Scaled Composites took what it described as an advanced all-composite design approach to building the rocket engine. “We did develop a new configuration of hybrid rocket motor,” Rutan said. “And we patented it. The patent is related to the fact that the whole motor cantilevers off the tank. And doesn’t require additional mounting and doesn’t build up stresses because of the temperature effects and the aerodynamic loads. It’s a key reason that this remains a very simple motor.
“During our development of the new hybrid rocket motor,” Rutan added, “Scaled contracted with four companies to provide components.” Most of the rocket engine was designed and developed in-house, though.
The two main parts of the rocket engine are the oxidizer tank and the integrated case/throat/nozzle (CTN), as shown in figure 5.5 and figure 5.6, respectively.
The oxidizer tank is a very important structural element of the rocket engine and SpaceShipOne as a whole. It is reusable and is bonded to the inside of the fuselage, all the way around, with an elastomeric
Г – ^
Fig. 5.5. This oxidizer tank stored the liquid nitrous oxide (N20). After the tank was filled, it self pressurized, so a pump was not needed to inject the oxidizer into the fuel. The photo shows the inner liner of the oxidizer tank. Mojave Aerospace Ventures LLC, photograph by David M. Moore
compound. The bond is damage tolerant and isolates vibration, and because of the size of the bond area, the loading due to the force from the rocket engine is distributed over a large area.
The oxidizer tank has a fiberglass liner and two titanium interface flanges, fore and aft. After pressure testing the liner, Scaled Composites contracted Thiokol to provide a graphite/epoxy overwrap using a filament-wrap process, which can be seen in figure 5.7.
The CTN is mounted directly on the rear flange of the oxidizer tank with bolts and an О-ring seal (refer to figure 5.8).This cantilever mounting requires no other additional support, and, by design, reduces the number of potential leak paths.
( >
Fig. 5.6. The CTN (case/throat/nozzle) was a large composite casing
filled with synthetic rubber used as fuel. Once the rocket engine was ignited, the exhaust moved through the casing, was compressed by the throat, and then expelled out the nozzle. Mojave Aerospace Ventures LLC, photograph by Scaled Composites
V__________________________________________ J
r ; ^
Fig. 5.7. The oxidizer tank had a special composite overwrap that allowed it to contain the oxidizer at a high pressure of 750 pounds per
square inch (psi). It was permanently bonded to the inside of the fuselage, so it was also an important structural member. Mojave Aerospace Ventures LLC, photograph by Scaled Composites

|
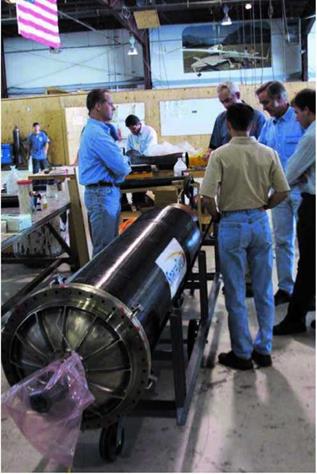
г
Fig. 5.8. The CTN attached directly to the oxidizer tank. This photograph shows the mounting ring used to bolt it on. The hybrid design allowed the fuel and oxidizer to be very close together, which reduced the overall complexity of the rocket engine. Mojave Aerospace Ventures LLC, photograph by David M. Moore
V_________________________________________
The 22-inch – (56-centimeter-) diameter case of the CTN, where the combustion occurs, is essentially a hollow tube lined with the rubber fuel. The throat forced the hot exhaust gases, passing from the case to the nozzles, to converge. The nozzle accelerated the hot exhaust gases to provide even greater thrust. The silica/phenolic high-temperature insulating liner and mounting rings of the case were assembled together with the throat and nozzle using graphite/epoxy composite overwrap. The cantilevered mounting also provided the advantage of being able to vary the length and diameter of the CTN without design modifications.
A safety feature was built into the CTN to warn of an impending burn-through. If the fiber-optic cable sealed between the liner and the overwrap detected a breach in the liner, the flow of oxidizer would be cut off and the rocket engine shut down. As an additional precaution, wires wrapped around the outside of the CTN could also be used to detect a burn-through.
AAE Aerospace supplied an ablative nozzle with an expansion ratio of 25:1 for the CTN. The expansion ratio compares the size of the throat to the size of the nozzle’s opening. The efficiency is altitude dependent, so this ratio gave SpaceShipOne the maximum thrust at launch altitude. The interior of the nozzle eroded away as the rocket engine burned, which helped to minimize the temperature of the nozzle itself.
The entire CTN had to be replaced after each spaceflight.
