The Phase II experiment involved six data-gathering flights using X-15-1 beginning with flight 1-42-67 on 5 December 1963, again with Rushworth as the pilot. As it happened, this proved to the fastest flight by a basic X-15, reaching Mach 6.06. Jack McKay flew the last flight (1-49-77) of the experiment on 30 June 1964. Three checkout flights (1-39-62 through 1-41-65) had preceded the data-gathering flights.108
The purpose of the experiment was to obtain quantitative data to determine the effects of aero – thermo distortions associated with vehicles flying at hypersonic speeds and extreme altitudes. Researchers believed the results were directly applicable to the Lockheed A-12/SR-71 and North American B-70/RS-70 programs, and to "future hypersonic reconnaissance systems." The Air Force conducted similar experiments (albeit at much lower speeds) using Martin RB-57D aircraft and high-altitude balloons.109
The high-acuity experiment package was somewhat more sophisticated than the one flown during Phase I, replacing the original KC-1 camera with a more sensitive KS-25. In addition to the new camera on the same ART-15A stabilized mount, researchers installed a small analog computer that collected signals from the X-15 stable platform to use for image-motion compensation and instrumentation to monitor the mechanical and optical performance of equipment. Seven downward-looking photometers measured the spectral changes in light with respect to altitude and provided a signal to the automatic exposure control system on the KS-25. Two additional upward-looking photometers monitored the amount of visible light remaining in the upper atmosphere. Instrumentation provided a continuous record of the temperature on the inner and outer surfaces of the photographic window. A multiple-pickup boundary-layer rake determined whether the boundary layer was laminar or turbulent and monitored its thickness for subsequent comparison with photographic quality. A display of delta cross-range using inertial system outputs in the cockpit center pedestal assisted the pilot in maintaining the correct course.119
The KS-25 and its additional electronics weighed 325 pounds in addition to the 156-pound experiment support package from the earlier tests. The KC-25 was much larger than the earlier KC-1, occupying a volume approximately 13 inches long, 10 inches wide, and 43 inches high; this camera took up the entire height of the instrument compartment. Again, Dr. J. Baker of Spica built a special lens that had a focal length of 24 inches and a relative aperture of f/4, and could provide a resolution of 70-90 lines per millimeter on Super-XX film. The film was nominally 4.5 by 4.5 inches and 250 feet of it were stored in the magazine. The camera had to undergo several modifications to adapt it to the X-15 environment. The automatic focus control was disabled since its time range was not compatible with the speed of the X-15, and the automatic exposure control was modified to fix the lens at f/4 (instead of varying it between f/4 and f/16). After it was modified, the Air Force tested the camera in a centrifuge at the Rocket Propulsion Laboratory at Edwards to determine the effects of large acceleration on its electromechanical properties.-1111!
The X-15 flew both high-speed and high-altitude flights with the experiment, and the Air Force analyzed the photographs to determine the influence of the hypersonic flight environment on the degradation of image quality. Researchers deemed the image quality from four particular flights (1-42-67, 1-45-72, 1-46-73, and 1-47-74) to be the best, and used these data for the analysis. These flights varied in altitude from 101,000 feet (three flights) to 175,000 feet (1-4673) and in speed from Mach 5.01 (1-46-73) to Mach 6.06 (1-42-67). NASA returned the experiment to the vendor for repair after it malfunctioned prior to launch on abort 1-A-68, and reinstalled it in time for flight 1-45-72. In addition to the support used in Phase I of this experiment, Phase II also used a Boeing RB-47 Stratojet equipped to photograph the same targets just before and after the X-15 flights, providing researchers with a known reference.-112
Researchers performed a laboratory analysis on the film to determine the extent of the deleterious effects of the flight conditions on the optical performance of the camera system. They determined the resolution for those frames that contained images of the three-bar resolving power targets. They then used these readings to check the values of resolution obtained by making microdensitometer traces of edges appearing in the photographs, converting these edge traces to transfer functions, and finding the intersection of these with the film threshold to estimate system resolution and determine the degradation in optical performance. The resolution ranged from less than 11 to greater than 60 lines per millimeter for a lens-emulsion combination whose low – contrast performance was between 80 and 90 lines under laboratory conditions.-113
Regardless of the technical considerations, the photography proved to be rather spectacular. On each flight the camera exposed a frame with the X-15 still attached to the NB-52 to use as a reference. This frame almost always had a resolution of over 80 lines per millimeter. On one flight the X-15 photographed the Indian Springs target while at Mach 5.47 and 101,400 feet, when the temperatures on the camera window were -4 degrees on the inner surface and +287°F on the outer surface. The resolution of the photograph was 60 lines per millimeter.114
Other examples included a photograph of Indian Springs AFB taken at Mach 5.43 and 120,000 feet, with inner and outer window temperatures of -1°F and +321°F, respectively. Three aircraft parked on the ramp of the base were readily identifiable. Another photo taken at Mach 4.37 and 169,600 feet also had a 60-line resolution. Researchers determined from these tests that the photographic quality obtained at high speeds and altitudes was acceptable. Researchers also performed a subjective analysis of the image quality for the bulk of the photographs in an effort to find some correlation between image quality and certain data from the flight environment. However, they could not establish any direct relationship.115
In the latter part of Phase II, researchers also tested several experimental near-infrared color films for the first time in flight. Various reports indicate that the X-15 flights led directly to the use of near-infrared color film during the conflict in Southeast Asia (the heat-sensitive colored emulsions showed enemy activity under the dense jungle canopy). Researchers soon adopted similar techniques for Earth-resource photography.116
Conclusions
The experiment had its share of problems. In addition to the accumulated navigation errors experienced on most flights that often precluded directly overflying the targets, numerous equipment malfunctions plagued the experiment. For instance, both the KC-l and KS-25 incorporated a vacuum system that used a sense line routed from the experiment to ambient pressure in the aircraft’s liquid-nitrogen bay. Sporadic malfunctions occurred that resulted in loss of vacuum and, hence, loss of data. A survey of six flights showed that three of them experienced
problems with the vacuum system.-1117!
The researchers did not believe the experiment was particularly conclusive, since there were many unanswered questions. For instance, researchers found isolated instances of high-quality images being obtained at speeds between Mach 2.5 and 6 at altitudes of 55,000-100,000 feet. However, they also noted nonperiodic image smears that evidently arose from image motion that was not accounted for in the flight data by vibration, aircraft motion, or stabilizer-mount movements. This behavior limited the analysis of the experimental results. Still, researchers concluded that the distortion of the quartz window due to thermal effects had a negligible effect on resolution, and that scattering from the turbulent boundary layer was not severe and its optical effects were slight in any case.!1181
It was also determined that the mathematical model used to predict the optical performance gave good agreement with the measured performance, and that further improvements in the method could not be made using the results of these X-15 flights. Like Phase I, the detailed results of Phase II remain classified.-1119!
However, it is likely that the results of this experiment are no longer terribly applicable. Although the 3-arc-second cameras tested on the X-15 apparently showed a negligible impact from the hypersonic aero-thermo environment, the increased sensitivity of the more-modern 0.5-arc – second (or better) cameras may well be subject to significant degradation from shock waves and boundary-layer flow.
