From the Martin Marietta post-flight report: "The actual flight environment in the area of the modified ventral fin proved to be much more severe than anticipated. The condition was directly attributable to interaction effects of the shock waves generated by the dummy ramjet, the ventral, and the pressure probes. The ablator applications in this area were inadequate to protect the structure under these flow conditions, and the vehicle suffered localized damage in the area."!330!
The flight had completely eroded the ablator application, including both the molded leading-edge detail and the sprayed MA-25S layer, from the forward portion of the ventral. The vehicle skin sustained major damage due to the excessively high heating in the shock impingement, which burned through at the leading edge and on the sides of the ventral at the torque box assembly. This also damaged the torque box and destroyed the wiring and pressure lines in the forward compartment.-!3331
A study of the thermocouple responses in the area of the ventral indicated that the ablator had provided at least some protection for the first 140 seconds of flight. Continual erosion of the ablator surfaces was occurring during this period, and by approximately 160 seconds the degradation was such that all protection broke down. The ablator materials should have had zero surface recession, but instead eroded away. The particles from the forward sections of ablator, in turn, caused severe impact erosion of the downstream ablator layer. The lower speed brakes were bare of ablator, and the material on the inboard edges of the main landing skids and the undersides of the side fairings experienced considerable abrasion.[352]
Otherwise, the ablator had performed well enough. The flight had uniformly charred the details over the leading edges of the wings, horizontal stabilizers, canopy, and dorsal stabilizer along their lengths. All of the parts had retained their shape, and the char layer attachment was firm. There were some signs of localized surface melt in areas of shock impingement during peak heating, but because of a continually varying velocity during the flight, shock presence in any one area was limited and the degradation was "insignificant." The nose-up trim attitude degraded the lower surface of the wing details more heavily than the upper surfaces; the reverse was true for the horizontal stabilizers.-1353
The lower, fixed portion of the dorsal stabilizer leading edge charred more heavily than the upper, movable rudder, and some evidence of unsymmetrical heating of the rudder was present, with the left side sustaining a higher heat load. The ablator details for both vane antennas were heavily charred and experienced local erosion or spallation of the char from their surface. They looked worse than they were; measurements showed that more than half an inch of ablator remained on the antennas, which were undamaged in any case.[354]
The sprayed MA-25S layer over the fuselage and side fairings showed varying degrees of effects. Thermal degradation, with the resultant reticulation of the ablator surface, occurred only on the forward areas of the nose. Ablator fissuring extended along the fuselage belly to approximately the forward vane antenna. The ablator on the crown of the fuselage and the belly aft of the vane antenna showed no evidence of thermal exposure.[355]
Engineers could easily correlate the varying amounts of charring experienced over the fuselage with their location or proximity to the various design features of the airplane. For instance, heavily charred areas were directly behind the pressure orifices in the ball nose. These openings were apparently sufficient to "trip" the flow, causing a rapid transition to turbulent boundary-layer conditions. The holes for the ballistic control-system thrusters greatly increased heating effects in their vicinity. Localized stagnation within the recesses apparently permitted burning of the ablator, evidenced by a surface discoloration. The thickness of the material behind the nose-gear door was seriously degraded.-1356
