However, North American was becoming concerned about the engine development effort, echoing many of the same concerns expressed by John Sloop at the NACA. At the 1956 industry conference, North American vice president Raymond H. Rice announced that the XLR99 was four months behind schedule.
The Air Force and Reaction Motors held meetings on 12 and 18 February, and the Air Force, the NACA, North American, and Reaction Motors met on 19 February. Data presented at these meetings confirmed that the engine was approximately four months behind schedule and overweight. Although the performance estimates were decreasing, the deterioration appeared to be relatively minor. General Estes wrote Hugh Dryden (and copied Rice) that "every effort will be expended to prevent further engine schedule slippage."*461
The NACA’s reaction to the February meeting was different. Hartley Soule reported that the Air Force accepted the four-month delay, but that Reaction Motors would deliver two engines by 1 September 1958 instead of one. The Air Force also accepted a decrease from 241 to 236 seconds of specific impulse, and a weight increase from 588 to 618 pounds. Soule pointed out that Reaction Motors had not yet conducted any thrust-chamber tests, and expressed doubt that the revised schedule was achievable. He also noted that the Air Force had scheduled additional engine progress meetings for June and September. On the other hand, the NACA agreed to help Reaction Motors optimize the engine nozzle for high-altitude operations in an attempt to recover some performance. Separately, on 29 March 1957 the X-15 Project Office reported that engine costs had increased to an estimated $14,000,000, plus fee.*471
Unfortunately, Hartley Soule’s premonitions proved correct. Reaction Motors informed the Air Force on 10 July 1957 that a nine-month schedule slip would be necessary to meet the February specifications. In addition, the development would cost $21,800,000-a 50% increase in only 100 days. Alternately, for $17,000,000 Reaction Motors could develop a compliant engine within the established schedule if the weight could be increased to 836 pounds from the original 618 pounds. Representatives from the Air Force, the NACA, North American, and Reaction Motors met at Wright Field on 29 July to discuss alternatives. The participants generally considered the performance penalty a lesser concern than the increased cost and schedule slip needed to develop the "specification" engine, and the Air Force elected to pursue the heavier engine. Reaction Motors mitigated some concerns when it subsequently reported that the turbopump was exceeding its performance goals, allowing a 197-pound reduction in hydrogen-peroxide propellant. In effect, this resulted in an engine that was only 51 pounds heavier than the original 588-pound specification.
Unfortunately, serious problems arose during development of the thrust chamber and injector assemblies. Primarily, the oxidizer tubes of the spaghetti-type injector tended to burn through at low thrust levels. The Air Force encouraged the company to redouble its efforts, but agreed to raise the minimum thrust requirement if necessary. The Air Force and Reaction Motors also discussed changing to a spud-type injector, but did not reach a final decision.*481
Despite the increase in weight, the engine program continued to fall behind. On 11 December 1957, during a meeting at the newly formed Propulsion Laboratory, the company reported an additional six-month delay.*491 Reaction Motors attributed this to an explosion that destroyed the first developmental engine, and a series of turbopump failures. The company also confirmed that it had failed to develop a spaghetti-type injector that met the performance and reliability requirements. Overall, the picture was rather bleak.
The spaghetti-type injector consisted of bundled tubing, with each metal tube going to an individual fuel injector. However, Lieutenant K. E. Weiss, the XLR99 project engineer for the Power Plant Laboratory, designed a spud-type injector that used small, perforated disks instead of tubes. Wright Field machine shops built several of the Weiss designs, and researchers ran preliminary tests in early 1958. By March, Reaction Motors was investigating using the spud-type injector on the XLR99.
