to Emphasize Operational Data,’ Aviation Week, June 1 3, 1966, pp. 60-62.
51 . NASA Dryden Fact Sheet, "XB-70,’ http://www. nasa. gov/centers/dryden/new/FactSheets/ FS-084-DFRC_prt. htm; Hallion and Gorn, On the Frontier, pp. 176-1 85, 421.
[373] Maglieri, "Summary of XB-70 Sonic Boom,’ pp. 4-5.
[374] R. T. Klinger, ”YF-1 2A Flight Test Sonic Boom Measurements,’ Lockheed Advanced Development Projects Report SP-815, June 1, 1965, Dryden archive, File LI-4-10A-1.
[375] John O. Powers, J. M. Sands, and Maglieri, "Survey of United States Sonic Boom Overflight Experimentation,’ NASA TM-X-66339, May 1969, pp. 9, 1 2-1 3.
[376] Peter W. Merlin, From Archangel to Senior Crown: Design and Development of the Blackbird (Res – ton, VA: AIAA, 2008), pp. 106-107, 116-118, 179; Hallion and Gorn, On the Frontier, p. 1 87.
[377] NSBEO, "Sonic Boom Experiments at Edwards Air Force Base; Interim Report’ (prepared under contract by Stanford Research Institute), pp. 1 -2, (hereinafter cited as SRI, "Edwards AFB Report’). For political and bureaucratic background on the NSBEO, see Conway, High-Speed Dreams, pp. 1 22-1 23.
[378] SRI, "Edwards AFB Report," p. 9.
[379] Maglieri, et al., "Summary of Variations of Sonic Boom Signatures Resulting from Atmospheric Effects," Feb. 1967, and "Preliminary Results of XB-70 Sonic Boom Field Tests During National Sonic Boom Evaluation Program," Mar. 1967, Annex C-1 and C-2, in SRI, "Edwards AFB Report;" H. H. Hubbard and D. J. Maglieri, "Sonic Boom Signature Data from Cruciform Microphone Array Experiments during the 1966-1 967 EAFB National Sonic Boom Evaluation Program," NASA TN-D – 6823, May 1972.
[380] SRI, "Edwards AFB Report," pp. 17-20, Annexes C-F; Maglieri, et al., "Sonic Boom Measurements for SR-71 Aircraft Operating at Mach Numbers to 3.0 and Altitudes to 24834 Meters," NASA TN-D-6823, Sept. 1972.
60. SRI, "Edwards AFB Report,’ pp. 1 1-16, Annex B; K. D. Kryter, "Psychological Experiments on Sonic Booms Conducted at Edwards Air Force Base, Final Report,’ (Menlo Park: SRI, 1968), summarized by Richard M. Roberds, "Sonic Boom and the Supersonic Transport,’ Air University Review, vol. 22, No. 7 (July-Aug. 1971), pp. 25-33.
[382] . SRI, "Edwards AFB Report,’ pp. 20-23, Annexes G and H; David Hoffman, "Sonic Boom Tests Fail to Win Any Boosters,’ Washington Post, Aug. 3, 1967, p. A3; A. J. Bloom, et al. (SRI), "Response of Structures to Sonic Booms Produced by XB-70, B-58, and F-104 Aircraft. . . at Edwards Air Force Base, Final Report,’ NSBEO 2-67, Oct. 1967; D. S. Findley, et al., "Vibration Responses of Test Structure No. 1 during the. . . National Sonic Boom Program,’ NASA TM-X-72706, June 1975, and "Vibration Responses of Test Structure No. 2 . . . ,’ NASA TM-X-72704, June 1975.
[383] TRACOR, Inc., "Public Reactions to Sonic Booms,’ NASA CR-1665, Sept. 1970.
[384] Hilton and Herbert R. Henderson documented the sonic boom measurements from the Apollo 15, 16, and 17 missions in NASA TNs D-6950, D-7606, and D-7806, published from 1972 to 1974.
[385] George T. Haglund and Edward J. Kane, "Flight Test Measurements and Analysis of Sonic Boom Phenomena Near the Shock Wave Extremity,’ NASA CR-2167, Feb. 1973; Telephone interview, Maglieri by Benson, Mar. 1 3, 2009.
[386] Harry W. Carlson, "Some Notes on the Present Status of Sonic Boom Prediction and Minimization Research,’ Third Conference on Sonic Boom Research. . . Washington, DC, Oct. 29-30, 1970, NASA SP-255, 1971, p. 395.
[387] Carlson, "An Investigation of Some Aspects of the Sonic Boom by Means of Wind-Tunnel Measurements of Pressures about Several Bodies at a Mach Number of 2.01,’ NASA TN-D-161, Dec. 1959. Carlson used Langley’s 4 by 4 Supersonic Pressure Wind Tunnel, completed in 1 948, for most of his experiments.
[388] For examples of these wind tunnel experiments, see Runyan, "Sonic Boom Capsule Summaries, as well as the NTRS bibliographical database.
[389] Carlson, "Wind Tunnel Measurements of the Sonic-Boom Characteristics of a Supersonic Bomber Model and a Correlation with Flight-Test Ground Measurements," NASA TM-X-700, July 1962.
[390] Carlson, "Correlation of Sonic-Boom Theory with Wind Tunnel and Flight Measurements," NASA TR-R-21 3, Dec. 1964. p. 1.
[391] Evert Clark, "Reduced Sonic Boom Foreseen for New High-Speed Airliner," New York Times, Jan. 1965, pp. 7, 1 2 (based on visit to NASA Langley).
71 . F. Edward McLean, "Some Nonasymptotic Effects of the Sonic Boom of Large Airplanes," NASA TN-D-2877, June 1965.
[393] Carlson, "Correlation of Sonic-Boom Theory," pp. 2-23. For an earlier status report on supersonic work at Langley and some at Ames, see William J. Alford and Cornelius Driver, "Recent Supersonic Transport Research," Astronautics & Aeronautics, vol. 2, No. 9 (Sept. 1 964), pp. 26-37; Chambers, Innovation in Flight, pp. 32-34.
[394] Carlson, "Configuration Effects on Sonic Boom,’ Proceedings of NASA Conference on Supersonic-Transport Feasibility Studies and Supporting Research, Sept. 17-19, 1963 . . . Hampton, VA, NASA TM-X-905, Dec. 1963, p. 381.
[395] Hubbard and Maglieri, "Factors Affecting Community Acceptance of the Sonic Boom,’ ibid., pp. 399-412.
[396] McLean, Supersonic Transport Technology, p. 46.
[397] JASA, vol. 39, no. 5, pt. 2 (Nov. 1966), pp. 519-572.
[398] F. Edward McLean and Barrett L. Shrout, "Design Methods for Minimization of Sonic Boom Pressure-Field Disturbances,’ ibid., 51 9-525. For an updated report, see Carlson, McLean, and Shrout, "A Wind Tunnel Study of Sonic-Boom Characteristics for Basic and Modified Models of a Supersonic Transport Configuration,’ NASA TM-X-1 236, May 1966.
[399] Evert Clark, "Sonic Boom to Limit Speed of Superjets Across U. S.,’ New York Times, Oct. 31 1966, pp. 1,71; "George Gardner, "Overland Flights by SST Still in Doubt,’ Washington Post, July 10, 1967, p. A7.
[400] A. R. Seebass, ed., Sonic Boom Research: Proceedings of a Conference. . . Washington, DC, Apr. 12, 1967, NASA SP-147, 1967.
[401] Maglieri, "Sonic Boom Flight Research-Some Effects of Airplane Operations and the Atmosphere on Sonic Boom Signatures,’ ibid., pp. 25-48.
81 . A. R. Seebass, "Preface,” ibid., p. iii.
[403] Carlson, "Experimental and Analytical Research on Sonic Boom Generation at NASA,’ ibid., pp. 9-23.
[404] Ira R. Schwartz, ed., Sonic Boom Research, Second Conference, Washington, DC, May 9-10, 1968, NASA SP-1 80, 1968, pp. iv-v.
[405] Ibid., 1 -193; For more on the ARAP computer program, see Wallace D. Hayes, et al., "Sonic Boom Propagation in a Stratified Atmosphere with Computer Program,’ NASA CR-1 299, Apr. 1969.
[406] Second Conference on Sonic Boom Research, p. vii.
[407] AGARD, Aircraft Engine Noise and Sonic Boom (see note 19 for bibliographical data).
[408] For a survey, see Daniel D. Baals and William R. Corliss, "Wind Tunnels of NASA," SP-440 (Washington, DC: NASA, 1981).
[409] Phillip M. Edge and Harvey H. Hubbard, "Review of Sonic-Boom Simulation Devices and Techniques," Dec. 1970, JASAJournal, vol. 51, No. 2, pt. 2 (Feb. 1972), p. 723.
[410] W. D. Beasly, J. D. Brooks, and R. L. Barger, "A Laboratory Investigation of N-Wave Focusing, NASA TN-D-5306, July 1 969; J. D. Brooks, et al., "Laboratory Investigation of Diffraction and Reflection of Sonic Booms by Buildings," NASA TN-D-5830, June 1970.
[411] Edge and Hubbard, "Review of Sonic Boom Simulation,’ pp. 724-728; Hugo E. Dahlke, et al., "The Shock-Expansion Tube and Its Application as a Sonic Boom Simulator,’ NASA CR-1055, June 1968; R. T Sturgielski, et al., "The Development of a Sonic Boom Simulator with Detonable Gases,’ NASA CR-1 844, Nov. 1971.
91 . Jerome Lukas and Karl D. Kryler, "A Preliminary Study of the Awakening and Startle Effects of Simulated Sonic Booms,’ NASA CR-1 193, Sept. 1968, "Awakening Effects of Simulated Sonic Booms and Subsonic Aircraft Noise. . . ,’ NASA CR-1599, May 1970.
[413] David Hoffman, "Report Sees Need for Study on Sonic Boom Tolerance,’ Washington Post, June 26, 1968, p. A3.
[414] Ira R. Schwartz, Sonic Boom Simulation Facilities,’ AGARD, Aircraft Engine Noise and Sonic Boom, p. 29-1.
[415] Philip M. Edge and William H. Mayes, "Description of Langley Low-Frequency Noise Facility and Study of Human Response to Noise Frequencies below 50 cps,’ NASA TN-D-3204, Jan. 1966.
[416] Roger Tomboulian, Research and Development of a Sonic Boom Simulation Device, NASA CR – 1 378, July 1969; Stacy V. Jones, "Sonic Boom Researchers Use Simulator,’ New York Times, May 10, 1969, pp. 37, 41.
[417] Ira R. Schwartz, "Sonic Boom Simulation Facilities,’ p. 29-6.
[418] B. K. O. Lundberg, "Aviation Safety and the SST,’ Astronautics & Aeronautics, vol. 3, No. 1 (Jan. 1966), p. 28. Lundberg was a Swedish scientist very critical of SSTs.
[419] See Conway, High-Speed Dreams, pp. 1 1 8-156.
[420] "The Shattering Boom,’ New York Times, June 8, 1968, p. 30.
[421] Ira R. Schwartz, ed., Third Conference on Sonic Boom Research. . . Washington, DC,
Oct. 29-30, 1970, NASA SP-255, 1971. The papers from the ASA’s Houston symposium were published in JASA, vol. 51, No. 2 (Feb. 1972), pt. 2.
[422] Third Conference on Sonic Boom Research, Preface by Ira Schwartz, p. iv.
[423] R. Seebass, "Comments on Sonic Boom Research,’ ibid., p. 411.
[424] Lynn W. Hunton, "Comments on Low Sonic Boom Configuration Research, ibid., p. 417.
[425] Carlson, "Sonic Boom Prediction and Minimization Research,’ ibid., p. 397.
[426] For a detailed postmortem, see Edward Wenk, "SST—Implications of a Political Decision, Astronautics & Aeronautics, vol. 9, No. 10 (Oct. 1971), pp. 40-49.
[427] Compiled by screening B. A. Fryer, et al., "Publications in Acoustics and Noise Control from the NASA Langley Research Center During 1940-1976," NASA TM-X-7402, July 1977. Five reports for 1967 that Maglieri (in reviewing the draft of this chapter) found missing from Fryer’s compilation have been added to that column.
[428] Stephen D. Ambrose, Nixon: Triumph of a Politician, vol. 2 (New York: Simon and Schuster, 1989), p. 433, cited by Conway, High-Speed Dreams, p. 153. For the political and bureaucratic background of the AST program, see Conway, pp. 1 53-158.
[429] F. Edward McLean, "SCAR Program Overview," Proceedings of the SCAR Conference. . . Hampton, VA, Nov. 9-12, 1976, pt. 1, NASA CP-001, 1976, pp. 1-3; McLean, Supersonic Cruise Technology, pp. 101-102.
[430] McLean, Supersonic Cruise Technology, pp. 104-108; Sherwood Hoffman, "Bibliography of Supersonic Cruise Aircraft Research (SCAR),’ NASA RP-1003, Nov. 1977, pp. 1-5.
1 1 0. Chambers, Innovation in Flight, pp. 39-40.
[432] McLean, Supersonic Cruise Technology, p. 103.
1 1 2. FAA Chronology, Apr. 27, 1 973. The rule was included as Federal Aviation Regulation (FAR) Section 91.817, Civil Aircraft Sonic Boom, effective Sept. 30, 1963.
1 1 3. Marvin Miles, "Hopes for SST Are Dim but R&D Continues—Just in Case,’ Los Angeles Times, Nov. 25, 1973, pp. G1, 11; McLean, Supersonic Cruise Technology, pp. 117-11 8; Conway, High-Speed Dreams, pp. 1 76-1 80.
[435] F. Edward McLean, "Some Non-asymptotic Effects on the Sonic Boom of Large Airplanes,’ NASA TN-D-2877, June 1965, as interpreted by Plotkin and Maglieri, "Sonic Boom Research,’ p. 5.
1 15. Miles, "Sonic Boom Not Insoluble, Scientist Says,’ Los Angeles Times, Dec. 10, 1970, pp. E4- E5; David S. Miller and Carlson, "Sonic Boom Minimization by Application of Heat or Force Fields to Airplane Airflow,’ NASA TN-D-5582, Dec. 1969; Rudolph J. Swigart, "An Experimental Study in the Validity of the Heat-Field Concept for Sonic Boom Alleviation,’ NASA CR-2381, Mar. 1974.
1 1 6. Antonio Ferri, Huai-Chu Wang, and Hans Sorensen, "Experimental Verification of Low Sonic Boom Configuration,’ NASA CR-2070, June 1973.
1 1 7. For a retrospective, see Percy J. Bobbit and Maglieri, "Dr. Antonio Ferri’s Contribution to Supersonic Transport Sonic-Boom Technology,’ Journal of Spacecraft and Rockets, vol. 40, no. 4 (July-Aug. 2003), pp.459-466.
1 1 8. A. R. George and R. Seebass, "Sonic-Boom Minimization,’ Nov. 1970, in JASA, vol. 51, no. 2, pt. 3 (Feb. 1972), pp. 686-694; A. R. Seebass and A. R George, "Sonic Boom Minimization through Aircraft Design and Operation,’ AIAA Paper 73-241, Jan. 1973; A. R. Seebass and A. R. George, "The Design and Operation of Aircraft to Minimize Their Sonic Boom,’ Journal of Aircraft, vol. 11, no. 9 (Sept. 1974), pp. 509-517. (Quote is from p. 516.)
1 1 9. Charles L. Thomas, "Extrapolation of Sonic Boom Pressure Signatures by the Waveform Parameter Method,’ NASA TN-D-6823, June 1972.
1 20. Carlson, Raymond L. Barger, and Robert J. Mack, "Application of Sonic-Boom Minimization Concepts in Supersonic Transport Design,’ NASA TN-D-721 8, June 1973.
[442] Ibid., p. 28.
[443] Edward J. Kane, "A Study to Determine the Feasibility of a Low Sonic Boom Supersonic Transport," AIAA Paper 73-1035, Oct. 1973. See also NASA CR-2332, Dec. 1973.
1 23. Sherwood Hoffman, "Bibliography of Supersonic Cruise Aircraft Research (SCAR)" [1 9721977], NASA RP-1003, Nov. 1977, and "Bibliography of Supersonic Cruise Research (SCR) Program from 1977 to Mid-1 980," NASA RP-1063, Dec. 1980.
1 24. Christine M. Darden, "Minimization of Sonic-Boom Parameters in Real and Isothermal Atmospheres,’ NASA TN D-7842, Mar. 1975; Darden, "Sonic Boom Minimization with Nose-Bluntness Relaxation,’ NASA TP-1 348, Jan. 1979; Darden, "Affordable/Acceptable Supersonic Flight: Is It Near?’ 40th Aircraft Symposium, Japan Society for Aeronautical and Space Sciences (JSASS), Yokohama, Oct. 9-1 1,2002.
1 25. Robert J. Mack and Darden, "Wind-Tunnel Investigation of the Validity of a Sonic-Boom – Minimization Concept,’ NASA TP-1421, Oct. 1979. They had previously presented their findings at an AIAA conference in Seattle on Mar. 12-14, 1 979 as "Some Effects of Applying Sonic Boom Minimization to Supersonic Cruise Aircraft Design,’ AIAA Paper 79-0652, also published in Journal of Aircraft, vol. 17, no. 3 (Mar. 1980), pp. 1 82-1 86.
1 26. Darden and Mack, "Current Research in Sonic-Boom Minimization,’ Proceedings of the SCAR Conference [ 1976], pt. 1, pp. 525-541 (quote from p. 526). Darden had discussed some of these topics in "Sonic Boom Theory – Its Status in Prediction and Minimization,’ AIAA Paper 76-1, presented at the AIAA Aerospace Sciences Meeting, Washington, DC, Jan. 26-28, 1976.
1 27. Carlson, "Simplified Sonic-Boom Prediction," NASA TP-1 1 22, Mar. 1978, p. 1.
1 28. Paul Holloway of Langley and colleagues from the Ames, Marshall, and Johnson centers presented an early analysis, "Shuttle Sonic Boom-Technology and Predictions," in AIAA Paper 73-1039, Oct. 1973.
1 29. NASA HQ (Myron S. Malkin), Environmental Impact Statement: Space Shuttle Program Final), Apr. 1978, pp. 106-1 16.
1 30. Including measurements in Hawaii, with the Shuttle at 253,000 feet and moving at Mach 23. Telephone interview, Maglieri by Benson, Mar. 1 8, 2009.
[452] Plotkin and Maglieri, "Sonic Boom Research,’ pp. 5-6, 10.
1 32. Raymond L. Barger, "Sonic-Boom Wave-Front Shapes and Curvatures Associated with Maneuvering Flight,’ NASA TP-161 1, Dec. 1979. Fig. 5 is from p. 23.
[454] James and Associates, ed., YF-12 Experiments Symposium: A conference held at Dryden Flight Research Center. . . Sept. 13-15, 1978, NASA CP-2054, 1978; Hallion and Gorn, On the Frontier, Appendix P [YF-12 Flight Chronology, 1969-1978], pp. 423-429. The Dryden Center tested an oblique wing aircraft, the AD-1, from 1979 to 1982. Although this configuration might have sonic boom benefits at mid-Mach speeds, it was not a consideration in this experimental program.
1 34. "Second Concorde Noise Report for Dulles Shows Consistency,’ Aviation Week, July 1 9, 1976, p. 235; William Claiborne, "Those Mystery Booms Defy Expert Explanation,’ Washington Post, Dec. 24, 1977, p. A1.
1 35. Deborah Shapely, "East Coast Mystery Booms: A Scientific Suspense Tale,’ Science, vol. 199, no. 4336 (Mar. 31, 1978), pp. 1416-1417; "Concordes Exempted from Noise Rules,’ Aviation Week, July 3, 1978, p. 33; GJ. MacDonald, et al., "Jason 1978 Sonic Boom Report,’ JSR-78-09 (Arlington, VA: SRI International, Nov. 1978); Richard Kerr, "East Coast Mystery Booms: Mystery Gone but Booms Linger On,’ Science, vol. 203, no. 4337 (Jan. 19, 1979), p. 256; John H. Gardner and Peter H. Rogers, "Thermospheric Propagation of Sonic Booms from the Concorde Supersonic Transport,’ Naval Research Laboratory Memo Report 3904, Feb. 14, 1979 (DTIC AD A067201).
1 36. Robert Kelly, "Supersonic Cruise Vehicle Research/Business Jet,’ Supersonic Cruise Research 79: Proceedings of a Conference. . . Hampton, VA, Nov. 13-16, 1979, NASA CP-2108, pt. 2, pp. 935-944.
1 37. Conway, High-Speed Dreams, pp. 1 80-1 88; Chambers, Innovations in Flight, p. 48.
[459] Darden, "Charts for Determining Potential Minimum Sonic-Boom Overpressures for Supersonic Cruise Aircraft," NASA TP-1 820, May 1981; Darden and R. J. Mack, "Some Effects of Applying Sonic Boom Minimization to Supersonic Aircraft," Journal of Aircraft, vol. 17, no. 3 (Mar. 1980), pp. 1 82-1 86.
[460] Hubbard, Maglieri, and David G. Stephens, "Sonic-Boom Research-Selected Bibliography with Annotation," NASA TM-87685, Sept. 1986.
[461] J. Micah Downing, "Lateral Spread of Sonic Boom Measurements from US Air Force Boomfile Flight Tests,’ High Speed Research: Sonic Boom; Proceedings of a Conference. . . Hampton, VA, Feb. 25-27, 1992, vol. 1, NASA CR-3172, pp. 117-129. For a description, see Robert E. Lee and Downing, “Boom Event Analyzer Recorder: the USAF Unmanned Sonic Boom Monitor,’ AIAA Paper 93-4431, Oct. 1993.
[462] Plotkin and Maglieri, “Sonic Boom Research,’ p. 6.
[463] John G. Norris, “AF Says ‘Sonic Boom’ Can Peril Civilians—Might be Used as Weapon,’ Washington Post, Nov. 9, 1954, pp. 1, 12; Downing, et al., “Measurement of Controlled Focused Sonic Booms from Maneuvering Aircraft,’ JASA, vol. 104, no. 1 (July 1998), pp. 1 1 2-1 21.
[464] Judy A. Rumerman, NASA Historical Data Book, vol. 6, NASA Space Applications, Aeronautics . . . and Resources, 1979-1988, NASA SP-2000-4012, 2000, pp. 177-178.
[465] Conway, High-Speed Flight, pp. 201-215; Paul Proctor, “Conference [sponsored by Battelle] Cites Potential Demand for Mach 5 Transports by Year 2000,’ Aviation Week, Nov. 10, 1986, pp. 42-46.
[466] Rumerman, NASA Historical Data Book, vol. 6, p. 178.
[467] Conway, High-Speed Dreams, pp. 21 8-228; Chambers, Innovations in Flight, p. 50.
[468] Maglieri, Victor E. Sothcroft, and John Hicks, "Influence of Vehicle Configurations and Flight Profile on X-30 Sonic Booms," AIAA Paper 90-5224, Oct. 29, 1990; Maglieri, "A Brief Review of the National Aero-Space Plane Sonic Booms Final Report," USAF Aeronautical Systems Center TR-94-9344, Dec. 1992.
[469] Darden, et al., Status of Sonic Boom Methodology and Understanding; Proceedings. . . Langley Research Center. . . Jan. 19-20, 1988, NASA CP-3027, June 1989. Fig. 6 is copied from p. 6.
[470] Boeing Commercial Airplanes, "High-Speed Civil Transport Study; Final Report,’ NASA CR-4234, Sept. 1989; Douglas Aircraft Company, "1989 High-Speed Civil Transport Studies,’ NASA CR-4375, May 1991 (published late with an extension). For a summary of Boeing’s early design process, see George T. Haglund, "HSCT Designs for Reduced Sonic Boom,’ AIAA Paper 91-3103, Sept. 1991.
[471] Allen H. Whitehead, ed., First Annual High-Speed Research Workshop; Proceedings. . . Williamsburg, VA, May 14-16, 1991, NASA CP-10087, Apr. 1992, pt. 1, pp. 5-22, 202.
[472] Ibid., pp. 272 and 275 quoted.
[473] Ibid., Table of Contents, pp. iv-v.
[474] Darden, ed., High-Speed Research: Sonic Boom; Proceeding. . . Langley Research Center.
. . Feb. 25-27, 1992, NASA CR-3172, Oct. 1992, vols. 1, 2.
[475] Thomas A. Edwards, ed., High-Speed Research: Sonic Boom; Proceedings. . . Ames Research Center. . . May 12-14, 1993, NASA CP-10132, vol. 1.
[476] David A. McCurdy, ed., High-Speed Research: 1994 Sonic Boom Workshop, Atmospheric Propagation and Acceptability Studies; Proceedings. . . Hampton, VA, June 1 -3, 1994, NASA CP-3209; High-Speed Research: 1994 Sonic Boom Workshop: Configuration, Design, Analysis, and Testing. . . Hampton, VA, June 1-3, 1994, NASA CP-209669, Dec. 1999.
[477] Daniel G. Baize, 1995 NASA High-Speed Research Program Sonic Boom Workshop: Proceedings . . . Langley Research Center. . . Sept. 12-13, 1995, NASA CP-3335, vol. 1, July 1966.
[478] For help in deciding which of the many research projects to cover, the author referred to Darden, "Progress in Sonic-Boom Understanding: Lessons Learned and Next Steps,’ 1994 Sonic Boom Workshop, pp. 269-292, for guidance.
[479] Thomas A. Edwards, et al., "Sonic Boom Prediction and Minimization using Computational Fluid Dynamics,’ First Annual High Speed Workshop [1991], pt. 2, p. 732.
[480] Darden, et al., "Design and Analysis of Low Boom Concepts at Langley Research Center,’ ibid., pp. 675-699); Peter G. Coen, "Development of a Computer Technique for Prediction of Transport Aircraft Flight Profile Sonic Boom Signatures,’ NASA CR-1 881 17, Mar. 1991 (M. S. Thesis, George Washington University).
[481] Percy J. Bobbit, "Application of Computational Fluid Dynamics and Laminar Flow Technology for Improved Performance and Sonic Boom Reduction,’ 1992 Sonic Boom Workshop, vol. 2, pp. 1 37-144.
[482] Mack and Darden, "Limitations on Wind-Tunnel Pressure Signature Extrapolation,’ 1992 Sonic Boom Workshop, vol. 2, pp. 201-220.
[483] Susan E. Cliff, et al., "Design and Computational/Experimental Analysis of Low Sonic Boom Configurations,’ 1994 Sonic Boom Workshop, vol. 2, pp. 33-57. For a review of CFD work
at Ames from 1989-1994, see Samsun Cheung, "Supersonic Civil Airplane Study and Design: Performance and Sonic Boom,’ NASA CR-197745, Jan. 1995.
[484] Christopher A. Lee, "Design and Testing of Low Sonic Boom Configurations and an Oblique All-Wing Supersonic Transport,’ NASA CR-197744, Feb. 1995.
[485] Maglieri, et al., "Feasibility Study on Conducting Overflight Measurements of Shaped Sonic Boom Signatures Using the Firebee BQM-34E RPV,’ NASA CR-1 89715, Feb. 1993. Fig. 7 is copied from p. 52, with waveforms based on a speed of Mach 1.3 at 20,000 feet rather than the 9,000 feet of planned flight tests.
[486] David Lux, et al., "Low-Boom SR-71 Modified Signature Demonstration Program,’ 1994 Sonic Boom Workshop: Configuration, Design, Analysis and Testing, pp. 237-248.
[487] Edward H. Haering, et al., "Measurement of the Basic SR-71 Airplane Near-Field Signature,’ 1994 Sonic Boom Workshop: Configuration, Design, Analysis, and Testing, pp. 171-197; John M. Morgenstern, et al., "SR-71A Reduced Sonic Boom Modification Design,’ ibid., pp. 199-217; Kamran Fouladi, "CFD Predictions of Sonic-Boom Characteristics for Unmodified and Modified SR – 71 Configurations,’ ibid., pp. 219-235. Fig. 8 is copied from p. 222.
[488] Catherine M. Bahm and Edward A. Haering, "Ground-Recorded Sonic Boom Signatures of F-1 8 Aircraft in Formation Flight," 1995 Sonic Boom Workshop, vol. 1, pp. 220-243.
[489] J. Micah Downing, "Lateral Spread of Sonic Boom Measurements from US Air Force Boomfile Flight Tests," 1992 Sonic Boom Workshop, vol. 1, pp. 1 17-1 36; Maglieri, et al., "A Summary of XB-70 Sonic Boom Signature Data, Final Report," NASA CR-1 89630, Apr. 1992.
[490] William L. Willshire and David W. DeVilbiss, "Preliminary Results from the White Sands Missile Range Sonic Boom Propagation Experiment,’ 1992 Sonic Boom Workshop, vol. 1, pp. 1 37-144.
[491] Gerry L. McAnich, "Atmospheric Effects on Sonic Boom—A Program Review,’ First Annual HSR Workshop, pp. 1 201-1 207; Allan D. Pierce and Victor W. Sparrow, "Relaxation and Turbulence Effects on Sonic Boom Signatures,’ ibid., pp. 1 21 1-1 234; Kenneth J. Plotkin, "The Effect of Turbulence and Molecular Relaxation on Sonic Boom Signatures,’ ibid., pp. 1 241-1 261; Lixin Yao, et al., "Statistical and Numerical Study of the Relation Between Weather and Sonic Boom,’ ibid., pp. 1 263-1 284.
[492] Leonard M. Weinstein, "An Optical Technique for Examining Aircraft Shock Wave Structures in Flight,’ 1994 Sonic Boom Workshop, Atmospheric Propagation, pp. 1-1 8. The following year Weinstein demonstrated improved results using a digital camera: "An Electronic Schlieren Camera for Aircraft Shock Wave Visualization,’ 1995 Sonic Boom Workshop, vol. 1, pp. 244-258.
[493] Kevin P. Shepherd, "Overview of NASA Human Response to Sonic Boom Program,’ First Annual HSR Workshop, pt. 3, pp. 1 287-1 291; Shepherd, et al., "Sonic Boom Acceptability Studies,’ ibid., pp. 1295-1311.
[494] David A. McCurdy, et al., "An In-Home Study of Subjective Response to Simulated Sonic Booms,’ 1994 Sonic Boom Workshop: Atmospheric Propagation and Acceptability, pp. 193207; McCurdy and Sherilyn A. Brown, "Subjective Response to Simulated Sonic Boom in Homes,’ 1995 Sonic Boom Workshop, pp. 278-297.
[495] James M. Fields, et al., "Residents’ Reactions to Long-Term Sonic Boom Exposure: Preliminary Results,
1994 Sonic Boom Workshop: Atmospheric Propagation and Acceptability, vol. 1, pp. 193-217.
[496] Conway, High-Speed Dreams, p. 253.
[497] Darden, "Progress in Sonic-Boom Understanding: Lessons Learned and Next Steps,’ 1994 Sonic Boom Workshop, Atmospheric Propagation and Acceptability, pp. 269-290.
[498] James M. Fields, "Reactions of Residents to Long-Term Sonic Boom Noise Environments,’ NASA CR-201704, June 1997.
[499] Edward A. Haering, L. J. Ehernberger, and Stephen A. Whitmore, "Preliminary Airborne Experiments for the SR-71 Sonic Boom Propagation Experiment,’ 1995 Sonic Boom Workshop, vol. 1, pp. 176-1 98; Stephen R. Norris, Haering, and James E. Murray, "Ground-Bases Sensors for the SR-71 Sonic Boom Propagation Experiment,’ ibid., pp. 199-21 8; Hugh W. Poling, "Sonic Boom Propagation Codes Validated by Flight Test,’ NASA CR-201634, Oct. 1996.
[500] Conway, High-Speed Dreams, pp. 286-300; James Schultz, "HSR Leaves Legacy of Spinoffs,’ Aerospace America, vol. 37, no. 9 (Sept. 1999), pp. 28-32. The Acoustical Society held its third sonic boom symposium in Norfolk from Oct. 15-16, 1998. Because of HSR distribution limitations, many of the presentations could be oral only, but a few years later, the ASA was able to publish some of them in a special edition of its journal. For a status report as of the end of the HSR, see Kenneth J. Plotkin, "State of the Art of Sonic Boom Modeling,’ JASA, vol. 111, No. 1, pt. 3 (Jan. 2002), pp. 530-536.
1 80. The study, originally completed in 1997, was in the process of being formally published by NASA as "A Compilation and Review of Supersonic Business Jet Studies from 1960-1995′ as this history was being written.
[502] Richard Seebass, "History and Economics of, and Prospects for, Commercial Supersonic Transport,’ (Paper 1) and "Sonic Boom Minimization’ (Paper 6), NATO Research and Technology Organization, Fluid Dynamics Research on Supersonic Aircraft [proceedings. . . Rhode Saint – Genese, Belgium, May 25-29, 1998], RTO-EN-4, Nov. 1998 (pp. 1-6 of Paper 1 and abstract of Paper 2 quoted). Sadly, Seebass would not live to see a low boom airplane configuration finally demonstrated in 2003.
1 82. Robert Wall, "Darpa Envisions New Supersonic Designs,’ Aviation Week, Aug. 28, 2000, p. 47; and "Novel Technologies in Quest for Quiet Flight,’ Aviation Week, Jan. 8, 2001, p. 61.