The various stacks and vents protruding from the airplane caused localized heating problems. Stagnation shock and trailing-wake damage were evident downstream from an external tank disconnect door that failed to close after the tanks were jettisoned. The ablator surface on the lower wing experienced varying degrees of charring over the whole area. This was heaviest adjacent to the molded leading edges, and some blistering was evident near the wing tips. However, the upper wing surfaces thermally degraded only near the leading edge details; the remainder of the surface was unaffected. Again, the ablator on the upper surface of the horizontal stabilizers degraded more heavily than the lower surfaces. Along the inboard edge of the stabilizers, next to the side fairings, sections of ablator were missing from both the top and bottom surfaces, forward of the torque tube. The open cavity of the stabilizer’s inboard closing rib and the adjacent fairing formed a channel to trap the airflow during flight. This resulted in severe heating within the cavity and caused degradation of the ablator from the back face.[357]
In addition to the thermal degradation, the stabilizer upper surfaces sustained a significant amount of impact damage. Some of the abrasions obviously occurred during landing since the exposed ablator was virgin material, while others had occurred early in flight and the exposed ablator had become charred. Engineers thought the likely cause was spallation of small pieces of upstream ablator of fluid droplets from the various vents and drains. As expected, ablation residue partially covered the unprotected right-hand windshield.13581
Pull tests were conducted at random locations on the surface of the ablator to determine whether it was still well bonded to the airplane. The results were generally acceptable. In the end, Martin Marietta believed that the ablator "performed satisfactorily except in the area of the modified ventral fin." Nevertheless, Martin went on to suggest a series of minor modifications that would solve some of the problems experienced on these two flights.-13591
The ablator obviously was not completely successful. Unexpectedly, the ablator actually prevented cooling of the airframe by preventing heat from absorbing into the underlying hot structure. The post-flight condition of the airplane was a surprise to Jack Kolf, an X0-15 project engineer at the FRC, who noted, "If there had been any question that the airplane was going to come back in that shape, we never would have flown it."13601
Engineers had not fully considered possible shock interaction with the ramjet shape at hypersonic speeds. As it turned out, the flow patterns were such that a tremendous shock wave impinged on the ramjet and its supporting structure. Researchers later estimated that the heat in the ventral stabilizer was 10 times higher than normal. The warning signs had been there in various wind – tunnel tests and previous flights, but researchers had not recognized them.13611
It is interesting to note that post-flight photographs of the X-15A-2 damage normally highlight two areas. The first is the ventral stabilizer and ramjet. Heating effects unquestionably damaged this area, although there had been indications on the previous flight that something was not right. The second area shown is the large fissures around the nose. When NASA replaced the ball nose before this flight, it used an outdated batch of MA-25S because it was all that was available. Although its application characteristics, cure rate, and appearance were the same as those of the "fresh" ablator used elsewhere, thermal exposure resulted in a greater shrink rate than the newer material. This produced much more pronounced fissuring, but it appeared that the ablator provided sufficient protection.13621