Scaled Composites looked to outside vendors to supply the remaining components for the rocket engine, which included the injector, the igniter, and the related controls and plumbing. Scaled Composites held a competition of its own to build these components.
Rocket-Engine Competition
Simplicity of design by reducing the number of parts is best illustrated by an experience Rutan had during his preliminary research into rocket-engine designs. Representatives of a rocket – engine vendor Rutan was visiting wanted to demonstrate how
Г
Fig. 5.9. At the front of the oxidizer tank are the fill, vent, and dump valves. The vent valve protects from over-pressurization, and the dump valve allows the tank to be drained in an emergency situation. Mojave Aerospace Ventures LLC, photograph by David M. Moore
their valve worked after showing him schematics and describing their engine design. They went out to the back of the building, where the valve was chilled with liquid nitrogen to a cryogenic operating temperature.
“The valve stuck,” Rutan said. “It didn’t work. It failed right there while I was looking at it.”
After they went back inside, he said to them, “Gentlemen, let me ask you, how many of those valves are in this motor?”
Twelve, they replied.
“Did you expect this to work today?” he asked.
There was no answer. Rutan knew enough about rocketry to know if there was such a thing as a simple one that operated at room temperature with one valve, that’s the one he wanted.
Rutan had been looking at more than twenty rocket-engine vendors. With the help of Tim Pickens, a bit of a maverick rocket expert, Rutan sketched up the design and passed it on. “I had sent them a sanitized requirement that didn’t divulge that we were doing manned flight. I said it was a reusable sounding rocket.”
Now, it was necessary to build the remaining engine components. In front of the oxidizer tank was the fill, vent, and dump system as well as the forward tank bulkhead. This was how the liquid nitrous oxide was added to the tank, how pressure was relieved in case of over-pressurization, and how the nitrous oxide could be drained in an emergency situation. These components were kept away from the hot side of the oxidizer tank to improve safety. The locations of these components are shown in figure 5.9.
Arguably the most critical valve of the whole project was the main control valve that supplied the oxidizer to the CTN. Without
the flow of nitrous oxide, there would be no rocket. So, this valve received special attention. Doug Shane cleverly named it the “oxy – no-more-on” valve. Connected to the oxy-no-more-on valve was the injector, which was essentially a showerhead that sprayed the liquid nitrous oxide into the CTN. Both the oxy-no-more-on valve and the injector were located inside the oxidizer tank. What this did was further reduce plumbing and had the added benefit of keeping these components at a constant temperature, which also simplified things. Figure 5.10 shows their positions from a rear view of the oxidizer tank.
The rear tank bulkhead, motor controller, head insulation, and igniter still needed to be built as well. The igniter was the heat source that initiated the reaction between the oxidizer and rubber fuel. The last part that remained was the actual rubber fuel itself, which had to be packed into the CTN.
From the list of more than twenty potential rocket-engine vendors, it came down to two: Environmental Aeroscience Corporation (eAc), of Miami, Florida, and SpaceDev, of Poway, California. This wasn’t a low-bid process. It was performance-based, and the competition would go back and forth. Rutan thought that having just one vendor try to make the last of the components was too much of a risk. “When you sole source, if they stumble, you have to pay them to pick up,” Rutan said. “If you’ve got two of them competing and they stumble, they spend their own money to catch up. That’s what the big ‘C’-word is—competition. And that happened. They both wanted to fly.”
In the middle of 2001, both vendors began to participate in a ground-test program that included cold flow tests, where the oxidizer and fuel weren’t ignited, as well as partial – and full-duration

Г Л
Fig. 5.10. The CTN mounted on a titanium flange at the rear of the oxidizer tank. Located inside the tank was the main control valve, also known as the "oxy-no-more-on" valve, that released the oxidizer into the CTN. Mojave Aerospace Ventures LLC, photograph by David M. Moore
v__________________ J
г

Fig. 5.11. The test stand trailer (TST) was used during the rocket – engine test firings. It contained all of the same components and systems to be used in SpaceShipOne, including an oxidizer tank that the CTNs were mounted onto. Mojave Aerospace Ventures LLC, photograph by David M. Moore
r ; л
Fig. 5.12. To fill SpaceShipOne or the TST with the oxidizer, nitrous oxide (N20), Scaled Composites used a special tanker truck called the mobile nitrous oxide delivery system (MONODS). Mojave Aerospace Ventures LLC, photograph by David M. Moore
V_______ )
hot-firings. All rocket engine testing employed the same type of components used in SpaceShipOne. Shaking out the full-scale designs on the ground at a Scaled Composites test site rather than in flight was a much more preferable way to address the “ups”—break up, burn up, and blow up.