1 83. Joseph W. Pawlowski, David H. Graham, Charles H. Boccadoro (NGC), Peter G. Coen (LaRC), and Domenic J. Maglieri (Eagle Aero.), "Origins and Overview of the Shaped Sonic Boom Demonstration Program,’ AIAA Paper 2005-5, presented at the 43rd Aerospace Sciences Meeting, Reno, NV, Jan. 10-13, 2005, pp. 3-7 (also published with briefing slides by the Air Force Research Laboratory as AFRL-VAWP-2005-300, Jan. 2005).
1 84. Ibid., p. 8; Edward D. Flinn, "Lowering the Boom on Supersonic Flight Noise,’ Aerospace America, vol. 40, No. 2 (Feb. 2002), pp. 20-21; Wyle Laboratories, "Wyle Engineers Play Significant Role in Northrop Grumman Sonic Boom Test Program,’ News Release 09-1 1, Sept. 1 1, 2003.
1 85. Keith H. Meredith, et al., "Computational Fluid Dynamics Comparison and Flight Test Measurement of F-5E Off-Body Pressures,’ AIAA Paper 2005-6, presented at 43rd Aerospace Sciences Meeting, Reno, NV, Jan. 10-13, 2005.
1 86. Graham Warwick, "F-5E Shapes Up to Change Sonic Boom,’ Flight international, Aug.
5, 2003, p. 30; T. A. Heppenheimer, "The Boom Stops Here,’ Air and Space Magazine, Nov. 2005, http://www. airspacemag. com/fight-today/boom. html.
1 87. Pawlowski, et al., "Origins and Overview of the SSBD,’ pp. 10-1 2; Peter G. Coen and Roy Martin, "Fixing the Sound Barrier: The DARPA/NASA/Northrop-Grumman Shaped Sonic Boom Flight Demonstration,’ Briefing at EAA AirVenture, Oshkosh, WI, July 2004. (Fig. 9 is taken from slide 21.)
1 88. Pawlowski, et al., "Origins and Overview of the SSBD," pp. 11-12; NASA Press Release 03-50, "NASA Opens New Chapter in Supersonic Flight," Sept. 4, 2003; Gary Creech, "NASA, Northrop Study Sonic Boom Reduction," Dryden X-Press, vol. 46, issue 2 (Mar. 2004). p. 1 .
1 89. Pawlowski, et al., "Origins and Overview of the SSBD," pp 1 2-1 3; David H. Graham, et al., "Wind Tunnel Validation of Shaped Sonic Boom Demonstration Aircraft Design," AIAA Paper 2005-7; Haering, et al., "Airborne Shaped Sonic Boom Demonstration Pressure Measurements with Computational Fluid Dynamics Comparisons," AIAA Paper 2005-9; Plotkin, et al., "Ground Data Collection of Shaped Sonic Boom Experiment Aircraft Pressure Signatures," AIAA Paper 2005-10; John M. Morgenstern, et al., "F-5 Shaped Sonic Boom Demonstrator’s Persistence of Boom Shaping Reduction through Turbulence," AIAA 2005-1 2; all papers presented at 43rd Aerospace Sciences Meeting, Reno, NV, Jan. 10-13, 2005.
[511] James R. Asker, "FAA Seeks Information on Sonic Boom Research,’ Aviation Week, June 2, 2003, p. 21; David Bond, "The Time is Right,’ Aviation Week, Oct. 20, 2003, pp. 57-58.
[512] Peter G. Coen, "Supersonic Vehicles Technology: Sonic Boom Technology Development and Demonstration’ and Preston A. Henne, "A Gulfstream Perspective on the DARPA QSP Program and Future Supersonic Initiatives,’ Briefing Slides, FAA Civil Supersonic Aircraft Workshop, Washington, DC, Nov.
1 3, 2003; Aimee Cunningham, "Sonic Booms and Human Ears: How Much Can the Public Tolerate,’ Popular Science, July 30, 2004, http://www. popsci. com/military-aviation-space/article/2004-07/ sonicbcoms-and-human-ears.
[513] Robert J. Mack, "A Supersonic Business Jet Concept Designed for Low Sonic Boom,’ NASA TM-2003-21 2435, Oct. 2003.
[514] For examples, see Graham Warwick, "Quiet Progress: Aircraft Designers Believe They Can Take the Loud Boom out of Supersonic Travel,’ Flight International, Oct. 20, 2004, pp. 32-33; Edward H. Phillips, "Boom Could Doom: Debate over Hybrid SSBJ Versus Pure Supersonic Is Heating Up,’ Aviation Week, June 1 3, 2005, pp. 84-85; Francis Fiorino, "Lowering the Boom,’ Aviation Week, Nov. 7, 2005, p. 72; "Supersonic Private Jets in Development,’ Business Travel News Online, Oct. 23, 2006; John Wiley, "The Super-Slow Emergence of Supersonic,’ Business and Commercial Aviation, Sept. 1, 2007, pp. 48-50; Edward H. Phillips, "Shock Wave: Flying Faster than Sound Is the Holy Grail of Business Aviation,’ Aviation Week, Oct. 8, 2007, pp. 50-51; Mark Huber, "Mach 1 for Millionaires,’ Air and Space Magazine, Mar.-Apr. 2006, http://www. airspacemag. com/fiight-tcday/millionaire. htmi
[515] Graham Warwick, "NASA Narrows R&D Agenda," Flight International, Feb. 1 5, 2006, p. 28; Ellen H. Thompson, et al., "NASA Funds Studies for Quieter Supersonic Boom," NASA News Release 05-176, July 8, 2005.
[516] David Collogan, "Manufacturers, NASA working on Bizjet Sonic Boom Project," The Weekly of Business Aviation, July 1 8, 2005, p. 21.
[517] Michael A. Dornheim, "Will Low Boom Fly? NASA Cutbacks Delay Flight Test of Shaped Demonstrator. . . ," Aviation Week, Nov. 7, 2005, pp. 68-69.
[518] U. S. Patent No. 6,698,684, "Supersonic Aircraft with Spike for Controlling and Reducing Sonic Boom," Mar. 2, 2004, http://www. patentstorm. us/patents/6698684/description. html.
[519] Jay Levine, "Lowering the Boom," July 29, 2005, http://www. nasa. gov/centers/dryden/ news/X-Press/stories/2005/072905.
[520] Donald C. Howe, et al., "Development of the Gulfstream Quiet Spike for Sonic Boom Minimization,’ AIAA Paper 2008-1 24, presented at 46th Aerospace Sciences Meeting, Reno, NV, Jan. 7-Ю, 2008; Natalie D. Spivey, et al., "Quiet Spike Build-up Ground Vibration Testing Approach,’ NASA TN-2007-214625, Nov. 2007.
[521] James W. Smolka, et al., "Flight Testing of the Gulfstream Quiet Spike on a NASA F-1 5B,’ paper presented to the Society of Experimental Test Pilots, Anaheim, CA, Sept. 27, 2007, 1 -24; Stephen B. Cumming, et al., "Aerodynamic Effects of a 24-foot Multi-segmented Telescoping Nose Boom on an F-15B Airplane,’ NASA TM-2008-214634, Apr. 2008.
[522] Smolka, et al., "Flight Testing of the Gulfstream Quiet Spike,’ pp. 28-38; Haering, et al., "Preliminary Results from the Quiet Spike Flight Test,’ briefing presented at the Fundamental Aeronautics Program meeting, New Orleans, Oct. 30-Nov. 1, 2007.
[523] "Aeronautics/Propulsion Laureate,’ Aviation Week, Mar. 17, 2008, p. 40; "Obituary: Gerard Schkolnik,’ ibid., Apr. 21, 2008, p. 22.
[524] Michael Braukus/Doc Mirleson, "NASA Restructures Aeronautics Research,’ NASA News Release 06-008, Jan. 1 2, 2006; Lisa Porter, "Reshaping NASA’s Aeronautics Program, Briefing,’ Jan. 1 2,
2006, http://www. nasa. gov/home/hqnews/2006/jan/ HQ_06008_ARMD_ Restructuring. html.
[525] Peter Coen, Mary Jo Long-Davis, and Louis Povinelli, "Fundamental Aeronautics Program Supersonics Project, Reference Document,’ May 26, 2006, pp. 36-37, http://www. aeronautics. nasa. gov/fap/documents. html (quote from p. 36).
[526] Jefferson Morris, "Quiet, Please: With More Emphasis on Partnering, NASA Continues Pursuit of Quieter Aircraft,’ Aviation Week, June 25, 2007, p. 57; Lisa J. Porter, "NASA’s Aeronautics Program,’ Fundamental Aeronautics Annual Meeting, New Orleans, Oct. 30, 2007, slide on "Supersonics System Level Metrics,’ http://www. aeronautics. nasa. gov/fap/PowerPoints/ARMD&FA_Intro. pdf;
Beth Hickey, "NASA Awards Future Aircraft Research Contracts,’ Contract Release C08-060, Oct. 6, 2008; Graham Warwick, "Forward Pitch,’ Aviation Week, Oct. 20, 2008, p. 22.
[527] Hans Greimel, "Japan to Talk with NASA on Supersonic Jet,’ Washington Post, May 8, 2006, http://www. washingtonpost. com/wp-dyn/content/article/2006/05/09/AR2226050800267; Beth Dickey, "NASA and JAXA to Conduct Joint Research on Sonic Boom Modeling,’ NASA News Release 09-1 17, May 8, 2008.
[528] "X-54A Designation Issued as Placeholder for Future Boom Research Aircraft,’ Aerospace Daily, July 21, 2008, p. 1.
[529] Haering, Smolka, James E. Murray, and Plotkin, "Flight Demonstration of Low Overpressure N – Wave Sonic Booms and Evanescent Waves,’ Innovations in Non-Linear Acoustics: 17th International Symposium on Nonlinear Acoustics, International Sonic Boom Forum, State College, PA, July 21 -22, 2005, American Institute of Physics Conference Proceedings, vol. 838 (May 2006), pp. 647-650.
[530] Jacob Klos and R. D. Bruel, "Vibro-Acoustical Response of Buildings Due to Sonic Boom Exposure: June 2006 Field Test,’ NASA TM-2007-214900, Sept. 2007.
[531] Creech, "Sonic Boom Tests Scheduled,’ Dryden News Release 07-38, July 5, 2007; Guy Norris, "Sonic Spike,’ Aviation Week, Oct. 8, 2007, p. 52; Haering, et al., "Initial Results from the Variable Intensity Sonic Boom Propagation Database,’ AIAA Paper 2008-3034, presented at the
14th AIAA/CEAS Aeroacoustics Conference, Vancouver, BC, Canada, May 5-7, 2008; Jacob Klos, "Vibro-Acoustic Response of Buildings Due to Sonic Boom Exposure: July 2007 Field Test,’ NASA TM-2008-215349, Sept. 2008.
[532] Brenda M. Sullivan, "Research on Subjective Response to Simulated Sonic Booms at NASA Langley Research Center,’ paper presented at International Sonic Boom Forum, State College, PA, July 21-22, 2005.
21 2. Brenda M. Sullivan, "Design of an Indoor Sonic Boom Simulator at NASA Langley Research Center,’ July 28, 2008, paper presented at Noise-Con 2008, Baltimore, July 12-14, 2008, and "Research at NASA on Human Response to Sonic Booms,’ Nov. 17, 2008, at 5th International Conference on Flow Dynamics, Sendai, Japan, Nov. 17-20, 2008; Coen, Lou Povinelli, and Kaz Civinskas, "Supersonics Project Overview,’ Fundamental Aeronautics Annual Meeting, Atlanta, Oct. 7, 2008, http://www. aeronautics. nasa. gov/fap/ PowerPoints/SUP_ATL_Overview. pdf.
21 3. "FAA Updates Policy on SST Noise Certification,’ The Weekly of Business Aviation, Oct. 27, 2008, p. 195.
214. "Supersonics Project Reference Document,’ p. 43. The acronym "LaNCETS’ was devised by Haering: Discussion with Benson, at the Dryden Flight Research Center, Dec. 1 2, 2008.
[536] Dryden Flight Research Center, "F-15B #837," http://www. nasa. gov/centers/dryden/ aircraft/F-I5Br837/iridex. html, accessed Feb. 1 1, 2009.
21 6. Larry Cliatt, et al., "Overview of the LaNCETS Flight Experiment and CFD Analysis," Briefing, Fundamental Aeronautics Annual Meeting, Atlanta, Oct. 2, 2008.
[538] J. H. Casper, et al., "Assessment of Near-Field Sonic Boom Simulation Tools," AIAA Paper 2008-6592 (p. 8 quoted) and Richard L. Campbell, et al., "Efficient Unstructured Grid Adaptation Methods for Sonic Boom Prediction," AIAA Paper 2008-7327, both presented at 26th Applied Aerodynamics Conference, Honolulu, Aug. 18-2 I, 2008.
21 8. Norris, "Sonic Solutions: NASA Uses Unique F-1 5B to Complete Design Tools for Quiet Supersonic Aircraft,’ Aviation Week, Jan. 5, 2009, p. 53; Creech and Beth Dickey, "Lancets Flights Probe Supersonic Shockwaves,’ Dryden News Release 09-04, Jan. 22, 2009; Tim Moes, "Sonic Boom Research at NASA Dryden: Objectives and Flight Results of the Lift and Nozzle Change Effects on Tail Shock (LaNCETS) Project,’ Partial Briefing Slides, International Test & Evaluation Association, Antelope Valley Chapter, Feb. 24, 2009; E-mail, Tim Moes to Benson, "Re: More Details on LaNCETS,’ Mar. 11, 2009.
21 9. For an early analysis, see Trong T. Bui, "CFD Analysis of Nozzle Jet Plume Effects on Sonic Boom Signature,’ AIAA Paper 2009-1 054, presented at 47th Aerospace Sciences Meeting, Orlando, FL, Jan. 5-8, 2009.
[541] Graham Warwick, et al., "Open Season," Aviation Week, Mar. 2, 2009, pp. 20-21.
[542] Warwick, "Beyond the N-Wave: Modifying NASA’s Arrow-Wing F-16XL Could Help Pave the Way for Low-Boom Supersonic Transports," Aviation Week, Mar. 23, 2009, p. 52.
[543] E-mail, Coen, Langley Research Center, to Benson, Apr. 10, 2009.
[544] Richard E. Young, Martha A. Smith, and Charles K. Sobeck, "Galileo Probe: In Situ Observations of Jupiter’s Atmosphere,’ Science, no. 272 (May 10, 1996), pp. 837-838.
[545] Mark Wolverton, "The Airplane That Flew Into Space,’ American Heritage of Invention and Technology, (summer 2001), pp. 1 2-20.
[546] J. Sorensen, "Titanium Matrix Composites—NASP Materials and Structures Augmentation Program,’ AIAA Paper 90-5207 (1990); Stanley W. Kandebo, "Boeing 777 to Incorporate New Alloy Developed for NASP,’ Aviation Week, May 3, 1993, p. 36; "NASP Materials and Structures Program, Titanium Matrix Composites,’ McDonnell-Douglas, Dec. 31, 1991, DTIC ADB-192559, Defense Technical Information Center.
[547] Walter Dornberger, V-2 (New York: The Viking Press, 1958 ed.), relates its history from the point of view of the German military commander of V-2 development and its principal research facility.
[548] Michael J. Neufeld, The Rocket and the Reich: Peenemunde and the Coming of the Ballistic Missile Era (Cambridge: Harvard University Press, 1995), pp. 250-251.
[549] Ronald Smelt, "A Critical Review of German Research on High-Speed Airflow,’ Journal of the Royal Aeronautical Society, vol. 50, No. 432 (Dec. 1946), pp. 899-934; Theodore von Karman, "Where We Stand: First Report to General of the Army H. H. Arnold on Long Range Research Problems of the AIR FORCES with a Review of German Plans and Developments,’ Aug. 22, 1945, vol. II-1, Copy No. 1 3, including Hsue-shen Tsien, "Reports on the Recent Aeronautical Developments
of Several Selected Fields in Germany and Switzerland,’ July 1945; Hsue-shen Tsien, "High Speed Aerodynamics,’ Dec. 1945; and F. L. Wattendorf, "Reports on Selected Topics of German and Swiss Aeronautical Developments,’ June 1 945; Peter P. Wegener, The Peenemunde Wind Tunnels: A Memoir (New Haven: Yale University Press, 1996), pp. 22-24, 70.
[550] William B. Anspacher, Betty Gay, Donald Marlowe, Paul Morgan, and Samuel Raff, The Legacy of the White Oak Laboratory (Dahlgren, VA: Naval Surface Warfare Center, 2000), pp. 209-210; Donald D. Baals and William R. Corliss, Wind Tunnels of NASA, SP-440 (Washington, DC: NASA, 1981), pp. 51-52; James R. Hansen, Engineer in Charge: A History of the Langley Aeronautical Laboratory, 1917-1958, SP-4305 (Washington, DC: NASA, 1987), p. 467.
[551] Quoted in Hansen, Engineer in Charge, pp. 344-345.
[552] John V. Becker, "Results of Recent Hypersonic and Unsteady Flow Research at the Langley Aeronautical Laboratory,’ Journal of Applied Physics, vol. 21 (July 1950), pp. 619-628; Patrick J. Johnston and Wallace C. Sawyer, "An Historical Perspective on Hypersonic Aerodynamic Research at the Langley Research Center,’ AIAA Paper 88-0230 (1988). For examples of its research, see Charles H. McLel – lan, Thomas W. Williams, and Mitchel H. Bertram, "Investigation of a Two-Step Nozzle in the Langley
1 1-inch Hypersonic Tunnel,’ NACA TN-2171 (1950); Charles H. McLellan and Thomas W. Williams, "Liquefaction of Air in the Langley 1 1-inch Hypersonic Tunnel,’ NACA TN-3302 (1954).
[553] John V. Becker, "The X-15 Project: Part I—Origins and Research Background,’ Astronautics & Aeronautics, vol. 2, No. 2 (Feb. 1964), pp. 52-61; Charles H. McLellan, "A Method for Increasing the Effectiveness of Stabilizing Surfaces at High Supersonic Mach Numbers,’ NACA RM-L54F21 (1954); Baals and Corliss, Wind Tunnels of NASA, pp. 56-57, 94-95; William T. Schaefer, Jr., "Characteristics of Major Active Wind Tunnels at the Langley Research Center,’ NASA TM-X-1 130 (1965), pp. 1 2, 27.
1 1 . Jacob Neufeld, The Development of Ballistic Missiles in the United States Air Force, 19451960 (Washington, DC: USAF, 1990), p. 293; Col. Edward N. Hall, USAF, "Air Force Missile Experience,’ in Lt. Col. Kenneth F. Gantz, ed., The United States Air Force Report on the Ballistic Missile: Its Technology, Logistics, and Strategy (Garden City, NY: Doubleday & Co., Inc., 1958), pp. 47-59; Donald MacKenzie, Inventing Accuracy (Cambridge: MIT Press, 1990).
1 2. P. H. Rose and W. I. Stark, "Stagnation Point Heat-Transfer Measurements in Dissociated Air,’ Journal of the Aeronautical Sciences, vol. 25, no. 2 (Feb. 1958), pp. 86-97.
1 3. John L. Chapman, Atlas: the Story of a Missile (New York: Harper & Brothers, 1 960), pp. 28-34, 74; Neufeld, Development of Ballistic Missiles, pp. 78, 44-50, 68-77; G. Harry Stine, ICBM: The Making of the Weapon that Changed the World (New York: Orion Books, 1 996), pp. 140-146, 162-174, 186-188.
[557] Bruno Augenstein, "Rand and North American Aviation’s Aerophysics Laboratory: An Early Interaction in Missiles and Space,’ International Astronautical Federation, Paper IAA-98-IAA.2.2.06 (1998); Neufeld, Development of Ballistic Missiles, pp. 259, 102-106, 1 17; Robert L. Perry, "The Atlas, Thor, Titan, and Minuteman,’ in Eugene M. Emme, ed., The History of Rocket Technology: Essays on Research, Development, and Utility (Detroit: Wayne State University Press, 1964), pp. 142-161.
[558] H. Julian Allen and AJ. Eggers, Jr., "A Study of the Motion and Aerodynamic Heating of Ballistic Missiles Entering the Earth’s Atmosphere at High Supersonic Speeds,’ NACA TR-1 381 (1 953); H. Julian Allen, "The Aerodynamic Heating of Atmospheric Entry Vehicles,’ in J. Gordon Hall, ed., Fundamental Phenomena in Hypersonic Flow: Proceedings of the International Symposium Sponsored by Cornell Aeronautical Laboratory (Ithaca, NY: Cornell University Press, 1966), pp. 6-10; Edwin P. Hartman, Adventures in Research: A History of the Ames Research Center, 1940-1965, NASA SP-4302 (Washington, DC: NASA, 1970), pp. 215-218.
[559] E. L. Resler, Shao-Chi Lin, and Arthur Kantrowitz, "The Production of High Temperature Gases in Shock Tubes,’ Journal of Applied Physics, vol. 23 (Dec. 1952), p. 1 397.
[560] Frank Kreith, Principles of Heat Transfer (Scranton, PA: International Textbook Co., 1965), pp. 538-545; George W. Sutton, "The Initial Development of Ablation Heat Protection: an Historical Perspective,’ Journal of Spacecraft and Rockets, vol. 19 (1982), pp. 3-1 1 .
1 8. "Re-Entry Research: The Lockheed X-17," Flight (Feb. 6, 1959), p. 181.
[562] James M. Grimwood and Francis Strowd, History of the Jupiter Missile System (Huntsville, AL: U. S. Army Ordnance Missile Command, July 27, 1962), pp. 18-20; Time (Nov. 18, 1957, pp. 19-20, and Dec. 8, 1958, p. 15); Joel W. Powell, "Thor-Able and Atlas Able," Journal of the British Interplanetary Society, vol. 37, No. 5 (May 1984), pp. 219-225; General Electric, "Thermal Flight Test Summary Report for Mark 3 Mod 1 Re-Entry Vehicles" (1 960), Defense Technical Information Center [DTIC] Report AD-362539; Convair, "Flight Test Evaluation Report, Missile 7D" (1959), DTIC AD-832686.
[563] Martin Marietta, "SV-5 PRIME Final Flight Test Summary," Report ER 14465 (1967).
[564] . Marcelle Size Knaack, Post-World War II Fighters, vol. 1 of Encyclopedia of U. S. Air Force Aircraft and Missile Systems (Washington, DC: Office of Air Force History, 1 978), p. 329; Richard A. DeMeis, "The Trisonic Titanium Republic,’ Air Enthusiast, vol. 7 (1978), pp. 198-21 3.
[565] Lee L. Peterson, "Evaluation Report on X-7A," AFMDC [Holloman AFB], ADJ 57-8184 (1957); and William A. Ritchie, "Evaluation Report on X-7A (System 601 B)," AFMDC DAS-58-8129 (1959).
[566] Robert S. Houston, Richard P. Hallion, and Ronald G. Boston, "Transiting from Air to Space: The North American X-15," and John V. Becker, "The Development of Winged Reentry Vehicles: An Essay from the NACA-NASA Perspective, 1952-1963," in Richard P. Hallion, ed., The Hypersonic Revolution: Eight Case Studies in the History of Hypersonic Technology, vol. 1: From Max Valier to Project PRIME,
1924-1967 (Wright-Patterson AFB: Aeronautical Systems Division, 1987), pp. I-xii, No. 1, 383-386.
[567] Harry Hansen, Engineer in Charge, NASA SP-4305, p. 428; Hansen, ed., The World Almanac and Book of Facts for 1956 (New York: New York World-Telegram Corp., 1956), p. 757.
[568] Dennis Jenkins, X-15: Extending the Frontiers of Flight, NASA SP-2007-562 (Washington, DC: NASA, 2007), pp. 336-337.
[569] U. S. Air Force Systems Command, History of the Arnold Engineering Development Center (Arnold Air Force Station, TN: AEDC, n. d.); Julius Lukasiewicz, Experimental Methods of Hypersonics (New York: Marcel Dekker, Inc., 1973), p. 247.
[570] Becker, "Development of Winged Reentry Vehicles,’ in Hallion, Hypersonic Revolution, vol. 1, p. 386.
[571] Becker, "The X-15 Project,’ pp. 52-61. Technical characteristics of Inconel X are from "Inconel X-750 Technical Data’ (Sylmar, CA: High Temp Metals, Inc., 2009).
[572] Richard P. Hallion, On the Frontier: Flight Research at Dryden, 1946-1982, SP-4303 (Washington, DC: NASA, 1984), pp. 70-71.
[573] McLellan, "A Method for Increasing the Effectiveness of Stabilizing Surfaces,’ NACA RM – L54F21 (1954).
[574] . John V. Becker, Norris F. Dow, Maxime A. Faget, Thomas A. Toll, and J. B. Whitten, "Research Airplane Study," NACA Langley (April 1954).
[575] Johnny G. Armstrong, "Flight Planning and Conduct of the X-15A-2 Envelope Expansion Program," AFFTC TD-69-4 (1969).
[576] William H. Dana, "The X-15 Airplane-Lessons Learned,’ AIAA Paper 93-0309 (1 993); Joseph Weil, "Review of the X-15 Program,’ NASA TN-D-1278 (1962).
[577] Perry V. Row and Jack Fischel, "X-1 5 Flight Test Experience,’ Astronautics and Aerospace Engineering, vol. 1 (June 1963), pp. 25-32.
[578] Quotes from "Research Airplane Committee Report on Conference on the Progress of the X-15 Project,’ NACA Langley Aeronautical Laboratory, 1956, p. 84; James I. Kilgore, "The Planes that Never Leave the Ground,’ American Heritage of Invention and Technology (winter 1989), pp. 60-62; John P. Smith, Lawrence J. Schilling, and Charles A. Wagner, "Simulation at Dryden Flight Research Facility from 1957 to 1982,’ NASA TM-101695 (1989), p. 4; Milton O. Thompson, At the Edge of Space: The X-15 Flight Program (Washington, DC: Smithsonian Institution Press, 1992), pp. 70-71.
[579] NASA FRC, "Experience with the X-15 Adaptive Flight Control System,’ NASA TN-D-6208 (1971); Perry V. Row and Jack Fischel, "Operational Flight-test Experience with the X-15 Airplane,’ AIAA Paper 63-075 (1963).
[580] Wendell H. Stillwell, X-15 Research Results, NASA SP-60 (Washington, DC: NASA, 1965), pp. 37-38; Robert G. Hoey and Richard E. Day, "Mission Planning and Operational Procedures for the X-15 Airplane,’ NASA TN-D-1 158 (1962), NTRS Document ID 19710070140.
[581] C. C. Clark and C. H. Woodling, "Centrifuge Simulation of the X-15 Research Aircraft,’ NADC MA-591 6 (1959); Jenkins, X-15, p. 279; NASA, "Research Airplane Committee Report on Conference on the Progress of the X-15 Project,’ (1958), pp. 107-1 16.
[582] For the Clark suit’s development, see A. Scott Crossfield with Clay Blair, Jr., Always Another Dawn: The Story of a Rocket Test Pilot (Cleveland: The World Publishing Co., 1960), pp.
253-261; Paul Crickmore, Lockheed SR-71 Blackbird (London: Osprey Publishing Ltd., 1986), pp. 100-102; T. A. Heppenheimer, History of the Space Shuttle, vol. 2, Development of the Shuttle, 1972-81 (Washington, DC: Smithsonian Institution Press, 2002), pp. 274-277; Jenkins, X-15, pp. 1 31-146; Loyd S. Swenson, James M. Grimwood, and Charles Alexander, This New Ocean: A History of Project Mercury NASA SP-4201 (Washington, DC: NASA, 1998), pp. 225-231.
[583] Time, Oct. 27, 1961, p. 89.
41 . Dana, "The X-15 Airplane-Lessons Learned," AIAA Paper 93-0309 (1993); Thompson, At the Edge of Space, pp. 200-202; Lawrence W. Taylor and George B. Merrick, "X-1 5 Airplane Stability Augmentation Systems," NASA TN-D-1 157 (1962); Robert A. Tremant, "Operational Experience and Characteristics of the X-15 Flight Control System," NASA TN-D-1402 (Dec. 1962), Donald R. Bellman, et al., Investigation of the Crash of the X-J5-3 Aircraft on November 15, 1967 (Edwards: NASA Flight Research Center, Jan. 1968), pp. 8-15.
[585] Kenneth E. Hodge, et al., Proceedings of the X-15 First Flight 30th Anniversary Celebration, CP 3 105 (Edwards: NASA, June 8, 1989); Hallion, On the Frontier, pp. 170-172; Donald P. Hearth and Albert E. Preyss, "Hypersonic Technology: Approach to an Expanded Program," Astronautics and Aeronautics, (Dec. 1976), pp. 20-37; "NASA to End Hypersonic Effort," Aviation Week and Space Technology (Sept. 26, 1977).
[586] Clarence J. Geiger, "Strangled Infant: The Boeing X-20A Dyna-Soar,’ in Hallion, Hypersonic Revolution, vol. 1, pp. 1 89-201; Capt. Roy F. Houchin, "The Rise and Fall of Dyna-Soar: A History of Air Force Hypersonic R&D, 1944-1963,’ Air Force Institute of Technology (1995), DTIC ADA-303832.
[587] John V. Becker, "The Development of Winged Reentry Vehicles: An Essay from the NACA – NASA Perspective, 1 952-1 963," in Hallion, Hypersonic Revolution, vol. 1, pp. 391-407; Alvin Seiff and H. Julian Allen, "Some Aspects of the Design of Hypersonic Boost-Glide Aircraft," NACA RM-A55E26 (1955); Alfred J. Eggers and Clarence Syvertson, "Aircraft Configurations Developing High Lift-Drag Ratios at High Supersonic Speeds," NACA RM-A55L05 (1956); Hansen, Engineer in Charge, pp. 467-473.
[588] Capt. Roy Houchin, "Hypersonic Technology and Aerospace Doctrine,’ Air Power History, vol. 46, no. 3 (fall 1999), pp. 4-17; Terry L. Sunday and John R. London, "The X-20 Space Plane: Past Innovation, Future Vision,’ in John Becklake, ed., History of Rocketry and Astronautics, vol. 17 (San Diego: American Astronautical Society/Univelt, 1995), pp. 253-284.
[589] Wyndham D. Miles, "The Polaris,’ in Emme, History of Rocket Technology, pp. 162-175.
[590] Curtis Peebles, "The Origin of the U. S. Space Shuttle— 1,’ Spaceflight, vol. 21, no. 11 (Nov. 1979), pp. 435-442.
[591] Geiger, "Strangled Infant,’ in Hallion, Hypersonic Revolution, vol. 1, pp. 31 3, 319-320.
[592] Ibid., pp. 294-310, 313.
[593] Boeing, "Summary of Technical Advances: X-20 Program,’ Report D2-2341 8 (July 1964).
[594] Robert L. Perry, Management of the National Reconnaissance Program, 1960-1965 (Chantilly, VA: NRO, 2001 edition of a Jan. 1969 work), p. 9; Jeffrey Richelson, American Espionage and the Soviet Target (New York: William Morrow, 1987), p. 1 84; F. R. Riddell and J. D. Teare, "The Differences Between Satellite and Ballistic Missile Re-Entry Problems,’ in Morton Alperin and Hollingsworth F. Gregory, eds., Vistas in Aeronautics, vol. 2 (New York: Pergamon Press, 1959), pp. 174-190; Leo Steg, "Materials for Re-Entry Heat Protection of Satellites,’ American Rocket Society Journal (Sept. 1960), pp. 815-822.
[595] Geiger, "Strangled Infant,’ in Hallion, Hypersonic Revolution, vol. 1, pp. 347-370.
[596] Aeronautical Systems Division, Proceedings of 1962 X-20A (Dyna-Soar) Symposium, vol. 3: Structures and Materials (Wright-Patterson AFB, OH: USAF, Mar. 1963), DTIC AD-346192; Howard J. Middendorf, "Materials and Processes for X-20A (Dyna-Soar),” Air Force Systems Command (June 1964), DTIC AD-449685; and William Cowie, "Utilization of Refractory Metals on the X-20A (Dyna-Soar),’ Air Force Systems Command (June 1964), DTIC AD-609169.
[597] ASD, X-20A Proceedings, vol. 3, DTIC AD-346192.
[598] Ibid.; Geiger, "Strangled Infant,’ in Hallion, Hypersonic Revolution, vol. 1, pp. 347-349, 361-370.
[599] Geiger, "Strangled Infant,” in Hallion, Hypersonic Revolution, vol. 1, pp. 344-346; R. L. Schleicher, "Structural Design of the X-15,’ Journal of the Royal Aeronautical Society (Oct. 1963), pp. 61 8-636.
[600] Richard P. Hallion, "ASSET: Pioneer of Lifting Reentry,’ in Hallion, ed., Hypersonic Revolution, vol. 1, pp. 451,461-465, 501-505; USAF Flight Dynamics Laboratory, "Advanced Technology Program: Technical Development Plan for Aerothermodynamic/Elastic Structural Systems Environmental Tests (ASSET)’ (Sept. 1963), pp. 1-5.