Experiment #6: Earth Atmospheric Degradation Effects
The Air Force combined experiment #6, originally known as the "environmental effects on optical measurements" experiment, with experiment #5.!120!
Experiment #7: Electric Side-Stick Controller
The ASD and FRC jointly sponsored this experiment to address pilots’ complaints about the feel of the side-stick controllers in the X-15. Side-stick controllers were of interest because of the relatively small cockpit space they required and the better support they provided for the pilot’s arm under accelerated flight conditions. Pilots criticized the side stick in the X-15 because of the adverse feel characteristics caused by connecting it mechanically to the center stick and the power actuators that moved the control surfaces. As in the much-later F-16, there was no mechanical linkage between the electric side stick and the flight-control system, and the electric side-stick would have transmitted instructions to the MH-96 adaptive control system to fly the airplane. In addition to providing a better control system for the X-15, the electric side-stick program would have provided experience applicable to the Dyna-Soar. By the end of 1962, North American had begun flight-testing a modified F-100C equipped with an electric side stick, but these tests were not completely successful. The Air Force put plans to install the electric side stick in the X-15 fixed-base simulator on hold, and then canceled the experiment at the end of 1963 when the Dyna-Soar program abruptly ended. NASA never installed the electric side stick in X-15-3.-1121!
Experiment #8: Detachable High-Temperature Leading Edge primary restraint; 2) a thin-skin, refractory-metal concept that relied on a low coefficient of expansion to minimize thermal stresses; 3) a prestressed leading edge that used a mechanically or thermally applied prestress system; and 4) a nonmetallic leading edge that contained an ablative material (much like North American’s X-15 proposal).-1122
The original X-15 wing and empennage leading edges used a round profile to minimize the effects of heating. NASA (particularly Ames) had wanted removable wing leading edges to allow different designs to be tested during the flight program, but these disappeared early in the development period. After the basic envelope expansion was completed, various researchers in the Air Force and NASA became interested in reviving the idea. Since replacing the wing leading edge would have required an extensive wing redesign, researchers decided to find an alternate way. The selected method was to modify a ventral rudder to accommodate leading edges manufactured from Rene 41 and tantalum, and the modified rudders were ready for flight in mid – 1966. However, it is unlikely that they ever flew, given that X-15A-2 was the only aircraft to fly with the ventral rudder during the time the modified units were available.-123
Sharp-leading-edge studies that were intended to evaluate various heating theories were also part of this experiment. The standard X-15 rudder had a leading-edge radius of 0.5 inch over the very forward 0.6 inch of chord. The sharp-leading-edge modification extended the leading edge of the dorsal rudder 5.16 inches forward, resulting in an overall chord of 9.00 feet. This sharp 347- stainless-steel leading edge had a radius of only 0.015 inch at the tip, and essentially had a knife-edge shape. To ensure turbulent flow along one side of the rudder, researchers placed boundary-layer trips consisting of spot welds 0.125 inch in diameter and 0.020 inch high on the right side approximately 5 inches from the leading edge.124
To gather data on flights with the sharp rudder, researchers mounted an Inconel X shear-layer rake impact probe on the left side of the sharp-leading-edge rudder 27 inches aft of the leading edge and 12 inches from the top. Eleven 30-gage chromel-alumel thermocouples were spot – welded to the inside surface of the skin, equally spaced chord-wise on the right side of the rudder 22 inches from the top. NASA installed six 0.25-inch-diameter pressure orifices near the thermocouples and connected the surface orifices and impact probes to standard NACA manometers in the side fairing of the fuselage. Similar instrumentation on a blunt-leading-edge rudder on X-15-2 collected baseline data; however, in this case the impact probe was on the right side 95 inches from the front of leading edge and 22 inches from the top of the rudder. The location of the probes was changed because the researchers wanted to gather slightly different data.123
The sharp rudder first flew on X-15-3 on 7 November 1963 (3-23-39) with Bob Rushworth at the controls. Several flights using X-15-2 had already gathered baseline data with the standard configuration. The X-15-3 would carry the sharp rudder through flight 3-33-54, when NASA removed it to install additional instrumentation. A normal rudder borrowed from X-15-1 replaced it for flight 3-34-55. NASA reinstalled the sharp rudder in time for flight 3-35-57, and X-15-3 continued to fly with it until the airplane was lost. The tests allowed researchers to validate various heating theories for both the blunt – and sharp-leading-edge shapes. In general, the theories fell into two groups: those that closely predicted the flight results (Moeckel and Love), and those that overestimated the heat transfer by 30-50% (Eckert).123
Experiment #9: Landing Computer
completion, but combined elements of it with experiment #14.-1127 Experiment #10: Infrared Exhaust Signature
The Air Force Geophysics Research Directorate sponsored experiment #10, with Leonard P. Marcotte as the principal investigator, to determine the infrared characteristics of a liquid- oxygen-ammonia rocket engine. This was conceptually similar to experiment #3 except that it involved the infrared spectrum instead of the ultraviolet. Measurements had been made of the signatures from Atlas and Titan ICBM engines; however, no measurements from oxygen-ammonia engines were available. Researchers wanted the data to use as part of a missile-detection system. The primary instrument was a Block Associates E-8 infrared radiometer that measured radiation in four spectral regions by focusing radiation through a calcium fluoride lens and four selective filters onto a lead sulfide detector. The range of the detectors was 2.5-7.0 microns. Personnel from the Cambridge Research Laboratory accomplished pre – and postflight checkouts of the package.-^128-
The experiment was carried in the tail-cone box of X-15-3 on seven flights during 1963 and early 1964, but because of mechanical problems, data were obtained on only a single mission. Researchers asked for four additional flights during late 1964, but apparently no flights were made. The detailed results are still classified. -1129
Experiment #11: High-Temperature Windows
The ASD sponsored experiment #11 to investigate various transparent materials in the high – temperature environment. The rapid buildup of temperature and dynamic force as cold structures reentered the atmosphere at hypersonic velocities created severe problems for the window designers. The window design and installation technique were critically important since both affected the heat transfer between the airframe and the transparency, as well as between the outer and inner window surfaces. NASA instrumented the X-15-2 canopy windows, as well as the center-of-gravity compartment windows, to provide precise temperature data. Among other things, the experiment tested the fused silica windows used on the photo optical degradation experiment (#5). The experiment acquired useful data on several flights during 1963.[130]
Proposals were later made to modify the experiment to test an X-20 window and retainer during high-speed flights on the X-15. Researchers wanted to install the window on one of the X-15-2 lower speed brakes and expose it to variable dynamic pressures on several Mach 6 flights during 1964. These plans never came to fruition after Secretary of Defense Robert McNamara canceled the Dyna-Soar program in December 1963. Nevertheless, X-15A-2 carried an instrumented window in the fixed portion of its ventral stabilizer for five flights during early 1966. Among other things, researchers used these flights to investigate whether ablator smoke and residue would adhere to the glass enough to hinder vision through the windshield; they concluded that it would.-1181-
Experiment #12: Atmospheric-Density Measurements
Given the increased operations of both high-altitude manned vehicles and military missiles, the Air Force considered it important to determine the atmospheric density at altitudes above 100,000 feet as well as the day-to-day variation. As originally envisioned, the experiment would have used an alphatron ionization gage in a modified wing tip (this experiment predated the wing-tip pod concept) on X-15-2 that was outside the contamination caused by the APU and
ballistic control exhausts. The measurements placed no constraints on the flight path or trajectory.-1132!