The original contract with Martin Marietta indicated the company was responsible for "touching up" the ablator twice to allow three flights with the initial application. The damage sustained by the ventral stabilizer precluded the aircraft from flying again in the near future. Consequently, the Air Force directed Martin to remove the ablator so that it could return the aircraft to North American for inspection and repair. NASA technicians under the direction of a Martin engineer, however, performed the actual removal. The technicians removed the MA-25S-1 strips from the service panel peripheries, cleaned the panel edges, and then applied polyethylene tape to protect the aircraft interior from contamination. They stripped the ablator layer using plexiglass scrapers and scrubbed the surface to remove all residual ablator material. The final cleaning was performed with aluminum wool and nylon pads with powdered cleanser, and wooden toothpicks proved useful for dislodging the ablator material from skin gaps and the heads of permanent fasteners.13631
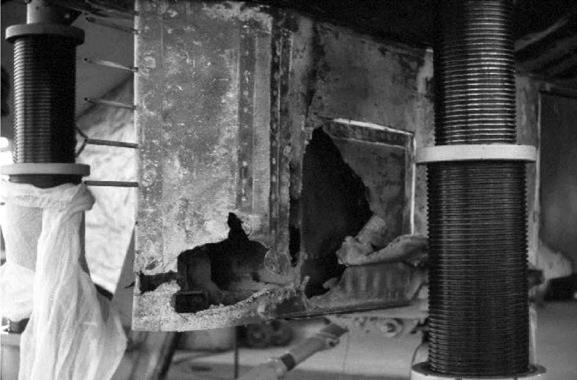
|
This is the ventral stabilizer after Flight 2-53-97; the ramjet had fallen off during landing. The X – 15A-2 skin sustained major damage due to the excessively high heating in the shock impingement, which burned through at the leading edge and on the sides of the ventral at the torque box assembly. This also damaged the torque box and destroyed the wiring and pressure lines in the forward compartment. (NASA)
NASA sent X-15A-2 to North American for repair and general maintenance. The airplane returned to Edwards on 27 June 1968, and a series of nondestructive load and thermal tests on the instrumented right wing began on 15 July in the FRC High Temperature Loads Calibration Laboratory. As it turned out, the airplane would never fly again.-1364-
Some of the problems encountered with the ablator were non-representative of possible future uses. North American had designed the X-15 with an uninsulated hot structure, but researchers expected to design any future vehicle with a more conventional airframe that would eliminate some of the problems encountered on this flight. However, other problems were very real. The amount of time it took to apply the ablator was unacceptable. Even considering that after they gained some experience the technicians could cut the application time in half or even more, the six weeks it took to coat the relatively small X-15 bode ill for larger vehicles.-1365-
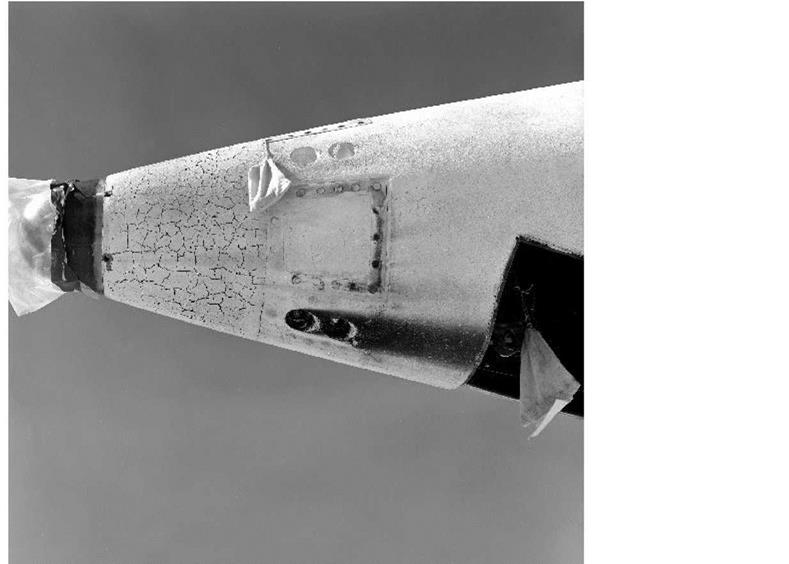
|
This is the nose of X-15A-2 after Flight 2-53-97. NASA had replaced the ball nose before this flight because of a maintenance issue, and had used an outdated batch of MA-25S to patch the area because it was all that was available. Although its application characteristics, cure rate, and appearance were the same as the "fresh" ablator used elsewhere, thermal exposure resulted in a greater shrink rate than the newer material. This produced much more pronounced fissuring, but analysis indicated that the ablator provided sufficient protection, despite appearances. (NASA)
The use of an ablative coating on X-15A-2 came at an interesting time. The development of what became the space shuttle was just beginning, with various study efforts being initiated under the auspices of NASA and the Air Force. It was obvious that some sort of reusable thermal protection system was going to be required on a space shuttle, and a great deal of attention initially turned to ablatives because they were the most mature technology available at the time. The experience with the X-15 provided very meaningful insights into the problems that the space shuttle undoubtedly would have encountered using this technology. Nevertheless, various contractors continued to propose the use of ablators on their space shuttle concepts, in decreasing quantity, until 1970 when several forms of ceramic tiles and metal "shingles" became the preferred concepts. Based at least partially on the results of the X-15 tests, the space shuttle program decided to go down a different road; whether that road was truly superior is open to debate. At least it represented a different set of problems.
