The RLA’s LOX/kerosene engines were to be the first such engines developed under Glushko in almost 15 years. In the mid to late 1950s Glushko had supervised the development of the RD-107/RD-108 engines for the R-7 missile and derived launch vehicles (sea-level thrust around 80 tons) and the RD-111 for the R-9ICBM (sea-level thrust 144 tons). All of these were four-chamber LOX/kerosene engines using an open combustion cycle, in which the gases used to drive the turbopumps are vented overboard. This system is also known in Russian terminology as “liquid-liquid”, because both the fuel and the oxidizer are injected into the combustion chamber in a liquid state. However, the development of the RD-111 was plagued by serious problems, including high-frequency oscillations in the combustion chamber, intermittent combustion, and the need to protect the chambers and nozzle walls from overheating.
In the early 1960s Glushko turned his attention to closed-cycle engines, in which the gases used for driving the turbines are routed to the combustion chamber to take part in the combustion process. This, together with the increased chamber pressure, produced much higher specific impulses than had been obtained earlier. One of the propellants entered the combustion chamber in a liquid form and the other in a gaseous form (which is why this system is also called the “gas-liquid” system by the Russians). Given the painful experience with the RD-111, Glushko was wary of using LOX/kerosene for these even more powerful engines. Instead, he decided to con-
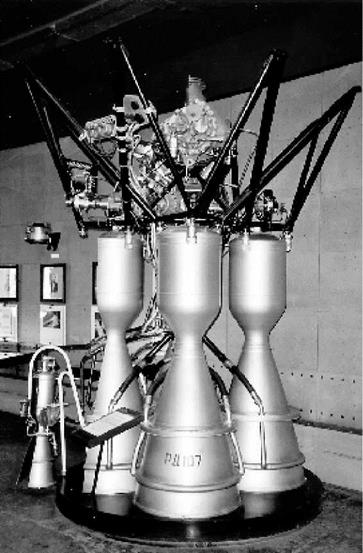
The RD-107 LOX/kerosene engine (B. Hendrickx).
|
centrate on storable propellants based on unsymmetrical dimethyl hydrazine (UDMH), which he had already mastered while developing open-cycle engines for the R-12, R-14, and R-16 missiles. In fact, Glushko’s preference for storable over cryogenic propellants can be traced back all the way to his years as a rocket pioneer at the GDL and RNII rocket research institutes in the 1930s.
All this had dire implications for the N-1 program. Glushko’s reluctance to build closed-cycle LOX/kerosene engines and Korolyov’s refusal to use the highly toxic
storable propellants for the rocket effectively ended the cooperation between the two chief designers. It forced Korolyov to rely on LOX/kerosene engines of the much less experienced OKB-276 Kuznetsov design bureau in Kuybyshev (which actually were of the closed-cycle type).
For the remainder of the 1960s, Glushko was mainly engaged in building closed – cycle engines with storable propellants for a variety of missiles and launch vehicles of the Chelomey and Yangel bureaus. Except for the R-7 derived rockets, all Soviet space launch vehicles that were operational around the turn of the decade (Kosmos, Tsiklon, Proton) were powered by such engines. They had been derived from nuclear missiles, which traditionally use storable propellants to enable them to be launched at short notice.
Energomash didn’t end its boycott on LOX/kerosene engines until the late 1960s, by which time enough experience had been gained with the closed-cycle combustion principle for engineers to feel confident enough to apply it in powerful LOX/kerosene engines. An opportunity to build such an engine arose in 1969, when the Chelomey bureau drew up plans for a mammoth rocket called UR-700M, intended to send Soviet cosmonauts to Mars. One version of the rocket that Chelomey looked into would have 600-ton thrust LOX/kerosene engines in the first and second stages. In 1970 Glushko’s engineers worked out plans for such an engine called RD-116 or 11D120, which presumably was a modified LOX/kerosene version of the singlechamber RD-270, a hypergolic engine earlier planned for Chelomey’s (unflown) UR-700 Moon rocket [31]. Although the UR-700M remained no more than a fantasy, Energomash was reportedly also ordered to investigate the possibility of using the same engine on the first stage of the N-1, which had suffered two launch failures in 1969. A small cluster of RD-116 engines would be enough to replace the N – 1’s thirty NK-15 first-stage engines [32].