[601] Aviation Week (May 24, 1965), p. 62; McDonnell, "ASSET ASV-3 Flight Test Report,’ Report B251 (65FD-234) (Jan. 4, 1965).
[602] McDonnell, "ASSET ASV-4 Flight Test Report,’ Report B707 (65FD-938) June 25, 1965), p. 156; Hallion, "ASSET,” in Hallion, ed., Hypersonic Revolution, vol. 1, p. 519.
[603] USAF Flight Dynamics Laboratory, "ASSET Final Briefing,’ Report 65FD-850 (Oct. 5, 1965).
61 . Paul Cooper and Paul F. Holloway, "The Shuttle Tile Story,’ Astronautics & Aeronautics, vol. 1 9, no. 1 (Jan. 1981), pp. 24-34; Wilson B. Schramm, Ronald P. Banas, and Y. Douglas Izu, "Space Shuttle Tile—The Early Lockheed Years,’ Lockheed Horizons, Issue 13 (1 983), pp. 2-15; T. A. Hep – penheimer, The Space Shuttle Decision, SP-4221 (Washington, DC: NASA, 1999).
[605] Lockheed Missiles and Space Corporation (LMSC), "Space Transport and Recovery System (Space Shuttle),’ LMSC A946332 (Mar. 1969), Shuttle Historical Documents Collection, N. SHHDC-0048, NASA Marshall Space Flight Center; LMSC, "Final Report: Integral Launch and ReEntry Vehicle,’ LMSC A959837 (Dec. 1969), Center for Aerospace Information 70N-31831.
[606] Richard C. Thuss, Harry G. Thibault, and Arnold Hiltz, "The Utilization of Silica Based Surface Insulation for the Space Shuttle Thermal Protection System,’ SAMPE National Technical Conference on Space Shuttle Materials, Huntsville, AL (Oct. 1971), pp. 453-464, Center for Aerospace Information 72A-10764; Schramm, et al., "Space Shuttle Tile’; LJ. Korb, C. A. Morant, R. M. Calland, and C. S. Thatcher, "The Shuttle Orbiter Thermal Protection System,’ and Wilson Schramm, "HRSI and LRSI—
The Early Years,’ both in American Ceramic Society Bulletin, vol. 60 (1981), pp. 1 188-1 195; L. J. Graham, F. E. Sugg, and W. Gonzalez, "Nondestructive Evaluation of Space Shuttle tiles,’ Ceramic Engineering and Science Proceedings, vol. 3 (1982), pp. 680-697; Robert L. Dotts, Donald M.
Curry, and Donald L. Tillian, "Orbiter Thermal Protection System,’ and William C. Schneider and Glenn J. Miller, "The Changing ‘Scales of the Bird’ (Shuttle Tile Structural Integrity),’ in Norman Chaffee, ed., "Space Shuttle Technical Conference,’ NASA Conference Publication 2343 (1983).
[607] Korb, et al., "Shuttle Orbiter TPS’; L. J. Korb and H. M. Clancy, "The Shuttle Thermal Protection System—A Material and Structural Overview,’ SAMPE 26th National Symposium, Los Angeles, CA (Apr. 1981), pp. 232-249 (Center for Aerospace Information 81A-44344).
[608] "NASA Space Shuttle Technology Conference,’ vol. 2: "Structures and Materials,’ NASA TM-X – 2273 (1971); Heppenheimer, The Space Shuttle Decision, pp. 341-346.
[609] Schramm, et al., "Space Shuttle Tile.’ See also Donald H. Humes, "Hypervelocity Impact Tests on Space Shuttle Orbiter Thermal Protection Material,’ NASA TM-X-74039 (1977); M. J. Suppans and C. J. Schroeder, "Space Shuttle Orbiter Thermal Protection Development and Verification Test Program,’ AIAA Paper 78-485 (1 978); R. Jeffrey Smith, "Shuttle Problems Compromise Space Program,’ Science (Nov. 23, 1979), pp. 910-91 2, 914; Mitch Waldrop, "Space Shuttle Tiles:
A Question of Bonding,’ Chemical and Engineering News, vol. 58 (May 1 2, 1980), pp. 27-29; W. C. Rochelle, et al., "Orbiter TPS Development and Certification testing at the NASA/JSC 1 0 MW Atmospheric Reentry Materials and Structures Evaluation Facility,’ AIAA Paper 83-0147 (1983).
[610] Richard G. O’Lone, "Thermal Tile Production Ready to Roll," Aviation Week (Nov. 8, 1976), pp. 51-54; L. J. Korb, C. A. Morant, R. M. Calland, and C. S. Thatcher, "The Shuttle Orbiter Thermal Protection System," American Ceramic Society Bulletin, vol. 60, 1981, pp. 1 1 88-1 193.
[611] L. J. Korb and H. M. Clancy, "Symposium on Reusable Surface Insulation for Space Shuttle,’ vol. 1, NASA TM-X-2719 (1973), pp. 14-15; "The Shuttle Thermal Protection System—A Material and Structural Overview,’ Apr. 1981, pp. 232-249, CASI 81A-44344.
[612] David H. Greenshields, "Orbiter Thermal Protection System Development’ (Apr. 1977), pp. 1-28-1-42, CASI 77A-35304; North American-Rockwell, "Space Shuttle System Summary Briefing,’ Report SV 72-19 (July 8, 1972); Korb, et al., "Shuttle”; Robert M. Powers, Shuttle: The Worlds First Spaceship (Harrisburg, PA: Stackpole Books, 1979), p. 241.
[613] Frank Kreith, Principles of Heat Transfer (Scranton, PA: International Textbook Co., 1965), pp. 534-538; Benjamin M. Elson, "New Unit to Test Shuttle Thermal Guard,’ Aviation Week (Mar.
31, 1975), pp. 52-53; H. K. Larson and H. E. Goldstein, "Space Shuttle Orbiter Thermal Protection Material Development and Testing,’ (Mar. 1978), pp. 189-194, CASI 79A-17673.
[614] CASI 79A-17673; CASI 81A-44344.
[615] Korb, et al., "Shuttle’; Elizabeth A. Muenger, Searching the Horizon: A History of Ames Research Center, 1940-1976, NASA SP-4304 (Washington, DC: NASA, 1985).
[616] Aviation Week (Mar. 31, 1975), pp. 52-53; CASI 81A-44344; Gregory P. McIntosh and Thomas P. Larkin, "The Space Shuttle’s Testing Gauntlet,’ Astronautics and Aeronautics (Jan. 1976), pp. 60, 62-64.
[617] McIntosh and Larkin, "Space Shuttle’s Testing Gauntlet,’ pp. 60, 62-64; Aviation Week (Mar. 31, 1975), p. 52; MJ. Suppans and CJ. Schroeder, "Space Shuttle Orbiter Thermal Protection Material,’ AIAA Paper 78-485 (1978).
[618] McIntosh and Larkin, "Space Shuttle’s Testing Gauntlet,’ pp. 60, 62-64.
[619] Donald H. Humes, "Hypervelocity Impact Tests on Space Shuttle Orbiter Thermal Protection Material,’ NASA TM X-74039 (1977), p. 1 2.
[620] W. C. Rochelle, et al., "Orbiter TPS Development and Certification Testing at the NASA/
JSC 10 MW Atmospheric Reentry Materials and Structures Evaluation Facility,’ AIAA Paper 830147 (1983); Richard G. O’Lone, "Shuttle Test Pace Intensifies at Ames,’ Aviation Week (June 24, 1974), p. 71; Mitch Waldrop, "Space Shuttle Tiles: A Question of Bonding,’ Chemical and Engineering News, vol. 58 (May 1 2, 1980), pp. 27-29; Paul A. Cooper and Paul F. Holloway, "Shuttle Tile Story,’ pp. 27, 29; William C. Schneider and Glenn J. Miller, "The Challenging ‘Scales of the Bird’ (Shuttle Tile Structural Integrity)’ in Norman Chaffee, ed., "Space Shuttle Technical Conference,’ NASA Conference Publication CP-2342 (1983), pp. 403-404.
[621] "First Shuttle Launch Vehicle Being Assembled at Palmdale," Aviation Week (Nov. 27, 1978), p. 64; Waldrop, "Tiles"; Craig Covault, "Thermal Tile Application Accelerated," Aviation Week (May 21, 1979), pp. 59-63.
[622] Aviation Week (Nov. 27, 1978), p. 64; Waldrop, "Tiles"; Craig Covault, "Administration Backs Shuttle Fund Rise," Aviation Week (Sept. 17, 1979), pp. 22-23.
[623] LJ. Graham, F. E. Sugg, and W. Gonzalez, "Nondestructive Evaluation of Space Shuttle Tiles, Ceramic Engineering and Science Proceedings, vol. 3, (1982), pp. 681-683; Schneider and Miller, "Challenging"; Astronautics and Aeronautics (Jan. 1981), p. 29.
81 . "Densification Process Applied to Shuttle Tiles," Aviation Week (Feb. 25, 1980), p. 22; Astronautics and Aeronautics (Jan. 1981), pp. 29-30.
[625] Aviation Week (Feb. 25, 1 980), pp. 22-24; Craig Covault, "Mated Shuttle Reaches Pad 39," Aviation Week (May 7, 1979), p. 14.
[626] Waldrop, "Tiles."
[627] "Shuttle Engine, Tile Work Proceeding on Schedule," Aviation Week (Sept. 15, 1 980), p. 26.
[628] "NASA Finishes Shuttle Mating," Aviation Week (Dec. 1, 1980), pp. 1 8-1 9; Aviation Week (Sept. 17, 1979), p. 22; "NASA Presses to Hold Tight Shuttle Schedule," Aviation Week (Aug. 4, 1980), p. 24.
[629] John D. Anderson, A History of Aerodynamics (New York: Cambridge University Press, 1997), pp. 441-443.
[630] Dean R. Chapman, Hans Mark, and Melvin W. Pirtle, "Computers vs. Wind Tunnels for Aerodynamic Flow Simulations,’ Astronautics and Aeronautics (Apr. 1975), p. 26.
[631] T. A. Heppenheimer, Hypersonic Technologies and the National Aerospace Plane (Arlington, VA: Pasha Publications, 1990), pp. 128-134.
[632] William D. Metz, "Midwest Computer Architect Struggles with the Speed of Light,’ Science (Jan. 27, 1978), pp. 404-405.
[633] Gina Bari Kolata, "Who Will Build the Next Supercomputer?" Science, Jan. 16, 1981, pp. 268-269; Randolph A. Graves, Jr., "Computational Fluid Dynamics: The Coming Revolution," Astronautics and Aeronautics (Mar. 1982), pp. 20-28; Astronautics and Aeronautics (Apr. 1975), pp. 22-30. For numbers of partial derivatives, see Dean R. Chapman, "Computational Aerodynamics Development and Outlook," AIAA Journal, vol. 17, No. 12 (1979), p. 1 294.
91 . Science, Jan. 16, 1981, pp. 268-269; Benjamin B. Elson, "Computer Seen Assuming Shuttle Tasks." Aviation Week (Sept. 3, 1973), pp. 14-16; D. L. Slotnick, "The Fastest Computer," Scientific American (Feb. 1971), pp. 76-87.
[635] Walter A. Reinhardt, "Parallel Computation of Unsteady, Three-Dimensional, Chemically Reacting, Nonequilibrium Flow Using a Time-Split Finite Volume Method on the Illiac IV," Journal of Physical Chemistry, vol. 81, no. 25 (1977), pp. 2427-2435.
[636] Richard G. O’Lone, "Tunnel Tests Yield New Orbiter Data," Aviation Week (June 30, 1975), pp. 43-44.
[637] Charlie C. Dill, et al., "The Space Shuttle Ascent Vehicle Aerodynamic Challenges: Configuration Design and Data Base Development,’ in Norman Chaffee, ed., "Space Shuttle Technical Conference,” NASA CP-2342, (1983), pp. 151-152, 161.
[638] Richard G. O’Lone, "Shuttle Task Pace Intensifies at Ames,’ Aviation Week (June 24, 1 974), p. 71; Craig Covault, "Thermal, Weight Concerns Force Changes to Shuttle,’ Aviation Week (Dec. 9, 1974), p. 19; Dill, et al., "Ascent,” pp. 154, 165.
[639] James C. Young, et al., "The Aerodynamic Challenges of the Design and Development of the Space Shuttle Orbiter,’ in Chaffee, "Conference,” pp. 217-220.
[640] C. Thomas Modlin, Jr., and George A. Zupp, Jr., "Shuttle Structural Dynamics Characteristics-The Analysis and Verification,’ in Chaffee, "Conference," p. 326; "COSMIC Software Catalog,’ NASA CR-191005 (1993).
[641] Dennis Jenkins, Space Shuttle: The History of the National Space Transportation System (Stillwater, MN: Voyageur Press), 2001, p. 416; James M. Grimwood, Barton C. Hacker, and Peter J. Vorzimmer, Project Gemini Technology and Operations: A Chronology, NASA SP-4002 (Washington, DC: NASA, 1969), pp. 68, 76, 121; Roger E. Bilstein, Stages to Saturn: A Technological History of the Apollo/Saturn Launch Vehicles, NASA SP-4206 (Washington, DC: NASA, 1980), pp. 360, 362-363.
[642] Modlin and Zupp, "Structural,’ p. 326; Alden C. Mackey and Ralph E. Gotto, "Structural Load Challenges During Space Shuttle Development,’ in Chaffee, "Conference,” pp. 335-339.
[643] Craig Covault, "NASA Evaluating Major Shuttle Orbiter Changes," Aviation Week (Oct. 10,
1977), p. 26; Photo of Structural Test Article, Aviation Week, Mar. 6, 1978, p. 1 3; Philip C. Glynn and Thomas L. Moser, "Orbital Structural Design and Verification," in Chaffee, "Conference," pp. 353-356.
[644] Richard J. Weber and John S. MacKay, "An Analysis of Ramjet Engines Using Supersonic Combustion,’ NACA TN-4386 (1958), p. 22; Irving Pinkel and John S. Serafim, "Graphical Method for Obtaining Flow Field in Two-Dimensional Supersonic Stream to Which Heat is Added,’ NACA TN-2206 (1950); Irving Pinkel, John S. Serafini, and John L. Gregg, "Pressure Distribution and Aerodynamic Coefficients Associated with Heat Addition to Supersonic Air Stream Adjacent to Two-Dimensional Supersonic Wing,’ NACA RM-E51K26 (1952).
[645] Alan Newman, "Speed Ahead of its Time,’ Johns Hopkins Magazine, vol. 40, no. 4 (Dec.
1988), pp. 26-31; Harold E. Gilreath, "The Beginning of Hypersonic Ramjet Research at APL,’ Johns Hopkins Applied Physics Laboratory Technical Digest, vol. 11, no. 3-4 (1990), pp. 319-335; G. L. Dugger, F. S. Billig, and W. H. Avery, "Hypersonic Propulsion Studies at the Applied Physics Laboratory, The Johns Hopkins University,’ Johns Hopkins University Applied Physics Laboratory Report TG 405 (June 14, 1961), esp. pp. 1-3; Frank D. Stull, Robert A. Jones, and William P. Zima, "Propulsion Concepts for High Speed Aircraft,’ Paper 75-1092, Society of Automotive Engineers (1975); Paul J. Waltrup, Griffin Y. Anderson, and Frank D. Stull, "Supersonic Combustion Ramjet (Scramjet) Engine Development in the United States,’ Johns Hopkins University Applied Physics Laboratory Paper 76-042 (1976); Paul J. Waltrup, "Liquid Fueled Supersonic Combustion Ramjets: A Research Perspective of the Past, Present and Future,’ AIAA Paper 86-0158 (1986); Paul J. Waltrup, "Hypersonic Airbreathing Propulsion: Evolution and Opportunities,’ in Advisory Group for Aeronautical Research and Development, Conference Proceedings on the Aerodynamics of Hypersonic Lifting Vehicles (Neuilly sur Seine, France: NATO – AGARD, 1987), pp. 1-29; and in Thomas C. Adamson, Jr., "Aeronautical and Aerospace Engineering Education at the University of Michigan,’ in Barnes McCormick, et al., Aerospace Engineering Education During the First Century of Flight (Reston, VA: AIAA, 2004), p. 54.
[646] Edward T. Curran, "Scramjet Engines: The First Forty Years,” Journal of Propulsion and Power, vol. 1 7, No. 6 (Nov.-Dec. 2001), pp. 1 1 38-1 148; Antonio Ferri, "Review of Scramjet Technology,’ Journal of Aircraft, vol. 5, no. 1 (Jan. 1968), pp. 3-10; T. A. Heppenheimer, Facing the Heat Barrier: A History of Hypersonics, SP-2007-4232 (Washington, DC: NASA, 2007), p. 103; R. R. Jamison, "Hypersonic Air Breathing Engines,’ in A. R. Collar and J. Tinkler, Hypersonic Flow: Proceedings of the Eleventh Symposium of the Colston Research Society held in the University of Bristol, Apr. 6-8, 1959 (London: Butterworths Scientific Publications, 1960), pp. 391-408; S. W. Greenwood, "Spaceplane Propulsion,’ The Aeroplane and Astronautics (May 25, 1961), pp. 597-599.
[647] John V. Becker, "Confronting Scramjet: The NASA Hypersonic Ramjet Experiment,’ in Richard P. Hallion, ed., The Hypersonic Revolution: Eight Case Studies in the History of Hypersonic Technology, vol. 2: From Scramjet to the National Aero-Space Plane, 1964-1986 (Wright-Patterson AFB: Aeronautical Systems Division, 1987), p. 752; Antonio Ferri, "Review of Problems in Application of Supersonic Combustion,’ 7th Lanchester Memorial Lecture, Journal of the Royal Aeronautical Society, vol. 68, no. 645 (Sept. 1964), pp. 595, 597; Antonio Ferri, "Supersonic Combustion Progress,’ Astronautics & Aeronautics, vol. 2, no. 8 (Aug. 1964), pp. 32-37; Heppenheimer, Facing the Heat Barrie, pp. 104-105.
[648] Air Force Scientific Advisory Board, "Memo-Report of the USAF Scientific Advisory Board Aerospace Vehides/Propulsion Panels on Aerospaceplane, VTOL, and Strategic Manned Aircraft’ (Oct.
24, 1963), pp. 1, 3, SAB Office files, USAF HQ, Pentagon, Washington, DC; see also F. E. Jariett and G. Karel, "Aerospaceplane: The Payload Capabilities of Various Recoverable Systems All Using Hydrogen Fuel,’ General Dynamics Astronautics Report AE62-0892 (Oct. 25, 1962), esp. pp. 8-23; "Aerospaceplane May be a Two-Stage Vehicle,’ Aviation Week & Space Technology (July 22, 1963), pp. 245-249; Heppenheimer, Facing the Heat Barrier, pp. 1 1 2-1 28.
[649] M. L. Brown and R. L. Maxwell, Marquardt Corporation, "Scramjet Incremental Flight Test Program,’ Summary, Marquardt-AF Aero-Propulsion Laboratory Report AFAPLTR-67-1 1 2 (1968), pp. 3-4; Becker, "Confronting Scramjet,’ in Hallion, ed., Hypersonic Revolution, vol. 2, pp. 747-861, examines the HRE in detail; John R. Henry and Griffin Y. Anderson, "Design Considerations for the Airframe-Integrated Scramjet,’ NASA TM-X-2895 (1973); Robert A. Jones and Paul W. Huber, "Toward Scramjet Aircraft,’ Astronautics and Aeronautics, vol. 16, no. 2 (Feb. 1978), pp. 38-48; G. Burton Northam and G. Y. Anderson, "Supersonic Combustion Ramjet Research at Langley,’ AIAA Paper 86-0159 (1986).
[650] NASA Langley completed 963 successful runs of three strut, parametric, and step-strut scramjets between 1976-1987; from Edward G. Ruf, "Airframe-Integrated Scramjet Engine tests in NASA Langley Scramjet Engine Test Facilities,’ at http://hapb-www. larc. nasa. gov/Public/ Engines/engine_tests. html, accessed on May 1, 2009.
[651] Northam and Anderson, "Supersonic Combustion Ramjet Research,’ AIAA Paper 86-0159, p. 7; for NASA and other work, see J. Menzler and T. W. Mertz, "Large Scale Supersonic Combustor Testing at Conditions Simulating Mach 8 Flight,’ AIAA Paper 70-715 (1970); Carl A. Trexler, "Inlet Performance of the Integrated Langley Scramjet Module (Mach 2.3 to 7.6),’ AIAA Paper 75-1212 (1975); Robert W. Guy and Ernest A. Mackley, "Initial Wind Tunnel Tests at Mach 4 and 7 of a Hydrogen-Burning, Airframe Integrated Scramjet,’ AIAA Paper 79-7045 (1 979); and R. C. Rogers, D. P. Capriotti, and R. W. Guy, "Experimental Supersonic Combustion Research at NASA Langley,’ AIAA Paper 2506 (1998).
[652] USAF Aeronautical Systems Division news release 84-21 1; Richard P. Hallion, "Yesterday, Today, and Tomorrow: From Shuttle to the National Aero-Space Plane,’ in Hallion, ed., Hypersonic Revolution, vol. 2, pp. 1 336-1 337, 1361; S. A. Tremaine and Jerry B. Arnett, "Transatmospheric Vehides—A Challenge for the Next Century,’ AIAA Paper 84-2414 (1984).
1 1 0. Quote from Heppenheimer interview with Arthur Thomas, Sept. 24, 1987.
[654] Quote from Heppenheimer interview with Robert Williams, May 1, 1986.
[655] National Commission on Space, Pioneering the Space Frontier (New York: Bantam Books,
1986), p. 1 84; Joint DOD-NASA Task Team Report, National Space Transportation and Support Study (Washington, DC: GPO, 1986); President Ronald Reagan, State of the Union Address, Feb. 4, 1986.
[656] Larry Schweikart, The Quest for the Orbital Jet: The National Aero-Space Plane Program 11983-1995), vol. 3 of Hallion, ed., The Hypersonic Revolution (Washington, DC: USAF, 1998), pp. 349, 279-351.
1 14. Stuart O. Schmitt, Theodore J. Wierzbanowski, and Johnny Johnson, "The Challenge of X-30 Flight Test,’ 31 st Symposium, Society of Experimental Test Pilots, Beverly Hills, CA, Sept. 26, 1987; United States General Accounting Office, "National Aero-Space Plane: A Technology Development and Demonstration Program to Build the X-30,’ Report GAO/NSIAD-88-1 22 (Apr. 1988); Alan W. Wilhite, et al., "Concepts Leading to the National Aero-Space Plane Program,’ AIAA Paper 90-0294 (1990); Robert B. Barthelemy, "The National Aero Space Plane Program: A Revolutionary Concept,’ Johns Hopkins Applied Physics Laboratory Technical Digest, vol. 11, no. 2 & 3 (1990), pp. 31 2-31 8; United States General Accounting Office, "National Aero-Space Plane: Key Issues Facing the Program,’ Report GAO/T-NSIAD-92-26 (Mar. 1992), pp. 4-15; Joseph F. Shea, et al., "Report of the Defense Science Board Task Force on National Aero-Space Plane (NASP) Program’ (1992); United States General Accounting Office, National Aero-Space Plane: Restructuring Future Research and Development Efforts, Report GAO/NSIAD-93-71 (Dec. 1992), p. 4; and Ray L. Chase and Ming H. Tang, "A History of the NASP Program from the Formation of the Joint Program Office to the Termination of the HySTP Scramjet Performance Demonstration Program,’ AIAA Paper 95-6031 (1995).
1 1 5. Author interview with Robert Williams, May 1, 1 986.
1 1 6. Quote from Douglas L. Dwoyer, Paul Kutler, and Louis A. Povinelli, "Retooling CFD for Hypersonic Aircraft,’ Aerospace America (Oct. 1987), p. 35.
1 1 7. Charles E. Cockrell, Jr., Walter C. Engelund, Robert D. Bittner, Tom N. Jentinck, Arthur D. Dilley, and Abdelkader Frendi, "Integrative Propulsive Computational Fluid Dynamics Methodology for the Hyper-X Flight Experiment.’ Journal of Spacecraft and Rockets (Nov.-Dec. 2001), pp. 838, 843; S. Srinivasan, R. D. Bittner, and BJ. Bobskill, "Summary of the GASP Code Application and Evaluation Effort for Scramjet Combustor Flow-fields,’ AIAA Paper 93-1973 (1993).
1 1 8. T. A. Heppenheimer, "Some Tractable Mathematics for Some Intractable Physics,’ Mosaic (National Science Foundation), spring 1991, p. 30.
1 19. Quote in P. Bradshaw, "Progress in Turbulence Research,’ AIAA Paper 90-1480 (1990), p. 3.
1 20. Jack J. Dongarra, "Performance of Various Computers Using Standard Linear Equations Software in a Fortran Environment,’ Argonne National Laboratory, Technical Memorandum 23 (Sept. 30, 1988).
121. "Super Supercomputers,’ Aviation Week (Feb. 16, 2009).
1 22. Krishnan Mahesh, et al., "Large-Eddy Simulation of Gas Turbine Combustors.’ Annual Research Briefs (Stanford: Center for Turbulence Research, Stanford University, 2001), pp. 3-17.
1 23. Author interview, John D. Anderson, Jr., Nov. 19, 2008.
[667] Quote: Charles E. Cockrell, Jr., et al., Journal of Spacecraft and Rockets (2001), p. 841;
L. D. Huebner, K. E. Rock, R. T. Voland, and A. R. Wieting, "Calibration of the Langley 8-Foot High Temperature Tunnel for Hypersonic Propulsion Airbreathing Testing,’ AIAA Paper 96-2197 (1 996).
1 25. R. W. Guy, et al., "Operating Characteristics of the Langley Mach 7 Scramjet Test Facility,’ NASA TM-81 929 (1 981); S. R. Thomas and R. W. Guy, "Expanded Operational Capabilities of the Langley Mach 7 Scramjet Test Facility, NASA TP-2186 (1 983); E. H. Andrews, Jr., et al., "Langley Mach 4 Scramjet Test Facility,’ NASA TM-86277 (1985); D. E. Reubush and R. L. Puster, "Modification to the Langley 8-Ft. High Temperature Tunnel for Hypersonic Propulsion Testing,’ AIAA Paper 1987-1887 (1987); D. W. Witte, et al., "1998 Calibration of the Mach 4.7 and Mach 6 Arc-Heated Scramjet Test Facility Nozzles,’ NASA TM-2004-21 3250 (2004).
1 26. The engines and their total successful test runs were Gov’t Baseline (1 14); Engine A (69); Engine A-1 (55); Engine A-2 (321); Engine A-2+ (72); Engine C (233); Engine B-1 (359); NASP SX-20 (160); NASP SXPE (142); and NASP CDE (24), a total of 1,549 successful test runs. See the previously cited Ruf, "Airframe-Integrated Scramjet Engine Tests in NASA Langley Scramjet Engine Test Facilities."
1 27. Engine tests totaled 876, at Mach 5, 7, 1 0, and 15. The engine configurations, tunnels, and test runs were: DFX, 467 runs (97 in CHSTF and 370 in the AHSTF); HXEM, 146 runs (1 30 in AH – STF and 16 in the 8-ft. HTT); HXFE, 54 runs (all in 8-ft. HTT); and HSM, 209 runs (all in HYPULSE); see the previously cited Ruf, "Airframe-Integrated Scramjet Engine Tests in NASA Langley Scramjet Engine Test Facilities."
1 28. Bruce A. Smith, "Elevon Failure Precedes Loss of First X-43A," Aviation Week, June 1 1, 2001, pp. 50-51; Michael Dornheim: "X-43 to Fly in Fall," July 28, 2003, pp. 36-37; "A Breath of Fast Air," April 5, 2004, pp. 28-29.
1 29. Thomas J. Bogar, Edwards A. Eiswirth, Lana M. Couch, James L. Hunt, and Charles R. Mc – Clinton, "Conceptual Design of a Mach 10, Global Reach Reconnaissance Aircraft," AIAA Paper 96-2894 (1996); Charles R. McClinton, Vincent L. Rausch, Joel Sitz, and Paul Reukauf, "Hyper-X Program Status," AIAA Paper 01-0828, 39th Aerospace Sciences Meeting, Reno, NV, Nov. 8-1 1, 2001; David E. Reubush, Luat T. Nguyen, and Vincent L. Rausch, "Review of X-43A Return to Flight Activities and Current Status," AIAA Paper 03-7085 (2003); Jay Levine, "Exploring the Hypersonic Realm," The X-Press, vol. 46, no. 10 (Nov. 26, 2004), pp. 1, 8; Michael Dornheim, "But Now What?" Aviation Week, Nov. 22, 2004, pp. 24-26.
1 30. W. J. Hennigan, "Test Flight Shatters Records," Los Angeles Times, May 27, 2010; Matthew Shaer, "Scramjet-Powered X-51A WaveRider Missile Breaks Mach 6 Record," Christian Science Monitor, May 27, 2010; "WaveRider Sets Record for Hypersonic Flight," Associated Press Release, May 27, 2010.
[674] R. M. Stanley and R. J. Sandstrom, "Development of the XS-1 Airplane,’ HQ Air Materiel Command, Air Force Supersonic Research Airplane XS-1, Report No. 1 (Wright Field: Air Materiel Command, Jan. 9, 1948), p. 7.
[675] Walter C. Williams, "Instrumentation, Airspeed Calibration, Tests, Results and Conclusions,’ HQ AMC, Air Force Supersonic Research Airplane XS1, p. 24.
[676] W. C. Williams and A. S. Crossfield, "Handling Qualities of High-Speed Airplanes,’ RM L52A08 (Jan. 28, 1952).
[677] It should be noted, of course, that the all-moving tail was essentially a "rediscovery’ of earlier design practice. All-moving tails, for very different reasons, had been a feature of early airplanes, typified by the Wright Flyer and numerous European examples such as the Bleriot and the Fokker Eindecker.
[678] For cases, see Edwin J. Saltzman and Theodore G. Ayers, Selected Examples of NACA/NASA Supersonic Flight Research, SP-51 3 (Edwards, CA: NASA Dryden Flight Research Center, 1 995).
[679] Robert. G. Hoey and Capt. Iven C. Kincheloe, "F-104A Stability and Control,’ AFFTC TR-56-14, April 1958.
[680] See Joseph R. Chambers, Partners in Freedom: Contributions of the Langley Research Center to U. S. Military Aircraft of the 1990s, SP-2000-4519 (Washington, DC: NASA, 2000), passim; Robert K. Geiger, et al., The AGARD History, 1952-1987 (Neuilly sur Seine: NATO Advisory Group for Aeronautical Research and Development, 1988 ed.), pp. ix-xxv; and Thomas C. Lass – man, Sources of Weapon Systems Innovation in the Department of Defense: The Role of In-House Research and Development, 1945-2000 (Washington, DC: Center for Military History, 2008), pp. 93-97.
[681] Personal Experience as an Air Force Flight Planner during the X-1 5 envelope expansion flight-testing.
[682] Robert A. Tremant, "Operational Experience and Characteristics of the X-15 Flight Control System," NASA Technical Note D-1402 (Dec. 1962), and Wendell H. Stillwell, X-15 Research Results, SP-60 (Washington, DC: NASA, 1965), pp. 51-52.
[683] L. W. Taylor, Jr., and J. W. Smith, "An Analysis of the Limit-Cycle and Structural-Resonance Characteristics of the X-15 Stability Augmentation System,’ NASA TN-D-4287 (Dec. 1967).
1 1 . Weneth D. Painter and George J. Sitterle, "Ground and Flight Test Methods for Determining Limit Cycle and Structural Resonance Characteristics of Aircraft Stability Augmentation Systems,’ NASA TN-D-6867 (1972).
1 2. R. W. Kempel and J. A. Manke, "Flight Evaluation of HL-10 Lifting Body Handling Qualities at Mach Numbers from 0.30 to 1.86", NASA TN-D-7537, (Jan. 1974).
1 3. Milton O. Thompson with J. D. Hunley, Flight Research: Problems Encountered and What They Should Teach Us, SP-2000-4522 (Washington, DC: NASA, 2000), pp. 19-20; see also R.
Dale Reed with Darlene Lister, Wingless Flight: The Lifting Body Story, SP-4220 (Washington, DC: NASA, 1997), pp. 96-102.
[687] Personal recollections from serving as a member of the YF-16 Taxi Test Incident review team.
[688] Robert G. Hoey, et al., "Flight Test Results from the Entry and Landing of the Space Shuttle Orbiter for the First Twelve Orbital Flights," AFFTC TR-85-1 1 (1985), p. 104. Robert G. Hoey, et al., "AFFTC Evaluation of the Space Shuttle Orbiter and Carrier Aircraft—NASA Approach and Landing Test," AFFTC TR-78-14, May 1978, pp. 104, 114, 117. See also Richard P. Hallion, On the Frontier: Flight Research at Dryden, 1946-1981, SP-4303 (Washington, DC: NASA, 1984), pp. 249-250.
[689] Dennis R. Jenkins, X-]5: Extending the Frontiers of Flight, SP-2007-562 (Washington, DC: NASA, 2007), p. 402.
