One of the more intriguing forms of aircraft propulsion is the ducted fan: the fan enclosed within a ring and powered by a drive train from an engine typically located elsewhere in the aircraft. Researchers interested in V/STOL flight expended great effort on ducted-fan approaches, and indeed, such an approach is incorporated on the Joint Strike Fighter, the Lockheed Martin F-35 Lightning II. Though ducted-fan propulsion for Conventional Take-Off and Landing aircraft had enjoyed at best a mixed record, those advocating it for V/STOL applications were hopeful it would prove more successful. Ducted-fan options included pivoting fans that could furnish direct lift, like tilt rotors, then pivot to furnish power for wing-borne forward flight, or rely on horizontal fans in a wing or fuselage to generate vertical lift, or combinations of these.
Ducted-fan aircraft intended for conventional flight were tried in many nations. Likewise, ducted-fan V/STOL adherents in various countries had proposed concepts for such craft. But the first two American ducted-fan V/STOL airplanes—that is, ducted-fan aircraft with wings, as opposed to various Hiller and Piasecki flying platforms—were the Doak Model 16, designated the VZ-4, and the Vanguard Omniplane. Each represented a different approach, though, of the two, only the Doak flew.[1401]
The Doak began as an Army research project, first flying in February 1956. A pleasing and imaginative design of conventional straight wing aerodynamic layout, it had a single 860-horsepower Lycoming YT53 turboshaft engine driving two pivoted ducted fans on the wingtips. During hover, variable inlet guide vanes in the ducts furnished roll control, with pitch and yaw control provided by vectored jet exhaust from
a variable tail nozzle. The Doak proved that its design approach worked, readily making vertical descents, transitions to conventional flight, and transition back to hover and landing, accelerating in just 17 seconds from 0 to 200 knots. It arrived at the NACA’s Langley laboratory in September 1957. Testing revealing a mix of undesirable handling qualities across its flight envelope, with one subsequent NASA study concluding that it
suffered from low inherent control power about all axes, sensitivity to ground-effect disturbances, large side forces associated with the large ducts, and a large (positive) dihedral effect which restricted operation to calm-air conditions and no crosswinds. No large STOL performance benefit was evident with this design.[1402]
During vertical descents, it buffeted with alternate left-and-right wingdropping. This became so severe as the plane approached stall angle that "roll control was not adequate to keep the aircraft upright,” noted pilot Jack Reeder. Large nose-up pitching moments required careful speed and duct-angle management to prevent duct-lip airflow stalling. In hover, the inlet guide vanes were "very inadequate.” In ground effect, Reeder noted:
if lifted clear of the ground by several feet, uncontrollable yawing and persistent lateral upsetting tendencies have been encountered. With the weak yaw control and, particularly the weak roll control, the unindoctrinated pilot may find himself unable to control the aircraft.[1403]
The Doak Company closed in 1960, and NASA retired the airplane in 1972. By that time, a ducted-fan successor, the Bell Aerospace Textron X-22A, was already flying. Far more unconventional in appearance than was the Doak, it nevertheless owed a technical debt to the earlier design. As NASA researchers had concluded from the VZ-4’s testing, the little Doak had "indicated the feasibility as well as the inherent problems of the tilt-duct concept, which helped the X-22 design which followed.”[1404]