The engineers could not find a reasonable way to mount the ionization gage, so the researchers rescoped the experiment to perform analytical research using air data gathered by the normal X – 15 ball nose and stable platform. Density-height profiles in the stratosphere and mesosphere were obtained from measurements of impact pressure, velocity, and altitude on two flights (214-28 and 2-20-36) in 1961 and four more (3-16-26, 3-20-31, 3-21-32, and 3-22-36) in 1963. The researchers noted that the modern recorders in X-15-3 provided more precise data, but the X-15 pressure-measuring system had a substantial lag in it, which made it difficult to perform an exact analysis. The density computations used a form of the Rayleigh pitot formula, and the data agreed well with measurements made by Arcas rocketsondes launched at Point Mugu around the time of the X-15 flights. The X-15 data generally indicated 5-7% greater densities than the standard predicted values at altitudes between 110,000 and 150,000 feet.31333
The Air Force Geophysics Research Directorate sponsored a follow-on experiment to determine the atmospheric density at high altitudes to provide data for the designers of future aerospace vehicles. The wing-tip pods finally allowed researchers to measure atmospheric impact pressure with a densatron ionization gage installed in the nose of the right wing-tip pod on X-15-1. The College of Engineering at the University of Michigan built the experiment under Air Force contract. Researchers used two flights (1-50-79 and 1-51-81) to check out the installation and measure temperatures in the instrument. NASA then installed a small amount of radioactive tritium in the gage to measure the atmospheric density above 90,000 feet.-1343
The intended goal of obtaining atmospheric density profiles on a regular basis was never realized; in fact, the experiment only flew on three more flights (five flights in four years). As the researchers later commented, "The research activity undertaken here was valuable if for no other reasons than to point out the numerous restrictions associated with a manned rocket vehicle."-11333
An analysis of the data showed that despite predictions that the wing-tip pods would be outside the interference area, the experiment was limited below 100,000 feet by the bow shock-wave interference, and above 240,000 feet by the residue from the ballistic control-system thrusters. In between those altitudes, the thrusters intermittently biased the gage output; however, researchers could still obtain sufficient data for useful analysis.31363
Experiment #13: Micrometeorite Collection
The Air Force Geophysics Research Directorate sponsored experiment #13 to collect samples of micrometeorites and extraterrestrial dust at altitudes above 150,000 feet. This was the initial impetus to manufacture the wing-tip pods, and researchers installed a collector in the nose of the left wing-tip pod on X-15-1. At high altitude and low dynamic pressure, the lid opened from the rear to a vertical position on top of the wing. As it lifted, rotating upward toward the front, it also swiveled so that the underside of the lid faced the aircraft fuselage and exposed the collector to the air stream. The collector then "broke seal" to expose a rotating collection surface behind an orifice in the side of the collector unit. The unit rotated to six different positions during the collection, and the location served to indicate the time of the event.31373
During flight 1-50-79 the collector door inadvertently opened during the exit phase and remained so for the remainder of the flight, but fortunately did not cause serious damage. The collector was flown on flight 1-51-81, without exposing the collection device, to determine the amount of contamination resulting from ground handling. The plan was to operate the collector on as many high-altitude flights of the X-15 as possible.-1138!
The experiment flew on flight 1-63-104, but the altitude attained on the flight was not sufficient to provide meaningful data, and an engine problem forced an emergency landing on Delamar Lake. After Jack McKay landed the X-15, the ground crew noticed that the collector box had extended, although they could not determine when this occurred. A postflight inspection revealed that the retraction mechanism was not functioning properly, and NASA returned the experiment to North American for repair.-139!
The experiment malfunctioned during preflight testing prior to flight 3-55-82 and NASA removed it from the aircraft. After it was modified to increase its reliability, the experiment flew on flight 1-65-108 to an altitude of 241,800 feet, but the collection rotor jammed in its second position. Subsequently, the experiment flew on both X-15-1 and X-15-3 and collected some particles during six flights. Unfortunately, residue from the ballistic control-system thrusters had contaminated the particles, and the Air Force canceled the experiment.-3401
Experiment #14: Advanced Integrated Flight-Data and Energy-Management Systems
The ASD and FRC jointly sponsored experiment #14. "A [principal] objective of this program is to obtain information to be applied to problems of design and use of advanced flight control equipment for vehicles which reenter the atmosphere from Earth orbits. Accordingly, a primary goal in the EMS design work has been to include the features of advanced orbital re-entry energy management systems to the maximum extent compatible with the X-15 vehicle and the flight control hardware to be tested." To this end, the Air Force contracted with Bell Aerosystems to develop a suitable unit targeted at the Dyna-Soar program. Robert W. Austin and John M. Ryken at Bell led the work on Advanced Technology Program (ATP) 667A.-141
James E. Love and Melvin E. Burke from the FRC, and Lieutenant Colonel Elmer F. Smith, director of the X-15 Project Office at Wright-Patterson AFB, worked out an MoU for including the Advanced Integrated Flight Control System (AIFCS) in the X-15 flight program. Smith signed the MoU on 9 September 1963 and Paul Bikle signed it on 12 September.-142!
Essentially the MoU indicated that the Air Force would be responsible for funding the development program, testing the system prior to its installation in an X-15, and maintaining the system after it was delivered. The FRC would handle the actual flight research program and provide a digital computer to upgrade the fixed-base simulator. The MoU stated that the X-15 Joint Program Coordinating Committee would determine the installation and flight schedule after "a reasonable reliability shall be demonstrated… as evidence in laboratory tests, rocket sled tests and finally flight tests in a Douglas F5D Skyray prior to the initiation of installation modifications of the X-15 airplane."-143!
The Bell system was extensively simulated using an analog system to experiment with different control-loop arrangements, and an IBM 7090 digital computer to work out the problems associated with the digital programming. The results showed that the system performed well in a range of missions covering the X-15 flight envelope. Although Bell would design the system,
Litton Industries would program it into one of their digital flight computers. The energy – management system (EMS) used slightly more than 3,000 words of memory and "about 15- percent of real-time on the Litton Flight Data System computer." The X-15-3 carried the system because it required the MH-96 adaptive flight-control system.144
Probably the most significant change from the system designed for Dyna-Soar was the use of an artificial dynamic pressure limit to ensure that the X-15 stayed within dynamic (q) and thermal limits. The decision to use a q-limit instead of directly using temperature as a control variable (as in the case of the Dyna-Soar) was the result of discussions among Air Force, Bell, and NASA personnel. The use of q-limits eliminated the need to instrument the exterior of the X-15 to obtain additional temperature data. The only inputs the system needed were dynamic pressure and altitude-rate information. The EMS performed four basic functions:[145
1. Computation of vehicle total maneuver potential, formation of a nondimensional ground area attainable, and generation of angle of attack and bank commands for vehicle destination maneuvering.
2. Computation of the minimum value of dynamic pressure attainable at the next pullout (perigee) point and generation of override commands required to insure that pullout conditions do not reach critical values.
3. Computations to nondimensionalize measured dynamic pressure and generation of override commands for a [angle of attack] and [bank angle] to ensure that present dynamic pressure and aerodynamic heating do not reach critical values. (A similar loop for control of "g" loading was not contained within the EMS since this was already provided in the Honeywell [MH-96] adaptive flight control system for the X-15.)