The mounting engine delays were beginning to threaten the entire X-15 project. In response, WADC commander Major General Stanley T. Wray and Brigadier General Haugen ordered an investigation of the technical and managerial problems. On 7 January 1958, the Air Force asked Reaction Motors to provide a revised schedule and explain how it would correct the various problems. The company submitted the schedule in mid-January, showing a new five-month delay and an increase in costs to $34,400,000-nearly double the July estimate.-1501
Accompanied by personnel from the X-15 Project Office and Propulsion Laboratory, generals Haugen and Wray visited Reaction Motors on 28 January 1958 to discuss the various concerns. Haugen commented on the company’s poor record of accomplishment up to that time, which was especially troubling given the importance of the X-15 project. Reaction Motors admitted to its "past deficiencies" and assured the generals that it could meet the current cost and schedule estimates. Haugen and Wray left only partly convinced.-1511
The Propulsion Laboratory and the X-15 Project Office reported their recommendations to the ARDC and WADC commanders in mid-February, and to the director of research and development in Air Force Headquarters, Major General Ralph P. Swofford, Jr., on 21 February 1958. These recommendations included continuing the Reaction Motors development program, using XLR11 engines for initial X-15 flights, approving overtime, assigning the project a top Department
of Defense priority (DX rating), establishing a Technical Advisory Group, and initiating an alternate engine development program.
Of these recommendations, the Air Force approved the use of XLR11 engines, an increased Reaction Motors effort, additional funds to cover the increased effort, and the establishment of the advisory group. The XLR11 decision hardly came as a surprise to the engineers at the HSFS and Lewis-they had suggested the same thing nearly three years earlier, as had some at Wright Field. Officials at Air Force headquarters denied the request for a top priority, although they approved a slightly improved priority. The X-15 Project Office postponed the decision concerning the development of an alternate engine, and made it clear that there was a clear distinction between proposals for an interim engine for the initial flight tests and an alternate engine to replace the XLR99 in the final X-15.1521
North American had already investigated the idea of installing a pair of XLR11s at the suggestion of L. Robert Carman. Scott Crossfield was not impressed with the idea and said, "I think we’d be making a big mistake." Crossfield was afraid that once the Air Force approved the change, the troublesome larger engine would never be installed, leaving the X-15 a Mach 3+ airplane instead of one twice that fast. Charlie Feltz and Harrison Storms, however, thought the concept had merit. The XLR11 used liquid oxygen, like the XLR99, so the oxidizer tank required no changes. The smaller engine used alcohol instead of ammonia, but the two liquids were roughly comparable and only minor changes were necessary. Feltz, for one, was slightly relieved: "I’ve been a little concerned about busting into space all at once with a brand-new airplane and a brand-new untried engine…. We’re trying to crack space, with a new pressure suit, reentry, new metal, landing—everything at once. I’ve got a real good buddy [Crossfield] who’s going to be flying that airplane for the first time, and I’d just as soon have him around for a while." After a few weeks, even Crossfield came around: "We should learn to crawl before we enter the Olympic hundred – yard dash." Once the government approved the concept of using XLR11s, the technicians at Edwards began assembling a dozen XLR11s from pieces and parts of various XLR11 and LR8 engines left over from previous programs.1531
The recommendations also resulted in the establishment of a Technical Advisory Group consisting of representatives from the ARDC, BuAer, NACA, and WADC. The first meeting was held at the Reaction Motors facility on 24 February 1958, and the group immediately determined that the thrust chamber was the item that could benefit the most from this advice, since it represented the greatest risk.-54
In addition to the Technical Advisory Group, the government enlisted the help of other rocket engineers to develop an alternate thrust chamber. North American, which owned Rocketdyne, was reluctant to become involved given its role as the X-15 airframe contractor. Eventually, however, generals Wray and Haugen convinced Lee Atwood to allow Rocketdyne to assist Reaction Motors and begin development of an alternate thrust chamber and injectors. Once North American overcame its corporate reluctance, Rocketdyne immediately began adapting the thrust chamber and injector from the Atlas ICBM XLR105-NA-1 sustainer engine to the XLR99.[55]