Bell Aerospace Textron’s X-22A grew out of company studies in the mid-1950s. Successive examination of Bell-proposed military concepts led to increasing service interest by the Navy, Air Force, Marine Corps, and Army for a range of transport, rescue, and counterinsurgency applications. In late 1962, the U. S. Navy signed a development contract with Bell for a half-scale flying testbed of one of the company’s proposed designs. This became the X-22A, two of which were built. Because the loss of any one fan would spell disaster, the X-22A used four General Electric T58 turboshaft engines, interconnected to the ducted fans so that an engine failure would not result in a loss fan power. NASA supported Bell’s development with extensive wind tunnel studies at Ames and Langley. Control was exercised by changing the pitch of each of the four propellers and by moving the four elevons. These eight variables were used to control the X-22 in normal flight with ducts horizontal and in hover with ducts vertical. In horizontal flight, pitch and roll were controlled by the elevons and yaw by differential variation of propeller pitch. For hovering flight, propeller pitch adjustments controlled pitch and roll, while elevon movements controlled yaw. During transition, control functions were phased in gradually as a function of duct tilt angle. The pilot was provided with artificial "feel” in yaw during forward flight, but this was removed during transition to hover. Pitch and roll "feel” were provided by a hydroelectric system that applied stick reactions proportional to g-forces. For hover, transition, and low-speed flight, a Stability Augmentation System was used to improve aircraft stability and handling characteristics. The X-22A was equipped with a sophisticated Variable Stability and Control System (VSCS) developed by the Calspan Corp. This allowed it to be programmed to behave like other existing or projected VTOL aircraft for assessment of flight characteristics. The VSCS interacted with the Smiths Industries head-up display (HUD) and the Kaiser Electronics head-down display (HDD). Data inputs to the VSCS included those from a low-speed airspeed sensor, the Linear Omnidirectional Resolving Airspeed System (LORAS), invented by Calspan’s Jack Beilman.[1405]
The first X-22A flew March 17, 1966, but a hydraulic system failure led to the loss of the aircraft in August of that year during an emergency vertical landing, fortunately without injury to the crew. The second X-22A became one of the more successful research aircraft ever flown,
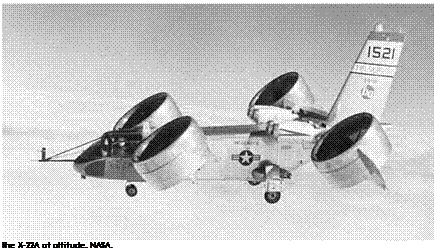 |
 |
completing over 500 flights and over 1,300 transitions, between commencement of its flight-test program at the end of January 1967 through its retirement from flight-testing 17 years later. It hovered at over 8,000 feet altitude and achieved a forward speed of 315 mph, proving conclusively that a tilt duct vehicle could fly faster than could a conventional helicopter. In May 1969, it was turned over to the Navy, which appointed Calspan to continue the flight-test program and fly it as a variable stability research and training aircraft. Eventually, three NASA test pilots flew it, two of whom were formerly at Calspan Corporation—Rogers Smith and G. Warren Hall—and Ron Gerdes from Ames. Assessing the X-22A’s place in V/STOL history, NASA researchers concluded:
Hover operation Out of Ground Effect (OGE) in no wind was rated excellent, with no perceptible hot-gas ingestion. A 12% positive thrust increase was generated In Ground Effect (IGE) by the favorable fountain. Airframe shaking and buffeting occurred at wheel heights up to about 15 ft, and cross-wind effects were quite noticeable because of large side forces generated by the ducts. Vertical cross-wind landings required an excessive bank angle to avoid lateral drift. STOL performance was rated good by virtue of the increased duct-lifting forces. Highspeed performance was limited by inherent high drag associated with the four large ducts. Transition to conventional flight could be made easily because of a wide transition
corridor; however, inherent damping was low. Deceleration and descent at low engine powers caused undesirable duct "buzz” as a result of flow separation on the lower duct lips. Vortex generators appreciably improved this flow-separation problem.[1406]
The X-22A proved to be a successful and versatile research tool, flying for at least 17 years and providing much valuable information on ducted VTOL systems and the larger operational issues of VTOL and STOL aircraft.