4. Computations to nondimensionalize measured rate of change of altitude and generation of commands to damp phugoid motions (long-period oscillations along the longitudinal axis).
The pilot could select either an automatic or manual energy-management mode. In the manual mode, the system displayed the results of the energy-management computations to the pilot but did not take any independent action. This allowed the pilot to fly the correct energy-management profile or to deviate from it as needed. In the automatic mode, the system displayed the same information to the pilot but also sent commands directly to the MH-96 to fly the desired reentry profile. The system was programmed to arrive at high key with "sufficient energy for the pilot to accomplish the final descent and landing with considerable energy reserve." Interestingly, the system did not direct the X-15 toward any particular heading over high key, so the pilot had to use some of the excess energy to establish a heading that would allow him to land.-1146
As development progressed, there were concerns that the system was requiring too much power and cooling. Jim Love and Lannie D. Webb from the FRC first voiced these concerns during a meeting on 17 September 1962 with Captain Hugh D. Clark and Captain James H. Smith from the ASD. Love indicated that the electrical demands were so high that the X-15-3 electrical system would have to be "beefed up" to accommodate the new system. Whereas the original Sperry stable platform required 1.4 pounds per minute of cooling, the new system required over 6.3 pounds per minute. The original Litton computer was finally tested in the NASA F5D (BuNo 142350/NASA 213) in late 1964, despite an initial intent to begin testing in January 1964. The F5D portion of the program ended on 31 March 1965 after 17 flights.-1^47
This experiment was reoriented in October 1964 to use Honeywell equipment instead of the originally procured Litton components. The centerpiece was an H-387 digital computer hooked to a new Lear Siegler instrument panel. In addition to conducting the experiments that were initiated under ATP 667A, researchers later included studies of pilot displays, energy management, and piloting problems during the exit phase of high-performance vehicles. The program expected to make 16 flights in X-15-3 to cover most of the flight envelope.-1^48
As finally defined for the X-15 program, this experiment was an evaluation of vertical-tape displays, energy-management concepts and techniques, and command guidance for boost and trajectory control. The equipment consisted of a Honeywell inertial system, coupler, and computer; a Honeywell AN/AYK-5 Alert digital computer; a Lear Siegler cockpit instrument panel with vertical-tape displays; the Honeywell MH-96 adaptive control system; and the ball nose.
NASA installed the system in X-15-3 during the weather down period in early 1966.-1149
Another part of the experiment was to test a boost-guidance technique and display that had been developed by the Ames Research Center and was called, logically enough, the Ames boost – guidance evaluation. For the most part, the experiment consisted of additional programming for the Alert computer. Data was displayed on the horizontal pointer of the three-axis attitude indicator, making it a "fly-to-null" display of altitude error plus altitude rate error. This change ultimately confused Mike Adams, and on flight 3-65-97 contributed to the loss of X-15-3. Researchers flew it for the first time on flight 3-58-87 to evaluate needle movement on the display. A postflight review of the cockpit film showed that the cross-pointer was moving as expected since the guidance parameters stored in the computer were not representative of the planned flight. Subsequent flights programmed the boost-guidance software to match the desired flight profile. On future flights, the pilot was to fly the boost portion using the boost-guidance program as long as the display of pitch attitude was within +2 degrees of the planned flight path. The experiment seemed to function as expected.[150]
Overall, the entire integrated flight-data system appeared to work well enough during the next 14 flights. Its performance on its last flight is more open to debate.
Experiment #15: Heat-Exchanger System or Vapor-Cycle Cooling
The ASD sponsored experiment #15 to verify performance estimates for evaporators and condensers at zero gravity. Researchers wanted to mount the experiment in the instrument compartment of X-15-1 during four high-altitude flights with a large zero-g parabola at the top. The first of the Garrett AiResearch heat exchangers (excess units from the canceled Dyna-Soar) arrived in early November 1964. North American conducted the initial performance tests in Inglewood during late November, and the unit underwent centrifuge tests at the Rocket Propulsion Laboratory at Edwards in mid-December 1964. Engineers tested the units aboard a KC-135 in early 1965 and scheduled the installation in X-15-1 for mid-1965.-1151
However, the experiment faced several challenges. The most pressing was that starting the large compressor needed to cool the equipment required more power than was available on either the X-15 or the NB-52. Engineers thought that installing larger alternators in the NB-52 might be possible, but the wiring on the carrier and the X-15 would have to be upgraded to a heavier gage to handle the load. Another possible method would be to start the compressor using ground power before takeoff since the X-15 APUs could supply the operating load, without starting the compressor. The compressor was equipped with an automatic shutoff feature that could detect a failure of one of the X-15 APUs; a single unit could not supply both the experiment and the airplane, and the airplane came first.-1152
Difficulties in bringing the experiment up to the safety standards demanded by the X-15 program delayed the experiment for over a year. As it ended up, NASA never installed the hardware on an X-15 and the experiment was moved to the Apollo Applications Program, which itself never got off the ground.-1153
Experiment #16: Rarefied Wake-Flow Experiment
The FRC sponsored a rather fanciful concept known as the "rarefied wake-flow" experiment.