[690] Donald R. Bellman, et al., Investigation of the Crash of the X-J5-3 Aircraft on November 15, 1967 (Edwards: NASA Flight Research Center, Jan. 1968), pp. 8-15.
1 8. For more on its strengths and weaknesses, see L. W. Taylor, Jr., and E. J. Adkins, "Adaptive Flight Control Systems—Pro and Con,’ NASA TM-X-56008 (1964).
[692] Personal experience as an X-15 flight planner and X-20 stability and control flight test engineer.
[693] G. B. Merrick and L. W. Taylor, Jr., "X-15 Stability Augmentation System,’ NASA Report H-271 (Jan. 1961); L. W. Taylor, Jr., and J. W. Smith, "An Analysis of the Limit Cycle and Structural Resonance Characteristics of the X-15 Stability Augmentation System,’ NASA TN-D-4287 (Dec. 1967).
21 . John P. Smith, Lawrence J. Schilling, and Charles A. Wagner, "Simulation at Dryden Flight Research Facility from 1957 to 1982,’ NASA TM-101695 (1989), p. 4; Stillwell, X-15 Research Results, pp. 61-69.
[695] Weneth D. Painter and George J. Sitterle, "Ground and Flight Test Methods for Determining Limit Cycle and Structural Resonance Characteristics of Aircraft Stability Augmentation Systems,’ NASA TN-D-6867 June 1972).
[696] Ibid.
[697] Personal experience as a member of the B-1 Flight Readiness Review Team.
[698] Personal experience as a member of the Light Weight Fighter Joint Test Force.
[699] Interview with John Manke, HL-10 test pilot.
[700] Maj. Robert Ettinger, Capt. Robert Majoros, and Lt. Col. Cecil W. Powell, "Air Force Evaluation of the Fly-By-Wire Portion of the Surviveable Flight Control System Advanced Development Program," AFFTC TR-73-32 (Aug. 1973).
[701] Maj. James A. Eggers and Maj. William Bryant, Jr., “Flying Qualities Evaluation of the YF-16 Prototype Light Weight Fighter," AFFTC TR-75-15 (1975).
[702] The early advent of digital fly-by-wire is the subject of another case study in this volume (Pic – cirillo) and so is not examined in great detail here.
[703] Dwain A. Deets and Kenneth J. Szalai, "Design and Flight Experience with a Digital Fly-By-Wire Control System in an F-8 Airplane,’ NATO Advisory Group for Aeronautical Research and Development Conference Paper AGARD-CP-1 37 (1974); see also James E. Tomayko, Computers Take Flight: A History of NASA’s Pioneering Digital Fly-By-Wire Project, SP-2000-4224 (Washington,
DC: NASA, 2000).
[704] . Interview with Manke; see also Tomayko, Computers Take Flight, pp. 111-114.
[705] Capt. Lawrence Damman, Capt. Ronald Grabe, Robert Kennington, and Paul W. Kirsten, "Flight Test Development of a Multimode Digital Flight Control System Implemented in an A-7D (DIGITAC)," AFFTC TR-76-15 (June 1976).
[706] Personal experience as a member of the X-29 Flight Readiness Review Team.
[707] Paul Pellicano, Joseph Krumenacker, and David Van Hoy, "X-29 High Angle-of-Attack Flight Test Procedures, Results, and Lessons Learned," Society of Flight Test Engineers 21st Annual Symposium, Aug. 1990.
[708] Eddie Zavala, "Fiber Optic Experience with the Smart Actuation System on the F-1 8 Systems Research Aircraft," NASA TM-97-206223, Oct. 1997.
[709] Robert Navarro, "Performance of an Electro-Hydrostatic Actuator on the F-1 8 Systems Research Aircraft," NASA TM-97-206224, Oct. 1997.
[710] Joel R. Sitz, "F-1 8 Systems Research Aircraft," NASA TM-4433 (1992); Lane E. Wallace, Flights of Discovery: 50 Years at the NASA Dryden Flight Research Center, SP-4309 (Washington, DC: NASA, 1996), pp. 124-125.
[711] Eggers and Bryant, "Flying Qualities Evaluation of the YF-16," AFFTC TR-75-15 (1975).
[712] Theodore G. Ayers and James B. Hallissy, "Historical Background and Design Evolution of the Transonic Aircraft Technology Supercritical Wing," NASA TM-81356 (1981); Paul W. Phillips and Stephen B. Smith, "AFTI/F-1 1 1 Mission Adaptive Wing (MAW) Automatic Flight Control System Modes Lift and Drag Characteristics," AFFTC TR-89-03 (1989).
[713] Andrew M. Lizotte and Michael J. Allen, "Twist Model Development and Results From the Active Aeroelastic Wing F/A-18 Aircraft," NASA TM-2005-212861 (2005); see also Chambers, Partners in Freedom, pp. 78-81.
[714] E. Nissim, "Design of Control Laws for Flutter Suppression Based on the Aerodynamic Energy Concept and Comparisons With Other Design Methods,’ Technical Report TP-3056, Research Engineering, NASA Dryden Flight Research Center (1990) [given also as American Institute of Aeronautics and Astronautics Conference Paper 89-1 21 2 (1989)].
[715] J. T. Foughner, Jr., and C. T. Bensinger, "F-16 Flutter Model Studies With External Wing Stores,’ NASA TM-74078 (1977); C. Hwang, E. Jonson, G. Mills, T. Noll, and M. Farmer, "Wind Tunnel Test of a Fighter Aircraft Wing/Store Flutter Suppression System: An International Effort,’ AGARD R-689 (1980); R. P. Peloubet, Jr., and R. L. Haller, "Wind-Tunnel Demonstration of Actrive Flutter Suppression Using F-16 Model with Stores,’ AFWAL TR-83-3046, vol. 1 (1983); Joseph R. Chambers, Innovation in Flight: Research of the NASA Langley Research Center on Revolutionary Advanced Concepts for Aeronautics, SP-2005-4539 (Washington, DC: NASA, 2005), pp. 196-203, 212-215.
[716] For perspectives on the various members of the Blackbird family, see Peter W. Merlin, From Archangel to Senior Crown: Design and Development of the Blackbird, (Reston, VA: American Institute for Aeronautics and Astronautics, 2008); and also his Mach 3+: NASA/USAF YF-12 Flight Research, 1969-1979, SP-2001-4525 (Washington, DC: NASA, 2001).
[717] Personal experience during SR-71 accident investigation; Ben R. Rich and Leo Janos, Skunk Works: A Personal Memoir of My Years of Lockheed (Boston: Little, Brown, and Co., 1994), pp. 192-237.
[718] Merlin, Mach 3+, pp. 39-42.
[719] Marcelle Size Knaack, Post-World War II Fighters, vol. 1 of Encyclopedia of U. S. Air Force Aircraft and Missile Systems (Washington, DC: Office of Air Force History, 1 978), pp. 1 1 4-1 16; Bill Gunston, Early Supersonic Fighters of the West (New York: Charles Scribner’s Sons, 1975), pp. 153-1 57; HSFS, "Flight Experience With Two High-Speed Airplanes Having Violent Lateral-Longitudinal Coupling in Aileron Rolls,’ RM H55A1 3 (1955); Hubert M. Drake and Wendell H. Stillwell, "Behavior of the Bell X-1A Research Airplane During Exploratory Flights at Mach Numbers Near 2.0 and at Extreme Altitudes,’ RM H55G25 (1955); Hubert M. Drake, Thomas W. Finch, and James
R. Peele, "Flight Measurements of Directional Stability to a Mach Number of 1.48 for an Airplane Tested with Three Different Vertical Tail Configurations,’ RM H55G26 (1955).
[720] Hubert M. Drake and Wendell H. Stillwell, "Behavior of the Bell X-1A Research Airplane During Exploratory Flights at Mach Numbers Near 2.0 and at Extreme Altitudes,’ RM H55G25 (1955); Capt. Iven C. Kincheloe, USAF, "Flight Research at High Altitude, Part II,’ in Proceedings of the Seventh AGARD General Assembly, Nov. 18-26, 1957 (Washington, DC: NATO Advisory Group for Aeronautical Research and Development, 1958).
[721] Bell X-2 No. 1 Accident Report, copy in History Office archives, Air Force Flight Test Center, Edwards AFB, CA.
[722] Ronald Bel Stiffler, The Bell X-2 Rocket Research Aircraft: The Flight Test Program (Edwards AFB: Air Force Flight Test Center, Aug. 1 2, 1957), p. 87; Richard E. Day, "Coupling Dynamics in Aircraft: A Historical Perspective," SP-532 (1997).
[723] Smith, Schilling, and Wagner, "Simulation at Dryden," p. 1.
51 . Ibid., p. 3.
[725] Capt. John Retelle, "Measured Weight, Balance, and Moments of Inertia of the X-24A Lifting Body," AFFTC TD-71-6 (1971).
53. K. W. Iliff, B. G. Powers, and L. W. Taylor, Jr., "A Comparison of Newton-Raphson and Other Methods for Determining Stability Derivatives from Flight Data," NASA Report H-544 (Mar. 1969).
54. K. W. Iliff and L. W. Taylor, Jr., "Determination of Stability Derivatives from Flight Data Using a Newton-Raphson Minimization Technique," NASA TN-D-6579 (Mar. 1972).
55. Kenneth W. Iliff, "Aircraft Parameter Estimation," AIAA Meeting Paper 1987-0623 (1987).
[727] David L Kohlman, William G. Schweikhard, and Donald R. L Renz, "Advances in Flight Test Instrumentation and Analysis’ SAE Doc. No. 871 802, Oct. 1987.
[728] C. C. Clark and C. H. Woodling, "Centrifuge Simulation of the X-1 5 Research Aircraft,’ NADC MA-5916 (1959).
[729] Personal recollections as a flight planning engineer participating in the X-15 centrifuge program. Also see Dennis Jenkins, X-15: Extending the Frontiers of Flight.
[730] Robert G. Hoey, Lt. Col. Harry R. Bratt, and Maj. Russell L. Rogers, "A Dynamic Simulation of Pilot Controlled Boost for the X-20A Air Vehicle," AFFTC TDR-63-21 (1964).
[731] Edwin P. Hartman, Adventures in Research: A History of Ames Research Center, 1940-1965, SP-4302 (Washington, DC: NASA, 1970), pp. 164-166; 257-258; Paul F. Borchers, James A. Franklin, Jay W. Fletcher, Flight Research at Ames: Fifty-Seven Years of Development and Validation of Aeronautical Technology, SP-3300 (Washington, DC: NASA, 1998), passim; William M. Kauffman, Charles J. Liddell, Jr., G. Allan Smith, and Rudolph D. Van Dyke, Jr., "An Apparatus for Varying Effective Dihedral in Flight with Application to a Study of Tolerable Dihedral on a Conventional Fighter Airplane," NACA Report 948 (1949); Walter E. McNeill and Brent Y. Creer, "A Summary of Results Obtained during Flight Simulation of Several Aircraft Prototypes with Variable Stability Airplanes," NACA RM-A56C08 (1956); Richard F. Vomaske, Melvin Sadoff, and Fred J. Drinkwater, III, "The Effect of Lateral-Directional Control Coupling on Pilot Control of an Airplane as Determined in Flight and a Fixed-Base Flight Simulator," NASA TN-D-1 141 (1961); William M. Kauffman and Fred J. Drinkwater, III, "Variable Stability Airplanes in Lateral Stability Research," Aeronautical Engineering Review, vol. 14, No. 8 (Aug. 1955), pp. 29-30.
61 . G. Warren Hall, "Research and Development History of USAF Stability T-33," Journal of the American Aviation Historical Society, vol. 19, no. 4 (winter 1974).
[733] Mostly notably of these were a North American JF-100C Super Sabre (another Ames project), a Martin-Air Force v-stab Convair F-106 Delta Dart; the NASA FRC General Purpose Airborne Simulator (a modified Lockheed Jetstar executive jet transport); the CALSPAN-Air Force Convair NC-1 31 H Total In-Flight Simulator (TIFS), retired in late 2008; the CALSPAN variable stability Douglas B-26 Invader; its successor, the CALSPAN v-stab Learjet; and the most recent, the CALSPAN VISTA Lockheed Martin NF-16.
[734] Shafer, "In-Flight Simulation Studies at the NASA Dryden Flight Research Facility."
[735] Gene J. Matranga and Neil A. Armstrong, "Approach and Landing Investigation at Lift-Drag Ratios of 2 to 4 Utilizing a Straight-Wing Fighter Airplane," NASA TM-X-31 (1959); Gene J. Matranga and Neil A. Armstrong, "Approach and Landing Investigation at Lift-Drag Ratios of 2 to 4 Utilizing a Delta-Wing Fighter Airplane," NASA TM-X-1 25 (1959); Stillwell, X-15 Research Results, pp. 38-39; Milton O. Thompson, At the Edge of Space: The X-15 Flight Program (Washington: Smithsonian Institution Press, 1992).
[736] B. L. Schofield, D. F. Richardson, and P. C. Hoag, "Terminal Area Energy Management, Approach, and Landing Investigation for Maneuvering Reentry Vehicles using F-111A and NB-52B Aircraft," AFFTC TD-70-2 (1970).
[737] Capt. Austin J. Lyons, "AFFTC Experiences with Hybrid Computation in a Real-Time Simulation of the X-15A-2," AFFTC TR-66-44 (1967).
[738] Richard E. Day, "Coupling Dynamics in Aircraft: A Historical Perspective,’ SP-532 (1997), p. 1.
[739] William H. Phillips, "Effect of Steady Rolling on Longitudinal and Directional Stability, NACA TN-627 (1948).
[740] Joseph Weil, Ordway B. Gates, Jr., Richard D. Banner, and Albert E. Kuhl, "Flight Experience of Inertia Coupling in Rolling Maneuvers,’ RM H55WEIL (1955); HSFS, "Flight Experience With Two High-Speed Airplanes Having Violent Lateral-Longitudinal Coupling in Aileron Rolls,’ RM H55A1 3 (1955); Hubert M. Drake and Wendell H. Stillwell, "Behavior of the Bell X-1A Research Airplane During Exploratory Flights at Mach Numbers Near 2.0 and at Extreme Altitudes,’ RM H55G25 (1955); Hubert M. Drake, Thomas W. Finch, and James R. Peele, "Flight Measurements of Directional Stability to a Mach Number of 1.48 for an Airplane Tested with Three Different Vertical Tail Configurations,’ RM H55G26 (1955); Walter C. Williams and William H. Phillips, "Some Recent Research on the Handling Qualities of Airplanes,’ RM H55L29a (1 956).
70. Robert G. Hoey and Capt. Milburn G. Apt, "F-100C Phase IV Stability and Control Test’ AFFTC TR-56-25, Oct. 1956, pp 8, 144, 145.
[742] . Day, "Coupling Dynamics in Aircraft,’ p. 1 .
[743] In engineering shorthand, Cn/Cna=Cl/Cla.
[744] Day, "Coupling Dynamics in Aircraft,’ p. 1 .
[745] Stillwell, X-15 Research Results, pp. 51-52; Thompson, At the Edge of Space, pp. 200-202.
[746] Personal experience as a flight planning engineer during the X-15 initial envelope expansion tests.
[747] Robert G. Hoey, "Correlation of X-15 Simulation Experience with Flight Test Results, AGARD Report 530 (1966).
[748] See, for example, Document 25 in J. D. Hunley, ed., Toward Mach 2: The Douglas D-558 Program, SP-4222 (Washington, DC: NASA, 1999), pp. 101-103.
[749] H. Julian Allen and Alfred J. Eggers, Jr., "A Study of the Motion and Aerodynamic Heating of Ballistic Missiles Entering the Earth’s Atmosphere at High Supersonic Speeds,’ NACA Technical Report 1381 (1958) [this widely distributed report was preceded by a more restricted limited-issue classified report for Government and industry earlier]; see also Hartman, Adventures in Research, pp.
215-218.
[750] Jenkins, X-15: Extending the Frontiers of Flight, passim.
80. Joel W. Powell and Ed Hengeveld, "ASSET and PRIME: Gliding Re-Entry Test Vehicles," Journal of the British Interplanetary Society, vol. 36 (1983), pp. 369-376.
[752] . Personal inspection of the SV-5D (X-23) heat shield following vehicle recovery.
[753] Johnny G. Armstrong, "Flight Planning and Conduct of the X-15A-2 Envelope Expansion Program", FTC TD-69-4, July 1969.
[754] John V. Becker, "The X-15 Program in Retrospect," Raumfahrtforschung (Mar.-Apr. 1969).
[755] Robert Godwin, ed., Dyna-Soar Hypersonic Strategic Weapons System (Burlington, ON, Canada: Apogee Books, 2003) has an excellent compilation of contemporary Dyna-Soar documents.
[756] M. H. Shirk, "ASSET: Aerothermoelastic Vehicles (AEV) Results and Conclusions,’ AFFDL 65FD – 1197 (1965); "ASSET Final Briefing,’ AFFDL 65FD-850 (1965).
[757] Paul Cooper and Paul F. Holloway, "The Shuttle Tile Story,’ Astronautics & Aeronautics, vol. 1 9, no. 1 (Jan. 1981), pp. 24-34; Robert G. Hoey, et al., "Evaluation of the Space Shuttle Orbiter First Orbital Flight: Final Report,’ AFFTC TR-8 1-21 (1981); NASA LRC, "Shuttle Performance: Lessons Learned,’ NASA Conference Publication 2283 (1 983); and Robert G. Hoey, et al., "Flight Test Results from the Entry and Landing of the Space Shuttle Orbiter for the First Twelve Orbital Flights: Final Report,’ AFFTC TR-85-1 1 (1985).
[758] John D. Anderson, Jr., A History of Aerodynamics, (Cambridge: Cambridge University Press,
1997), pp. 23, 25, 31, 35; Edme Mariotte, Traite de la percussion ou choc des corps (Paris: Academy of Sciences, 1673).
[759] For further references in the history of fluid dynamics, see R. Giacomelli and E. Pistolesi, "Historical Sketch,’ in William F. Durand, ed., Aerodynamic Theory, vol. 1 (Berlin: Julius Springer Verlag, 1934); Theodore von Karman, Aerodynamics (Cornell: Cornell University Press, 1954); G. A. Tokaty, A History and Philosophy of Fluid Mechanics (Henley, UK: G. T. Foulis and Co., Ltd., 1971); Olivier Darrigol, Worlds of Flow: A History of Hydrodynamics from the Bernoullis to Prandtl (Oxford: Oxford University Press, 2005); and Michael Eckert, The Dawn of Fluid Dynamics: A Discipline Between Science and Technology (Weinheim, Germany: Wiley-VCH Verlag GmbH & Co. KGaA, 2006). All trace the evolution of fluid mechanics and aerodynamics in great detail, with excellent references to primary sources and other works.
[760] Isaac Newton, Mathematical Principles of Natural Philosophy (Chicago: Encyclopedia Britan – nica, Inc., 1952 ed. of a 1687 work), pp. 159-267.
[761] As explicated by Leonhard Euler in his Principles of the Motion of Fluids (1752), General Principles of the State of Equilibrium of Fluids (1753), and General Principles of the Motion of Fluids (1755).
[762] Anderson, History of Aerodynamics, p. 89.
[763] C. L.M. H. Navier, "Memoire sur les du mouvement des fluids,’ Memoires de I’Academie Royale des Sciences, No. 6 (1 823), pp. 389-416.
[764] G. G. Stokes, "On the Theories of the Internal Friction of Fluids in Motion, and of the Equilibrium and Motion of Elastic Solids,’ Transactions of the Cambridge Philosophical Society, vol. 8, no. 22 (1845), pp. 287-342.
[765] This discussion is elaborated upon in the author’s Computational Fluid Dynamics: The Basics With Applications (New York: McGraw-Hill, 1995).
[766] Ibid., p. 3.
[767] L. F. Richardson, "The Approximate Arithmetical Solution by Finite Differences of Physical Problems Involving Differential Equations, With Application to the Stresses in a Masonry Dam,’ Philosophical Transactions of the Royal Society of London, ser. A, vol. 210 (1910), pp. 307-357.
1 1 . Many partial differential equations fall within one of the following categories: elliptic equations, parabolic equations, and hyperbolic equations, differentiated by their mathematical (and graphical) behavior. The setting-up of a given numerical solution of these equations depends critically on whether the equation in question is elliptic, parabolic, or hyperbolic.
[769] Richard Courant, K. O. Friedrichs, and Hans Lewy, "Uber die Partiellen Differenzengleichungen der Mathematischen Physik,’ Mathematische Annalen, vol. 100, (1928), pp. 32-74. All three emigrated to the U. S.
1 3. Paul E. Ceruzzi, Beyond the Limits: Flight Enters the Computer Age (Cambridge: MIT Press, 1989), p. 15.
[771] "Super Supercomputers,’ Aviation Week (Feb. 16, 2009).
[772] J. W. Strutt (Lord Rayleigh), "On the Resistance of Fluids,’ Philosophical Magazine, ser. 57 (1876), pp. 430-441.
[773] Milton O. Van Dyke, "Supersonic Flow Past a Family of Blunt Axisymmetric Bodies,’ NASA Technical Report R-1 (1959).
[774] In the old days of obtaining the computer results printed out on paper, I would tell my students to tear off the last page, keep it, and throw the rest out, because the last page contained the answer.
[775] G. Moretti and M. Abbett, "A Time-Dependent Computational Method for Blunt Body Flows, AIAA Journal, vol. 4, no. 1 2 (1966), pp. 2136-2141.
[776] Earll Murman and Julian D. Cole, "Calculation of Plane Steady Transonic flows,’ AIAA Journal, vol. 9, no. 1 (Jan. 1971), pp 114-121.
[777] A. Jameson, W. Schmidt, and E. Turkel, "Numerical Solution of the Euler Equations by Finite Volume Methods Using Runge-Kutta Time-Stepping Schemes,’ AIAA Paper 81-1 259 (1 981); see also A. Jameson, "Successes and Challenges in Computation Aerodynamics,’ AIAA Paper 871184 (1987).
[778] Eli Turkel, "Algorithms for the Euler and Navier-Stokes equations for supercomputers,’ NASA CR-172543 (1985), p. 1.
[779] R. W. MacCormack, "The Effect of Viscosity in Hypervelocity Impact Cratering,’ AIAA Paper 69-354 (1969).
[780] KJ. Weilmuenster, “High Angle of Attack Inviscid Flow Calculations of Shuttle-Like Vehicles with Comparisons to Flight Data,’ AIAA Paper No. 83-1 798 (1 983). For Weilmuenster’s earlier work, see his “Solution of a large hydrodynamic problem using the STAR-100 computer,’ NASA TM-X – 7394 (1976).
[781] J. S. Shang and S. J. Scherr, "Navier-Stokes Solution for a Complete Re-entry Configuration,’ Journal of Aircraft, vol. 23, no. 12 (1986), pp. 881-888.
[782] See P. Perrier, "Industrial Methodologies for the Design of Hypersonic Vehicles,’ and Richard D. Neumann, "Defining the Aerothermodynamic Methodology,’ in J. J. Bertin, et al., Hypersonics, vol.
1: Defining the Hypersonic Environment (Boston: Birkhauser Boston, Inc., 1 989), pp. 93-160.
[783] The author has had the privilege of looking over Peter Gnoffo’s shoulder for two decades as he progressively developed LAURA. Some examples of work carried out with the LAURA code are given in Robert B. Greendyke and Peter A. Gnoffo "Convective and Radiative Heating for Vehicle Return from the Moon and Mars," NASA TM-1 10185 (1995); Kenneth Sutton and Peter A. Gnoffo, "Multi-Component Diffusion with Application to Computational Aerothermodynamics," AIAA Paper 98-2575 (1998); William L. Kleb, et al., "Collaborative Software Development in Support of Fast Adaptive AeroSpace Tools (FAAST)," AIAA Paper 2003-3978 (2003); Peter A. Gnoffo and Jeffrey A. White, "Computational Aerothermodynamic Simulation Issues on Unstructured Grids," AIAA Paper 2004-2371 (2004); Peter A. Gnoffo, "Simulation of Stagnation Region Heating in Hypersonic Flow on Tetrahedral Grids," AIAA Paper 2007-3960 (2007); Karen L. Bibb, et al., "Parallel, Gradient-Based Anisotropic Mesh Adaption for Re-Entry Vehicle Configurations," AIAA Paper 2006-3579 (2007); Christopher O. Johnson, et al.,"The Influence on Radiative Heating for Earth Entry," NASA Document ID 20080023455 (2008); Richard A. Thompson and Peter A. Gnoffo, "Implementation of a Blowing Boundary Condition in the LAURA Code," NASA Document ID 20080008560 (2008); Peter A. Gnoffo, "Multi-Dimensional, Inviscid Flux Reconstruction for Simulation of Hypersonic Heating on Tetrahedral Grids," AIAA Paper 2009-0599 (2009); and Gnoffo, Peter A., et al., "Implementation of Radiation, Ablation, and Free Energy Minimization Modules for Coupled Simulations of Hypersonic Flow," AIAA Paper 2009-1 399 (2009).
[784] Judy Conlon, "OVERFLOW Code Empowers Computational Fluid Dynamics,’ NASA Insights, vol. 5 (Apr. 1998).
[785] For more on CFL3D and its applications, see J. L. Thomas, and R. W. Walters, "Upwind Relaxation Algorithms for the Navier-Stokes Equations,’ AIAA Paper 85-1501-CP (1 985); J. L. Thomas, B. van Leer, and R. W. Walters, "Implicit Flux-Split Schemes for the Euler Equations,’ AIAA Paper 85-1680 (1985); W. K. Anderson, J. L. Thomas, and B. van Leer, "Comparison of Finite Volume Flux Vector Splitting for the Euler Equations,’ AIAA Journal, vol. 24, no. 9 (Sept. 1986), pp. 1453-1460; J. L. Thomas, et al., "High-Speed Inlet Flows,’ Symposium on Advances and Applications in CFD, Winter Annual Meeting of ASME, Chicago, IL, Nov. 1988; W. B. Compton, III, J. L. Thomas, W. K. Abeyounis, and M. L. Mason, "Transonic Navier-Stokes Solutions of ThreeDimensional Afterbody Flows,’ NASA TM-41 1 1 (1989); J. L. Thomas, "An Implicit Multigrid Scheme for Hypersonic Strong-Interaction Flowfields," Comm. Applied Numerical Methods, vol. 8 (1992), pp. 683-693; and J. L. Thomas, "Reynolds Number Effects on Supersonic Asymmetrical Flows over a Cone,’ Journal of Aircraft, vol. 30 no. 4, (Apr. 1993), pp. 488-495.
[786] There are many topics touching on structural analysis and loads prediction, which the author has not covered. Materials science is excluded, for this paper considers methods for predicting the macroscopic characteristics of a structure, not analyzing the microscopic properties of the materials from which it is built. So too are computer-aided design, computational fluid dynamics, multidisciplinary optimization, structural test and data analysis techniques, and nondestructive inspection/evaluation, aside from passing reference. Though this paper focuses on NASA activities and contributions, there is no intent to minimize the importance of contributions from the aircraft industry, the technical software industry, universities, and other research organizations.
[787] A. F. Zahm and L. H. Crook, "Airplane Stress Analysis,’ Report No. 82, Aerodynamical Laboratory, Bureau of Construction and Repair, U. S. Navy (1918); Roy G. Miller, "Torsion of wing trusses at diving speeds,’ NACA TR-104, Langley Research Center (1921); F. H. Norton and D. L. Bacon, "The pressure distribution over the horizontal tail surfaces of an airplane II,’ NACA TR-1 19, Langley Research Center (1921); Norton and W. G. Brown, "Pressure distribution over the rudder and fin of an airplane in flight,’ NACA TR-149, Langley Research Center (1923); J. C. Hunsaker and E. B. Wilson, "Report on Behavior of Aeroplanes in Gusts,’ Massachusetts Institute of Technology (1915), (prepared by MIT and predating the establishment of the NACA but listed and marked as NACA-TR-1); E. P. Warner, "Static Testing and Proposed Standard Specifications,’ NACA TN-6, Langley Field, VA (July 1920), p. 1.
[788] W. Jefferson Stroud, e-mail message to author, Mar. 29, 2009.
[789] Stroud, e-mail to author.
[790] Interview of Annie J. Easley by Sandra Johnson, Cleveland, OH, Aug. 21, 2001, pp.2, 8, in NASA Oral History Project, on NASA Glenn Research Center History Office Web site at http:// grchistory. grc. nasa. gov/index. cfm, accessed Apr. 29, 2009.
[791] Henry Pearson, William McGowan, and James Donegan, "Horizontal Tail Loads in Maneuvering Flight,’ NACA TR-1007, Langley Aeronautical Laboratory, VA (1 950); Interview of Gonzalo Mendoza and Zachary Hazen by author, Wichita, KS, Apr. 6, 2009.
[792] Arthur W. Leissa, "The Historical Basis of the Rayleigh and Ritz Methods,’ in 7th International Symposium on Vibrations of Continuous Systems, Zakopane, Poland, July 2009.
[793] "Carlo Alberto Castigliano,’ at http://www-groups. dcs. st-and. ac. uk/~history/Biographies/ Castigliano. html, accessed May 22, 2009.
[794] Stanley U. Benscoter and Richard H. MacNeal, "Equivalent Plate Theory for a Straight Multicell Wing," NACA TN-2786 (1952), p. 1.
[795] Benscoter and MacNeal, "Equivalent Plate Theory," NACA TN-2786, p. 28.
1 1 . Victor Paschkis and Frederick Ryder, Direct Analog Computers (New York: John Wiley & Sons, Inc., 1968), preface.
1 2. Paschkis and Ryder, p. 383.
1 3. Glenn Bugos, Atmosphere of Freedom: Sixty Years at the NASA Ames Research Center, NASA SP-4314 (Washington, DC: NASA, 2000), pp. 181-182.
[799] Gene Waltman, Black Magic and Gremlins, pp. 1-4.
[800] Jeremy Meyers, "A Brief History of the Computer (b. c. – 1 993a. d.)," on Meyers’s Web site at http://www. jeremymeyers. eom/comp#EDC, accessed Apr. 29, 2009; see also Paul E. Ceruzzi, A History of Modern Computing (Cambridge: MIT Press, 1999), pp. 7, 15, 20-21 .
[801] Meyers, "A Brief History of the Computer (b. c. – 1 993a. d.)."
[802] M. J. Turner, R. W. Clough, H. C. Martin, and L. J. Topp, "Stiffness and deflection analysis of complex structures,’ Journal of the Aeronautical Sciences, vol. 23 (1956), pp. 805-823.
1 8. John R. Brauer, What Every Engineer Should Know about Finite Element Analysis (New York: Marcel Dekker, 1993), pp. 2-3; Edward R. Champion, Jr., and J. Michael Ensminger, Finite Element Analysis with Personal Computers (New York: Marcel Dekker, Inc., 1988), p. 1.
[804] Thomas J. Butler, "Operating in the Age of NASTRAN," p. 1.
[805] Anita S. West and William F. Hubka, "Matrix Methods and Automation in Structural Engineering," NASA CR-71230 (1966), p. 12.
[806] Butler, "Operating in the Age of NASTRAN," p. 2.
[807] C. Thomas Modlin, Jr., e-mail message to author, Apr. 23, 2009.
[808] Caleb W. McCormick, The NASTRAN Users’ Manual, NASA SP-222 (1970), p. i.
[809] Butler, "Age of NASTRAN," p. 2.
[810] "Matrix Methods in Structural Mechanics,’ Air Force Flight Dynamics Laboratory, Wright-Patterson Air Force Base, OH, (proceedings published Nov. 1966, conference date unknown); abstract on Defense Technical Information Center Web site at http://oai. dtic. mil/oai/oai? verb=getRecord& metadataPrefix=html&identifier=AD0646300, accessed May 25, 2009.
[811] Butler, "Age of NASTRAN,’ pp. 3-4.
[812] McCormick, The NASTRAN Users’ Manual, p. iii; Butler, "Age of NASTRAN," pp.
4-6; Butler also lists many more members and describes their contributions. At time of writing, document is available in the Tenth NASTRAN Users’ Colloquium, NASA CP-2249, on the NASA Technical Reports Server at http://ntrs. nasa. gov/archive/nasa/casi. ntrs. nasa. gov/198.300.04182_198.300.4182.pdf, accessed Aug. 13, 2009.
[813] J. P. Raney, DJ. Weidman, and H. M. Adelman, "NASTRAN: Status, Maintenance, and Future Development," in First NASTRAN Users’ Colloquium, NASA Langley Research Center (1971), p. 1.
[814] McCormick, NASTRAN Users Manual, pp. iii-iv.
[815] Butler, "Age of NASTRAN," p. 7.
[816] Ibid., pp. 2-3.
[817] Raney, Weidman, and Adelman, 1 971, in First NASTRAN Users’ Colloquium, p. 1.
[818] Ibid., p. 2.
[819] Foreword to the First User’s Colloquium, 1971.
[820] McCormick, The NASTRAN User’s Manual, pp. vii-viii.
[821] Raney, Weidman, and Adelman, "NASTRAN: Status, Maintence, and Future Development,’ in First NASTRAN Users’ Colloquium, NASA Langley Research Center (1971).