In terms of experience, eAc had built a lot of hybrid rocket engines and had run some with diameters of up to 16 inches (41 centimeters). SpaceDev, on the other hand, had only run little hybrids with 15 pounds-force (67 newtons) of thrust.
This meant eAc was off to a quick lead. By June of 2002, the first set of results came in. Scaled Composites selected eAc as the supplier of the front-end propulsion components. However, both vendors continued to develop the remaining rocket-engine components.
To run all the rocket-engine tests, the test stand trailer (TST), a partial, operational mockup of SpaceShipOne shown in figure 5.11, acted as a portable test bed. It comprised the complete rocket engine, including the CTN and oxidizer tank, and the forward section of the fuselage. The TST provided instrumentation to analyze vibration, temperature, and stress conditions that the flight components would face during spaceflight. It also had load cells, which were sensors mounted on the trailer, that allowed engineers to evaluate the rocket – engine performance.
Setup for rocket-engine tests typically took several days. Since the TST was mobile, preparations began inside a hangar at Scaled Composites. Once the CTN was in place and all the other components were hooked up, the TST was towed out to the firing range. Figure 5.12 shows the specialized tanker truck called the mobile nitrous oxide delivery system (MONODS) that then fills the oxidizer tank.
Mission Control ran the rocket-engine tests remotely, and an underground computer near the TST collected and transmitted live data. The countdown procedures for the ground testing are listed in table 5.1.
Since testing occurred on the ground, a nozzle with an expansion ratio of 10:1 was used, as opposed to 25:1 used for actual flights.
SpaceDev had fired first, a 15-second burn on November 21, 2002. The rocket roar was deafening for each hot-fire of the rocket engine. The ground shook. Figure 5.13 shows the tip of a fiery plume stretched out more than thirty feet, scorching the ground and sending smoke billowing across the desert.
“The SpaceDev motor was the only one that had a critical safety issue. In the first round, a valve wouldn’t close and it keep burning and burning,” Rutan said. Although Scaled Composites was slow to extinguish the fire, no significant damage occurred.
After more than nine months of firing rocket engines, the gap between eAc and SpaceDev had disappeared. Each had little differences. For example, SpaceDev used four ports to flow the oxidizer into the CTN, whereas eAc used just one, and they each had a proprietary rubber fuel and system for refueling the CTN. But both had exceeded performance expectations.
With the exception of the fire caused by a stuck valve at the very onset of test firing, the hybrid rocket engine demonstrated safety and reliability. The cantilever mounting concept proved structurally sound, the oxidizer and CTN performed as designed, and the “ups” were avoided altogether.
Scaled Composites had both companies commit prices for components, not only for the upcoming flight test and Ansari X Prize rocket engines, but for twenty-two other rocket engines slated for what was called Task 21, the spaceflights after the Ansari X Prize attempts.

Table 5.1 Rocket Engine Test Countdown
(source: Mojave Aerospace Ventures LLC, provided courtesy of Scaled Composites)
|
|
T-48 hours Mounting the CTN
The fully fueled CTN (engine) and valve are mounted to the oxidizer tank using the mounting trolley. Alignment is checked and bolts are tightened to the specified tolerances.
T-36 hours Instrumentation and Integration
The motor controller, pressure bottles, actuation valves, and all the sensors are installed and tested on the test bed. New CTNs require new temperature and strain sensors, while CTNs being fired for the second or third time are "plug and play."
T-24 hours Moving Time
The test trailer with the fully fueled CTN (engine) is moved from Scaled’s hangar to the test site. There it is bolted down, final instrumentation is completed, and the system is connected to Mission Control.
T-4 hours Filling the Tank
Nitrous oxide is transferred from the MONODS to the oxidizer tank on the test trailer after it has been brought up to temperature and pressure. Temperatures and pressures must be carefully controlled to ensure a safe transfer.
T-0 hours The Final Countdown
After final system checks have been made, cameras have been started, and range safety has been checked, a quick countdown is called and the switch is thrown. The motor controller automatically ignites and fires the engine for a preprogrammed period of time.
“SpaceDev’s components were lighter, which helped our performance,” Rutan said. “Keep in mind, we knew that we had to have really the best performance in order to win the X Prize because we had a weight growth. So, we needed all the performance we could get. SpaceDev’s components had a little more efficiency, on the order of three percent for the same weight of propellant.”
SpaceDev actually turned out to be cheaper, too—all characteristics Rutan was very fond of. In September of 2003, the development phase of SpaceShipOne’ s rocket engine was completed. SpaceDev got the nod.
Figure 5.14 shows a rocket engine installed in SpaceShipOne without the fairing in place, so the unsupported ended of the CTN is apparent.