Initially the plan was to tow an inflatable plastic sphere behind the X-15. By measuring the tension on the tow rope and analyzing photographs, the researchers hoped to determine the atmospheric density above 200,000 feet and the drag characteristics of a towed sphere in free – molecular-flow regions, assess the effect of vehicle flow fields, and study supersonic wakes. Additional investigations included the motion of a towed drag body and the viability of inflatable reentry vehicle deceleration devices.-11541
The experiment was modified so that a small Mylar balloon could be released (instead of towed) from the tail-cone box on X-15-3 at altitudes above 250,000 feet to investigate the properties of supersonic wakes at low densities. The experiment would require two flights above 300,000 feet using balloons originally procured for Project Mercury, and researchers wanted four additional flights above 250,000 feet using somewhat sturdier balloons. Two unsuccessful attempts (flights 3-21-32 and 3-22-36) to release a Mercury balloon occurred in mid-1963, marking the end of this idea.-1155-
The experiment ended up using a Pace flow transducer mounted in the forward section of the X – 15 left wing-tip pod. This installation negated many of the original secondary objectives of the experiment. The revised experiment called for flights above 300,000 feet, which resulted in very few flight opportunities, and by December 1964 it was determined that flights above 250,000 feet would be sufficient. (Only four program flights were above 300,000 feet, while 15 others got above 250,000 feet.) The experiment was an evaluation of a mechanical transducer for rarefied – flow measurement and measured upper-atmosphere ambient density. NASA carried the experiment on a "standby" status to replace experiment #13 if opportunity allowed, but by the end of 1965 the experiment apparently still had not flown. In April 1966 the ballast nose cone for the wing-tip pods was modified to accept the Pace transducer, allowing the experiment to be installed in either wing-tip pod on either X-15-1 or X-15-3. The experiment flew several times on each airplane during 1966 and 1967.-1561
Experiment #17: MIT-Apollo Horizon Photometer
The Office of Manned Space Flight sponsored experiment #17 to measure the Earth’s horizon – intensity profile as a function of altitude to different wavelengths in the visible spectrum. This was officially called the "simultaneous photographic horizon scanner experiment," and was in many respects a follow-on to the Langley horizon definition experiment (#4) using much more sophisticated equipment. The MIT project was large and wide-ranging, using various aircraft, sounding rockets, as well as Mercury and Gemini spacecraft, to carry radiometers to measure the Earth’s infrared horizon. Of these, the X-15 carried the largest and most sophisticated package to define the Earth’s limb for use as an artificial horizon for the space sextant carried aboard the Apollo spacecraft. Researchers designed the sextant as a backup device in the event of a radar or communications failure. NASA installed a single Phase I and two Phase II experiments on X-15- 1.H5Z1
The interim Phase I system was a fixed platform in the tail-cone box supporting three MIT Instrument Laboratory-designed photosensitive instruments (a photomultiplier photometer, a solid-state photometer, and a camera) pointing aft and approximately aligned with the aircraft thrust axis. Researchers evaluated the fixed platform during flight 1-51-81, and flew four additional flights to obtain photometer output levels.-1581
horizon-scan rates to obtain the most useful data independent of aircraft maneuvering. A door that opened above 100,000 feet covered all of the instruments during the X-15 exit phase. NASA installed the Phase II experiment in X-15-1 during the weather down period in early 1966. The initial plan was to fly a single flight to 220,000 feet as a checkout of the system, and then fly four data-gathering flights to 250,000 feet under various seasonal sun-angle and atmospheric conditions with the system pointed approximately true north.-159
Flight 1-63-104 was the checkout for part 1 of Phase II, and postflight inspection showed that the experiment was in good condition despite the emergency landing. The experiment flew on flights 1-65-108, 1-66-111, 1-67-112, and 1-68-113, but did not obtain data on flights 165-108 and 1-67-112 because of electrical power problems, or on flight 1-68-113 due to a loss of the scan signal. An evaluation of the data from flight 1-66-111 indicated that the photometer functioned properly but the star tracker did not acquire Polaris as programmed. The experiment subsequently flew on four additional flights and gathered good data on all of them.-160
Five flights (part 2 of Phase II) added a Barnes infrared edge tracker to measure the 14-40-micron infrared profile. The Manned Spacecraft Center sponsored this part of the experiment using an instrument designed for spacecraft attitude stabilization in the Apollo Applications Program. The Barnes instrument was essentially a telescope employing a 2.4-inch-diameter silicon lens mounted on the elevator under the skylight hatch of X-15-1. North American installed this hardware, collocated with the WTR launch-monitoring experiment, in early 1967. Researchers checked out the experiment on flight 1-76-134, and made four data-gathering flights between June and September 1968. Flight 1-80-140 was the last flight of the experiment, and Paul Bikle reported that "star recognition was not achieved."-161-
One of the more interesting aspects of the experiment was that the High Range could not provide sufficiently accurate radar data to meet the needs of MIT. Instead, NASA arranged for the Sandia Corporation to track the X-15 using the MPS-25 radar at Cactus Flats, Nevada. This radar could track the airplane with 0.10-milliradian-attitude accuracy and a range accuracy of several yards.-1162-
The experiment concluded that the concept was feasible for use as a space-navigation technique, but because the most stable portions of the radiance were in the near-ultraviolet range, it was usable only during daylight portions of an orbit. To verify that the idea worked from greater distances, NASA asked the astronauts on Apollo 8, 10, and 11 to make visual sightings of the Earth’s horizon using the onboard spacecraft sextant. This exercise was conducted several times en route to and returning from the Moon, and revealed that the sextant had relatively good accuracy compared to radar positioning.-162-
Experiment #18: Supersonic Deceleration Devices
Initially, NASA Langley sponsored experiment #18 to test the concept of inflatable devices. During the late 1950s, engineers thought they could use internal pressure to erect and stabilize structures in space because of the lack of atmosphere and gravity. The inflation of these structures, however, was difficult to investigate on the ground. A test would consist of carrying the structure either internally or externally on the X-15, ejecting it at high altitude under conditions of zero-g and zero dynamic pressure, and then photographing the inflation of the structure. It was expected that the experiment could be packaged in place of the ventral rudder if the equipment was not too large; otherwise, an external store might be required.-164-
After more thought, this concept seemed a bit far-fetched. The experiment was reoriented away from inflatable structures and toward inflatable decelerator devices. In this incarnation, the experiment was sponsored by the FRC to evaluate the drag, stability, and deployment characteristics of various decelerator configurations at Mach numbers as high as 5 and altitudes as high as 200,000 feet. Dr. Heinrich at the University of Minnesota had developed a variety of such devices, and researchers at Langley studied a number of configurations in wind tunnels to determine which ones held the most promise for actual flight tests. The possibilities included inflatable spheres and cones, and various self-inflating parachutes. In December 1964 the plan was to fly the first X-15 decelerator tests during the early summer of 1965 and deploy the decelerator at Mach 4 following burnout. The tests would require the installation of a decelerator tow kit in the tail-cone box. NASA fabricated the modification kits for two X-15 airplanes and gathered preliminary data in April 1965 using an F-104 to drop a decelerator at Mach 1.8 from
57.0 feet. Engineers made some modifications to X-15-3 to support the experiment during the weather down period in early 1966, but apparently never installed the experiment.-1165
Experiment #19: High-Altitude Sky Brightness
The ASD sponsored experiment #19 to determine the intensity, polarization, and spectral distribution of the daytime sky at high altitudes. Researchers would use the information to develop electro-optical tracking systems that were capable of discriminating a star’s optical signal from the surrounding sky’s brightness. Northrop Nortronics was developing a spectrophotometer for use on a Lockheed U-2 reconnaissance aircraft as part of the High Altitude Daytime Sky Background Radiation Measurement Program to survey the sky at altitudes between 20,000 and
70.0 feet in 10,000-foot increments. The Air Force, however, desired data obtained at up to
200.0 feet, and in 1962 the service modified the Nortronics contract to develop instrumentation
for the X-15. The goal was to survey the sky in the range of 3,500-7,500 , with a spectral
resolution of approximately 2 , to support the design of future star trackers. Researchers
extrapolated the data gathered by the U-2 to higher altitudes and used it to predict and verify data acquired by the X-15 since the effects of high-speed aerodynamics were largely unknown. The researchers wanted the X-15 to acquire data from 40,000 feet to 200,000 feet.-166
The High-Altitude Sky Brightness Experiment (#19) surveyed the sky in the range between 3,500 to 7,500 angstroms, with a spectral resolution of approximately 2 angstroms to support the designs of future star trackers. Researchers extrapolated the data gathered by the U-2 to higher altitudes and used it to predict and verify data acquired by the X-15. The spectrophotometer sensor was located in the rear portion of the left wing-tip pod, and flew on both X-15-1 and X – 15-o. (NASA)
Researchers first flew the spectrophotometer in the rear portion of the left wing-tip pod of X-15- 1 on flights 1-50-79 and 1-52-85 to check out its operation. The experiment flew on flight 163-104, but the emergency landing precluded the acquisition of any meaningful data.