NASA expended a great deal of study effort examining the benefits of lift-fan technology and various design approaches that might be taken in design of a practical military and civil lift-fan aircraft. In the course of these trials, involving model tests, tests of candidate fan technologies, and examinations of lift-fan aircraft (such as the ill-fated Vanguard Omniplane), researchers studied an experimental Army-Ryan program, the XV-5A Vertifan. The XV-5A was an ill-fated program, like its contemporary, the Army-Lockheed XV-4 Hummingbird, which is discussed subsequently. Between them, the aircraft built of these two types killed three test pilots and nearly a fourth. Powered by two General Electric J85 engines driving in-wing fans and a nose pitch-control fan (like the Vanguard Omniplane) and used for conventional propulsion, the first of two XV-5As flew in 1964 but crashed during a public demonstration at Edwards AFB in August 1965, killing Ryan test pilot Lou Everett. The second fared little better, crashing in October 1966 at Edwards after one lift fan ingested a rescue hoist deployed from the aircraft, causing an asymmetric loss of lift. Air Force test pilot Maj. David Tittle perished while ejecting from the ailing aircraft, which, in sad irony, impacted with surprisingly little damage. Rebuilt as the XV-5B with some changes to its avionics, cockpit layout, ejection seat, and landing gear, it flew again in 1968, flying afterward at Ames Research Center on a variety of NASA investigations led by David Hickey, until its retirement in 1974.[1407]
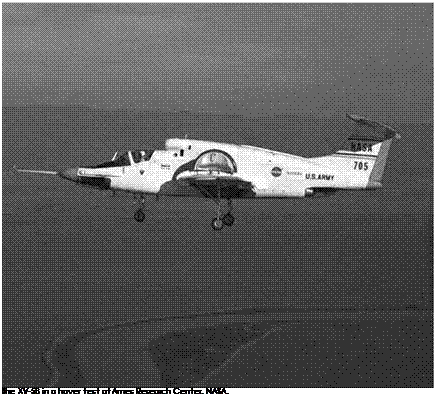 |
 |
Among these studies were tests in and out of ground effect of various wing and inlet configurations, exit-vane designs, nose fans, and control devices. The research studies focused on problems of transition from vertical to horizontal flight, and on improvements of the lift fans to provide quieter, smaller fans with greater thrust. These studies were funded in part by the U. S. Army Aeronautical Research Laboratory, reflecting the Army’s interest in V/STOL aircraft technology and maturation. Ames researchers found that the XV-5B could take off and land vertically from an area the size of a tennis court; hover in midair for several minutes like a helicopter; and fly straight up, down, backward, or to either side at speeds up to 25 mph. As well, it could operate like a conventional jet airplane using a runway, flying up to 525 mph. However, though a NASA summary report on V/STOL concepts concluded, "The lift-fan concept proved to be relatively free of mechanical problems,” tests revealed that the XV-4B was still far from a practical vehicle. Hot – gas ingestion degraded engine performance while in ground effect, drag
from the fan installations limited STOL performance, combinations of fan overspeed and a nose-up tendency complicated conversions, and the design layout hinted at a potential deep-stall problem characteristic of many T-tail aircraft. NASA concluded: "This configuration has limited high-speed potential because of the relatively thick wing section needed to house the lift fans and vectoring hardware.”[1408]
As part of an Advanced Short Take-Off and Vertical Landing (ASTOVL) study program that began in 1980, NASA continued detailed studies of ducted lift fans, among other propulsion concepts intended for a supersonic successor to the vectored-thrust AV-8B Harrier II. The outcome of that development effort was validated in the successful flighttesting of a lift fan on the STOVL variant of the Lockheed Martin X-35, the experimental proof-of-concept demonstrator for the F-35 Joint Strike Fighter a quarter century later.[1409] In this regard, lessons learned from NASA’s various lift-fan programs, particularly the XV-5A and XV-5B, compiled by Ames test pilot and distinguished V/STOL researcher Ronald