[822] Ibid.
[823] 5th NASTRAN Users’ Colloquium, 1976, pp. 331-352; 8th, 1979, pp. 1 1-32; 9th, 1980, pp. 201-223; I 1th, 1983, pp. 226-248; and 13th, 1985, pp. 320-340.
[824] "Aircraft Design Analysis,’ in Spinoff, NASA, 1979, p. 63.
[825] 15th NASTRAN Users’ Colloquium, 1987, pp. 166-183.
41 . Rainey and Weidman, "NASTRAN: A Progress Report,’ 2nd NASTRAN Users’ Colloquium (1972), p. 1.
[827] 2nd NASTRAN Users’ Colloquium, p. 421.
[828] Additional information is provided in the appendixes.
[829] Harry G. Schaefer, "Implementation of Mixed Formulation Elements in PC/NASTRAN," in 21st NASTRAN Users’ Colloquium (1992), pp. 1-7.
[830] J. P. Giesing, T. P. Kalman, and W. P. Rodden, "Correction Factor Techniques for Improving Aerodynamic Prediction Methods," NASA CR-144967 (1976).
[831] Interview of Thomas Christy and John Splichal (aircraft industry) by author, Wichita, KS, May 12, 2009.
[832] "MSC Software Highlights’ on MSC Web site at http://www. mscsoftware. com/about/ history. cfm? Q=135&Z=339&Y=346, accessed Feb. 12, 2009.
[833] 14th User Colloquium, 1986, p. 1.
[834] Butler, "Age of NASTRAN,” p. 7.
[835] Ibid., p. 8.
51 . "Stresses and Strains,’ Spinoff, 1998.
[837] Federal Trade Commission news release, "MSC Software Settles FTC Charges by Divesting Nastran [s/c] Software,’ Aug. 14, 2002, at http://www. ftc. gov/opa/2002/08/mscsoftware. shtm, accessed May 14, 2009.
[838] John P. Gyekenyesi, "SCARE: A Post-Processor Program to MSC/NASTRAN,’ abstract from NASA Technical Reports Server at http://ntrs. nasa. gov; Karen F. Bartos and Michael A. Ernst, "Evaluation
of MARC for the Analysis of Rotating Composite Blades,’ NASA TM-4423 (1993), p. 1; and Jim Loughlin, "FEM and Multiphysics Applications at NASA/GSFC,’ NASA Goddard Space Flight Center, in 2004 ANSYS Conference, May 24, 2004, Greenbelt, MD; view graph presentation on NASA Technical Report Server at http://ntrs. nasa. gov, accessed May 1 2, 2009.
[839] F. Douglas Johnson and Martin Kokus, "NASA Technology Utilization Program: A Summary of Cost Benefit Studies,’ NASA CR-201936 (1977), pp. i, 3. See also Johnson, Emily Miller, Nancy Gunderson, Panayes Gatseos, Charles F. Mourning, Thomas Basinger, and Kokus, "NASA Tech Brief Program: A Cost Benefit Evaluation,’ NASA CR-201938 (1977); and Spinoff, 1991, pp. 1 32-143.
[840] Joseph M. Carlson, "NASA Technology Transfer: The Computer Software Dissemination Program,’ in NASTRAN: Users’ Experiences, Langley Research Center (1971), pp. 551-552.
[841] Computer Software Management and Information Center (COSMIC), A Directory of Computer Programs Available from COSMIC, vol. 1, (Athens, GA: University of Georgia, 1967).
[842] Carlson, "NASA Technology Transfer,’ pp. 551-552.
[843] COSMIC, "COSMIC: 1981 Catalog of Computer Programs,’ NASA CR-163916 (1981), abstract, on NASA Technical Reports Server at http://ntrs. nasa. gov, accessed Mar. 16, 2009.
[844] COSMIC, "Monthly Progress Report,’ NASA CR-195809 (1994), pp. 1-3; Innovation, vol. 1, no. 6 (Nov./Dec. 1993), at http://ipp. nasa. gov/innovation/Innovationl6/ SoftwareWarehouse. html, accessed Feb. 1 1, 2009.
[845] COSMIC, A Directory of Computer Programs Available from COSMIC, vol. 1 (Athens, GA: University of Georgia, 1967).
61 . Johnson and Kokus, "Summary of Cost-Benefit Studies.’
[847] Open Channel Foundation, "About the Open Channel Foundation and Open Channel Software’ at http://www. openchannelfoundation. org, accessed Feb. 10, 2009; "NTTC and Open Channel Software Launch NASA Software Applications Collection as Space Agency Celebrates Birthday,’ Oct. 1 0, 2001; "Open Channel Publishes the NASA COSMIC Collection,’ at http:// www. openchannelfoundation. org/cosmic, Open Channel Foundation, accessed Feb. 12, 2009. A list of NASA-developed programs for finite element analysis is reported in Appendix D. As of this writing, the programs and related tasks are available through the Open Channel Foundation Web site. All except GEOFEST were originally released through COSMIC.
[848] Interview of Chittur Venkatasubban by author, Wichita, KS, May 1 4, 2009.
[849] Jennifer Ross-Nazzal, e-mail to author, Apr. 10, 2009; NASA, 9th NASTRAN Users’ Colloquium; Two Centers are not discussed in great detail because they undertake little work in computational structural analysis: the Kennedy Space Center and the Stennis Space Center. With responsibility for spacecraft launch operations, vehicle preparation, and integration, Kennedy maintains a minimal structural engineering staff, which is concerned primarily with supporting the Center’s launch equipment. Thus, this Center is not active in structural analysis methods research and development, though it did host the 9th NASTRAN Users’ Colloquium. The primary mission of Stennis is to test a very specific type of hardware, namely the ground-testing of rocket engines. More recently, it has added research in remote sensing. But with the exception of a small number of studies related to the operation of the Center’s own test equipment, the Stennis Space Center’s involvement in research and development in computational methods
is minimal. For more information, see John D. Anderson, Jr., "NASA and the Evolution of Computational Fluid Dynamics,’ a companion essay in this volume.
[850] For more information, see Anderson, "NASA and the Evolution of Computational Fluid Dynamics.’
[851] Interview of John Gallman by author, Wichita, KS, Apr. 4, 2009.
[852] Paul F. Borchers, James A. Franklin, and Jay W. Fletcher, Flight Research at Ames: Fifty-Seven Years of Development and Validation of Aeronautical Technology, 1940-1997, NASA SP-3300 (Washington, DC: NASA, 1998), p. 67.
[853] Wayne Johnson, "A Comprehensive Analytical Model of Rotorcraft Aerodynamics and Dynamics, Part III: Program Manual," NASA TM-81 1 84/AVRADCOM TR-80-A-7, Ames Research Center and U. S. Army Aviation Research and Development Command, June 1980, p. vii.
[854] F. K. Straub, K. B. Sangha, and B. Panda, "Advance finite element modeling of rotor blade aeroelasticity," American Helicopter Society Journal, vol. 39, no. 2 (Apr. 1994), pp. 56-68.
[855] A. Stewart Hopkins and Peter Likins, "Analysis of structures with rotating, flexible substructures," AIAA Paper 87-0951 (1987); D. H. Hodges, A. S. Hopkins, D. L. Kunz, and H. E. Hinnant, "Introduction to GRASP: General Rotorcraft Aeromechanical Stability Program—A Modern Approach to Rotorcraft Modeling," 42nd American Helicopter Society, Washington, DC (1986).
71 . Garret N. Vanderplaats, CONMIN: A FORTRAN Program for Constrained Function Minimization, Users Manual, (Moffett Field, CA: Ames Research Center and U. S. Army Air Mobility R&D Laboratory, 1973).
[857] Ashish K. Sareen, Daniel P. Schrage, and T. S. Murthy, "Rotorcraft Airframe Structural Optimization for Combined Vibration and Fatigue Constraints,’ 47th American Helicopter Society (AHSj Forum, Phoenix, AZ (1991).
[858] "Aircraft Design Software,’ Spinoff, 1997, p. 107; Phoenix Integration, "About Phoenix,’ on Phoenix Integration Web site at http://www. phcenix-int. com/about/company_profile. php, accessed May 11, 2009.
[859] G. P. Guruswamy, "ENSAERO: A multidisciplinary Program for Fluid/Structural Interaction Studies of Aerospace Vehicles,’ Computing Systems in Engineering, vol. 1, nos. 2-4 (1990), pp. 237-256.
[860] Manoj K. Bhardwaj, "Aeroelastic Analysis of Modern Complex Wings Using ENSAERO and NASTRAN,’ Progress Report, Virginia Polytechnic Institute and State University (1995); and Rakesh K. Kapania, Bhardwaj, Eric Reichenbach, and Guruswamy, "Aeroelastic Analysis of Modern Complex Wings,’ AIAA-96-401 1 (1996).
[861] Author’s experience.
[862] Richard P. Hallion and Michael H. Gorn, On the Frontier: Experimental Flight at NASA Dryden (Washington, DC: Smithsonian Books, 2002), pp. 344-354.
[863] Martin Brenner, e-mail message to author, May 8, 2009.
[864] W. L. Ko, R. D. Quinn, L. Gong, L. S. Schuster, and D. Gonzales, "Reentry Heat Transfer Analysis of the Space Shuttle Orbiter,’ in Howard B. Adelman, ed., NASA Langley Research Center Computational Aspects of Heat Transfer in Structures, NASA CP-2216 (1981), pp. 295-325.
[865] K. K. Gupta, "STARS—A General-Purpose Finite Element Computer Program for Analysis of Engineering Structures," NASA RP-1 1 29 (1984); Gupta, M. J. Brenner, and L. S. Voelker, "Development of an Integrated Aeroservoelastic Analysis Program and Correlation With Test Data," NASA TP-31 20 (1991); and Brenner, e-mail message to author, May 8, 2009.
81 . Interview of Charles Blankenship by author, Mar. 26, 2009.
[867] Search of NASA Technical Reports Server at http://ntrs. nasa. gov, Apr. 20, 2009.
[868] Nancy P. Sykes, ed., NASA Workshop on Computational Structural Mechanics, NASA CP – 10012 (1989).
[869] Open Channel Foundation, "AIRLOADS,’ on Open Channel Foundation Web site at http:// www. openchannelfoundation. org/projects/AIRLOADS, accessed May 6, 2009.
[870] "Auto Design," Spinoff, NASA, 1986, p. 72.
[871] Gary L. Farley and Donald J. Baker, "Graphics and Composite Material Computer Program Enhancements for SPAR," NASA TM-80209 (1980); and J. L. Rogers, Jr., "Programming Structural Synthesis System," NASA Tech Briefs, vol. 10, no. 2 (May 1986).
[872] Anees Ahmad and Lamar Hawkins, "Development of Software to Model AXAF-1 Image Quality," NASA CR-203978 (1996), p. 1.
[873] Cody R. Godines and Randall D. Manteufel, "Probabilistic Analysis and Density Parameter Estimation Within Nessus," NASA CR-2002-212008 (2002).
[874] "Structural Analysis Made NESSUSary," Spinoff, NASA, 2005, p. 94.
[875] John P. Gyekenyesi, "SCARE: A Post-Processor Program to MSC/NASTRAN," abstract from NASA Technical Reports Server at http://ntrs. nasa. gov.
[876] N. N. Nemeth, et al., "Ceramics Analysis and Reliability," NASA TP-2916 (1990) pp. 1-3.
[877] Nemeth, Lynn M. Powers, L. A. Janosik, and J. P. Gyekenyesi, "Lifetime reliability evaluation of structural ceramic parts with the CARES/LIFE computer program," in 34th AIAAjASME)ASCE/AHS/ ASC Structures, Structural Dynamics, and Materials Conference, CA, Apr. 19-22, 1993; abstract from NASA Technical Reports Server at http://ntrs. nasa. gov.
[878] Stephen F. Duffy and John P. Gyekenyesi, "CCARES: A computer algorithm for the reliability analysis of laminated CMC components," NASA TM-1 1 1096 (1993).
[879] Nemeth, "CARES: Ceramics Analysis and Reliability Evaluation of Structures," NASA Lewis Research Center Report LEW-15168 (1994).
[880] Research & Technology, NASA Lewis Research Center, Cleveland, OH, 1996, p. 100.
[881] P. L.N. Murthy and C. C. Chamis, "ICAN: Integrated Composites Analyzer,’ 25th Structures, Structural Dynamics and Materials Conference, Palm Springs, CA (1 984).
[882] NASA Technical Reports Server at http://ntrs. nasa. gov, accessed May 14, 2009.
[883] Research & Technology, p. 76.
[884] "A ‘Tread’ Ahead of the Competition,’ Spinoff, NASA, 2002, pp. 72-73.
[885] J. B. Mason, "The NASTRAN Hydroelastic Analyzer," NASA TM-X-65617 (1972); R. H. Mac – Neal, R. L. Harder, and Mason, "NASTRAN Cyclic Symmetry Capability," Goddard Space Flight Center, Sept. 1973, abstract on NASA Technical Reports Server at http://ntrs. nasa. gov, accessed Apr. 20, 2009; and W. R. Case, "Dynamic Substructure Analysis of the International Ultraviolet Explorer (IUE) Spacecraft," Goddard Space Flight Center, Sept. 1973, abstract on NASA Technical Reports Server at http://ntrs. nasa. gov, accessed Apr. 20, 2009.
[886] H. Lee and J. B. Mason, "NASTRAN Thermal Analyzer: A General Purpose Finite Element Heat Transfer Computer Program,’ in NASA Langley Research Center, 2nd NASTRAN Users’ Colloquium (1972), p. 444.
[887] Ibid., p. 445.
[888] Ibid., p. 449.
[889] E. F. Puccinelli, "View Factor Computer Program (Program VIEW) User’s Manual,’ Goddard Space Flight Center, July 1973, abstract on NASA Technical Reports Server at http://ntrs. nasa. gov, accessed Apr. 20, 2009.
[890] JPL Annual Reports at http://www. jpl. nasa. gov/about/reports. cfm, accessed Apr. 25, 2009.
[891] Jet Propulsion Laboratory, "NASA Facts: Jet Propulsion Laboratory,’ NASA, http://www. jpl. nasa. gov/news/fact_sheets/jpl. pdf, accessed Aug. 13, 2009.
[892] R. Levy and S. Wall, "Savings in NASTRAN Decomposition Time by Sequencing to Reduce Active Columns,’ in NASA Langley Research Center, NASTRAN: Users’ Experiences (1971), pp. 627-631.
[893] Search of NASA Technical Reports Server at http://ntrs. nasa. gov, Apr. 22, 2009.
[894] F. A. Akyuz and E. Heer, VISCEL Computer Program User Manual for Analysis of Linear Viscoelastic Structures, vol. 1: Users’ Manual, (Pasadena: NASA Jet Propulsion Laboratory, 1971).
1 1 0. NASA Scientific and Technical Information, "Computer Technology for Industry,’ Spinoff Database at http://www. sti. nasa. gov/spinoff/database, accessed April 25, 2009.
[896] NASA Scientific and Technical Information, "Auxiliary Power Units,’ Spinoff Database.
[897] Eric B. Becker and Trent Miller, "Final Report: Development of Non-Linear Finite Element Computer Code," NASA CR-179965 (1985).
1 1 3. James L. Beck, "Probabilistic System Identification in the Time Domain," in USAF-NASA, USAF/ NASA Workshop of Model Determination for Large Space Systems (Pasadena: California Institute of Technology, 1988), abstract from NASA Technical Reports Server at http://ntrs. nasa. gov, accessed Apr. 24, 2009, notes: "Areas of application for system identification include the following: (1) Model Evaluation. . . (2) Model Improvement. . . (3) Empirical Modeling [using experimental data in the initial development of a model, when existing methods or information about the system are not sufficient]; and (4) Damage Detection and Assessment-continual or episodic updating of a structural model through vibration monitoring to detect and locate any structural damage."
1 14. Beck, "Probabilistic System Identification."
[900] Y. Yam, "AU-FREDI—Autonomous Frequency Domain Identification,’ JPL, 1994, abstract from NASA Technical Reports Server at http://ntrs. nasa. gov, accessed Apr. 25, 2009.
1 16. According to Modlin, who was the Johnson representative on the Ad Hoc Group for Structural Analysis leading up to the development of NASTRAN, in an e-mail message to author, Apr. 23, 2009.
1 17. Ross-Nazzal, e-mail to author, Apr. 7, 2009.
[903] Interview of Aleck C. Bond by Rebecca Wright (No. 3), Houston, TX, July 1 5, 1999, in JSC Oral Histories project at http://www. jsc. nasa. gov/history/oral_histories/oral_histories. htm, accessed Apr. 25, 2009.
1 1 9. Modlin, e-mail message to author, Apr. 23, 2009; and Ross-Nazzal, e-mail message to author, Apr. 7, 2009.
1 20. Modlin, e-mail message to author, Apr. 23, 2009.
[906] Shivakumar Mettu, et al, "NASGRO 3.0—A Software for Analyzing Aging Aircraft,’ in NASA-FAA-DOD, 2nd Joint NASA/FAA/DoD Conference on Aging Aircraft, pt. 2, (Washington, DC: NASA-FAA-DOD, 1999), pp. 792-801.
1 22. Search of NASA Technical Reports Server at http://ntrs. nasa. gov, Apr. 20, 2009.
1 23. WJ. Stroud, (NASA Langley, retired), e-mail message to author, Mar. 29, 2009.
1 24. Kay S. Bales, "Structural Mechanics Division Research and Technology Plans for FY 1989 and Accomplishments for FY 1988," NASA TM-101592 (1989).
1 25. Eleanor C. Wynne, "Structural Dynamics Division Research and Technology Accomplishments for FY 1990 and Plans for FY 1991," NASA TM-102770 (1991), p. 1.
1 26. Raymond G. Kvaternik, "The NASA/Industry Design Analysis Methods for Vibration (DAMVIBS) Program—A Government Overview,’ in Kvaternik, ed., A Government/Industry Summary of the Design Analysis Methods for Vibrations (DAMVIBS) Program, NASA CP-101 14 (1993), p. 9.
1 27. R. Gabel, P. Lang, and D. Reed, "The NASA/Industry Design Analysis Methods for Vibration (DAMVIBS) Program—Boeing Helicopters Airframe Finite Element Modeling,’ in Kvaternik, ed., A Gov ernment/Industry Summary of the Design Analysis Methods for Vibrations (DAMVIBSj Program, NASA CP-101 14 (1993), p. 23.
[913] For example, from Bell: "Structural optimization was found to be a useful tool and Bell is continuing with development of this methodology and integrating it into the design process to efficiently achieve minimum weight and vibration levels in future designs. The work that was accomplished under the NASA DAMVIBS program has had a major influence on the ‘hardening’ and growth of vibration technology in the helicopter industry. . . . ‘ From Sikorsky: "Prior to the DAMVIBS program, attempts to reduce [vibration] were usually limited to making modifications or adding vibration-control devices to an already designed and built airframe, in a trial-and-error fashion.’ The Sikorsky team noted that DAMVIBS-funded work had "brought for the first time the introduction of low-vibration design into the design cycle at Sikorsky.’ See James D. Cronkhite, "The NASA/Industry Design Analysis Methods for Vibration (DAMVIBS) Program—Bell Helicopter Textron Accomplishments,’ in Kvaternik, ed., A Government/Industry Summary of the Design Analysis Methods for Vibrations (DAMVIBSj Program, NASA CP-101 14 (1993), pp. 11, 22; and William J. Twomey, "The NASA/Industry Design Analysis Methods for Vibration (DAMVIBS) Program—Sikorsky Aircraft—Advances Toward Interacting with the Airframe Design Process,’ in Kvaternik, ed., A Government/Industry Summary of the Design Analysis Methods for Vibrations (DAMVIBSj Program, NASA CP-101 14 (1993), p. 47.
[914] Gabel, Lang, and Reed, "DAMVIBS—Boeing,’ p. 33. 130. Ibid., p. 33-34.
[915] Ibid., p. 33-34.
[916] Mostafa Toossi, Richard Weisenburger, and Mostafa Hashemi-Kia, "The NASA/Industry Design Analysis Methods for Vibration (DAMVIBS) Program—McDonnell Douglas Helicopter Company Achievements,’ in Kvaternik, ed., A Government/Industry Summary of the Design Analysis Methods for Vibrations (DAMVIBS) Program, NASA CP-101 14 (1993), p. 44.
1 32. Twomey, "DAMVIBS—Sikorsky," p. 47.
[918] Ibid., p. 47.
[919] Ibid., p. 52.
1 35. William T. Yeager, Jr., "A Historical Overview of Aeroelasticity Branch and Transonic Dynamics Tunnel Contributions to Rotorcraft Technology and Development," NASA TM-2001-21 1054 (2001), p. 38
1 36. Kvaternik, "The NASA/Industry Design Analysis Methods for Vibrations (DAMVIBS) Program: Accomplishments and Contributions," NASA TM-104192 (1991), p. 13.
1 37. WJ. Stroud, (NASA Langley, retired), e-mail message to author, Mar. 28, 2009.
1 38. Victor W. Sparrow and Ralph D. Buehrle, "Fuzzy Structures Analysis of Aircraft Panels in NASTRAN," AIAA Paper 2001-1 320 (2001).
1 39. Jaroslaw Sobieszczanski-Sobieski, "An Integrated Computer Procedure for Sizing Composite Airframe Structures," NASA TP-1 300 (1979).
[925] L. Bernard Garrett, "Interactive Modeling, Design and Analysis of Large Spacecraft,’ NASA Langley Research Center (1982), on NASA Technical Reports Server at http://ntrs. nasa. gov, accessed Apr. 4, 2009.
[926] J. L. Rogers, Jr., J. Sobieszczanski-Sobieski, and R. B. Bhat, "Structural Optimization,’ Tech Briefs, vol. 7, no. 2, p. 1 84, May 1 983; abstract on NASA Technical Reports Server at http:// ntrs. nasa. gov, accessed Apr. 4, 2009.
[927] Rogers, "NETS/PROSSS—Nets Coupled with the Programming System for Structural Synthesis,’ LAR-1481 8, Langley Research Center; abstract on NASA Technical Reports Server at http://ntrs. nasa. gov, accessed Apr. 4, 2009; and J. L. Rogers, Jr., "System for Structural Synthesis Combines Finite – Element Analysis and Optimization Programs,’ NASA Tech Briefs, vol. 8, no. 2 (Nov. 1984), p. 242.
[928] "Structural Analysis and Design Software,’ Spinoff, NASA, 1997, p. 96.
[929] "Efficient, Multi-Scale Design Takes Flight,’ Spinoff, NASA, 2003, pp. 68-69.
[930] Search of NASA Technical Reports Server at http://ntrs. nasa. gov, Apr. 20, 2009.
[931] Andrew J. Dunar and Stephen P. Waring, Power to Explore: A History of the Marshall Space Flight Center, 1960-1990, NASA SP-431 3 (Washington, DC: NASA, 1999), pp. 44-50.
[932] J. B. Graham and P. L. Luz, "Preliminary In-Flight Loads Analysis of In-Line Launch Vehicles Using the VLOADS 1.4 Program," NASA TM-1998-208472 (1998).
[933] C. Chamis, "CELFE/NASTRAN code for the analysis of structures subjected to high velocity impact," NASA TM-79048 (1978); abstract on NASA Technical Report Server at http://ntrs. nasa. gov, accessed Apr. 26, 2009.
[934] Neil Otte, "PATRAN-STAGS Translator (PATSTAGS)," NASA TM-100388 (1990).
[935] Southwest Research Institute, "NESSUS/NASTRAN Interface," NASA CR-202778 (1996).
[936] NASA DFRC Fact Sheet: YF-1 2A, at http://www. nasa. gov/centers/dryden/news/ FactSheets, accessed Aug. 1 3, 2009. For a detailed examination of this program, see a companion essay by William Flanagan.
[937] Hallion and Gorn, On the Frontier, pp. 423-426.
[938] James A. Albers, in James and Associates, eds., YF-12 Experiments Symposium, vol. 1, NASA CP-2054 (1978), p. 25.
[939] Peter W. Merlin, Mach 3+: NASA/USAF YF-12 Fiight Research, 1969-1979, NASA SP- 2001-4525, No. 25 in the Monographs in Aerospace History series (Washington, DC: NASA, 2002), pp. 8, 95.
[940] Quoted in Merlin, Mach 3+, p. 90.
[941] Jerald M. Jenkins and Albert E. Kuhl, "Recent Load Calibrations Experience with the YF 1 2 Airplane,’ in James and Associates, eds., YF-12 Experiments Symposium, vol. 1, NASA CP-2054 (1978), p. 49.
[942] Merlin, Mach 3+, p. 92; Hallion and Gorn, On the Frontier, pp. 1 88-1 89 and 423-424.
[943] Merlin, Mach 3+, p. 90.
[944] Robert R. Meyer, Jr., and V. Michael DeAngelis, "Flight-Measured Aerodynamic Loads on a 0.92 Aspect Ratio Lifting Surface,’ in James and Associates, eds., YF-12 Experiments Symposium, vol. 1, NASA CP-2054 (1978), p. 77.
[945] Merlin, Mach 3+, p. 42.
[946] James and Associates, eds., YF-12 Experiments Symposium, vol. 1, NASA CP-2054 (1978).
[947] Merlin, Mach 3+, pp. 93-94.
[948] Borchers, et al., Flight Research at Ames, p. 71.
[949] Hallion and Gorn, On The Frontier, pp. 276-278.
[950] Richard C. Monaghan, "Description of the HiMAT Tailored Composite Structure and Laboratory Measured Vehicle Shape Under Load," NASA TM-81 354 (1981), pp. 4-5, 7.
[951] Walter J. Sefic and Karl F. Anderson, "NASA High Temperature Loads Calibration Laboratory,’ NASA TM-X-1 868 (1969), pp. 3-4.
[952] Glenn B. Gilyard, "The Oblique Wing Research Aircraft: A Test Bed for Unsteady Aerodynamic and Aeroelastic Research,’ in NASA Langley Research Center, Transonic Unsteady Aerodynamics and Aeroelasticity, pt. 2, Report N89-19247 (1987), p. 41 2; JJ. Burken, G. S. Alag, and G. B. Gilyard, "Aeroelastic Control of Oblique-Wing Aircraft,’ NASA TM-86808 (1986).
[953] Robert E. Curry and Alex G. Sim, "In-Flight Total Forces, Moments, and Static Aeroelastic Characteristics of an Oblique-Wing Research Airplane,’ NASA TP-2224 (1984), p. 1 5.
[954] Jones continued to study it and advocate it until his death in 1999; the author had the pleasure of hearing him lecture on this topic in the aerodynamics class that Jones taught at Stanford University in the 1980s. For Jones, see statement of William Sears in Ames Research Center staff, "Collected Works of Robert T. Jones,’ NASA TM-X-3334 (1976), pp. vii-ix; Hallion, "Lippisch Gluhareff, and Jones: The Emergence of the Delta Planform and the Origins of the Sweptwing in the United States,’ Aerospace Historian, vol. 26, No. 1 (Mar. 1979), pp. 1-10; and Walter G. Vincenti, "Robert Thomas Jones,’ in Biographical Memoirs, vol. 86 (Washington, DC: National Academy of Sciences, 2005), pp. 3-21.
[955] Steve Smith, interview with author, Apr. 6, 2009; and M. J. Rutkowski, "Aeroelastic stability analysis of the AD-1 Manned Oblique-Wing Aircraft," NASA TM-78439 (1977).
[956] Curry and Sim, "In-Flight Total Forces," p. 3.
[957] Ibid., pp. 3-4.
[958] Ibid., pp. 3-4, 10.
[959] Smith, interview with author.
[960] Curry and Sim, "In-Flight Total Forces,’ pp. 7-8.
[961] Gilyard, "The Oblique Wing Research Aircraft.
[962] Mendoza and Hazen, interview with author.
[963] Sefic and Maxwell, "X-29A Overview,’ p. 2.
[964] Philip Mason, Edward Lerner, and Lawrence Sobel, "Applications of Integrated Design/Analy – sis Systems in Aerospace Structural Design,’ in NASA Langley Research Center, Recent Advances in Multidisciplinary Analysis and Optimization, pt. 1 (1989), p. 25.
[965] Ibid., p. 26.
[966] Sefic and Maxwell, "X-29A Overview,’ p. 3.
[967] Ibid., pp. 3-4.
[968] Ibid., p. 4.
1 84. Quoted in Dryden Flight Research Center "Fact Sheets: X-29," http://www. nasa. gov/ centers/dryden/news/FactSheets, accessed Mar. 19, 2009.
1 85. David F. Voracek and Robert Clarke, "Buffet Induced Structural/Flight Control System Interaction of the X 29A Aircraft," AIAA Paper 91-1053 (1991); and Michael W. Kehoe, Lisa J. Bjarke, and Edward J. Laurie, "An In-Flight Interaction of the X 29A Canard and Flight Control System," NASA TM-10171 8 (1990).
1 86. K. K. Gupta, M. J. Brenner, and L. S. Volker, "Integrated Aeroservoelastic Analysis Capability With X 29A Analytical Comparisons," AIAA Paper 87-0907 (1987).
1 87. Thomas Christy and John Splichal (aircraft industry), interview by author, Wichita, KS, May 1 2, 2009; Jadic interview.
[973] Butler, "Operating in the Age of NASTRAN,’ p. xx.
[974] Mendoza, Hazen, Jadic, and Christy-Splichal interviews by author.
[975] Jadic interview; and author’s experience.
[976] A. R. Dusto, et al., A Method for Predicting the Stability Characteristics of an Elastic Airplane, vol. 1: FLEXSTAB Theoretical Description, NASA CR-1 1471 2 (1974), p. xxi.
[977] R. L. Sims, "User’s Manual for FSLIP-3, FLEXSTAB Loads Integration Program," NASA TM – 81364 (1981), p. 1.
[978] Lawrence S. Schuster, "NASTRAN /FLEXSTAB Procedure for Static Aeroelastic Analysis," NASA TM-84897 (1984).
[979] R. D. Miller, R. I. Kroll, and R. E. Clemmons, Dynamic Loads Analysis System /DYLOFLEX) Summary, vol. 1: Engineering Formulation, NASA CR-2846-1 (1979).
[980] Albert Kaufman, "Simplified Method for Nonlinear Structural Analysis,’ NASA TP-2208 (1983), p. 2.
[981] K. W. Brown, M. S. Hirschbein, and C. C. Chamis, "Finite Element Engine Blade Structural Optimization," AIAA Paper 85-0645 (1985).
[982] R. L. Thompson and R. J. Maffeo, "A Computer Analysis Program for Interfacing Thermal and Structural Codes," NASA TM-87021 (1985).
[983] Frank F. Monasa and Joseph M. Roche, "Collapse Analysis of a Waffle Plate Strongback for Space Station Freedom," NASA TM-10541 2 (1992).
[984] Karen F. Bartos and Michael A. Ernst, "Evaluation of MARC for the Analysis of Rotating Composite Blades," NASA TM-4423 (1993), p. 1.
[985] E. S. Reddy and G. H. Abumeri, "Blade Assessment for Ice Impact (BLASIM), User’s Manual, Version 1.0," NASA CR-19075 (1993), pp.1.1-1.2.
[986] G. H. Abumeri, E. S. Reddy, P. L.N. Murthy, and C. C. Chamis, "Dynamic Analysis of a Pre-and – Post Ice Impacted Blade," NASA TM-105829 (1992).
[987] G. K. Jones and KJ. McEntire, "NPLOT: An Interactive Plotting Program for NASTRAN Finite Element Models," in NASA, 13th NASTRAN Users’ Colloquium (1985), pp. 1 10-1 32;
K. McEntire, "NPLOT—NASTRAN Plot," program abstract, Jan. 1994, on NASA Technical Reports Server at http://ntrs. nasa. gov, accessed Apr. 20, 2009.
[988] Gregory Moore, "Integrated Modeling of Optical Systems (IMOS): An Assessment and Future Directions,’ Goddard Space Flight Center and Jet Propulsion Laboratory, in FEMCI Workshop 2001, abstract on NASA Technical Reports Server at http://ntrs. nasa. gov, accessed Apr. 20, 2009.
[989] Harold P. Frisch, "DISCOS-Dynamic Interaction Simulation of Controls and Structures (IBM Version),’ Computer Program abstract, Goddard Space Flight Center, Jan. 1994, on NASA Technical Reports Server at http://ntrs. nasa. gov, accessed Apr. 20, 2009.
[990] Frisch, "NASDS-NASTRAN/DISCOS/SAMSAN DMAP Bridging Program,’ Computer Program abstract, Goddard Space Flight Center, Jan. 1 994, on NASA Technical Reports Server at http://ntrs. nasa. gov, accessed Apr. 20, 2009.
[991] D. W. Lips, "Approaches and Possible Improvements in the Area of Multibody Dynamics Modeling,’ NASA CR-179227 (1987).
[992] Frisch, "Control system software, simulation, and robotic applications,’ in NASA Goddard Space Flight Center, Technology 2000, vol. 1 (Washington, DC: NASA, 1991), pp. 315-321 .