Researchers obtained data on flight 1-65-108, and the experiment flew on flight 1-66-111; however, no useful results were obtained because a slow-blow fuse failed. Engineers conducted several tests in an environmental chamber to investigate the fuse, which consistently failed at
140,0 feet and -158°F. They eventually traced the problem to a power connector on the experiment. After repairs were made, the instrument flew several flights aboard X-15-3 beginning with 3-56-83, and acquired useful data on at least two flights.-1167!
Experiment #20: Western Test Range Launch Monitoring
The ASD funded experiment #20 under the name "Pacific Missile Range (PMR) launch monitoring." The goal was to measure from high altitude the signature of an ascending ballistic missile to determine the feasibility of using the ultraviolet spectrum for space-based detection and tracking systems. There was initial concern regarding this experiment because the timing requirements seemed very critical given the short duration of X-15 flights and the acceleration profile of an ICBM. Nevertheless, the Air Force deemed the experiment important for national security and requested six flights in excess of 250,000 feet. In mid-1964 the Air Force awarded a contract to the Northrop Space Laboratories to design and fabricate equipment. A review of the preliminary design revealed that the experiment package and its recording equipment were too large to fit on X-15-1, so the Air Force, NASA, and Northrop were reevaluating the problem as 1965 ended.[168]
Eventually Northrop worked through the problems and NASA installed the experiment during the weather down period in early 1966. The experiment consisted of an optical system, a vidicon camera, a four-spectral-band radiometer, and a servo-driven scanning mirror installed on the extensible elevator under the skylight hatch of X-15-1. The experiment first flew on 15 June 1967 (flight 1-72-125), but an electrical malfunction within the experiment precluded a complete operational checkout. The X-15-1 subsequently carried the experiment on eight additional flights.-116^
The primary target for the experiment would be a Minuteman II ICBM launched from Vandenberg AFB, although some thought was given to trying the experiment against a Titan II target. The Air Force also wanted the X-15 to track multiple Minuteman ICBMs launched from Vandenberg in rapid sequence (simulating an actual wartime response). In each case, the X-15 portion of the experiment would be secondary to other reasons for launching the missiles. Whatever experiment the Air Force was conducting involved the use of a B-52 in addition to the target ICBMs.[170]
The most ambitious of the follow-on experiments was the Western Range Launch Monitoring Experiment (#20) installed under the Skylight hatch on X-15-1. The X-15 was supposed to track a Minuteman ICBM launched from Vandenberg AFB, but the timing of getting the X-15 in position at the exact moment the ICBM was launched never worked. (NASA)
On 22-23 May 1968, representatives from the Air Force, NASA, and Northrop met to discuss various aspects of the upcoming flights. The first order of business was to discuss the security classification surrounding the project, and the Air Force agreed that the only classified data the FRC would receive would be the actual launch time of the targets. The representative from the Strategic Air Command (SAC), Lieutenant Colonel John McElveen, indicated that SAC "will do everything possible to insure a successful coordination with the exception of compromising their primary objective." This would include allowing Vandenberg to adjust its launch times to coincide with X-15 launches as long as the delays were a reasonable length of time.-1171
The attendees spent most of the meeting discussing how to make sure the ICBM and X-15 would be in position at the right time. They decided that, whenever possible, the experiment should be scheduled for between 1000 and 1400 hours Pacific daylight time. The X-15 flight planners would purposefully schedule the X-15 so that it would arrive at its launch point either on time or slightly late, since the Air Force could hold off on launching the target but could not recall it once it was launched. For the multiple-target missions, Vandenberg would launch the Minuteman
ICBMs 30 seconds apart. Procedures allowed the Air Force B-52 to hold while the NB-52/X-15 got into position for launch, and to time the launch of the target ICBMs. Nevertheless, this experiment would have required extraordinary luck to have everything in place at exactly the right time.-1172!
The Air Force apparently put a high priority on this experiment since it was one of the two reasons listed for extending Air Force funding of the X-15 program into 1968. Unfortunately, the first nine attempts to coordinate this aerial ballet failed. On at least two occasions, equipment on the X-15 failed to operate as expected, and on another Vandenberg could not launch the target because of a technical problem. The experiment also required very precise flight-path control. For instance, during flight 1-79-139 the experiment extended 129 seconds after launch. It immediately began searching for the target, but quickly failed after the elevator and azimuth torquers drove against their stops. It was later determined that Bill Dana deployed the experiment slightly before the airplane achieved the 0 2-degree pitch and roll attitude requirement.
Engineers warned Dana and Pete Knight not to extend the experiment until the airplane was stable as it approached apogee.-1172!
As the flight went on, more difficulties arose. About 208 seconds after launch, NASA-1 requested Bill Dana to retract the experiment. Things appeared normal at first, and the experiment retracted without the delays noted on some previous flights. However, the timing was unfortunate since the call was made a bit later than planned, and the automatic timer interrupted the normal action and initiated an emergency-retract sequence. Nevertheless, the experiment successfully retracted. Since a demonstration of the normal retraction sequence was required before the experiment could become "operational," NASA scheduled a flight to check out the mechanism. On flight 180-142, Pete Knight extended the experiment 162 seconds after launch and the sensor went into track mode 5 seconds later. At 240,000 feet, Knight commanded the experiment to retract, but indications at 220,000 feet showed that it had not. Knight activated the emergency mode, with satisfactory results.-11742
Finally, the Air Force and NASA managed the first coordinated launch of the X-15 and a WTR target. Flight 1-81-141 launched from Smith Ranch on a magnetic heading of 169 degrees, within 3 seconds of the optimum time. Bill Dana reached the planned 36-degree pitch angle 30 seconds after launch and held it until burnout at 5,400 fps. The flight experienced a nose-left thrust misalignment that caused 4.5-degree of sideslip, but Dana did not use any rudder input during the exit phase, resulting in a 3-degree error in ground track. The experiment was extended at approximately 235,000 feet as planned (roughly 137 seconds after X-15 launch), but 2.8 seconds later all power was lost to the system and the experiment retracted. The flight did not acquire any useful data.-11752
The last attempt was on the 200th X-15 flight. The launch attempt on 21 November 1968 was coordinated with Vandenberg, and the Air Force launched a Minuteman II at 1028 hours; unfortunately, the X-15 never left the ground because of a problem with the NB-52A. By this time the Air Force had spent $700,000 on the experiment, not counting the normal flight costs of the X-15 (which carried other experiments as well) or the cost of the Minuteman ICBMs (which were being launched anyway).-11762
Experiment #21: Structural Research
hypersonic outer wing panel was required to withstand temperatures beyond Mach 8 without the use of ablative coatings. Both panels needed extensive instrumentation for loads, stresses, and temperatures. The FRC received proposals in late 1964, but never built or tested the panels. By the end of 1965, NASA placed this experiment on "inactive" status.-177
Experiment #22: Air-Breathing Propulsion
Very early on, a small group of researchers believed that the X-15 was a potentially useful test bed for various air-breathing propulsion system components, including complete ramjet engines. The airplane was capable of speeds in the Mach 3-5 region, in which inlet and exit problems were greatest, and a ramjet engine was considered a desirable method of propulsion. The X-15 would provide testing under true atmospheric conditions (ground-test facilities were seldom able to achieve the proper stagnation temperatures and Reynolds number). The X-15 would also permit closer control of test conditions than was possible with ground-controlled rockets, such as those launched at the Pilotless Aircraft Research Division (PARD).178-
The most desirable position for the propulsion test package appeared to be in place of the ventral rudder, although it had to be jettisoned before landing to provide adequate clearance for the landing gear. At this point Dick Day and Bob Hoey had not proposed to fly the X-15 with the ventral removed, so this was one of the larger unknowns of the initial engine proposal. Two wing – root tanks, each holding about 100 gallons of liquid hydrogen, carried fuel for the ramjet. Other positions for the engine would be possible if permanently attached engines were required. For example, a small engine could replace one of the wing root tanks or a pair of engines mounted under the wing tips.179
The FRC proposed the first truly serious version of this experiment as "an extensive air-breathing engine development program… in which one or more sub-scale modular experimental engines would be flown in a true flight environment aboard the X-15." Somehow, the experiment took on a life of its own and morphed into the hypersonic research engine (HRE) project (discussed separately below).