M. Gerdes, are included as an appendix to this study.
Proving the Tilt Rotor: From XV-3 and X-100 to XV-15 and on to V-22
One V/STOL concept that proved to have enduring appeal was the tilt rotor, which entered production and operational service with the joint – service Bell-Boeing V-22 Osprey. The tilt rotor functioned like a twin-rotor helicopter during lift-off, hover, and landing. But for cruising flight, it tilted forward to operate as high aspect ratio propellers. Such a concept meant that the tilt rotor would necessarily have its rotors pod-mounted on the tips of conventional wings.[1410]
Though various designers across the globe envisioned tilt rotor con – vertiplanes, the first successful one was the Bell Model 200, produced by Bell Helicopter for the Air Force and Army as the XV-3 under a joint Army-USAF "convertiplane” program started in August 1950. Relatively
streamlined and looking more like an airplane than did many early V/STOL testbeds, the XV-3 had an empty weight of 3,600 pounds and a normal gross weight of just 4,800 pounds, as it was relatively underpowered. A single Pratt & Whitney R985 radial piston engine producing 450 horsepower drove two three-bladed rotors via drive shafts. With this propulsion system, the XV-3 completed its first hover in August 1955, piloted by Floyd Carlson.[1411]
Flight-testing over the next year demonstrated flight at progressive levels of rotor tilt, though it had not made a full 90-degree conversion of its rotors to level position before it crashed while landing in October 1956 from a rotor instability. Bell test pilot Dick Stansbury survived but was seriously injured. Afterward, the second XV-3 was equipped with stiffer two-bladed rotors. On December 18, 1958, Bell test pilot Bill Quinlan achieved a full conversion from a helicopter-like ascent to forward flight like an airplane. During the XV-3 flight-test program, the lack of engine power prevented it from hovering out of ground effect. When
it did hover in ground effect, reflected rotor wash caused unpredictable darting, something the tilt rotor V-22 experienced four decades later during its testing. The lack of an SAS further exacerbated pilot hover challenges, and in gusty air, high pilot workload was required to hover. The XV3 transited rapidly from hover to conventional flight, requiring only small pitch changes across the range of speed and angle of attack encompassed by the transition corridor. Pitch and yaw dynamic instability triggered by side forces as blade angle was increased limited maximum cruise speed to 140 knots and pointed to rotor dynamics and flight control challenges that future tilt rotors would have to overcome. In all of this research, Bell blended extensive analytical studies and scale model experiments with tests in the Ames 40-foot by 80-foot wind tunnel.[1412]
In May 1959, the surviving XV-3 was delivered to the Air Force Flight Test Center at Edwards Air Force Base (AFB), where it underwent a 3-month Air Force evaluation before being delivered for more extensive testing and research to the Ames Research Center. During Edwards’s testing, Maj. Robert Ferry successfully demonstrated a power – off reconversion to a vertical autorotation descent and landing, an important milestone. At Ames, Hervey Quigley carried out the research, and Don Heinle and Fred Drinkwater conducted most of the test flying, in the course of which the XV-3 was modified with a large ventral fin to improve its directional stability. In the Ames tests, flapping of the teetering rotors during maneuvers introduced moments that reduced damping of the longitudinal and lateral-directional oscillations to near zero at speeds approaching 140 knots. Despite these problems and despite being underpowered and limited in payload, the XV-3 proved the capability of the tilt rotor to perform in-flight conversions between the helicopter and the airplane modes, though much work on understanding rotor dynamics and flight control issues needed to be done. The XV-3 flew at Ames until summer 1962, when it began an extensive series of wind tunnel studies in the 40-foot by 80-foot tunnel. In November 1968, during 200-mph tunnel trials, fatigue failure in one wingtip led to separation of the rotors and their pylons from the aircraft, bringing its 13-year test career, at last, to an end. By that time, it had validated the tilt rotor concept, thus influencing—as discussed subsequently—the next step forward in experimental tilt rotor design, the XV-15. That vehicle,
of course, would exert an even greater influence upon development of its operational successor, the V-22 Osprey.[1413]