An additional complication soon developed, although it apparently did not significantly affect the development effort; Reaction Motors and the Thiokol Chemical Corporation began merger negotiations in the early part of 1958. During this period the anticipated reorganization undoubtedly created a distracting uncertainty among Reaction Motors management and employees. Reaction Motors Incorporated (RMI) stockholders approved the merger on 17 April 1958, and the company subsequently became the Reaction Motors Division (RMD) of Thiokol Chemical Corporation.-1561
The Air Force decision to bring Rocketdyne into the fray motivated Reaction Motors to consider alternate designs. However, by the end of April the Air Force acknowledged there were not sufficient funds to develop alternate designs from Rocketdyne and Reaction Motors. Believing that the Rocketdyne XLR105 derivative offered the best chance of success, the Powerplant Laboratory urged Reaction Motors to subcontract with Rocketdyne for its development. Reaction Motors evaluated which design offered the most promise and presented the results at a meeting of Reaction Motors, Rocketdyne, NACA, and WADC representatives on 27 May 1958 at Wright Field. The participants concluded that the Reaction Motors concentric shell thrust chamber would not solve the chamber burnout issue, and Reaction Motors did not believe it could complete the design in time to support the flight program in any case. Since this was obviously not acceptable, all parties agreed that Reaction Motors should discontinue its efforts and subcontract with Rocketdyne for the XLR105 derivative. Two days later the Air Force officially transmitted the 27 May decisions to Reaction Motors.-1571
The next day Reaction Motors and Rocketdyne agreed that $500,000 would fund the development effort through mid-July. Rocketdyne estimated it would cost $1,746,756 to develop the alternate thrust chamber. Producing 14 chambers for initial testing would cost $811,244, and 14 flight chambers would add $657,300.[58]
Despite the appearance of progress, neither the Air Force nor the NACA was completely happy with the progress of the engine development effort. The Propulsion Laboratory prepared two letters intended to provide additional motivation for Reaction Motors. The first was from General Wray to General Anderson, dated 17 June 1958:[59]
For some time, General Haugen and I have been concerned by the poor progress made by Reaction Motors Division on the development of the XLR99 rocket engine for the X-15 airplane program. This engine was one that had been recommended…on the strength of a supposed advanced state of development of the LR30 rocket engine.. In spite of this state of development, Reaction Motors Division has experienced continual schedule slippage and financial overruns.. It is by their own admission, as well as the conclusions of our project engineers, that Reaction Motors Division has used poor judgment and management during the early stages of the engine development program. Inability to meet performance and original Preliminary Flight Rating Test initiation date, which was a contractor deficiency, has resulted in submission of supplemental proposals. This by acceptance or rejection has placed the Air Force in the undesirable position of making program decisions which we would have preferred the contractor, through better management, to have made at a much earlier date.
Wray also wrote a second letter addressed to Thiokol president Joseph W. Crosby, but felt it would have more impact if Anderson signed it. Anderson shortened the four-page draft to two pages before he sent it to Crosby on 27 June. Anderson had tempered Wray’s adversarial tone somewhat, but still left little doubt that the Air Force was upset. The letter implied, but never explicitly stated, that cancellation of the entire contract for nonperformance was an option. In retrospect, it was high unlikely that the Air Force would ever have taken such drastic action since it likely would have spelled the end of the X-15 program as well.[60]
It is difficult to determine whether the letters, or even the implied threat to cancel the Reaction Motors contract, had any effect on the program. Regardless, things began to improve. Test engines at Lake Denmark accumulated more firing time during the first two weeks of July than during the entire program to date. The tests showed that performance was somewhat low, but by 7 August 1958, engine performance increased to within 2.5% of the specification. Of course, the "specification" had and would change over the course of the contract, as illustrated below:[61]
|
Proposal
|
Specification 91F
|
Specification 91M
|
February 1956
|
June 1958
|
March 1961
|
Maximum thrust at 45,000 feet (lbf)
|
57,000
|
57,000
|
57,000
|
Minimum thrust at 45,000 feet (lbf)
|
19,500
|
19,500
|
31,500
|
Specific impulse at sea level (sec)
|
241
|
238
|
230
|
Specific impulse at 45,000 feet (sec)
|
278
|
272
|
265
|
Engine dry weight (pounds)
|
540
|
856
|
910
|
Engine wet weight (pounds)
|
625
|
990
|
1,025
|
Although the maximum thrust remained constant, the decrease in specific impulse along with the increased weight had serious performance implications for the X-15. The change in the minimum thrust had less effect, and greatly simplified the development effort, but even so, the flight program seldom used low throttle settings.