Experiment #23: Infrared Scanning Radiometer
The ASD and later the Air Force Research Technology Division sponsored experiment #23 as a follow-on to the infrared exhaust signature experiment (#10) to determine the feasibility of an infrared imaging instrument operating at Mach 3-5 at altitudes between 90,000 and 120,000 feet. NASA installed a Singer scanning radiometer in the lower portion of the instrument compartment of X-15-1 during mid-March 1965. The experiment looked through an Iratran IV window in the lower fuselage and recorded the reflected solar radiation as well as radiation emitted by Earth.-1180-
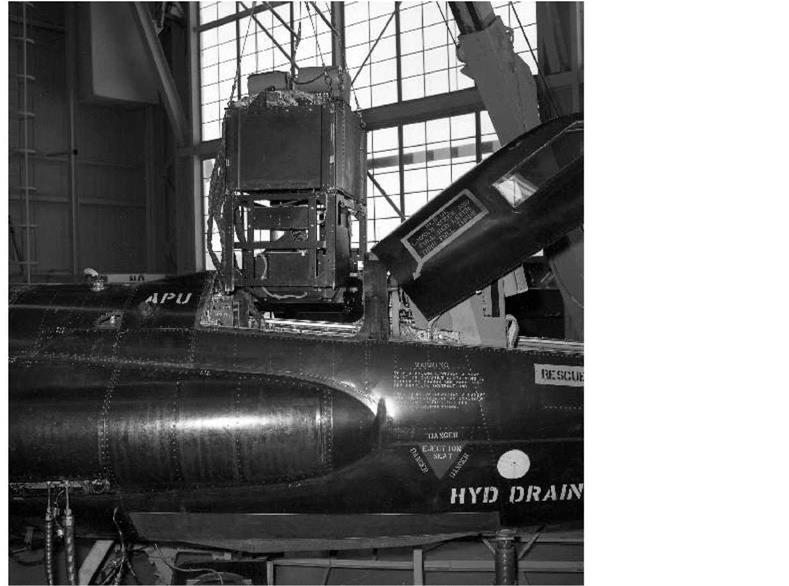
|
The Infrared Scanning Radiometer Experiment (#10) was used to determine the feasibility of an infrared imaging instrument operating at Mach 3-5 at altitudes between 90,000 and 120,000 feet. A Singer scanning radiometer was installed in the lower portion of the instrument compartment of X-15-1 during mid-March 1965. The experiment looked through an Iratran IV window in the lower fuselage and recorded the reflected solar radiation as well as radiation emitted by Earth. (NASA)
The first of six flights was made on 26 March 1965 (1-53-86); the last was flight 1-60-99 on 30 September 1965. Actually, flight 1-59-98 was supposed to be the last flight, but a broken wire had precluded the acquisition of any useful data. The Air Force decided to leave the experiment on the airplane for Pete Knight’s familiarization flight (1-60-99), although Knight did not attempt to fly the profile normally required for the experiment. Despite this, the experiment obtained good data. Although the experiment only generated a crude, two-dimensional image, it proved that it was possible to perform infrared reconnaissance at hypersonic speeds. The development of a Germanium metal window that was transparent to infrared photography offset the masking effect of an aerodynamically heated window. This work reportedly advanced the development of infrared line scanners, such as the Texas Instruments AN/AAS-18, that went on to operational service on various Air Force reconnaissance aircraft. The Earth Resources Development Agency (ERDA) also capitalized on this technology by contracting with the Mead Corporation to develop several portable suitcase-size scanners for use on general aviation aircraft to detect various forms of pollution.-1181!
Experiment #24: High-Altitude Infrared Background Measurements
Experiment #24 was sponsored by the Air Force Research Technology Division to obtain high – altitude infrared measurements of the Earth, horizon, and sky in the 3-5- and 8-14-micron regions for use in various surveillance applications (i. e., target tracking). The measuring device was a simple dual-channel, solid-state radiometer with a flat rotating mirror that provided a circular scan. A self-contained liquid-helium system cooled the experiment. The Autonetics Division of North American built the experiment, and NASA installed it in the right wing-tip pod on X-15-1 during the weather down period in early 1966. Researchers requested three flights to altitudes above 150,000 feet, but the only verifiable attempt was on the aborted 200th flight.11821
Experiment #25: Optical Background Measurements
The Air Force Research Technology Division sponsored experiment #25 as an extension of the ultraviolet exhaust plume experiment (#3). The objective was to obtain narrow-band optical – background measurements covering the spectral region between 0.3 and 1.3 microns. Northrop modified the existing Barnes high-resolution spectrometer and associated equipment from experiment #3 to operate at visible wavelengths.11831
Researchers installed the experiment in the X-15-3 tail-cone box to determine the background characteristics of the atmosphere and Earth when viewed with a narrow-band receiver. The data was applicable to future laser systems for space vehicles. The experiment had flown twice by the end of 1965, but had gathered little usable data because of system noise. Researchers modified their equipment and the experiment flew on two additional checkout flights in mid-1966.11841
Flights 3-53-79 and 3-54-80 carried the experiment. The first flight failed to acquire useful data due to improper instrumentation, and Bill Dana inadvertently turned off the experiment after only 131 seconds on the second. The experimenter reported, however, that the limited data collected was satisfactory. The experiment was last flown on flight 3-56-83, and good data were collected.11851
Experiment #26: Supersonic Transport (SST) Structural Demonstration Techniques
The Air Force Research Technology Division sponsored experiment #26 to evaluate a new technique for determining the mechanical loads and thermal stress experienced by aerospace vehicles exposed to a thermal environment. Republic Aviation developed an experimental analytical procedure that enabled the determination of loads, deformation, and stresses from given strain and temperature measurements. Laboratory tests on a box beam and frame structure yielded data with a calculated accuracy of 10%. This procedure could be proof-tested on the X – 15 and then used to validate the analytical design methods and structural load criteria used for the SST and other advanced aerospace vehicles.11861
Researchers proposed to install thermocouples and strain gages in the fuselage-wing attachment structures and fabricate one horizontal stabilizer with strain gages and thermocouples installed on the spars. Approximately 360 sensors would have been required to perform the tests.11871
The researchers forwarded a suggested program for using this technology to the Federal Aviation
Administration (FAA) for possible funding. The FAA endorsed the requirement but thought it would be more appropriate for NASA to fund the experiment. NASA reviewed the experiment and agreed that a well-verified means of interpreting flight loads and thermal stress data was essential for the future SST, and that NASA should be responsible for developing the technique. However, NASA did not believe that a specific experiment of this magnitude was required to assess the Republic method.-1188-
Eventually, however, the FRC approved and sponsored at least part of the experiment, which was broken into two parts called, logically enough, Phase I and Phase II. The Phase I program used a slightly instrumented set of horizontal stabilizers during several flights to gather baseline airplane data. The tests began on flight 3-52-78 on 18 July 1966 and concluded on flight 3-61-91 on 20 July 1967. Not every flight collected data, due to a variety of malfunctions, but sufficient data were gathered. On several Phase I flights the pilots noted a slight buffet and beta excursion under some flight conditions, a phenomenon the researchers could not explain.-189-
Phase II included a new set of horizontal stabilizers that were manufactured by North American during May 1966. NASA instrumented the left-hand unit with 128 strain gages and 125 thermocouples, and tested it in the High Temperature Loads Calibration Laboratory before installing it on X-15-3 in time for flight 3-62-92. To investigate buffet and beta excursions experienced during the Phase I portion of the experiment, pilots performed maneuvers at Mach 2.5, 3.7, and 4.0 with a pull-up to approximately 12 degrees angle of attack made at each Mach number. The pilots did not notice a buffet or beta excursion at the two higher Mach numbers, but at Mach 2.5 they experienced results similar to those encountered on the two previous flights.