Before settlement on the tilt rotor as exemplified by Bell’s design approach with the XV-3, researchers considered another seemingly closely related concept: the tilt prop. However, the tilt prop idea was different. Researchers had long known that rotating propellers generate a powerful side force, and Curtiss-Wright Corporation engineers envisioned taking advantage of this property by using smaller diameter and lower aspect ratio propellers than tilt rotors that could use this "radial lift force” as a means of lifting a V/STOL airplane vertically. Such a design, they hoped, would have higher top-end speed after conversion than an XV-3-like tilt rotor approach.[1414]
The result was the X-100, a small testbed whose twin broad-chord propellers were driven by a single Lycoming YT53-L-1 turboshaft engine. Its jet exhaust vented through an omnidirectional tail nozzle, furnishing low-speed pitch and yaw control. Differential propeller operation furnished roll control during hover. The X-100 underwent testing in Ames 40-foot by 80-foot tunnel and extensive ground trials before making its first flight in March 1960. In August, it underwent a NASA flight evaluation, after which it went to Langley Research Center for further testing, including downwash effects on various kinds of ground surfaces.[1415] Langley pilot Jack Reeder found it longitudinally unstable during conversions, something "very undesirable during landing approaches, particularly under instrument conditions.” During hover it demonstrated "erratic wing dropping and yawing,” necessitating "noticeably large” corrective control inputs to correct, and "weak” yaw control that prevented holding a desired heading. It "settled rapidly toward the ground when upset in bank or pitch attitude” while in ground effect, again, something he found "very undesirable.” On the positive side, he found that "The X-100 aircraft suffers no apparent stall problems.”[1416]
 |
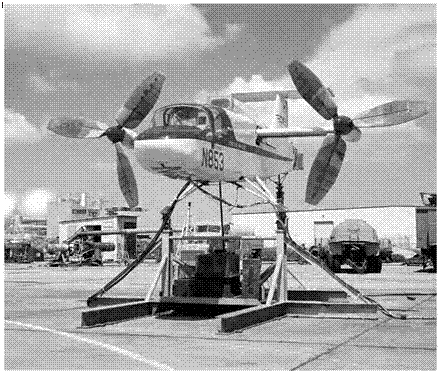 |
In October 1961, the X-100 was seriously damaged in a hovering accident that, fortunately, did not result in injury to its pilot. Despite its mediocre performance, it had demonstrated the feasibility of the radial – lift propeller concept. Thus, Curtiss-Wright continued pursuing the tilt prop approach but now chose to make a four-propeller craft with equal span fore and aft wings, rather than an X-100-like twin-rotor design. The company subsequently received an Air Force developmental contract for this larger and more powerful design, which became the experimental X-19. Of the two that were built, only the first flew, and it had a brief and troubled flight-test program before crashing in August 1965 at the FAA’s National Aviation Facilities Experimental Center (NAFEC) after experiencing a catastrophic gearbox failure. Fortunately, its crew ejected from the now-propless testbed before it plunged to Earth. At the company’s request, the X-19 program was terminated the following December. The accident, one NASA authority concluded, "exemplified an inherent deficiency of this VTOL (lift) arrangement: to safely transmit power to the extremities of the planform, very strong (and fatigue-resistant)
structures must be incorporated with an obvious weight penalty.”[1417] The future belonged to the tilt rotor, not tilt prop.
Though tests with the XV-3 had identified numerous challenges in stability and control, handling qualities, and the dynamics of the combined wing-pylon-rotor interactions, the program encouraged tilt rotor proponents to continue their studies. So promising did the tilt rotor appear that the Army and NASA formed a joint project office at Ames to study tilt rotor technology and undertook a number of simulations of such systems to refine project goals and efficiencies.[1418] In 1971, Dr. Leonard Roberts of Ames’s Aeronautics and Flight Mechanics Directorate established a V/STOL Projects Office under Woody Cook to develop and flight-test new V/STOL aircraft. That same year, in partnership with the Army, NASA launched a competitive development program for the design and fabrication of two tilt rotor research aircraft. Four companies responded, and Boeing and Bell received study contracts in October 1972. After evaluating each proposal, NASA selected Bell’s Model D301 for development, issuing Bell a contract at the end of July 1973.[1419]
As developed, the XV-15 was an elegant and streamlined technology demonstrator, a two-pilot testbed powered by twin Lycoming T53 turboshafts rated at 1,550 horsepower each, driving 25-foot-diameter three-bladed prop rotors. Bell completed the first XV-15 in October 1976 and, after ground tie-down testing, undertook its first preliminary hover
trials in May 1977, piloted by Ron Erhart and Dorman Cannon. In May 1978, before flight envelope expansion, it went into the Ames 40-foot by 80-foot wind tunnel for extensive stability, performance, and loads tests. Ames’s aeronautical facilities greatly influenced the XV-15’s development, particularly simulations of anticipated behavior and operational nuances, and tilt rotor performance and dynamic tests in the wind tunnel.[1420]