By August it was obvious that Rocketdyne had been rather optimistic. At this point the Reaction Motors subcontract with Rocketdyne had already cost $3,125,000-almost double the original estimate. The Propulsion Laboratory believed this was unreasonable given that the original premise was that the XLR105 was a well-established design that needed only minor changes to adapt it to the XLR99. There had been so little progress that the Propulsion Laboratory suggested the Rocketdyne effort be canceled "as soon as possible."*62*
A meeting held at Reaction Motors on 15 August 1958 included Hartley Soule, Brigadier General Haugen, Brigadier General Waymond A. Davis, and representatives from Air Force Headquarters, the ARDC, and the WADC. Reaction Motors and Rocketdyne provided briefings on the status of their respective efforts, and the participants agreed to freeze the engine design using the Reaction Motors thrust chamber. Reaction Motors was encouraged to continue making minor changes to the injector in an attempt to improve performance, but was cautioned not to delay the schedule or to sacrifice reliability. Surprisingly, given the Propulsion Laboratory’s recommendation, the group postponed making any decision on the Rocketdyne effort until October.*63*
Reaction Motors made encouraging progress during September as the company continued to test the engine and injectors. The Rocketdyne program, however, failed to make any significant contributions, primarily because the company could not figure out how to mate its thrust chamber with the Reaction Motors ignition system. The X-15 Project Office conceded that the Rocketdyne effort was an "expensive and apparently fruitless" activity.*641
On 7 October 1958, the Technical Advisory Group reviewed the engine programs and concluded that although the Rocketdyne effort might offer higher performance at some point in the future, Reaction Motors was well on its way to producing an acceptable engine that would be available sooner. As a result, on 10 October 1958 the Propulsion Laboratory again recommended terminating the Rocketdyne effort, but this time Headquarters WADC and the X-15 Project Office agreed. Reaction Motors subsequently terminated the Rocketdyne subcontract.*651
Development progress continued at a reasonable pace during the remainder of 1958, despite several failures. For instance, Reaction Motors traced a destructive failure on 24 October to components that had already been recognized as inadequate. Since Reaction Motors was already redesigning the parts, the Air Force did not consider the failure significant.*66*
Despite the best efforts of all concerned during 1958, problems remained at the beginning of 1959. At a 20 January meeting of the Technical Advisory Group, Reaction Motors admitted the engine still suffered from injector failures at low power settings, excessive heat buildup during idle, and minor leakage from various components. A few days later, on 23 January, excessive vibration in a test engine at Lake Denmark resulted in a fuel-manifold failure. Despite the seemingly long list of deficiencies, it was apparent that the development effort would ultimately produce an acceptable engine.*67*
Static testing of prototype XLR99s and associated systems took place at the Reaction Motors facility in Lake Denmark, New Jersey. The test program used four test stands: three at Lake Denmark and stand E1 at the Picatinny Arsenal. The largest stand (R2 at Lake Denmark) was set up to test a complete aircraft system, including a structurally accurate aft fuselage, at all attitudes. Stands R2W and R3 at Lake Denmark were capable of horizontal firing only. The former was used for durability testing and environmental testing, and the latter was used for delivery acceptance tests because it was equipped with an elaborate thrust-vector mount. The test area at Lake Denmark contained support facilities with a storage capacity of 30,000 gallons of liquid oxygen, 18,000 gallons of anhydrous ammonia, and 4,000 gallons of hydrogen peroxide.