In the end the idea was dropped because it would also have implied a radical redesign of the N-1 rocket. However, it does seem to have whetted Glushko’s appetite to continue studies of such engines, the more so because a new policy was emerging in the early 1970s to abandon storable propellants in favor of cryogenic and hydrocarbon propellants in new, dedicated space launch vehicles.
As a result, work on high-thrust LOX/kerosene engines at Energomash resumed in earnest in 1973. The studies focused not only on standard kerosene, but also an advanced synthetic hydrocarbon fuel known as tsiklin or sintin. Based on furfural and propylene, it had a higher specific impulse than ordinary kerosene, but was also much more expensive.
In the course of 1973 proposals were presented for single-chamber, two-chamber, and four-chamber versions of a 500+ ton thrust LOX/kerosene engine. There was serious debate between the proponents of the single and four-chamber versions, which both had their advantages and drawbacks. A key meeting at Energomash in the second half of 1973 opted for the four-chamber version. After all, Energomash had had experience with multi-chamber engines since the 1950s. Furthermore, there had been numerous problems with the development of the 640-ton single-chamber RD-270 for the UR-700. Finally, by using four smaller combustion chambers it would be easier to test them by modifying test models of existing combustion chambers for storable propellants. The meeting also approved a so-called “modular design” for the engines, making it possible to use them in a standardized fleet of rockets [33].
Still, all these were no more than internal decisions within Energomash that didn’t stand much chance of being implemented until the bureau merged with TsKBEM to form NPO Energiya in May 1974 and Glushko got the opportunity to advance his RLA idea. But even at this stage there was no consensus what the LOX/kerosene engines should look like. Some of the disagreements centered around such things as the pressure in the combustion chamber and the type of combustion cycle. Some claimed the pressure in the combustion chamber shouldn’t exceed 200 atmospheres, making the engine more reliable. However, a lower pressure translates into bigger combustion chambers and less payload, and the compromise reached was to have a pressure of 250 atmospheres. Others felt the engine should use a fuel – rich combustion cycle, lowering the risk of turbopump burn-throughs. That was countered by the argument that an oxidizer-rich preburner engine is more efficient and easier to reuse because it leaves behind less soot residue [34].
There was also more fundamental debate over the thrust of the engine. Some felt that the task of building a four-chamber engine with a single, powerful turbopump assembly was too challenging and instead preferred single-chamber engines in the 150-ton thrust range with smaller, individual turbopumps. In other words, rather than having a handful of very powerful engines, it would be better to install a large number of low-thrust engines [35]. One concern with the high-thrust engines was that they would expose the rocket to serious vibrations in case of a sudden emergency shutdown, making it necessary to strengthen the rocket’s structure and lower its payload capacity [36].
Bearing in mind these two schools of thought, two design departments at Energomash got down to studying engines in two thrust classes. Department 729 focused on engines ranging in thrust from 112.5 to 263.5 tons: the RD-128, RD-129, and RD-124 for the first stage of the RLA family and the RD-125, RD-126, and RD-127 for the second and third stages. Department 728 initially concentrated on an engine with a phenomenal thrust of 1,003 tons (the RD-150), but then scaled back its ambitions to a 600-ton thrust engine called RD-123 [37]. This is the engine that finally got selected in 1975 for use in the first stage of the Soviet space shuttle stack and the progenitor of the eventually developed RD-170. A determining factor in this choice must have been the negative experience of flying many low-thrust engines on the first stage of the N-1. Moreover, Glushko must have feared that if the choice did fall on the low-thrust engines, there would have been attempts to de-mothball the Kuznetsov bureau’s N-1 engines rather than introduce his new LOX/kerosene engines. However, the debate would flare up again in the early 1980s when the RD-170 was plagued by serious development problems (see Chapter 6).