At 10:30:07.4 on 15 November 1967, X-15-3 dropped away from the NB-52B 45,000 feet over Delamar Dry Lake. Major Michael J. Adams was at the controls, making his seventh X-15 flight. Adams had spent slightly over 23 hours in the fixed-base simulator practicing this particular mission (3-67-95), which was intended to evaluate the Ames boost guidance display and conduct several experiments, including measuring the ultraviolet plume of rocket exhausts at high altitude. About 1 minute after launch, as X-15-3 passed through 85,000 feet, an electrical disturbance caused the MH-96 dampers to trip out. It was later determined the disturbance most probably had emanated from electrical arcing in the experiment in the nose of the right wing-tip pod that was being flown for the first time. Adams reset the dampers and continued.-366
As planned, Adams switched the cockpit sideslip attitude indicator to an alternate display mode. One of the more controversial aspects of the attitude indicator was a second use for the crosspointers, which were developed late in the program to allow precise pointing of several experiments. In this mode the cross-pointers displayed vernier attitude errors (pitch error on the alpha needle, and bank error on the beta needle). A switch allowed the pilot to control the display mode. During the climb, the pilot switched the display to the vernier-attitude-error mode, and would normally have switched back to the sideslip mode prior to reentry.367-
Unlike the other two airplanes, X-15-3 automatically blended the ballistic control-system thrusters with the aerodynamic controls as needed using the right side stick, allowing the pilot to largely ignore the dedicated ballistic controller on the left. The electrical disturbances fooled the flight-control system into believing that the dynamic pressure was higher than it actually was, resulting in the system failing to engage the ballistic control system as would normally occur at high altitude. Adams felt the lack of response as the airplane approached maximum altitude and began using the left side stick to operate the thrusters. Unfortunately, Adams reverted to flying the vertical needle on the attitude indicator as if it were still showing sideslip instead of its actual vernier-attitude-error display.366
Pete Knight was NASA-1 on the ground. As the X-15 climbed after engine shutdown, Adams initiated a wing-rocking maneuver to sweep the ultraviolet plume experiment up and down across the horizon. Because Adams was apparently interpreting the attitude indicator incorrectly, he began rocking the wings excessively. After Adams stopped the wing rocking, the X-15 began to drift toward its peak altitude, flying with a 15-degree sideslip to the right. As Adams descended, the drift began again and X-15-3 yawed at a right angle to the flight path. The airplane entered a hypersonic spin as it encountered rapidly increasing dynamic pressure at 130,000 feet.369
The designers of the NASA control room had not thought to provide a heading indication, so the controllers were unaware of the attitude of the airplane. Everybody knew the ball nose did not accurately align with the relative wind at altitudes above 250,000 feet, so there was little concern when the angle of attack and angle of sideslip began drifting off nominal values near peak altitude. In reality, the airplane was yawing wildly, eventually turning completely around. Fifteen seconds later Adams reported that the airplane "seems squirrelly" and at 1034 hours he advised, "I’m in a spin, Pete." Adams radioed again, "I’m in a spin," followed by groans as the pilot was subjected to heavy accelerations. Engineers knew very little about the hypersonic spin characteristics of the X-15, and there was no recommended spin recovery technique.-1370-
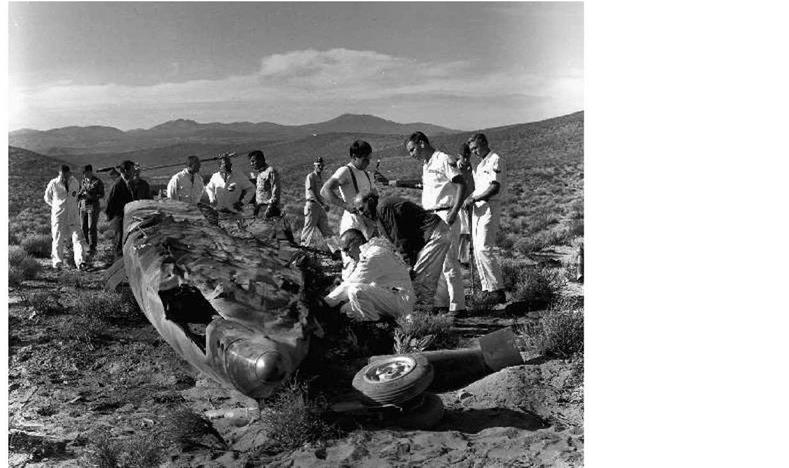
|
At 10:30:07.4 on 15 November 1967, X-15-3 dropped away from the NB-52B 45,000 feet over Deiamar Dry Lake with Major Michael J. Adams at the controls. Technical problems combined with possible piloting issues caused the X-15-3 to break-up at approximately 62,000 feet with a velocity of about 3,800 fps and a dynamic pressure of 1,300 psf. The wreckage fell near Johannesburg, California. (NASA)
Realizing that X-15-3 would never make it back to Rogers Dry Lake, the chase pilots-Hugh M. Jackson and Bill Dana-shoved their F-104s into afterburner and raced for Ballarat and Cuddeback, the most likely emergency landing lakes. In the X-15, Adams used the combined power of the aerodynamic and ballistic controls against the spin. Eventually, largely through a weathervane effect, the airplane recovered at 120,000 feet and 140 psf. It then entered an inverted Mach 4.7 dive at an angle of nearly 45 degrees. At this point, it looked like Adams might pull out of the dive. However, a technical problem emerged as the MH-96 entered a limit-cycle oscillation when the airplane emerged from the spin. This prevented the system from reducing the pitch gain in response to the increasing dynamic pressure. While descending at over 2,700 fps, the X-15 began to exhibit an increasingly severe rapid pitching motion. The severe oscillations in the flight – control system effectively blocked pilot inputs. As it passed through 65,000 feet, X-15-3 was descending in an inverted dive at Mach 3.93 and approaching both the side-load and normal-load limits. At 1034:57.5, the airplane broke up at approximately 62,000 feet with a velocity of about 3,800 fps and a dynamic pressure of 1,300 psf. An Air Force pilot spotted the wreckage near the town of Johannesburg. Mike Adams was dead, and X-15-3 was destroyed.-1371!