[993] M. Smoot Katow, "Static Analysis of the 64-m (21 Oft) Antenna Reflector Structure,’ in NASA Langley Research Center, NASTRAN: Users’ Experiences (Hampton, VA, NASA, 1971), pp. 123-1 29.
[994] Roy Levy, "Computer-Aided Design of Antenna Structures and Components,’ JPL, in 2nd National Symposium on Computerized Structural Analysis and Design, Washington, DC (1976); abstract in NASA Technical Report Server at http://ntrs. nasa. gov, accessed Apr. 24, 2009.
21 0. Levy, "Structural Optimization and Recent Large Ground Antenna Installations,’ in NASA, Recent Advances in Multidisciplinary Analysis and Optimization, pt. 3 (Washington, DC: NASA, 1989), pp. 1393-1416.
[996] NASA Technical Reports Server at http://ntrs. nasa. gov, accessed Apr. 20, 2009.
21 2. James P. Smith, "BUCKY Instruction Manual Version 3.3,’ NASA TM-104793 (1994), p. 2.
21 3. Norman F. Knight, Jr., and Charles C. Rankin, "STAGS Example Problems Manual,’ NASA CR-2006-214281 (2006), p. 5; B. O. Almroth and A. M. Holmes, "An experimental study of the strength and stability of thin monocoque shells with reinforced and unreinforced rectangular cutouts,’ NASA CR-1 15267 (1971), abstract on NASA Technical Reports Server at http://ntrs. nasa. gov, accessed May 10, 2009.
[999] B. O. Almroth and FA Brogan, "The STAGS Computer Code,’ NASA CR-2950 (1978), pp. 1-2.
21 5. C. C. Rankin, P. Stehlin, and F. A. Brogan, "Enhancements to the STAGS Computer Code,’ NASA CR-4000 (1986), pp. 1, 3.
[1001] "Structural Analysis,’ Spinoff, NASA Technology Utilization Office, 1991, p. 57.
[1002] Knight and Rankin, "STAGS Example Problems Manual’; Donald J. Baker, "Response of Damaged and Undamaged Tailored Extension-Shear-Coupled Composite Panels,’ Journal of Aircraft, vol. 43, no. 2 (2008), pp. 517-527.
21 8. Search of NASA Technical Reports Server at http://ntrs. nasa. gov, accessed Apr. 20, 2009.
[1004] L. Dequay, A. Lusk, and S. Nunez, "Integrated flow and structural modeling for rocket engine component test facility propellant systems,’ AIAA Paper 91-2402 (1991).
[1005] Henry A. Cole, e-mail message to author, Apr. 19, 2009.
[1006] Glenn E. Bugos, e-mail to author, Apr. 3, 2009.
[1007] Smith interview by author (by telephone), Apr. 6, 2009.
[1008] Hallion and Gorn, On The Frontier, pp. 100, 358.
[1009] Sefic and Karl F. Anderson, "NASA High Temperature Loads Calibration Laboratory,’ NASA TM-X-1 868 (1969), p. 1.
[1010] "Fact Sheets: NASA Dryden’s Contributions to Spaceflight,’ http://www. nasa. gov/centers/ dryden/news/FactSheets, accessed Mar. 19, 2009.
[1011] Martin Brenner, e-mail message to author, May 8, 2009.
[1012] Gerald V. Brown, Robert E. Kielb, Erwin H. Meyn, Richard E. Morris, and Stephen J. Posta, "Lewis Research Center Spin Rig and Its Use in Vibration Analysis of Rotating Systems,’ NASA TP – 2304 (1984), p. 1.
[1013] Erik M. Conway, High-Speed Dreams (Baltimore: Johns Hopkins University Press, 2005), p. 57.
[1014] Richard A. DeMeis, "The Trisonic Titanium Republic,’ Air Enthusiast, No. 7, (July—Sept. 1978), pp. 198-21 3; Dale D. Myers, "The Navaho Cruise Missile: A Burst of Technology,’ Acta Astronau – tica, vol. 26 (Nov. 8-10, 1992), pp. 741-748.
[1015] David Robarge, Archangel: CIA’s Supersonic A-1 2 Reconnaissance Aircraft (McLean, VA: CIA Center for the Study of Intelligence, 2007), pp. 1 1-12; see also Paul F. Crickmore, Lockheed SR-71 Blackbird (London: Osprey Publishing Ltd., 1986), pp. 90-92.
[1016] "Evaluation Report on X-15 Research Aircraft Design Competition,’ Aug. 5, 1955, pp. 99-101, Record Group 255, Philadelphia Federal Records Center, National Archives and Records Service.
[1017] "Briefing: Rolls-Royce,’ The Economist (Jan. 10, 2009), pp. 60-62.
[1018] Willy Ley, Rockets, Missiles, and Space Travel (New York: Viking, 1957), p. 213.
[1019] Jay Miller, The X-Planes, X-1 to X-45 (North Branch, MN: Specialty Press, 2001). See also Lee L. Peterson, "Evaluation Report on X-7A," Report AFMDC ADJ 57-81 84, Oct. 3, 1957; and William A. Ritchie, "Evaluation Report on X-7A (System 601 B)," Report AFMDC DAS 58-81 29, Jan. 1959, copies in the Archives of the Air Force Historical Research Agency, Maxwell AFB, Montgomery, AL.
[1020] Author interview with Paul Czysz, Mar. 1 3, 1 986.
[1021] Time, June 1 3, 1960, p. 70; P. H. Rose and W. I. Stark, "Stagnation Point Heat-Transfer Measurements in Dissociated Air." Journal of the Aeronautical Sciences (Feb. 1958), pp. 86-97; P. H. Rose, "Physical Gas Dynamics Research at the Avco Research Lab," AGARD Report 145, July 1957, p. 1.
[1022] Richard E. Young, Martha A. Smith, and Charles K. Sobeck, "Galileo Probe: In Situ Observations of Jupiter’s Atmosphere,’ Science (May 10, 1996), pp. 837-838.
1 1 . James R. Hansen, Engineer in Charge: A History of the Langley Aeronautical Laboratory, 1917-1958, NASA SP-4305 (Washington: GPO, 1987), pp. 343-347.
1 2. Data from Matthew J. Donachie, Jr., Superalloys Source Book (Metals Park, OH: American Society for Metals, 1984), pp. 3-19.
[1025] Ibid., pp. 3-19.
[1026] Deborah D. L. Chung, Carbon Fiber Composites (Boston: Butterworth-Heinemann, 1994), pp. 5-10.
[1027] Paul R. Becker, "Leading-Edge Structural Material System of the Space Shuttle,’ American Ceramic Society Bulletin, vol. 60, No. 1 1 (1981), pp. 1210-1214; LJ. Korb, C. A. Morant, R. M. Calland, and C. S. Thatcher, "The Shuttle Orbiter Thermal Protection System,’ American Ceramic Society Bulletin, vol. 60 (1981), pp. 1188-1193; Anon., "Technical Overview: Oxidation Resistant Carbon-Carbon for the Space Shuttle,’ Vought Missiles and Space Company, n. d. (c. 1970).
[1028] NASA, Columbia Accident Investigation Report, (Washington, DC: GPO, 2003), p. 12.
1 8. Chung, Carbon Fiber Composites, pp. 1 16-1 1 8.
[1030] See George W. Sutton, "The Initial Development of Ablation Heat Protection, An Historical Survey,’ Journal of Spacecraft and Rockets, (Jan.-Feb. 1982), pp. 3-1 1; and H. Julian Allen and A. J. Eggers, Jr., "A Study of the Motion and Aerodynamic Heating of Ballistic Missiles Entering the Earth’s Atmosphere at High Supersonic Speeds,’ NACA TR-1 381 (1953), which summarizes his early research and that of Alfred J. Eggers.
[1031] C. E. Brown, WJ. O’Sullivan, and C. H. Zimmerman, "A Study of the Problems Related to High Speed, High Altitude Flight," NACA Langley, 1953; Jacob Neufeld, The Development of Ballistic Missiles in the United States Air Force, 1945-1960 (Washington: Office of Air Force History, 1990).
21 . Army Ballistic Missile Agency staff, Re-Entry Studies, vol. 1. (Redstone Arsenal, AL: ABMA,
Nov. 25, 1958), pp. 2, 24-25, 31, 37-45, 61; Sutton, "Initial Development of Ablation Heat Protection," pp. 3-11.
[1033] E. R. Riddell and J. D. Teare, "The Differences Between Satellite and Ballistic Missile Re-Entry Problems," in Morton Alperin and Hollingsworth F. Gregory, eds., Vistas in Astronautics, vol. 2 (New York: Pergamon Press, 1959,) pp. 174-190.
[1034] Leo Steg, "Materials for Re-Entry Heat Protection of Satellites,’ American Rocket Society Journal (Sept. 1960), pp. 815-822.
[1035] Time (Nov. 18, 1957), pp. 19-20; (Apr. 27, 1959), p. 16; Joel W. Powell, "Thor-Able and Atlas-Able,’ Journal of the British Interplanetary Society (May 1984), pp. 219-225; Kevin C. Ruffner, Corona: Americas First Satellite Program (McLean, VA: Central Intelligence Agency, 1995); see also T. A. Heppenheimer, "Toward Transatmospheric Flight,’ (in this volume) for additional details.
[1036] ASD staff, Proceedings of 1962 X-20A (Dyna-Soar) Symposium, vol. 3, Structures and Materials (Wright Patterson AFB: USAF Aeronautical Systems Division, 1963), DTIC AD-34691 2, pp. IN-3-1 -2 to -5, III-3-1-1 8 to -23, II-4-2-2 to -8. Re: Rene 41, see Howard J. Middendorf, "Materials and Processes for X-20A (Dyna-Soar),’ Air Force Systems Command, June 1 964, DTIC AD-449685, pp. 28, 41.
[1037] William Cowie, "Utilization of Refractory Metals on the X-20A (Dyna-Soar),’ Air Force Systems Command, June 1964, DTIC: AD-609169; AD-449685, pp. 3-5, 20; AD-346912, pp. III-3-1-7, III-4-1-2 to -3.
[1038] DTIC AD-34691 2, p. III-3-1 -8; Alvin Seiff and H. Julian Allen, "Some Aspects of the Design of Hypersonic Boost-Glide Aircraft,’ NACA RM-A55E26 (1955); and Clarence Geiger, "Strangled Infant: The X-20 Dyna-Soar,’ in Richard P. Hallion, ed., Hypersonic Revolution, vol. 1 (Bolling AFB: USAF, 1998).
[1039] DTIC: AD-609169; AD-4496845, pp. 3-5, 20; AD-34691 2, pp. III-3-1-7, III-4-1-2 -3.
[1040] DTIC: AD-34691 2, p. III-3-1-8; AD-449685, p. iii.
[1041] DTIC AD-34691 2, pp. 111-3-6-2 to -15 (quotes, pp. -8, -1 1); "Scientific Advisory Board Meme Report of the Aerospace Vehicles Panel on Dyna-Soar Panel Flutter,’ Apr. 20, 1962. See also Hep – penheimer, "Toward Transatmospheric Flight.’
[1042] DTIC: AD-449685, pp. 49-50; AD-609169, pp. 1 3, 29; AD-346912, pp. 43-1-6 to -7, IN-3-6-2, IN-3-6-1 3 to -14.
[1043] DTIC AD-346912, pp. III-3-1-8, III-3-4-4; "How Mercury Capsule Design Evolved," Aviation Week (Sept. 21, 1959), pp. 52-59.
[1044] DTIC AD-34691 2, pp. III-4-5-3 to -6, III-4-5-16.
[1045] Ibid., pp. III-4-5-1 3 to -1 8, III-4-5-35.
[1046] Ibid., pp. III-3-4-4 to -6, III-3-4-20.
[1047] Ibid., p. III-3-4-4; Geiger, "Strangled Infant,’ p. 357. See Heppenheimer, "Toward Transatmospheric Flight.’
[1048] DTIC AD-34691 2, pp. 111-4-6-5 to -7.
[1049] Ibid., pp. 3-1-10 to -12; Geiger, "Strangled Infant,’ pp. 361-368.
[1050] DTIC: AD-34691 2, pp. 111-4-6-9 to -11; AD-449685, pp. 63-65.
[1051] DTIC: AD-34691 2, pp. III-4-6-7 to -8; AD-449685, pp. 57-59.
[1052] DTIC AD-34691 2, pp. III-3-1-10 to -11; Dennis Jenkins, Space Shuttle (Stillwater, MN: Voya – geur Press, 2001).
[1053] DTIC AD-346912, pp. Ш-3-1-1 4 to -15; Geiger, "Strangled Infant," pp. 347-349, 360-361.
[1054] See Table 1 in Heppenheimer, "Toward Transatmospheric Flight," for specific advances by structural element. See also Terry L. Sunday and John R. London, "The X-20 Space Plane: Past Innovation, Future Vision," in John Becklake, ed., History of Rocketry and Astronautics, vol. 17 of the AAS History Series (San Diego: Univelt, 1995), pp. 253-284; Geiger, "Strangled Infant," pp. 344-346; R. L. Schleicher, "Structural Design of the X-1 5," Journal of the Royal Aeronautical Society (Oct. 1963), pp. 618-636.
[1055] Hallion, Hypersonic Revolution, vol. 1, p. II-xvi (intro to Geig
[1056] "Advanced Technology Program: Technical Development Plan for Aerothermodynamic/Elastic Structural System Environmental Tests (ASSET),’ Air Force Systems Command, Sept. 9, 1963.
[1057] Ibid., pp. 4, 11-1 3; Hallion, "ASSET,” in Hypersonic Revolution, vol. 1, pp. 451,464-465.
[1058] See Table 2 in Heppenheimer, "Toward Transatmospheric Flight,’ for a list of these flights and performance objectives.
[1059] Hallion, "ASSET,” pp. 510-512 (quote, p. 512).
[1060] Ibid., pp. 51 2-516 (quote, p. 515); "ASSET ASV-3 Flight Test Report," McDonnell Aircraft Corp., Jan. 4, 1965, DTIC AD-357523; advertisement, Aviation Week, May 24, 1965, p. 62.
[1061] "Fourth ASSET Glider Gathers Data," Aviation Week, Nov. 2, 1964, pp. 25-26; "ASSET ASV-4 Flight Test Report," McDonnell Aircraft Corp., June 25, 1965, DTIC AD-366546; Hallion, "ASSET," pp. 516-519.
[1062] . F. M. Anthony, R. R. Fisher, and R. G. Helenbrook, "Selection of Space Shuttle Thermal Protection Systems," AIAA Paper 71-443 (1971).
[1063] Wilson B. Schramm, Ronald P. Banas, and Y. Douglas Izu, "Space Shuttle Tile—The Early Lockheed Years,” Lockheed Horizons, No. 13, 1983, pp. 2-1 5.
[1064] Ibid.
[1065] Korb, et al., "The Shuttle Orbiter"; Wilson Schramm, "HRSI and LRSI—The Early Years," American Ceramic Society Bulletin, vol. 60 (1981), pp. 1194-1 195.
[1066] Korb, et al., "The Shuttle Orbiter"; NASA, NASA Space Shuttle Technology Conference, vol.
2, "Structures and Materials," NASA TM-X-2273 (1971); Richard C. Thuss, Harry G. Thibault, and Arnold Hiltz, "The Utilization of Silica Based Thermal Insulation for the Space Shuttle Thermal Protection System," CASI 72A-10764, Oct. 1971.
[1067] Schramm, et al., "Space Shuttle Tile’; Schramm, "HRSI.
[1068] CASI 72A-10764; NASA TM-X-2273, pp. 39-93.
[1069] "Space Shuttle Program Definition: Phase B Extension Final Report,’ Grumman B35-43 RP-33 (Mar. 15, 1972); North American Rockwell 1971 Reports SV 71-50 and SV 71-59 (1971); "Interim Report to OMSF: Phase B System Study Extension,’ McDonnell-Douglas report (Sept. 1, 1971), p. 36.
[1070] Heppenheimer, The Space Shuttle Decision, NASA SP-4221 (Washington, DC: NASA,
1999); Jenkins, Space Shuttle, pp. 141-150.
[1071] Heppenheimer, Turbulent Skies: The History of Commercial Aviation (New York: John Wiley,
1995); author interview with Max Faget, Mar. 4, 1997.
[1072] L. J. Korb and H. M. Clancy, "The Shuttle Thermal Protection System,’ CASI 81A-44344 (1981), pp. 232-249; Korb, et al., "The Shuttle Orbiter,’ p. 1 1 89.
[1073] John Mauer interview of Charles Donlan, Oct. 19, 1983, Oral History Series, Shuffle Interviews, Box 1, JSC History Collection, University of Houston-Clear Lake; author interview of Faget, Mar. 4, 1997.
[1074] CASI 81A-44344, Ref. 62.
[1075] "Sortie Module May Cut Experiment Cost," Aviation Week (Jan. 17, 1972), p. 17; North American Rockwell Report SV 72-19, 1972.
[1076] Schramm, et al., "Space Shuttle Tile," Ref. 53, pp. 1 1-14; William S. Hieronymus, "Two Reusable Materials Studied for Orbiter Thermal Protection," Aviation Week (Mar. 27, 1972), p. 48.
[1077] Heppenheimer, Development of the Space Shuttle, 1972-1981, (Washington: Smithsonian Institution Press, 2002); Jenkins, Space Shuttle.
[1078] NASA SP-4221, pp. 335-340, 348-349; Grumman Report B35-43 RP-33; Michael L. Yaffee, "Program Changes Boost Grumman Shuttle,’ Aviation Week (July 1 2, 1963), pp. 36-39.
[1079] "External LH2 Tank Study Final Report,’ McDonnell-Douglas Report MDC E076-1, June 30, 1971.
[1080] NASA SP-4221, pp. 420-422; Heppenheimer, Development, p. 1 88.
[1081] Miller, X-Planes, pp. 256-261; "SV-5D PRIME Final Flight Test Summary," Martin Marietta Report ER-14465, Sept. 1967; William J. Normyle, "Manned Flight Tests to Seek Lifting-Body Technology," Aviation Week (May 16, 1966), pp. 64-75; John L. Vitelli and Richard P. Hallion, "Project PRIME: Hypersonic Reentry from Space," in Hallion, ed., Hypersonic Revolution, vol. 1, pp. 641,648-649.
[1082] . Martin Marietta Report ER-1 4465, p. I-1; Vitelli and Hallion, "Project PRIME," in Hallion, ed., Hypersonic Revolution, vol. 1, pp. 694-702; B. K. Thomas, "USAF Nears Lifting Body Tests," Aviation Week July 10, 1967), pp. 99-101.
[1083] Scott Pace, "Engineering Design and Political Choice: The Space Shuttle 1969-72,’ master’s thesis (Cambridge: Massachusetts Institute of Technology, May 1982), pp. 1 79-1 88.
[1084] "Briefing: Rolls-Royce,’ The Economist (Jan. 10, 2009), pp. 60-62.
[1085] Nitin P. Padture, Maurice Gelland, and Eric H. Jordan, "Thermal Barrier Coatings for Gas – Turbine Engine Applications," Science, vol. 296 (Apr. 1 2, 2002), pp. 280-284.
[1086] Robert A. Miller, "History of Thermal Barrier Coatings for Gas Turbine Engines,’ NASA TM – 2009-215459 (2009).
[1087] G. W. Goward, "Seventeen Years of Thermal Barrier Coatings,’ in Department of Energy, Proceedings of the Workshop on Coatings for Advanced Heat Engines, Castine, ME, July 27-30, 1987 (Washington, DC: U. S. Department of Energy, 1987).
[1088] Author interview with Robert A. Miller, June 10, 2009; see also Miller, NASA TM-2009-215459.
[1089] Dong-ming Zhu and Miller, "Investigation of Thermal High Cycle and Low Cycle Fatigue Mechanisms of Thick Thermal Barrier Coatings,’ Materials Science and Engineering, vol. A245 (l998), pp. 212-223.
[1090] Miller interview.
[1091] Zhu and Miller, "Development of Advanced Low Conductivity Thermal Barrier Coatings,’ International Journal of Applied Ceramic Technology, vol. l (2004), pp. 86-94.
[1092] R. McCallum, "Casting Critical Components,’ Superalloys Source Book, pp. 286-291.
[1093] J. E. Northwood, "Improving Turbine Blade Performance by Solidification Control,’ Superalloys Source Book, pp. 292-296.
[1094] M. Gell, D. H. Duhl, and A. F. Giami, "The Development of Single Crystal Turbine Blades, Superalloys Source Book, pp. 297-306.
[1095] Heppenheimer, "Making Planes from Powder,’ High Technology (Sept. 1986), pp. 54-55; author interview of Philip Parrish, Mar. 21, 1986.
[1096] J. Sorensen, "Titanium Matrix Composites—NASP Materials and Structures Augmentation Program," AIAA Paper 90-5207 (1990); Stanley W. Kandebo, "Boeing 777 to Incorporate New Alloy Developed for NASP," Aviation Week (May 3, 1993), p. 36; "NASP Materials and Structures Program: Titanium Matrix Composites," McDonnell-Douglas, DTIC ADB-1 92559, (Dec. 31, 1 991).
[1097] John Bradley, "Test and Evaluation Report for Carbon/Carbon Wing Box Component.’ General Dynamics, DTIC ADB-191627, (Feb. 21, 1992).
[1098] Leonard David, "Lift for Public Space Travel,’ Aerospace America (Feb. 2009), pp. 24-29.
[1099] Rockwell International, “High Conductivity Composites: Executive Summary, Copper Materials, Beryllium Materials, Coatings, Ceramic Materials and Joining,’ DTIC ADB-191898 (Mar. 1993); Terence Ronald, “Status and Applications of Materials Developed for NASP,’ AIAA Paper 95-6131 (1995).
[1100] Frank C. Conahan, “National Aero-Space Plane: Restructuring Further Research and Development Efforts,’ General Accounting Office Report NSIAD-93-71 (Dec. 3, 1992), table, p. 20.
[1101] . An early example was the innovative Focke-Wulf FW 190 fighter of World War II fame. Its landing gear and flaps were electrically controlled and actuated by small reliable high-torque electric motors. A variable incidence electrically controlled and actuated movable horizontal stabilizer maintained trim about the longitudinal (pitch) axis and was regularly used to relieve the heavy control forces encountered during steep dives (the FW 190 exceeded Mach 0.8 during testing). Another highly advanced FW 190 feature was the BMW 801 Kommandogerat (command equipment). This consisted of a mechanical-hydraulic analog computer that automatically adjusted engine fuel flow, variable pitch propeller setting, supercharger setting, fuel mixture, and ignition timing in response to pilot commands via the single throttle lever. This pioneering step in computerized integrated propulsion control systems greatly simplified engine control. See Albert C. Piccirillo, "Electric Aircraft Pioneer—The Focke-Wulf Fw 190,’ Society of Automotive Engineers (SAE) Paper 965631, Oct. 1996.
[1102] Control cables were replaced with rigid pushrods in German World War II flight control systems, for example in the FW 190 and the Fiesler Fi-1 03 pulsejet-powered cruise missile (the V-1). Push – rods minimized effects produced by control cables stretching under load.
[1103] "NASA Dryden Flight Research Center Pilot Biographies.’ http://www. nasa. gov/centers/dryden/ news/Biographies/Pilots/index. html, accessed July 21, 2009. Herb Hoover was the first civilian pilot to fly faster than the speed of sound. He exceeded Mach 1 in the Bell XS-1 on Mar. 10, 1948.
[1104] Lawrence K. Loftin, "Quest for Performance: The Evolution of Modern Aircraft,’ Part II, ch. 1 2, Science and Technology Branch, NASA SP-468 (1985).
[1105] Richard P. Hallion, "The Air Force and the Supersonic Breakthrough,’ published in Technology and the Air Force: A Retrospective Assessment, Air Force History and Museums Program, Washington, DC, 1997.
[1106] Hallion, "On the Frontier: Flight Research at Dryden, 1946-1981,’ NASA SP-4303 (1984).
[1107] Michael J. Neufeld, "The Rocket and the Reich; Peenemunde and the Coming of the Ballistic Missile Era,’ The Smithsonian Institution, published by The Free Press, a division of Simon and Schuster, New York, 1995. James E. Tomayko, "Computers Take Flight: A History of NASA’s Pioneering Digital Fly-by Wire Project,’ NASA SP-2000-4224 (2000).
[1108] Much like the Space Shuttle is carried on top of the NASA Boeing 747s when it is ferried from Edwards AFB to Cape Kennedy, FL.
[1109] Tomayko, "Blind Faith: The United States Air Force and the Development of Fly-By-Wire Technology,’ Technology and the Air Force: A Retrospective Assessment, Air Force History and Museums Program, Washington, DC, 1 997.
1 0. Dutch roll is a term commonly used to describe an out of phase combination of yawing and rolling. Dutch roll instability can be improved by the use of a yaw damper.
1 1. The Hs 1 29 was armed with a variety of cannon that could include a 75-millimeter antitank gun.
1 2. Norman C. Weingarten, "History of In-Flight Simulation & Flying Qualities Research at CAL – SPAN," AIAA Journal of Aircraft, vol. 42, no. 2, March/April 2005.
1 3. Paul F. Borchers, James A. Franklin, and Jay W. Fletcher, "Flight Research at Ames, 1 9401 997: Fifty-Seven Years of Development and Validation of Aeronautical Technology," NASA SP-3300 (1998).
1 4. Rowland F. Pocock, "German Guided Missiles of the Second World War," Arco Publishing Company, Inc., New York, 1967. These included Matador, Snark, BOMARC, Rascal, plus many others developed in a number of countries. See Gavin D. Jenny, James W. Morris, and Vernon R. Schmitt, ‘Fly-byWire, A Historical and Design Perspective," The Society of Automotive Engineers, 1998.
[1115] An electrical side stick controller was developed in Germany during the Second World War to guide air-launched Henshel Hs 293 and Ruhrstahl Fritz X missiles against ships maneuvering at sea. Command signals were transmitted from the controller to the missiles via radio link. A similar guidance approach was used on the surface-to-air Wasserfall (Waterfall) command-guided antiaircraft missile. Examples of these weapons are on display at the National Air and Space Museum’s Udvar-Hazy Center at Dulles
Airport near Washington, DC, and at the National Museum of the U. S. Air Force in Dayton, OH.
1 6. Bill Alford was killed on Oct. 12, 1959, in the crash of a British Blackburn Buccaneer during a visiting test pilot evaluation flight from the Aircraft and Armament Experimental Establishment at Boscombe Down in the United Kingdom.
1 7. Donald L. Mallick, with Peter W. Merlin, "The Smell of Kerosene: A Test Pilot’s Odyssey," NASA SP-4108 (2003).
1 8. S. A. Sjoberg, "Some Experience With Side Controllers,’ Research Airplane Committee Report on the Progress of the X-15 Project, pp. 167-174; Conference held at NACA Langley Aeronautical Laboratory, Langley Field, VA, Oct. 25-26, 1956.
1 9. "Automatic Flight Control System Sought,’ Aviation Week, Aug. 6, 1956, pp. 275-284.
[1120] Duane McRuer and Dunstan Graham, "A Flight Control Century: Triumphs of the Systems Approach,’ Paper 617, Journal of Guidance, Control and Dynamics, vol. 27, no. 2, pp.
161-173, AIAA, 2003.
[1121] J. K.B. Illingworth and H. W. Chinn, "Variable Stability and Control Tests on the S. C.1 Aircraft in Jet-Borne Flight, with Particular Emphasis on Reference to Desirable VTOL Flying Qualities,’ Royal Aircraft Establishment, Bedford, U. K., Her Majesty’s Stationery Office, London, 1969.
[1122] D. Lean and H. W. Chinn, "Review of General Operating Experience with a Jet-Lift VTOL Research Aircraft (Short S. C. 1),’ Aeronautical Research Council Current Paper C. P. No. 832, Her Majesty’s Stationery Office, London, 1965.
[1123] Illingworth and Chinn, "Variable Stability and Control Tests on the S. C.1 Aircraft in Jet-Borne Flight, with Particular Emphasis on Reference to Desirable VTOL Flying Qualities."
[1124] J. C. Floyd, "The Canadian Approach to All-Weather Interceptor Development, Fourteenth British Commonwealth Lecture," The Journal of the Royal Aeronautical Society, vol. 62, No. 576, Dec. 1958.
[1125] Thirty-one former CF-1 05 engineers were hired by NASA with several going on to hold important positions within the NASA Mercury, Gemini, and Apollo programs. Chris Gainor, "Arrows to the Moon: Avro’s Engineers and the Space Race,’ (Burlington: Apogee Books, 2001).
[1126] "Experience with the X-15 Adaptive Flight Control System,’ NASA TN-D-6208, NASA Flight Research Center, Edwards, CA (March 1 971).
[1127] Hallion, "On the Frontier Flight Research at Dryden, 1946-1981 .’
[1128] Allan F. Damp, "Evaluation Tests on Boulton-Paul VC-10 Aileron Integrated Flight Control Actuator,’ Commercial Division, Boeing Company, Renton, WA, Mar. 10, 1970.
[1129] Molly Neal, "VC10: Vickers-Armstrongs’ Long-range Airliner,’ Flight International, May 10, 1962.
[1130] Ray Sturtivant, "British Research and Development Aircraft: Seventy Years at the Leading Edge,’ Haynes/Foulis, 1990; Kyrill Von Gersdorff, "Transfer of German Aeronautical Knowledge After 1945,’ in Hirschel, Ernst Heinrich, Horst Prem, and Gero Madelung, "Aeronautical Research in Germany (From Lilienthal to Today),’ Springer-Verlag, Berlin Heidelberg, 2004.
[1131] B. S. Wolfe, "The Concorde Automatic Flight Control System: A Description of the Automatic Flight Control System for the Anglo-French Supersonic Transport and its Development to Date,’ Aircraft Engineering and Aerospace Technology, vol. 39, issue 5, 1967.
[1132] During the war in Southeast Asia, 8,961 U. S. aircraft were lost. Of these, Air Force losses totaled 2,251, the Navy 859, the Marine Corps 463, and the Army 5,388 (mostly helicopters). The McDonnell-Douglas F-4 Phantom was the predominant fighter/attack aircraft used by the USAF, the USMC, and the Navy during the Vietnam war. A total of 765 F-4s were lost.
[1133] Robert E. Ball, "The Fundamentals of Aircraft Combat Survivability Analysis and Design,’ American Institute of Aeronautics and Astronautics (AIAA), New York, 1985.
[1134] Gavin D. Jenny, "JB-47E Fly-By-Wire Flight Test Program (Phase I),’ Air Force Flight Dynamics Laboratory TR-69-40, Wright-Patterson AFB, OH, Sept. 1969.
[1135] Gavin D. Jenny, James W. Morris, and Vernon R. Schmitt, "Fly-by-Wire, A Historical and Design Perspective,’ The Society of Automotive Engineers (SAE), 1998.
[1136] Tomayko, "Blind Faith: The United States Air Force and the Development of Fly-By-Wire Technology,’ Technology and the Air Force: A Retrospective Assessment, Air Force History and Museums Program, Washington, DC, 1 997.
[1137] Michael L. Yaffee, "Survivable Controls Gain Emphasis,’ Aviation Week, Feb. 2, 1970.
[1138] Jenny, "JB-47E Fly-By-Wire Flight Test Program (Phase I).’
[1139] Ibid.
[1140] Ibid.
[1141] Tomayko, "Computers Take Flight: A History of NASA’s Pioneering Digital Fly-by Wire Project.
[1142] In a Dec. 30, 2006, e-mail, Drury Wood wrote: "I was the project test pilot on this airplane. Flew all of the test rigs and full size over 600 flights. Made the record flights, Awarded Bundesver – dienstkreuz am Bande and Society of Experimental Test Pilots’ highest award, Kinchloe."
[1143] Ulrich Butter, "Control, Navigation, Avionics, Cockpit," in Ernest Heinrich Hirschel, Horst Prem, and Gero Madelung, Aeronautical Research in Germany (From Lilienthal to Today), Springer-Verlag, Berlin Heidelberg, 2004.
[1144] "RAE Electric Hunter," Flight Internationa/, June 28, 1973, pp. 1010-101 1.
[1145] Yefim Gordon, "An Industry of Prototypes: Sukhoi T-4, Russia’s Mach 3 Bomber," Wings of Fame, vol. 9, Aerospace Publishing Limited, London, 1997.
[1146] In an interview published in Krylya Rodiny, No. 8, Aug. 1989, under the title "An Aircraft of the 21 st Century,’ the chief designer at the Sukhoi OKB (Experimental Design Bureau), Mikhail Petrovich Simonov, commented: "It is also time to talk about those for whom risk, courage, and a willingness to devote their lives to learning the unknown. . . . I am talking about the test pilots of our design bureau. . . . Back then we did not know how the frequency responses of control match the human capabilities. Zhenya [Solovyev] ended up in a resonant mode and was killed and the aircraft was destroyed.’
[1147] Gordon and Peter Davidson, "Sukhoi Su-27 Flanker,’ Specialty Press, 2006.
[1148] David C. Aronstein and Albert C. Piccirillo, "The Lightweight Fighter Program: A Successful Approach to Fighter Technology Transition," AIAA, 1996. M. J. Wendl, G. G. Grose, J. L. Porter, and V. R. Pruitt, "Flight/Propulsion Control Integration Aspects of Energy Management," Society of Automotive Engineers, Paper No. 740480, 1974.