Reaction Motors began engine-system testing during the fall of 1958, and by the beginning of 1959 eight flight-representative engines were undergoing some level of testing. Engine run time progressed consistently, and the engines accumulated approximately 340 minutes of operation during the first quarter of 1959. Various components logged even greater run times, with the thrust chamber accumulating nearly 1,800 minutes and the turbopump over 4,200 minutes. The oxidizer pump, loosely based on the oxidizer pump used on the XLR30, operated at approximately 13,000 rpm. The fuel pump operated at 20,790 rpm and was essentially identical to the XLR30 unit. Each pump generated nearly 1,500 horsepower and had an output pressure of approximately 1,200 psi. The combined oxidizer/fuel flow rate at maximum thrust was 13,000 pounds per minute, exhausting the 18,000-pound propellant supply in 85 seconds.
The company finally reached a long-sought goal on 18 April 1959 when the first XLR99 completed its factory acceptance tests. This was the engine scheduled for use in the formal preliminary flight rating test (PFRT), which was based on an MIL-E-6626 modified to include "man-rating" requirements,. The completion of the PFRT series formed the basis of the engine’s approval for use in the X-15. The PFRT began the same day the factory acceptance tests were completed, and ran through 5 May 1960. The tests used four engines on test stands R2 and R3 at Lake Denmark, and E1 at Picatinny. Additional component tests took place at the Reaction Motors Component Laboratories and the Associated Testing Laboratories in Cadwell, New Jersey. Reaction Motors personnel conducted all of the tests under the watchful eye of Air Force engineers and inspectors. Captain K. E. Weiss, the XLR99 project engineer, was present for about half of the tests.[68]
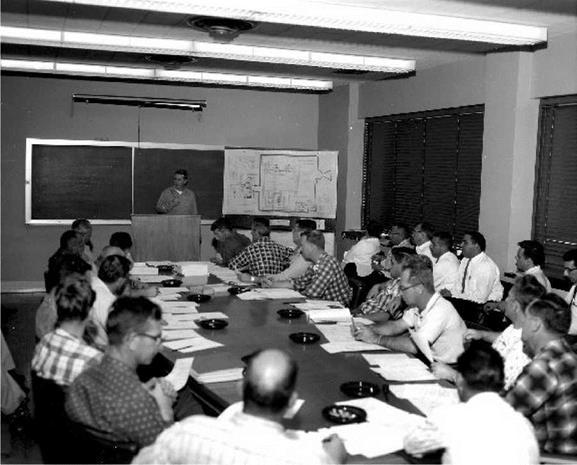
|
The XLR99 was a great deal more complicated than the XLR11 engines used in most other X – planes. Reaction Motors conducted training classes for the Air Force and NASA personnel who would be responsible for operating and maintaining the engines at Edwards AFB. This was long before computer-aided instruction had even been dreamed of, and the classes were conducted using mimeographed course material and chalkboards. (U. S. Air Force)
In order to obtain a high level of confidence in the service life of the engine, the Air Force required two engines to each accumulate 60 minutes of operational time. Some of the tests were challenging: "[T]he engine shall be run at thrust levels of 50,000, 37,500, and 25,000 pounds for the corresponding durations of 87, 110, and 156 seconds. In addition, one run will be made at 90% of minimum thrust for 170 seconds duration and one run at 110% of maximum thrust for 80 seconds duration." In addition, to demonstrate the "all attitude" capability, an engine performed a series of tests while being fired with the thrust vector 90 degrees up and also 30 degrees down.1691
Unfortunately, the PFRT got off to a somewhat less than ideal start. The PFRT began with engine 012 performing the attitude test series. After it successfully completed nine 90-degree tests, Reaction Motors repositioned the engine for the 30-degree nose-down test. After several runs, a faulty weld in the second-stage igniter liquid-oxygen feed line developed a leak that resulted in a fire. The damage to the engine caused Reaction Motors to withdraw it from the test program for extensive repairs. To prevent further occurrence of this type of failure, engineers redesigned the igniter line to eliminate the weld, and the company revised its weld inspection program. The redesigned igniter line subsequently accumulated 1 hour of operation in engines 012 and 102 without incident. Since the original engine had not completed the 30-degree test series, all of those tests were repeated using engine 102.1701