The second XV-15 went to Dryden for contractor flight tests, conducted between April 1979 and July 1980, and was delivered to NASA for research in August.[1421] By that time, NASA, Army, and contractor researchers had already concluded:
The XV-15 tilt rotor has exhibited excellent handling qualities in all modes of flight. In the helicopter mode it is a stable platform that allows precision hover and agility with low pilot workload. Vibration levels are low as are both internal and external noise levels. The conversion procedure is uncomplicated by schedules, and it is easy to perform. During the
conversion or reconversion, acceleration or deceleration are impressive and make it difficult for conventional helicopters or airplanes to stay with the XV-15. Handling qualities are excellent within the airplane mode envelope investigated to date; however, gust response is unusual. Although internal noise levels are up somewhat in the airplane mode, external noise levels are very low. Overall the XV-15 is a versatile and unique aircraft which is demonstrating technology that has the potential for widespread civil and military application.[1422]
Such belief in the aircraft led to its participation in the 1981 Paris Air Show, the first time NASA had demonstrated one of its research vehicles in an international venue. It was an important vote of confidence in tilt rotor technology, made more evident still by the XV-15’s stopover at the Royal Aircraft Establishment at Farnborough, where it demonstrated its capabilities before British aeronautical authorities. In 1995, 14 years after its first Paris appearance, the XV-15 would again fly at Le Bourget, this time in company with its successor, the Bell-Boeing V-22 Osprey.[1423]
Over its two-decade test program, the XV-15 was not immune to various mishaps, though fortunately, no one was seriously injured. Both aircraft experienced various emergencies, including forced landings after engine failures, a close call from a bird strike that cracked a wing spar, a tree strike, near-structural failure caused by an unsuitable form of titanium alloy fortuitously discovered before it could do harm, intergranular corrosion that caused potentially dangerous hairline blade cracks, and even one major accident. In August 1991, the first XV-15 crashed while landing after an improperly secured nut separated from a linkage controlling one of the prop rotors. Pilots Ron Erhart and Guy Dabadie were not seriously injured, though the accident destroyed the aircraft.[1424]
In retrospect, the XV-15 was the most influential demonstrator aircraft program that Ames ever pursued. For a cost to taxpayers of $50.4 million, NASA and its partners significantly advanced the technology and capability of tilt rotor technology. In over two decades of flight operations, more than 300 guest pilots would fly in the XV-15. As well, it would operate from the New York Port Authority heliport, fly abroad,
 |
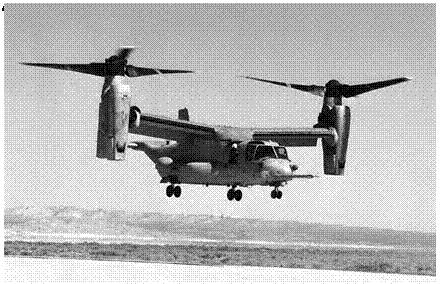 |
and go to sea, demonstrating its ability to operate from amphibious assault ships. Among the many at Ames who contributed to making the program a success were NASA’s Wally Deckert, Mark Kelly, and Demo Giulianetti, and the Army’s Paul Yaggy, Dean Borgman, and Kipling Edenborough, who furnished critical guidance and oversight as the project was being established. Dave Few, Army Lt. Col. James Brown, and John Magee served as Program Managers. Principal investigators were Laurel Schroers, Gary Churchill, Marty Maisel, and Jim Weiberg. The project pilots were Daniel Dugan, Ronald Gerdes, George Tucker, Lt. Col. Grady Wilson, and Lt. Col. Rick Simmons. They shepherded the XV-15 through two decades of research on flying qualities and stability and control evaluations, control law development, side stick controller tests, performance evaluations in all flight modes, acoustics tests, flow surveys, and documentation of its loads, structural dynamics, and aero – elastic stability characteristics, generating a useful database that was digitized by Ames and made available to industry and military customers. In sum, the XV-15 did much to advance the V/STOL cause, particularly that of the tilt rotor concept.[1425]
In particular, flight experience with the XV-15 contributed greatly to the development of the joint-service V-22 Osprey tilt rotor.[1426] This Bell – Boeing aircraft, now in service with the U. S. Marines, the U. S. Navy, and the U. S. Air Force, fulfills a variety of roles, including combat assault, insertion and support of special operations forces (SOF), combat search and rescue (CSAR), and logistical support. Time will tell whether the V-22 Osprey will come to enjoy the longevity and ubiquity attendant to conventional joint-service fixed and rotary wing transports, such as the legendary Douglas C-47, Lockheed C130, Bell UH-1, and Sikorsky H-53.