[1149] U. S. industry interest in "vortex lift" increased during the early 1 960s as a result of NASA Langley aerodynamic studies of foreign delta wing aircraft such as the Concorde supersonic transport and the combination canard/delta wing Swedish AJ-37 Viggen fighter. Langley’s vortex lift research program was led by Edward Polhamus, with researcher Linwood McKinney studying the favorable effects of vortexes on lift produced by strong leading-edge vortex flow off slender lifting surfaces.
See Chambers, Joseph R., Partners in Freedom: Contributions of the Langley Research Center to U. S. Military Aircraft of the 1990s, Monographs in Aerospace History No. 19, NASA, Washington,
DC, 2000.
[1150] Aronstein and Piccirillo, "The Lightweight Fighter Program: A Successful Approach to Fighter Technology Transition."
[1151] Robert B. Voas, "Manned Control of Mercury Spacecraft,’ Astronautics, vol. 7, no. 3, Mar. 1962, p. 18.
[1152] "LLRV Fact Sheet,’ FS-2002-09-026-DFRC, NASA Dryden Flight Research Center.
[1153] LLRV No. 2 is on display at the Dryden Flight Research Center.
[1154] Tomayko, "Computers Take Flight: A History of NASA’s Pioneering Digital Fly-by Wire Project.
[1155] The DSKY had been developed for the Apollo program and enabled input and output to the digital computer system. It was used during Phase I of the DFBW F-8 program.
[1156] Tomayko, "Computers Take Flight: A History of NASA’s Pioneering Digital Fly-by Wire Project."
[1157] These Sperry-developed analog computers were also used in the Air Force’s YF-4E fly-by-wire project, which was in progress at the same time as NASA’s DFBW F-8 effort. Ibid.
[1158] Gain is a measure of the sensitivity of the aircraft to command inputs to the flight control system.
[1159] As noted earlier, the NACA had evaluated a side stick controller as early as 1952. Side stick controllers had been successfully used in the NASA F9F-2, F-107A, and X-15, as well as the Mercury, Gemini, and Apollo space vehicles, and they were planned to be used in the upcoming Space Shuttle. The Air Force had flight-tested a side stick controller in a B-47E and a C-141 in the late 1960s and was planning on its use in the fly-by-wire project 680J YF-4E Survivable Flight Control System (SFCS) test aircraft.
[1160] Kenneth J. Szalai, telephone conversation with author, Mar. 1 1, 2009.
[1161] Tomayko, "Computers Take Flight: A History of NASA’s Pioneering Digital Fly-by Wire Project.
[1162] Szalai, telephone conversation.
[1163] Szalai, Calvin R. Jarvis, Gary E. Krier, Vincent A. Megna, Larry D. Brock, and Robert N. O’Donnell, "Digital Fly-by-Wire Flight Control Validation Experience," NASA TM-72860 (Dec. 1978). R. E. Bailey, M. F. Schaeffer, R. E. Smith, and J. F. Stewart, "Flight Test Experience With Pilot-Induced-Oscillation Suppression Filters," NASA TM-86028, NASA Dryden Research Center (Jan. 1984).
[1164] Digital Fly-By-Wire, "The All-Electric Airplane," NASA Dryden TF-2001-02 DFRC.
[1165] Szalai, et al., "Digital Fly-By-Wire Flight Control Validation Experience."
[1166] Szalai, e-mail to the author, Mar. 1 1, 2009.
[1167] "General Dynamics and Northrop to Build Lightweight Fighter Prototypes,’ Interavia, July 1972, p. 693.
[1168] C. Droste and J. Walker, "The General Dynamics Case Study on the F-16 Fly-By-Wire Flight Control System,’ AIAA Professional Study Series, AIAA, New York, June 1998.
[1169] Chambers, Partners in Freedom.
[1170] Later, during high angle-of-attack flight-testing of an early production F-16, the aircraft entered a stabilized deep-stall condition following a series of rolls in a vertical climbing maneuver. The test pilot was unable to recover with normal aerodynamic controls and used the anti-spin parachute installed for high angle-of-attack testing. NASA worked with the Air Force and the contractor to develop a fix that involved a "pitch rocker’ technique to force the aircraft out of the deep stall. The approach was incorporated into the production F-16 flight control system as a pilot selectable emergency recovery mode. In addition, the horizontal tail area of the production F-16 was increased by about 25 percent. Ibid.
[1171] B. R. Ashworth and William M. Kahlbaum, Jr., "Description and Performance of the Langley Differential Maneuvering Simulator,’ NASA TN-D-7304, NASA Langley Research Center (June 1973).
[1172] Chambers, Partners in Freedom.
[1173] Joe Stout, "What a Wonderful Airplane: YF-16 First Flight,’ Code One Magazine, General Dynamics, July 1992.
[1174] Aronstein and Piccirillo, "The Lightweight Fighter Program: A Successful Approach to Fighter Technology Transition."
[1175] H. J. Hillaker, "The F-16: A Technology Demonstrator, a Prototype, and a Flight Demonstrator," Proceedings of AIAA Aircraft Prototype and Technology Demonstrator Symposium, AIAA, New York, 1983, pp. 113-120.
[1176] Aronstein and Piccirillo, "The Lightweight Fighter Program: A Successful Approach to Fighter Technology Transition."
[1177] Ibid.
[1178] Stout, "What a Wonderful Airplane: YF-16 First Flight.’ Joseph F. Baugher, "General Dynamics YF-16/CCV," American Military Aircraft, Mar. 31, 2000.
[1179] L. Martin and D. Gangsaas, "Testing the YC-14 Flight Control System Software,’ AIAA Journal of Guidance and Control, July-Aug. 1 978.
[1180] H. A. Rediess and E. C. Buckley, "Technology Review of Flight Crucial Flight Control Systems (Application of Optical Technology),’ NASA CR-172332 (Supplement 1) (Sept. 1984).
[1181] . Martin, et al., "Testing the YC-1 4 Flight Control System Software.’
[1182] Stephen D. Ishmael and Donald R. McMonagle, "AFTI/F-16 Flight Test Results and Lessons, NASA TM-84920 (Oct. 1983).
[1183] Ibid.
[1184] Gary Creech, "AFTI/F-1 6 Retires After 22 Years," The Dryden Express, Dryden Flight Research Center, vol. 43, issue 2, Feb. 23, 2001.
[1185] James Blaylock, Donald Swihart, and William Urshel, "Integration of Advanced Safety Enhancements for F-16 Terrain Following," AIAA-1987-2906.
[1186] Charles A. Baird and Franklin B. Snyder, with introduction by Lt. Mark Bierele, AFTI/F-16 Program Office, "Terrain-Aided Altitude Computations on the AFTI/F-1 6," Harris Corporation, Melbourne, FL, Aug. 1990.
[1187] Finley Barfield, Duke Browning, and Judith Probert, "All Terrain Ground Collision Avoidance and Maneuver Terrain Following for Automated Low Level Night Attack,’ IEEE AES Systems Magazine, Mar. 1993.
[1188] Robert Navarro, "Performance of an Electro-Hydrostatic Actuator on the F-1 8 Systems Research Aircraft,’ NASA TM-97-206224, NASA Dryden Flight Research Center (1997).
[1189] James W. Ramsey, "Power-by-Wire," Avionics Magazine, May 1, 2001 .
[1190] Droste, et al., "The General Dynamics Case Study on the F-16 Fly-By-Wire Flight Control System.
[1191] Ramsey, "Power-by-Wire."
[1192] Ibid.
[1193] Ramsey, "Power-by-Wire."
[1194] Creech, "AFTI/F-16 Retires After 22 Years.”
[1195] Ibid.
[1196] "AFTI F-1 6 Fact Sheet," National Museum of the U. S. Air Force, 2001.
[1197] Stephen D. Ishmael, Dale A. Mackall, and Victoria A. Regenie, "Design Implications From AFTI/F16 Flight Test,’ NASA TM-86026, NASA Ames Research Center, Dryden Flight Research Facility, Edwards, CA (1984); Ishmael, et al., "AFTI/F-16 Flight Test Results and Lessons’; Mackall, ‘Development and Flight Test Experiences with a Flight-Crucial Digital Control System,’ NASA TP – 2857, NASA Ames Research Center, Dryden Flight Research Facility, Edwards, CA (Nov. 1988); Mackall, "AFTI/F-16 Digital Flight Control System Experience,’ in Gary P. Beasley, ed., NASA Aircraft Controls Research 1983, pp. 469-487, NASA CP-2296 (1984), Proceedings of Workshop Held at NASA Langley Research Center, Oct. 25-27, 1983.
[1198] John Rushby, "Formal Methods and the Digital Systems Validation for Airborne Systems,’ NASA CR-4551, NASA Langley Research Center (Dec. 1, 1993).
[1199] Mackall, "Development and Flight Test Experiences with a Flight-Crucial Digital Control System.’
1 00. Rushby, "Formal Methods and the Digital Systems Validation for Airborne Systems.’
[1201] Mackall, "Development and Flight Test Experiences with a Flight-Crucial Digital Control System.
[1202] Ibid.
[1203] Ibid.
[1204] Ibid.
1 05. Rushby, "Formal Methods and the Certification of Critical Systems,’ SRI CSL-93-07, SRI International (Nov. 1993).
1 06. "Formal Methods Specification and Verification Guidebook for Software and Computer Systems, Volume I: Planning and Technology Insertion,’ NASA TP-98-208193 (1998); "Formal Methods Specification and Analysis Guidebook for the Verification of Software and Computer Systems, Volume II: A Practitioner’s Companion,’ NASA GB-001-97 (1997).
[1207] Szalai, et al., "Digital Fly-By-Wire Flight Control Validation Experience.’
1 08. Rediess, et al., "Technology Review of Flight Crucial Flight Control Systems (Application of Optical Technology)."
[1209] E. Robert Lemble, "DIGITAC—A Unique Digital Flight Control Testbed Aircraft," AAA-19901288, SFTE, DGLR, and SETP Biannual Flight Test Conference, 5th, Ontario, CA, May 22-24, 1990.
1 10. Dennis R. Furman, "USAF Test Pilot School Use of DIGITAC in Systems Testing,’ Society of Automotive Engineers Document No. 851 827, Oct. 1985.
[1211] Robert W. Kempel and Michael R. Earls, "Flight Control Systems Development and Flight Test Experience with the HiMAT Research Vehicles," NASA TP-2822 (June 1988).
1 12. "HiMAT: Highly Maneuverable Aircraft Technology," NASA Dryden FS-2002-06-025-DFRC (2002).
[1213] Kempel, "Flight Experience with a Backup Flight Control System for the HiMAT Research Vehicle," AIAA Paper 82-1541 (Aug. 1982).
1 14. E. L. Duke, F. P. Jones, and R. B Roncoli, "Development of a Flight Test Maneuver Autopilot for a Highly Maneuverable Aircraft," NASA TP-2218 (1986).
[1215] Mackall, "Development and Flight Test Experiences with a Flight-Crucial Digital Control System," p. 112.
1 16. Dwain A. Deets, V. Michael DeAngelis, and David P. Lux, "HiMAT Flight Program: Test Results and Program Assessment Overview," NASA TM-86725 (June 1986).
1 17. Butter, "Control, Navigation, Avionics, Cockpit,’ Aeronautical Research in Germany (From Lilienthal to Today), Springer-Verlag, Berlin Heidelberg, 2004.
1 1 8. Rediess, et al., "Technology Review of Flight Crucial Flight Control Systems (Application of Optical Technology).’
1 19. C. J. Yeo, "The Fly-by-Wire Jaguar,’ Society of Experimental Test Pilots (SETPj 27th Symposium Proceedings, Beverly Hills, CA, Sept. 28-Oct. 1, 1983, pp. 193-214.
1 20. Katsuhei Shibata and Hideaki Ohmiya, "The T-2 Control Configured Vehicle Development, Integration and Flight Test,’ AIAA-1988-3882, published in Technical Papers, pt. 1 (A89-1 8051 05-06) AIAA/IEEE Digital Avionics Systems Conference, San Jose, CA, Oct. 17-20, 1988, pp. 177-184.
[1221] Terrill W. Putnam, "X-29 Flight-Research Program," NASA TM-86025, Ames Research Center- Dryden Flight Research Facility, Edwards, CA (Jan. 1984).
[1222] Ibid.
[1223] Ibid.
1 24. Robert Clarke, John J. Burken, John T. Bosworth, and Jeffery E. Bauer, "X-29 Flight Control Lessons Learned," NASA TM-4598 (June 1984).
1 25. Sewell was later killed in the crash of a World War II-era Grumman TBM Avenger torpedo bomber during a takeoff from Danielston, CT, on Aug. 4, 1988. With Grumman since 1 969, he had flown with the USMC in Korea and Vietnam and had over 10,000 flying hours on 1 40 different aircraft types.
1 26. Developed by NASA and originally tested on the NASA F-8 Super Critical Wing (SCW) aircraft at Dryden in the 1 970s, a supercritical airfoil has a flattened upper surface compared to a conventional airfoil shape. This shape delays the onset of shock waves on the upper wing surface and reduces their strength, theoretically resulting in a decrease in overall drag.
1 27. "X-29 Fact Sheet," NASA Dryden Flight Research Center, Mar. 1, 2008.
1 28. Chambers, Partners in Freedom.
1 29. Jeffrey E. Bauer, Robert Clarke, and John J. Burken, "Flight Test of the X-29A at High Angle of Attack: Flight Dynamics and Controls,’ NASA TP-3537 (Feb. 1995).
1 30. Ibid.
[1231] Ibid.; Chambers, Partners in Freedom.
1 32. Mackall, "Development and Flight Test Experiences with a Flight-Crucial Digital Control System."
[1233] R. Guyton and F. Luria, "Flight Testing of Pneumatic Forebody Vortex Control on the X-29 Technology Demonstrator," Society of Automotive Engineers (SAE) No. 922008, Oct. 1992.
1 34. Hallion and Michael H. Gorn, On the Frontier: Experimental Flight at NASA Dryden, (Washington: Smithsonian Books, 2003), Appendix W, X-29 flight test chronology.
1 35. "X-31 Enhanced Fighter Maneuverability Demonstrator Fact Sheet,’ NASA Dryden Flight Research Center, 2001 .
1 36. Chambers, Partners in Freedom.
1 37. Rushby, "Formal Methods and the Certification of Critical Systems,’ SRI-CSL-93-07, SRI International, Nov. 1993. Rushby, "Formal Methods and the Digital Systems Validation for Airborne Systems,’ NASA CR-4551 (Dec. 1, 1993).
1 38. "X-31 Enhanced Fighter Maneuverability Demonstrator Fact Sheet.’
1 39. A Split-S maneuver consists of a 1 80-degree roll to inverted flight followed by a pull-through to erect level flight with the aircraft ending up positioned 1 80 degrees from its initial heading at a lower altitude.
1 40. Patrick C. Stoliker and Bosworth, "Evaluation of High-Angle-of-Attack Handling Qualities for the X-31A Using Standard Evaluation Maneuvers," NASA TM-104322 (1996).
[1241] Chambers, Partners in Freedom.
1 42. Al Groves, Fred Knox, Rogers Smith, and Jim Wisneski, "X-31 Flight Test Update," 37th Symposium Proceedings, Society of Experimental Test Pilots (SETPj, Lancaster, CA, 1993, pp. 100-1 16.
[1243] Chambers, Partners in Freedom:.
[1244] A nonconventional poststall turning maneuver named in honor of Dr.-Ing. Wolfgang Herbst, who, as director of advanced design and technology at the Military Aircraft Division of Messerschmitt – Bolkow-Blohm in Germany, had emphasized designs capable of poststall maneuvering. The author of numerous technical articles and papers dealing with preliminary aircraft design, aerodynamics, and maneuverability, Herbst died in the crash of a replica FW 190 fighter that he was flying in 1993.
[1245] Dave Canter, "X-31 Post-Stall Envelope Expansion and Tactical Utility Testing,’ Fourth High Alpha Conference, NASA Dryden Flight Research Center, July 1 2-14, 1994 (NASA CP-10143), vol. 2.
[1246] Bosworth and P. C. Stoliker, "The X-31A Quasi-Tailless Flight Test Results," NASA TP-3624 (1996).
1 47. Don Haley, "Ice Cause of X-31 Crash," NASA R-5-203, Dryden Flight Research Center (Nov. 7, 1995).
[1248] Jay Levine, "X-31 ‘s loss," Dryden Flight Research Center X-Press, Jan. 2004.
[1249] The Kiel probe was also found to be more susceptible to ice accumulation, a fact discovered after the accident through wind tunnel testing.
[1250] Ibid.
[1251] "X-31 VECTOR Program Phase I Begins," NASA Dryden PR-98-09 (Mar. 9, 1998)
1 52. The RM-1 was license manufactured by Volvo in Sweden and was a derivative of the General Electric GE F404 engine used in the F/A-1 8.
1 53. James Darcy, "Successful First Flight for VECTOR X-31 at Pax,’ NAS Patuxent River Release 01-040 (Feb. 28, 2001).
[1254] "EADS/Boeing X-31,’ Flugrevue Magazine, Dec. 28, 2002.
1 55. Karl Schwartz, "Successful ESTOL Landings with the X-31 A," Flugreview, July 2003.
[1256] J. R. Wilson, "X-31 Finds a Shorter Path to Success," Aerospace America, Aug. 2003.
1 57. "YF-1 2 Flight Research Program," NASA Dryden Technology Fact Sheet TF-2004-1 7, NASA Dryden Flight Research Center (2004).
[1258] "Lockheed YF-1 2 NASA Fact Sheet," FS-2002-09-047 DFRC, NASA Dryden Flight Research Center (2002).
1 59. L. K. Myers, D. A. Mackall, and F. W. Burcham, Jr., "Flight Test Results of a Digital Electronic Engine Control System in an F-15 Airplane,’ AIAA Paper 82-1080 (June 1982).
1 60. "Digital Electronic Engine Control,’ NASA Dryden Technology Fact Sheet TF-2004-03, Dryden Flight Research Center (2004).
[1261] Frank W. Burcham, Lawrence P. Myers, and Ronald J. Ray, "Predicted Performance Benefits of an Adaptive Digital Engine Control System on an F-15 Airplane,’ NASA TM-85916 (Jan. 1985).
1 62. "The HIDEC Program,’ NASA Dryden Research Center Technology Fact Sheet, 1999.
1 63. Engine stall margin is a measure of the amount that engine operating pressure is reduced to provide a margin of safety to help prevent engine compressor stall due to excessive pressure.
[1264] Jennifer L. Baer-Riedhart and Robert J. Landy, "Highly Integrated Digital Electronic Control-Digital Flight Control, Aircraft Model Identification and Adaptive Engine Control,’ NASA TM-86793 (Mar.
1987); "The HIDEC Program,’ NASA Dryden Flight Research Center Technology Fact Sheet, 1999.
1 65. Glen B. Gilyard and John S. Orme, "Subsonic Flight Test Evaluation of a Performance Seeking Algoritm on an F-15 Airplane,’ NASA TM-4400 (Aug. 1992).
1 66. Baer-Riedhart, et al., "Highly Integrated Digital Electronic Control-Digital Flight Control, Aircraft Model Identification and Adaptive Engine Control’; "The HIDEC Program,’ NASA Dryden Flight Research Center Technology Fact Sheet, 1999.
[1267] "F-15 Flight Research Facility,’ NASA Dryden Flight Research Center Fact Sheet FS-022, 1999.
1 68. Tomayko, "The Story of Self-Repairing Flight Control Systems,’ Dryden Historical Study, No. 1, Christian Gelzer, ed., 2003.
[1269] "F-15 Flight Research Facility."
1 70. "F-1 5 HIDEC (Highly Integrated Digital Electronic Control)," NASA Dryden Flight Research Center Fact Sheet, 1999.
1 71. Tomayko, "The Story of Self-Repairing Flight Control Systems."
[1272] "Propulsion Controlled Aircraft," NASA Dryden Fact Sheet FS-041, 1999.
1 73. The canards used on the NF-1 5B were based on the F/A-1 8 horizontal stabilators.
1 74. Chambers, Partners in Freedom.
[1275] "NASA NF-15B Research Aircraft Fact Sheet,’ Dryden Flight Research Center, Mar. 1 1, 2009.
[1276] John C. DeLaat, George W. Gallops, Laura J. Kerr, Robert P. Kielb, John S. Orme, Robert D. Southwick, and Mark G. Walsh, “High Stability Engine Control (HISTEC) Flight Test Results,’ NASA TM-1998-208481 (July 1998).
[1277] Ibid.
1 78. Tomayko, "The Story of Self-Repairing Flight Control Systems."
1 79. Peggy S. Williams-Hayes, "Flight Test Implementation of a Second Generation Intelligent Flight Control System," NASA TM-2005-213669 (Nov. 2005).
1 80. "Intelligent Flight Control System," NASA Dryden Fact Sheet FS-076, Feb. 1 3, 2006.
[1281] M. G. Perhinschi, J. Burken, M. R. Napolitano, G. Campa, and M. L. Fravolini, "Performance Comparison of Different Neural Augmentation for the NASA Gen – 2 IFCS F-15 Control Laws,’ Proceedings of the 2004 American Control Conference, Boston, MA, 2004.
1 82. Creech, "NASA Dryden Neural Network Passes Milestone,’ NASA Dryden Press Release, Sept. 3, 2003.
1 83. Bosworth and Williams-Hayes, "Flight Test Results from the NF-15B Intelligent Flight Control System (IFCS) Project with Adaptation to a Simulated Stabilator Failure,’ AIAA Paper 2007-281 8, 2007.
1 84. Cory Ippolito, John Kaneshige, and Yoo-Hsiu Yeh, "Neural Adaptive Flight Control Testing on an Unmanned Experimental Aerial Vehicle,’ AIAA Paper 2007-2827, 2003; Tomayko, "The Story of Self-Repairing Flight Control Systems.’
1 85. "NASA NF-15B Research Aircraft Fact Sheet.’
1 86. Aronstein and Piccirillo, "Have Blue and the F-1 17A, Evolution of the "Stealth Fighter,’ American Institute of Aeronautics and Astronautics, Reston, VA, 1997.
1 87. Brian W. Kowal, Carl J. Scherz, and Richard Quinliven, "C-17 Flight Control System Overview,’ IEEE Aerospace and Electronic Systems Magazine, July 1 992.
1 88. C. Favre, "Fly-by-Wire for Commercial Aircraft: the Airbus Experience,’ International Journal of Control, vol. 59, no. 1, 1994, pp. 1 39-157.
1 89. "All-Electric Aircraft Research Speeds Up,’ Aerospace America, Jan. 2009, pp. 4-8.
1 90. William Palmer, "Submarine Fly-by-Wire Ship Control System Certification Program Leverages Aviation Industry Best Practice,’ Wavelengths Online, The Official Publication of the Naval Surface Warfare Center, Carderock Division, Oct. 1, 2004.
[1291] . William H. More, ed., National Transportation Statistics (Washington, DC: U. S. Department of Transportation, 2009), p. 72.
[1292] Roger E. Bilstein, Orders of Magnitude: A History of the NACA and NASA, 1915-1990, NASA SP-4406 (Washington, DC: NASA, 1989), p. 9.
[1293] Edward M. Kerwin, Jr., "Procedures for Estimating the Near Field Noise of Rotating Aircraft Propellers,’ presented at the Fifty-First Meeting of the Acoustical Society of America, Cambridge, MA, June 17-23, 1956.
[1294] J. H. Doolittle, The Airport and Its Neighbors, The Report of the President’s Airport Commission (Washington, DC: U. S. Government Printing Office, 1952), p. 45.
[1295] Alain Depitre, "Aircraft Noise Certification History/Development," presented at the ICAO Noise Certification Workshop, Montreal, 2004, p. 3.
[1296] Alleviation of Jet Aircraft Noise Near Airports (Washington, DC: U. S. Office of Science and Technology, 1966), p. 8.
[1297] Newell D. Sanders, Aircraft Engine Noise Reduction, NASA SP-31 1 (Washington, DC: NASA, 1972), p. 2.
[1298] David M. Bearden, Noise Abatement and Control: An Overview of Federal Standards and Regulations (Washington, DC: Congressional Research Service, 2006), p. 3.
9. U. S. Government Support of the U. S. Commercial Aircraft Industry, Prepared for the Commission of the European Communities (Washington, DC: Arnold and Porter, 1991), pp. 37-43.
1 0. Sanders, Aircraft Engine Noise Reduction, NASA SP-31 1 (Washington, DC: NASA, 1 972),
p. 2.
1 1. M. J. Benzakein, S. B. Kazin, and F. Montegani, "NASA/GE Quiet Engine ‘A," AIAA Paper 72-657 (1972).
[1300] 2. Vicki L. Golich and Thomas E. Pinelli, Knowledge Diffusion in the U. S. Aerospace Industry (London: Alex Publishing, 1998), p. 61.
1 3. Robert V. Garvin, "Starting Something Big: The Commercial Emergence of GE Aircraft Engines, AIAA Paper 72-657 (1999), pp. 162-165.
[1302] A. P. Adamson, "Quiet Clean Short-Haul Experimental Engine (QCSEE) Design Rationale,’ SAE Paper 750605 (1975).
[1303] Garvin, "Starting Something Big,’ pp. 162-165.
[1304] C. C. Ciepluch, "A Review of the QCSEE Program,” NASA TM-X-71 818 (1975).
1 7. Ciepluch and W. S. Willis, "QCSEE—The Key to Future Short-Haul Air Transport,’ ICAO Bulletin 34 (1979).
[1306] "A Giant Step in Jetliner Propulsion,’ Spinoff 1996 (Washington, DC: NASA, 1 996), pp. 56-57.
[1307] U. S. Government Support of the U. S. Commercial Aircraft Industry (1991).
[1308] Peter G. Batterton, "Energy Efficient Engine Program Contributions to Aircraft Fuel Conservation, NASA TM-83741 (1984).
[1309] Louis J. Williams, Small Transport Aircraft Technology (Honolulu: University Press of the Pacific, 2001), pp. 37-39.
[1310] U. S. Government Support of the U. S. Commercial Aircraft Industry.
[1311] Lawrence. E. Macioce, John W. Schaefer, and Neal T. Saunders, "The Energy Efficient Engine Project," NASA TM-81566 (1980).
[1312] Saunders, "Advanced Component Technologies for Energy-Efficient Turbofan Engines,’ NASA TM-81507 (1980).
[1313] Guy Norris and Mark Wagner, Boeing 777: The Technological Marvel (Osceola, WI: MBI Publishing, 2001).
[1314] NASA Glenn Research Center at Lewis Field: Achieving the Extraordinary (Cleveland: NASA, 1999), p. 24.
[1315] "A Giant Step in Jetliner Propulsion," Spinoff 1996 (Washington, DC: NASA, 1996).
[1316] Williams, Small Transport Aircraft Technology, p. 38.
[1317] Roy D. Hager and Deborah Vrabel, Advanced Turboprop Project, NASA SP-495 (Washington, DC: NASA, 1988), p. 5.
[1318] Mark D. Bowles and Virginia P. Dawson, "The Advanced Turboprop Project: Radical Innovation in a Conservative Environment,’ in From Engineering Science to Big Science, The NACA and NASA Collier Trophy Research Project Winners, NASA SP-4219 (Washington, DC: NASA, 1998), p. 323.
[1319] Glenn A. Mitchell, "Experimental Aerodynamic Performance of Advanced 40 Degree-Swept, 10-Blade Propeller Model at Mach 0.6 to 0.85,’ NASA TM-88969 (1988).
[1320] Bowles and Dawson, "The Advanced Turboprop Project,’ p. 323.
[1321] Ibid.
[1322] "Full Scale Technology Demonstration of a Modern Counterrotating Unducted Fan Engine Concept: Design Test,’ NASA CR-1 80867 (1987).
[1323] Deb Case and Rick Kennedy, "GE and NASA To Begin Wind-Tunnel Testing This Summer of Open Rotor Jet Engine Systems,’ GE Aviation News Release (Evendale, OH: General Electric, 2009).
[1324] Ibid.
[1325] Jeff Schweitzer, "An Overview of Recent Collaboration Research with NASA in Ultra High Bypass Technology,’ presented at the NASA Fundamental Aeronautics 2007 Annual Meeting, New Orleans, Oct. 30-Nov. 1, 2007.
[1326] Alan H. Epstein, Statement Before the Subcommittee on Aviation Committee on Transportation and Infrastructure, U. S. House of Representatives Hearing on Aviation and Environment: Noise, Washington, DC, Oct. 24, 2007.
[1327] "Pratt & Whitney Pure Power PW1000G Engines," Pratt & Whitney S16154.9.08 (2008).
[1328] C. R. Jarvis, "An Overview of NASA’s Digital Fly-By-Wire Technology Development Program,’ NASA 75N18246 (1975).
[1329] James E. Tomayko, Computers Take Flight: A History of NASA’s Pioneering Digital Fly-By-Wire Project, NASA SP-4224 (Washington, DC: NASA, 2000), p. vii.
[1330] James F. Stewart, Frank W. Burcham, Jr., and Donald H. Gatlin, "Flight-Determined Benefits of Integrated Flight-Propulsion Control Systems," NASA TM-4393 (1992), pp. 2-4.
[1331] T. W. Putnam, "Digital Electronic Engine Control History," NASA 86N25344 (1984), p. 2.
[1332] "The DEEC," NASA TF-2004-03-DFRC (2004).
[1333] "Digital Electronic Engine Control (DEEC) Flight Evaluation in an F-15 Airplane," NASA CP – 2298 (1984).
[1334] Christian Gelzer, "60 Years of Cutting-Edge Flight Research Marked at NASA Dryden," Dryden News Release 06-37 (2006).
[1335] John S. Orne, "Performance Seeking Control Program Overview," NASA 95N3301 1 (1995), p. 32.
[1336] "Aircraft Accident Report: United Airlines Flight 232, McDonnell Douglas DC-10-10, Sioux Gateway Airport, Sioux City, Iowa, July 19, 1989," NTSB AAR-90-06 (1989).
[1337] Tom Tucker, Touchdown: The Development of Propulsion Controlled Aircraft at NASA Dryden (Washington, DC: NASA, 1999).
[1338] "Propulsion/ACEE," NASA FACTS-93/8-81 (1981).
[1339] Jennifer L. Baer-Riedhart and Robert J. Landy, "Highly Integrated Digital Electronic Control-Digital Flight Control, Aircraft Model Identification and Adaptive Engine Control,’ NASA TM-86793 (1987).
[1340] John K. Lytle, "The Numerical Propulsion System Simulation: A Multidisciplinary Design System for Aerospace Vehicles,’ NASA TM-1999-209194 (1999), p. 1.
[1341] John Lytle, Greg Follen, Cynthia Naiman, Austin Evans, Joseph Veres, Karl Owen, and Isaac Lopez, ‘Numerical Propulsion System Simulation (NPSS) 1999 Industry Review,’ NASA TM-2000-209795 (2000), p. 7.
[1342] Ann K. Sehra, "The Numerical Propulsion System Simulation: A Vision for Virtual Engine Testing,’ presented at the American Society of Mechanical Engineers TURBO EXPO, Barcelona, Spain, May 8-U, 2006.
[1343] Cynthia G. Naiman and Gregory J. Follen, "Numerical Propulsion System Simulation—A Common Tool for Aerospace Propulsion Being Developed,’ Research and Technology Report 2000 (Cleveland: NASA, 2001).
[1344] Ibid.
[1345] Laurel J. Strauber and Cynthia G. Naiman, "Numerical Propulsion System Simulation (NPSS):
An Award Winning Propulsion System Simulation Tool,’ Research and Technology Report 2001 (Cleveland: NASA, 2002).
[1346] "NPSS User Guide, Software Release: NPSS 1.6.5,’ NASA NPSSUser (2008), pp. 1-1 to 1-2.
[1347] Edward J. Hall, Joseph Rasche, Todd A. Simons, and Daniel Hoyniak, "NPSS Multidisciplinary Integration and Analysis,’ NASA CR-2006-21 3890 (2006).
[1348] Joe Shaw, "Ultra-Efficient Engine Technology Project Continued to Contribute to Breakthrough Technologies,’ Research and Technology Report 2002 (Cleveland: NASA, 2003).
[1349] Lori A. Manthey, "NASA Glenn Research Center UEET (Ultra-Efficient Engine Technology) Program: Agenda and Abstracts,’ NASA RTOP-714-01-4A (2001).
[1350] Manthey, "Ultra-Efficient Engine Technology (UEET) Program,’ Research and Technology Report 2001 (NASA, 2002).
[1351] Ronald C. Plybon, Allan VanDeWall, Rajiv Sampath, Mahadevan Balasubramaniam, Ramak – rishna Mallina, and Rohinton Irani, "High Fidelity System Simulation of Multiple Components in Support of the UEET Program,’ NASA CR-2006-214230 (2006).
[1352] Kathleen M. Tacina and Changlie Wey, "NASA Glenn High Pressure Low NOx Emissions Research,’ NASA TM-2008-214974 (2008).