Another problem was more serious, and continued throughout the flight program. During the PFRT, approximately 80 square inches of the Rokide Z171 ceramic coating used to insulate the firing chamber peeled off from engine 014. A heat-transfer analysis indicated that the loss of the Rokide coating would not produce a chamber burn-through, but the engineers did not understand why it came off. However, the engine successfully completed its 1 hour of operation, so Reaction Motors revised the acceptable Rokide loss specification based on this performance. Other problems included a transient vibration problem during start that could not be isolated. Fortunately, the built-in vibration cutoff circuit demonstrated that it would shut down the engine before a hazardous condition developed, and restarting the engine after the cutoff was usually successful. The test series experienced a variety of other minor problems, mostly resulting from faulty welds in various components, such as the turbine inlet and exhaust cases. The Air Force did not believe any of these were serious enough to terminate the tests or reject the engine.-1721
Reaction Motors conducted over 200 successful firings during the test program, accumulating 146 minutes of main chamber operation. In the end, one engine ran for 64 minutes and 100 starts; another ran for 65 minutes and 137 starts. The 231 seconds of specific impulse was 7 seconds below specification, but the engine met all other requirements. Engineers explained the low specific impulse by noting that "to expedite the development program, injector design was frozen before the optimum design was achieved." However, nobody expected the slight reduction in specific impulse to have any particular effect on the X-15 program.1771
Reaction Motors subsequently demonstrated the engine’s durability by accumulating more than 60 minutes of operating time on two different engines. One engine fired 108 times without having any more than routine maintenance. In addition, a series of 93 tests demonstrated that the engine would react safely under imposed malfunction conditions, and 234 engine tests demonstrated performance and safety requirements. Of these, 192 were full engine-firing demonstrations, and the remaining 42 were safety-limit tests that did not require thrust-chamber
operation. The PFRT cleared the engine to operate between 50% and 100% of full thrust. Testing continued, however, and the Air Force subsequently cleared the engine to operate at 30% of full thrust, meeting the initial contract specification.-1741
It is interesting to note that early in the proposal stage, North American determined that the aerodynamic drag of the X-15 was not as important a design factor as was normally the case with contemporary jet-powered fighters.-75 This was largely due to the amount of excess thrust expected to be available from the engine. Engineers considered weight the largest driver in the overall airplane design. Only about 10% of the total engine thrust was necessary to overcome drag, and another 20% was required to overcome weight. The remaining 70% of engine thrust was available to accelerate the X-15.76
At the time it was built, the XLR99 was the largest man-rated rocket engine yet developed. Of course, this would soon change as the manned space program accelerated into high gear. The 915-pound XLR99 could produce 50,000 pounds of thrust (lbf) at sea level, 57,000 lbf at 45,000 feet, and 57,850 lbf at 100,000 feet. The nominal oxidizer-to-fuel ratio was 1.25:1, and the engine had a normal chamber pressure of 600 psi. Playing with the oxidizer-to-fuel ratio could slightly increase the thrust, and the amount of thrust varied somewhat among engines because of manufacturing tolerances. Some engines produced over 61,000 lbf at specific altitudes. The engine had a specific impulse of 230-lbf-sec/lbm at sea level and 276-lbf-sec/lbm at 100,000 feet. The engine was throttleable from 30% to 100%, although the first couple of engines were limited to 50% on the low end until early 1962. Even after Reaction Motors modified the engines and the Air Force approved the use of 30% thrust, a high vibration level meant that they were operationally restricted to no less than 40% thrust. The amount of available propellant was all that limited the duration of any given run. Reaction Motors estimated the service life (mean time between overhaul) of the engine at 1 hour or 100 starts.77