accident, an unofficial search party from the FRC found the cockpit camera but not the film cartridge. Since the film cassette was lighter than the camera, engineers theorized that the cassette must have been blown north by winds at altitude. A search party organized by Victor Horton converged on the area on 29 November, and Willard E. Dives found the cassette. The film was flown to the EG&G laboratory in Boston for processing.
Johnny Armstrong and Jack Kolf began analyzing the cockpit film when it returned. Armstrong later recalled, "We had the time history from the flight recorded in the control room. We could see the vertical needle on the attitude indicator in the film and correlated the time of the film and the recorded time history. It became clear to us that the pilot was making manual ballistic inputs as if the vertical needle was sideslip rather than roll angle. His inputs were in the correct direction to make sideslip zero if it had been sideslip. However since it was roll angle his inputs drove the nose further from away from the flight path and eventually into… a spin."372
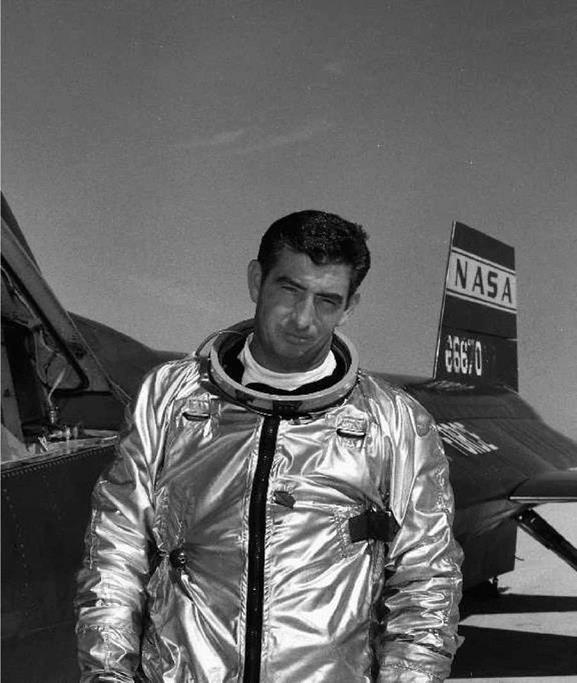
|
Mike Adams flew the X-15 for 13 months from 6 October 1966 until 15 November 1967, making seven flights. All of these were with the XLR99 engine and he reached Mach 5.59, a maximum speed of 3,822 mph, and an altitude of 266,000 feet. Adams died on Flight 3-65-97. The Air Force posthumously awarded Mike Adams an astronaut rating for his last flight in X-15-3, which had attained an altitude of 266,000 feet (50.38 miles). This was the only fatality during the program’s 199 flights. (NASA)
The accident board concluded that Adams misinterpreted his instruments, and combined with distraction and possible vertigo, this led him to allow the heading of the X-15-3 to deviate unexpectedly. The overall effectiveness of the MH-96 had been degraded by the electrical disturbance early in the flight, further adding to the pilot’s workload. The MH-96 then caused the airplane to break up. The board made two major recommendations: install a telemetered heading indicator in the control room, visible to the flight controller, and medically screen X-15 pilot candidates for labyrinth (vertigo) sensitivity. Because of the crash, NASA added an attitude indicator in the control room to display real-time heading, pitch, roll, sideslip, and angle-of – attack information. Although it was not specifically called out in the accident report, many engineers came away with a more important lesson: do not use the same instrument to display multiple different indications in a high-workload or high-stress environment.-1373
The Air Force posthumously awarded Mike Adams an astronaut rating for his last flight in X-15- 3, which had attained an altitude of 266,000 feet (50.38 miles). This was the only fatality that occurred during the program’s 199 flights.-1374!