[1353] Michael T. Tong and Scott M. Jones, "An Updated Assessment of NASA Ultra-Efficient Engine Technologies,’ presented at 17th International Symposium on Airbreathing Engines, Munich, Germany, Sept. 4-9, 2006.
[1354] James A. DiCarlo, Hee Mann Yun, Gregory N. Morscher, and Ramakrishna T. Bhatt, "High – Performance SiC/SiC Ceramic Composite Systems Developed for 1315 C (2400 F) Engine Components,’ Research and Technology Report 2003 (Cleveland: NASA, 2004).
[1355] Cecile M. Burg, Geoffrey A. Hill, Sherilyn A. Brown, and Karl A. Geiselhart, "Propulsion Airframe Aeroacoustics Technology Evaluation and Selection Using a Multi-Attribute Decision Making Process and Non-Deterministic Design," AIAA Paper 2004-4436 (2004).
[1356] Sanjay Garg, "NASA Glenn Research in Controls and Diagnostics for Intelligent Aerospace Propulsion Systems," presented at the Integrated Condition Management 2006 Conference, Anaheim, CA, Nov. 14-16, 2006.
[1357] Mary Jo Long-Davis, "Integrated Components Technology Demonstrations Overview," NTRS Document ID 200.502.14062 (2001).
[1358] Michael T. Tong and Scott M. Jones, "An Updated Assessment of NASA Ultra-Efficient Engine Technologies," ISABE-2005-1 1 63 (2005), p. 3.
[1359] John W. Douglass, "NASA Aeronautics Research Funding: The Wrong Direction," Space News, Mar. 28, 2005, opinion page.
[1360] C. L. Stotler and A. P. Coppa, "Containment of Composite Fan Blades,’ NASA CR-159544 (1979).
[1361] Bob Griffiths, "Composite Fan Blade Containment Case: Innovative Use of Carbon-Fiber Braid Yields a Ductile Structure that Resists Blade Impact,’ High Performance Composites (May 1, 2005).
[1362] Ibid.
[1363] "Damage-Tolerant Fan Casings for Jet Engines,’ Spinoff 2006 (Washington, DC: NASA, 2006), p. 14.
[1364] C. L. Stotler and A. P. Coppa, "Containment of Composite Fan Blades,’ NASA CR-159544 (1979).
[1365] "Damage-Tolerant Fan Casings for Jet Engines.
[1366] Interview of Envia by Jim Banke, Cape Canaveral, Feb. 4, 2009.
[1367] Jeffrey J. Berton, Envia, and Casey L. Burley, "An Analytical Assessment of NASA’s N1 Subsonic Fixed Wing Project Noise Goal," NASA LF99-8609 (2009).
81 . Envia, "Progress Toward SFW N+1 Noise Goal,’ presented at the NASA Fundamental Aeronautics Program 2nd Annual Meeting, Atlanta, Oct. 7, 2008.
[1369] Beth Dickey, "NASA Awards Future Vehicle Aircraft Research Contracts,’ NASA Contract Release C08-60 (2008).
[1370] Don Weir, ed., "Engine Validation of Noise and Emission Reduction Technology Phase 1, NASA CR-2008-215225 (2008).
[1371] Interview of Russell Thomas by Banke, Cape Canaveral, Feb. 4, 2009.
[1372] The Administration’s fiscal year 2010 budget request for NASA is $507 million, compared with the 1998 aeronautics budget of $1.5 billion. Opening Remarks of Senator Barbara Mikulski, Chairwoman of the Senate Appropriations Subcommittee on Commerce, Justice, Science, and Related Agencies. Hearing of the Fiscal Year 2010 Budget Request for NASA. U. S. Congress. May 21, 2009.
[1373] Joseph Chambers, Innovation in Flight (SP-2005-4539), p. 46.
[1374] The author thanks Robert Arrighi, archivist, Wyle Information Systems, History Program at Glenn, for providing instrumental documents, and Air Force Capt. Jarrett S. Lee, for providing insights and support.
[1375] Virginia P. Dawson, Engines and Innovation: Lewis Laboratory and American Propulsion Technology, NASA SP-4306 (1991), ch. 9.
[1376] Neal T. Saunders and Arthur J. Glassman, "Lewis Aeropropulsion Technology: Remembering the Past and Challenging the Future,’ NASA Lewis Research Center, 1991.
[1377] Ibid.
[1378] Ibid.
[1379] Phone interview of Dennis Huff by Caitlin Harrington, Mar. 31, 2009. See also Valerie J. Lyons and Arlene S. Levine, "An Overview of NASA’s Contributions to Energy Technology,’ NASA AIAA – 2008-5641 Jan. 2009).
[1380] Ibid.
[1381] Ibid. See also Arnold Engineering Development Center, Propulsion and Wind Tunnel Facility,
http://www. nimr. org/systems/images/pwt. html accessed July 29, 2009.
1 1 . Statistics available from Energy Information Administration, U. S. Imports by Country of Origin, http://tonto. eia. doe. gov/dnav/pet/pet_move_impcus_a2_nus_epc0_im0_mbblpd_a. htm, accessed July 29, 2009.
1 2. Mark D. Bowles and Virginia Dawson, "The Advanced Turboprop Project: Radical Innovation in a Conservative Environment," From Engineering Science to Big Science, Pamela Mack, ed., (Washington, DC: NASA, 1998), p. 7.
1 3. Ibid.
[1385] General Electric, "Keeping a Bold Promise,’ GE Aviation, Evendale, OH, Sept. 1 2, 1 983.
[1386] "The Energy Conservative Engines Program at Lewis,’ Lewis News, Aug. 3, 1979, History Office archives, NASA Glenn Research Center.
[1387] Lyons and Levine, "An Overview of NASA’s Contributions to Energy Technology."
[1388] Erick M. Conway, High Speed Dreams (Baltimore: Johns Hopkins University Press, 2005),
p. 166.
1 8. Chambers, Innovation in Flight.
[1390] Phone interview with Dan Bulzan, NASA’s Associate Principle Investigator for the Subsonic Fixed Wing and Supersonic Aeronautics Project, by Harrington, Mar. 1 2, 2009.
[1391] International Panel on Climate Change, "Fourth Assessment Report,’ 2007.
[1392] Ibid.
[1393] IPCCs forecasts are based on projections regarding the future economy and the development of new energy-saving aircraft technology, so they are inherently uncertain. See U. S. Government Accountability Office, "Aviation and Climate Change: Aircraft Emissions Expected to Grow, but Technological and Operational Improvements and Government Policies Can Help Control Emissions,’ GA0-09-544 Jan. 2009).
[1394] Phone interview of David Ed Crow by Harrington, Pratt & Whitney Customer Training Center, Hartford, CT, Mar. 27, 2009. For noise concerns related to Advanced Turboprop, see also Bowles and Dawson, "The Advanced Turboprop Project,’ From Engineering Science to Big Science,
Pamela Mack, ed., p. 27.
[1395] Phone interview of John Baughman, General Electric’s Manager of Military Advanced Systems Design, by Harrington, Apr. 24, 2009.
[1396] For example, see U. S. Patent No. 4,550,561, "Method for Improving the Fuel Efficiency of a Gas Turbine Engine,’ Nov. 5, 1985, awarded to NASA Lewis researcher George A. Coffinberry and assigned to the U. S. Government.
[1397] International Civil Aviation Organization, Environment Section: Civil Aircraft Emissions, http:// www. icao. int/icao/en/env/aee. htm, accessed July 29, 2009.
[1398] U. S. Government Accountability Office, "Aviation’s Effects on the Global Atmosphere Are Potentially Significant and Expected to Grow,’ GAO/RCED-00-57 (Feb. 2000) available at http://www. gao. gov/archive/2000/rc00057.pdf, accessed July 29, 2009.
[1399] "The Energy Conservative Engines Program at Lewis,’ Lewis News, Aug. 3, 1979.
[1400] Ibid.
[1401] Ibid.
31 . General Electric, "Keeping a Bold Promise,’ GE Aviation, Evendale, OH, Sept. 1 2, 1 983.
[1403] Jeffrey Ethell, "Fuel Economy in Aviation," NASA SP-462 (1983), p. 42.
[1404] Harrington, Baughman interview.
[1405] Harrington, Crow interview.
[1406] Harrington, Baughman interview.
[1407] Ibid.
[1408] Harrington, Crow interview.
[1409] Ethell, "Fuel Economy in Aviation,’ p. 30.
[1410] Ibid., p. 31-42.
[1411] Harrington, Baughman interview.
[1412] Ibid.
[1413] Harrington, Crow interview.
[1414] NASA, NASA’s High Speed Research Program, http://cea. larc. nasa. gov/PAIS/HSR- Overview2.html, accessed July 29, 2009.
[1415] Ibid.
[1416] Committee on High Speed Research, Aeronautics and Space Engineering Board, Commission on Engineering and Technical Systems, National Research Council, U. S. Supersonic Aircraft: Assessing NASA’s High Speed Research Program (Washington, DC: National Academies Press, 1997), p. 53.
[1417] "Advanced Subsonic Technology Program Plan,’ Office of Aero-Space Technology, NASA (May 1999).
[1418] John Rohde, "Overview of the NASA AST and UEET Emissions Reductions Projects,’ Mar. 1, 2002, http://www. techtransferberkeley. edu/aviation02downloads/JohnRohde. pdf, accessed July 29, 2009.
[1419] Ibid.
[1420] U. S. Government Accountability Office, "Aviation’s Effects on the Global Atmosphere Are Potentially Significant and Expected to Grow."
[1421] "Advanced Subsonic Technology Program Plan."
51 . NASA, "Ultra Efficient Engine Technology Program," June 25, 2001, http://www. grc. nasa. gov/WWW/RT/RT2000/2000/2100shaw. html, accessed July 29, 2009.
[1423] Joe Shaw and Catherine Pettie, "NASA Ultra Efficient Engine Technology Project Overview," NASA Glenn Research Center NASA CP-2004-212963, vol. 1.
[1424] Ibid.
[1425] NASA, Industry Roundtable: Aerospace Industry Enterprise, NASA Headquarters, htp://www. aeronautics. nasa. gov/events/showcase/environ. htm? goto=index. htm, accessed July 29, 2009.
[1426] Ibid.
[1427] Committee on High Speed Research, Aeronautics and Space Engineering Board, Commission on Engineering and Technical Systems, National Research Council, U. S. Supersonic Aircraft: Assessing NASA’s High Speed Research Program (1 997), p. 55.
[1428] U. S. Supersonic Aircraft, p. 54.
[1429] Ibid.
[1430] Harrington, Crow interview.
[1431] Harrington, Bulzan interview.
61 . Bowles and Dawson, "The Advanced Turboprop Project,’ p. 1 0.
[1433] NACA/NASA Research and Development Projects Receiving the RobertJ Collier Trophy, http://history. nasa. gov/Timeline/collierhtml, accessed July 29, 2009.
[1434] Bowles and Dawson, "The Advanced Turboprop Project."
[1435] Edwin J. Graber, "Overview of NASA PTA Propfan Flight Test Program," NASA Glenn Research Center, Nov. 1, 1987, CASI Doc. 19880006423; and B. H. Little, D. T. Poland, H. W. Bartel,
C. C. Withers, and P. C. Brown, "Propfan Test Assessment (PTA) Final Project Report," NASA CR – 185138 (1989).
[1436] Bowles and Dawson, "The Advanced Turboprop Project."
[1437] Harrington, Baughman interview.
[1438] Ibid.
[1439] James J. Haggerty, "Propfan Update,’ Aerospace, fall/winter 1986, pp. 10-1 1.
[1440] Graber, "Overview of NASA PTA’; Harrington, Baughman interview.
[1441] Bowles and Dawson, "The Advanced Turboprop Project.’
71 . Harrington, Crow interview.
[1443] Bowles and Dawson, "The Advanced Turboprop Project.’
[1444] Harrington, Crow interview.
[1445] United Technologies, Inc., Leading Change: The Geared Turbofan Engine, Pratt & Whitney Customer Training Center, Hartford, CT, 2009.
[1446] Harrington, Baughman interview.
[1447] General Electric, "GE Launches Engine Core for New Commercial Airplanes,’ July 1 3, 2008, available at htp://www. businesswire. com/portal/site/home/permalink/?ndmViewid=news_ view&newsId=20080713005020, accessed July 29, 2009.
[1448] Harrington, Huff interview.
[1449] Harrington, Huff interview.
[1450] Chambers, "Concept to Reality: Contributions of the NASA Langley Research Center to Civil Aircraft of the 1990s," NASA SP 2003-4529 (2003), http://oea. larc. nasa. gov/PAIS/ Concept2Reality/composites. html, accessed July 29, 2009.
[1451] Ibid.
[1452] Ibid.
[1453] Ethell, "Fuel Economy in Aviation," p. 59.
[1454] Ibid., p. 71.
[1455] "NASA Technology,’ Dryden Flight Research Center, Oct. 21, 2008, available at http:// www. nasa. gov/centers/dryden/news/X-Press/stories/2008/10_08_technology. html, accessed July 29, 2009.
[1456] Ethell, "Fuel Economy in Aviation,’ p. 77; see also N. A. Radovich, D. Dreim, D. A. O’Keefe,
L. Linner, S. K. Pathak, J. S. Reaser, D. Richardson, J. Sweers, and F. Conner, "Study for the Optimization of a Transport Aircraft Wing for Maximum Fuel Efficiency," vol. 1: "Methodology, Criteria, Aeroelastic Model Definition, and Results," NASA CR-172551 (1985).
[1457] Dryden Flight Research Center, "NASA Technology.’ Whitcomb’s work is thoroughly discussed by Jeremy Kinney in a companion case study.
[1458] Dryden Flight Research Center, "NASA Dryden Technology Facts: Winglets," htp://www. nasa. gov/centers/dryden/about/Organizations/Technology/Facts/TF-2004-15-DFRC. htrril, accessed July 29, 2009.
[1459] Ibid.
[1460] Albert L. Braslow, A History of Suction-Type Laminar Flow Control with Emphasis on Flight Research, Monographs in Aerospace History, No. 1 3 (Washington, DC: NASA History Division, Office of Policy and Plans, NASA Headquarters, 1999), p. 1.
[1461] Dryden Flight Research Center, "Fact Sheet: F-16XL Laminar Flow Research Aircraft,’ updated Mar. 1, 2008, http://www. nasa. gov/centers/dryden/news/FactSheets/FS-023-DFRC. html, accessed July 29, 2009.
91 . Mary L. Sandy and H. Keith Henry, "Flight Tests Prove Concept for Jet Liner Fuel Economy,’ NASA Headquarters Press Release, Aug. 23, 1990, http://www. nasa. gov/home/ hqnews/1990/90-115.txt, accessed July 29, 2009.
[1463] Braslow, A History of Suction-Type Laminar Flew Control with Emphasis on Flight Research, p. 32.
[1464] Dryden Flight Research Center, "Fact Sheet: F-16XL Laminar Flow Research Aircraft.’
[1465] Graham Warwick, "NASA Steps Up Research into Fuel Efficient Aircraft,’ Flight International, June 14, 2007, available at http://www. flightglobal. eom/artides/2007/06/14/214635/ nasa-steps-up-research-into-efficient-aircraft. html, accessed July 29, 2009.
[1466] Warwick, "NASA Pushes Blended Wing/Body," Aviation Week, Jan. 1 3, 2009, available at http://www. aviationweek. com/aw/generic/story.sp? iC=news/BoCy01 1309. xml&headline=NASA%20Pushes%20Bbndecl%20Wing/Body%20Sehannel=spaee, accessed July 29, 2009.
[1467] Travis L. Turner, Randolph H. Cabell, Roberto J. Cano, and Richard J. Silcox, "Testing of SMA-Enabled Active Chevron Prototypes Under Representative Flow Conditions,’ NASA Langley Research Center, Report LAR-17332, Paper 6928-36, CASI Doc. 20080014174 (2008); Vance Dippold, III, "CFD Analyses and Jet-Noise Predictions of Chevron Nozzles with Vortex Stabilization,’ NASA TM-2008-215150 (2008).
[1468] Abe Silverstein and Eldon Hall, "Research Memorandum: Liquid Hydrogen as Jet Fuel for High Altitude Aircraft,’ Lewis Flight Propulsion Laboratory, Cleveland, OH, N63-12541, (Apr. 15, 1955).
[1469] Ibid.
[1470] Donald R. Mulholland, Loren W. Acker, Harold H. Christenson, and William V. Gough, "Flight Investigation of a Liquid-Hydrogen Fuel System," NACA RM-E57F19a (1957).
[1471] Silverstein and Hall, "Research Memorandum: Liquid Hydrogen as Jet Fuel for High Altitude Aircraft."
[1472] John L. Sloop, "Liquid Hydrogen as a Propulsion Fuel," NASA SP-4404 (Washington, DC: NASA, 1978).
[1473] Ibid.
[1474] D. Daggett, O. Hadaller, R. Hendricks, and R. Walther, "Alternative Fuels and Their Potential Impact on Aviation,’ NASA TM-2006-214365 (2006); see also C. G. Jay, "Hydrogen Enrichment of Synthetic Fuel,’ NASA Tech Briefs, vol. 3, no. 1 (June 1, 1978), NTTC Doc. 19780000039.
[1475] Lyons and Levine, "An Overview of NASA’s Contributions to Energy Technology."
[1476] NASA Glenn Research Center Propulsion Systems Division Combustion Branch, updated July 24, 2008, available at http://www. grc. nasa. gov/WWW/combustion, accessed July 29, 2009.
[1477] Sloop, "Liquid Hydrogen as a Propulsion Fuel."
[1478] Harrington, Lyons phone interview, Apr. 27, 2009.
[1479] Anita Liang, Chief, Aeropropulsion Projects Office, "Emerging Fuel Cell Developments at NASA for Aircraft Applications,’ Glenn Research Center, 2003, available at http://www. netl. doe. gcv/publicaticns/prcceedings/03/seca/Anita%20Liang. pdf, accessed July 29, 2009.
[1480] Ibid.
1 10. Boeing, "Boeing Successfully Flies First Fuel-Cell Powered Plane,’ Apr. 3, 2008, http:// www. bceing. com/news/releases/2008/q2/080403a_nr. html, accessed July 29, 2009.
[1482] See, for example, A. L. Nagel, WJ. Alford, and J. F. Dugan, "Future Long-Range Transports: Prospects for Improved Fuel Efficiency,’ NASA TM-X-72659 (1975).
1 1 2. Robert D. Wicofski, "Comparison of Alternate Fuel for Aircraft,’ NASA TM-80155 (Sept. 1979).
[1484] Ibid.
[1485] A plant that produces Fischer-Tropsch synthetic fuel, which is being used by the U. S. Air Force to power jet engines, requires five times the capital costs as an oil refinery. See Gerrard Cowan and Harrington, "Adding Fuel to the Fire: Energy and Defence,’ Janes Defence Weekly, Nov. 21, 2008.
1 15. Harrington, "USAF Promotes Fuel Alternative,’ Janes Defence Weekly, Mar. 16, 2007.
1 1 6. NASA has had a long-standing interest in such research. See, for example, R. Bradford, W. T. Atkins, R. M. Bass, R. Dascher, J. Dunkin, N. Luce, W. Seward, and D. Warren, "Coal Conversion and Synthetic-Fuel Production,’ NASA Tech Briefs, vol. 5, no. 1 (Aug. 1, 1980), p. 56.
1 1 7. Harrington, Bulzan interview.
[1489] Ibid.
1 1 9. President Barack Obama, Remarks by the President at the National Academy of Sciences Annual Meeting, (Washington, DC: Office of the Press Secretary, Apr. 27, 2009). Available at http://www. whitehouse. gov/the_press_ofhce/Remarks-by-the-President-at-therNational-Academy-of- Sciences-Annual-Meeting, accessed July 29, 2009.
1 20. The White House, "NASA Budget Highlights: The National Aeronautics and Space Administration 2010 Budget,’ updated Apr. 28, 2009, available at http://www. nasa. gov/news/ budget/index. html, accessed July 29, 2009.
[1492] Federal Energy Administration, under direction of National Science Foundation, "Project Independence Blueprint,’ Solar Energy PB 248 507 (reproduced by National Technical Information Service, U. S. Department of Commerce, Springfield, VA, Nov. 1974), pp. I-3, I-20-22.
[1493] See Robert W. Righter, Wind Energy in America: A History (Norman, OK: University of Oklahoma Press, 1996), pp. 44-49 and 106.
[1494] Palmer C. Putnam, "Wind Power: Yesterday, Today, and Tomorrow,’ NASA CP-2230 (Proceedings of a workshop sponsored by U. S. Department of Energy, Wind Energy Technology Division, and NASA Lewis Research Center, Cleveland, OH, July 28-30, 1981).
[1495] Righter, Wind Energy in America, pp. 1 26-1 37.
[1496] "MOD-0A 200 Kilowatt Wind Turbine Generator Design and Analysis Report,’ executive summary, DOE/NASA/0163-1; NASA CR-165127; AESD-TME-3051 (Aug. 1980), p. 2.
[1497] In 2007, Purdue University recognized Joseph Savino’s work on wind energy and other accomplishments during his 41 years with NASA by awarding him its Outstanding Mechanical Engineer Award.
[1498] Ronald L. Thomas and Joseph M. Savino, "Status of Wind Energy Conversion,’ NASA TM – X-71 523 (technical paper presented at RANN Symposium Sponsored by the National Science Foundation, Washington, DC, Nov. 18-20, 1973), pp. 1-5.
[1499] R. Thomas, R. Puthoff, and J. Savino, "Plans and Status of the NASA-Lewis Research Center Wind Energy Project,’ (technical paper to be presented at the Joint Power Conference cosponsored by the Institute of Electronic and Electrical Engineers and American Society of Mechanical Engineers, Portland, OR, Sept. 28-Oct. 1, 1975), p. 1.
[1500] Richard L. Puthoff, "Fabrication and Assembly of the ERDA/NASA 100-Kilowatt Experimental Wind Turbine," NASA TM-X-3390 (1976), pp. 1-9; and Thomas, Puthoff, and Savino, "Plans and Status of the NASA-Lewis Research Center Wind Energy Project," pp. 3-4.
[1501] Ronald L. Thomas and Richard M. Donovon, "Large Wind Turbine Generators." NASA TM – 73767 (1978), pp. 3-5.
1 1 . "MOD-0A 200 Kilowatt Wind Turbine Generator Design and Analysis Report,’ executive summary, DOE/NASA/0163-1; NASA CR-165127; AESD-TME-3051 (Aug. 1980), p. 1.
1 2. Louis V. Divone, "Evolution of the Modern Wind Turbine,’ ch. 3, in David A. Spera, ed., Wind Turbine Technology: Fundamental Concepts of Wind Turbine Engineering (New York: ASME Press, 1994) pp. 1 16-117.
1 3. D. A. Spera, L. A. Viterna, T. R. Richards, and H. E. Neustadter, "Preliminary Analysis of Performance and Loads Data from the 2-Megawatt MOD-1 Wind Turbine Generator,’ NASA TM-81408 (1979), pp. 1-3; L. A. Viterna, "The NASA-LeRC Wind Turbine Sound Prediction Code,’ presented at Second DOE/NASA Wind Turbine Dynamics Workshop, Cleveland, Feb. 24-26, 1981.
[1505] Richard R. Douglas, "Large Wind Turbine Design Characteristics and R&D Requirements," NASA CP-2106; DOE Publication CONF-7904111 (workshop held at Cleveland, OH, Apr. 24-26, 1979), pp. 61-65.
[1506] Darrell H. Baldwin and Jerry Kennard, "Development of Large, Horizontal-Axis Wind Turbines, NASA TM-86950 (1985), pp. 3-5 and Table 1.
[1507] Ibid., p. 4; and telephone interview of Larry Viterna by author, Apr. 27, 2009.
[1508] Divone, "Evolution of Modern Wind Turbines,’ ch. 3, in Spera, Wind Turbine Technology, p. 1 30.
1 8. General Electric Company, Advanced Energy Programs Department, "MOD-5A Wind Turbine Generator Program Design Report,’ vol. 1, executive summary, NASA CR-174734 (1984), pp. 1 -6.
[1510] Boeing Aerospace Company, "MOD-5B Wind Turbine System Final Report,’ vol. 1, executive summary, NASA CR-1 80896 (1988), p. 2-2, and vol. 3, "Acceptance Testing,’ NASA CR-
1 80898 (1988), pp. v-vi, 1 -1, 8-1, and B-1.
[1511] Divone, "Evolution of Modern Wind Turbines,’ in Spera, Wind Turbine Technology, pp. 130-131.
[1512] R. R. Douglas, Boeing Engineering and Construction Company, "Conceptual Design of the 7 Megawatt Mod-5B Wind Turbine Generator Final Report,’ N83-19272 (1982), pp. 1-7; and Boeing Aerospace Company, "Mod-5B Wind Turbine System Final Report,’ vol. 3, pp. v, vi, 1-1,8-1, and B-1.
[1513] "Mod-5B Wind Turbine Generator Final Report,’ vol. 1, pp. 7-1 and 7-2.
[1514] Douglass, "Conceptual Design of the 7 Megawatt Mod-5 Wind Turbine Generator,’ p. 6.
[1515] Boeing Aerospace Company, "Mod-5B Wind Turbine System Final Report,’ vol. 1, executive summary, NASA CR-1 80896 (Mar. 1988), p. 8-1.
[1516] Darrell H. Baldwin and Bradford S. Linscott, "The Federal Wind Program at NASA Lewis Research Center,’ NASA TM-83480 (1983), pp. 5-9.
[1517] W. R. Batesole, Kaman Aerospace Corporation, "Fiberglass Composite Blades for the 2 MW Mod-1 Wind Turbine Generator,’ NASA CR-2230, Cleveland, OH, July 28-30, 1981, pp. 215-226.
[1518] Viterna and David C. Janetzke, "Theoretical and Experimental Power From Large Horizontal – Axis Wind Turbines," NASA TM-82944 (Sept. 1982); and "Wind Energy Reaps Rewards," NASA release dated May 31, 2006, http://www. nasa. gov/vision/earth/technolcgies/wind_turbines_ prt. htm, accessed Aug. 20, 2009.
[1519] "ERAST: Environmental Research Aircraft and Sensor Technology,’ NASA FS-2002-08-020 DFRC, pp. 1-3.
[1520] Mishap Investigation Board, "Investigation of the Helios Prototype Aircraft Mishap,’ vol. 1 (Mishap Report), NASA (Jan. 2004), p. 16.
[1521] "Pathfinder Solar-Powered Aircraft’ NASA, Dryden Flight Research Center Fact Sheet, FS-034.
[1522] . "Global Stratospheric Change: Requirements for a Very-High Altitude Aircraft for Atmospheric Research," (workshop held in Truckee, CA, July 15-16, 1989), NASA CP-10041 (1989), p. xi.
[1523] "Global Stratospheric Change,’ workshop held in Truckee, CA, p. 2.
[1524] The ERAST program was the first large NASA program to use a Joint Sponsored Research Agreement. The JSRA type arrangement was first researched as a new form of contracting option in the 1980s at NASA Ames. Ames had previously used this type of joint arrangement on three smaller projects. Jack Glazer, a NASA Ames attorney, started research in 1988 on the possibility of using the "Other Transaction Authority’ clause in the Space Act of 1958 for application to collaborative projects. Glazer recommended creating AmTech as a nonprofit company to document JSRA legal and policy issues and to establish prototype projects. (See "The Promise of ERAST,’ NASA Dryden, Oct. 2004.)
[1525] "Joint Sponsored Research Agreement: Environmental Research Aircraft & Sensor Technology: ‘ERAST Alliance’ for High Altitude, Long Endurance Unmanned Aerial Vehicles,’ (Office of Aeronautics, NASA, Aug. 1994), pp. 1 and 39.
[1526] Ibid. p. 44.
[1527] "NASA Dryden, AeroVironment Sign Solar/Electric Aircraft Pact,’ NASA Dryden News Release 02-48 (Aug. 19, 2002).
[1528] Mishap Investigation Board, "Investigation of Helios Prototype Aircraft Mishap,’ p. 16.
[1529] Alexander Laufer, Todd Post, Edward J. Hoffman, and Ronald A. Heifotz, Shared Voyage: Learning and Unlearning from Remarkable Projects (Washington, DC: NASA History Division, 2005), ch. 4, "Flying High on Spirit: The Pathfinder Solar-Powered Airplane,’ p. 1 25.
[1530] Ibid., p. 130.
[1531] Jay Levine, ed., "The X-Press," vol. 44, issue 2, Dryden Flight Center (May 8, 2002), p. 3.
41 . Levine, ed., "The X-Press," vol. 45, issue 4, Dryden Flight Center (June 2003).
[1533] Laufer, et al., Shared Voyage, section 2, ch. 4, p. 1 29.
[1534] Ibid., p.1 31.
[1535] Derek L. Lisoski and Mark B. Tischler, "Solar Powered Stratosphere Research Aircraft-Flight Test and Systems Identification,’ presented at the RTO SCI Symposium held in Madrid, Spain, May 5-7, 1998, and published in RTO MP-1 1, p. 27-4.
[1536] Laufer, et al., Shared Voyage, section 4, ch. 4, p. 224, and information from John Del Frate.
[1537] Lisoski and Tischler, "Solar Powered Stratospheric Research Aircraft-Flight Test and Systems Identification,’ pp. 27-1 through 27-5; and "Pathfinder Solar-Powered Aircraft,’ NASA Dryden Flight Research Center, FS-034.
[1538] Review comments of Del Frate to author, Aug. 4, 2009.
[1539] As Del Frate recalls: "Flight termination can vary from aircraft to aircraft. We chose to not cripple the aircraft if we had a problem, but rather we would cut power to the motors and use a small chute off-center to provide asymmetrical drag to put PF into a descending spiral in order to not destroy the aircraft. As a result, the wind aloft could carry us quite a ways downwind."
[1540] Del Frate and Gary B. Cosentino, "Recent Flight Test Experience with Uninhabited Aerial Vehicles at NASA Dryden Flight Research Center," NASA TM-1998-206546 (Apr. 1998), p. 5.
[1541] Ibid.
[1542] . "NASA Dryden Fact Sheet-Pathfinder Solar-Powered Aircraft,’ Dryden Flight Research Center, FS-034, pp. 2-3.
[1543] See, for example, "Pathfinder Solar-Powered Aircraft Begins Science Missions,’ NASA Release: 97-45, http://www. nasa. gov/centers/dryden/news/NewsReleases/1997/97-45. html, accessed Aug. 20, 2009.
[1544] Stephen S. Wegener and James Brass, "Environmental Research Aircraft and Sensor Technology-New Technologies for Earth Science,’ Earth Science Enterprise, Atmospheric Chemistry and Dynamics, p. 177.
[1545] S. M. Schoenung and S. S. Wegener, "Meteorological and Remote Sensing Applications of High Altitude Unmaned Aerial Vehicles,’ presented at the Fourth International Airborne Remote Sensing Conference and Exposition/21st Canadian Symposium on Remote Sensing, Ottawa, Ontario, Canada, June 21-24, 1999, sections 1 .0 ("Introduction”) and 2.0 ("Applications’).
[1546] Del Frate, e-mail to author, Aug. 4, 2009.
[1547] See "Originating Technology/NASA Contribution,’ pp. 66-67, Environment and Resources Management.
[1548] Michael A. Dornheim, "The Quest for Perpetual Flight: Special Fuel Cells Key to Months-long Flight,’ Aviation Week & Space Technology (Feb. 28, 2000), pp. 58-61; telephone interview of Del Frate by author (Apr. 27, 2009), along with followup e-mail.
[1549] Dornheim, "The Quest for Perpetual Flight,’ Aviation Week & Space Technology, pp. 58-61 .
[1550] Telephone interview of Del Frate by author (Apr. 2, 2009), and followup e-mail.
60. "Centurion,’ NASA Dryden Flight Research Center Fact Sheet FS-056.
[1552] . NASA never tested the Helios configuration (both HP-01 and HP-03) at Edwards, only testing Centurion. (Information from Del Frate, Aug. 4, 2009.)
[1553] "Helios Prototype,’ Dryden Flight Research Center Fact Sheet FS-068.
[1554] John D. Hunley and Yvonne Kellogg, compilers, Proceedings of addresses, sessions and workshops of the NASA ERAST Exclusive Preview sponsored by NASA Dryden Flight Research Center, Edwards, CA, Oct. 13, 1999, ERAST: Scientific Applications and Technology Commercialization (Sept. 2000), p. 4.
[1555] Ibid., p. 6.
[1556] Mishap Investigation Board, "Investigation of the Helios Prototype Aircraft Mishap,’ passim.
[1557] Ibid., p. 45.
[1558] Ibid., pp. 10, 54, 87-89, and Table 10.1.
[1559] Ibid., pp. 10, 89, and Table 10-1. Both HP-01 and HP-03 had a total of five under-wing pods; the HP-03 configuration replaced the original center pod with the fuel cell pod.
[1560] Ibid., p. 10.
[1561] D. J. Bents, "Solar Airplanes and Regenerative Fuel Cells,’ presentation to the 43rd annual I. R.I. S. show in Mayfield Heights, OH, Oct. 9, 2007.