The beta excursion registered about 3 degrees, but the pilot was not positive that buffet occurred during this maneuver. Buffet had been experienced at 10.5 degrees on the previous flight. The only configuration change that occurred between the flights was the replacement of the Phase I horizontal stabilizer with the Phase II units. To evaluate this, NASA reinstalled the original horizontal stabilizers for flight 3-63-94. The pilot did not notice any buffet, leading researchers to suspect some minor manufacturing flaw in the new horizontal stabilizers. Unfortunately, X-15- 3 was lost before researchers could complete any further work. Since the experiment depended on the PCM telemetry system in X-15-3, researchers could not move it to X-15-1.[190]
Another test in this series was to study of the effect of various discontinuities on local surface heating between Mach 4 and Mach 6. To avoid having to make detailed local measurements, the experiment was designed to determine the ratio of the heating rates on two symmetrically located panels under the center fuselage and on the wing tips. One panel in each location would have the discontinuity while the other would not. Discontinuities included forward and aft facing steps, wavy surfaces (sinusoidal distortions), streamwise corners, and antenna posts. At least two X-15- 3 flights included the step panels, and the wavy panels made at least three flights.-119^
Experiment #27: Hycon Camera
The Air Force Research Technology Division sponsored experiment #27. It was conceptually an extension of experiment #5, which had used KC-1 and KS-25 cameras to acquire optical data at speeds between Mach 6 and Mach 8. This experiment used X-15-2 and was approximately 80% complete at the time of Jack McKay’s accident in the second airplane. The experiment, however, continued after X-15A-2 returned to service.-192
resulting data permitted the investigation of contrast attenuation at high altitudes and showed the feasibility of performing aerial photography from supersonic vehicles. These tests began as early as 9 October 1962 (flight 2-30-51) when the 6-inch oblique camera photographed the Las Vegas area from very high altitude using black and white film. During flight 2-39-70 on 22 June 1965, the 6-inch camera used color film to take a similar photo, and the 12-inch camera photographed Indian Springs AFB using color-infrared Ektachrome film. These tests included the evaluation of a special film, Kodak SO-190, which had a resolution of almost 200 lines per millimeter, a speed index of 6, and very low granularity.193-
In late December 1965, a new Maurer model 500 camera replaced the Hycon in the center-of – gravity compartment on X-15A-2. NASA installed the camera during the weather down period during early 1966, with the intent to carry it throughout the envelope-expansion flights beginning with flight 2-49-86. Preflight tests of the system indicated that the experiment was functioning satisfactorily, but checks of the system before launch showed that the platform would not erect properly. Despite this, the camera data were satisfactory and the quality of the resulting photographs was excellent. The X-15A-2 carried the camera on two more flights, also with satisfactory results.-194!
A Hycon KA-51A "Chicago Aerial" camera then replaced the Maurer, which only flew one time on flight 2-52-96. For the next flight of X-15A-2, NASA removed the Hycon experiment and installed an aft-viewing Millikan 16-mm camera to photograph the dummy ramjet.195-
Experiment #28: X-Ray Air Density
There is no record of what organization sponsored experiment #28. The experiment consisted of an X-ray tube and detector located in the forward portion of the right wing-tip pod. The wing-tip pod skin scattered the X-rays, and solid-state cells measured the backscatter to determine air density. The design and fabrication of this experiment began in late 1965 and several flights during 1967 and 1968 apparently carried it, although no results could be ascertained.196
Experiment #29: JPL Solar-Spectrum Measurements
The JPL sponsored experiment #29, which consisted of a spectrometer containing 12 sensors and a servo-positioning system installed in the rear section of the left wing-tip pod of X-15-1. Researchers wanted to use the data to improve the methods of correcting for atmospheric absorption, determine the absolute energy of the sun, and calibrate solar cells to validate solar simulation. JPL built the experiment in early 1966, but a pop-up hatch used to expose the spectrometer failed the qualification test in April 1966. Researchers subsequently redesigned the experiment to use a quartz window in the pod instead of a hatch to eliminate the problem. At the same time, researchers modified the experiment to use the new PCM telemetry system in X-15-
3.1197]
The experiment first flew on flight 3-58-87, and later on two additional flights. A preliminary review of the data showed excessive electrical noise on the data channel, but researchers considered the data acceptable.198-
Experiment #30: Spectrophotometry
have a sponsor of formal approval, although it did apparently receive an experiment number. By the end of 1966, NASA had canceled the experiment before any actual hardware development was undertaken.[199]
Experiment #31: Fixed Alpha Nose
The FRC sponsored the fixed-ball-nose experiment to investigate the feasibility of using a fixed – sphere-cone sensor to measure air data parameters in extreme flight environments. Rodney K. Bogue and John P. Cary built the experiment hardware.-1200
The standard X-15 ball nose proved to be remarkably reliable given its operating environment, performing less than satisfactorily on only one of its first 70 flights. Nevertheless, in retrospect, the ball nose was an overly complicated solution to the problem. All that was really needed was a way to compute the difference in pressure between opposing ports, not to drive the entire sensor to seek the null pressure.
Late in the program, NASA flew an experiment that used a non-moving sensor to detect the angle of attack. Researchers attached a fixed ball nose on the left wing-tip pod, permitting the use of the normal ball nose for comparison purposes. The sensor consisted of a ported sphere, 4.36 inches in diameter, mounted on the nose of the pod. The total length of the sensor was 18.75 inches, but it looked like a simple extension of the pod. Five pressure ports were located on the pod. One port was 5 degrees below the zero angle-of-attack stagnation point, and the remaining four ports were located symmetrically around this point in the vertical and horizontal planes. The vertical ports were used to measure the angle of attack. Researchers planned to use the horizontal ports for the angle of sideslip, but this was never implemented. The sensor flew on a single flight (1-53-86) to Mach 5.17 with Bob Rushworth at the controls.-1200
The standard ball nose had a demonstrated measurement error of less than 0.25 degree over its entire operating range. On its single flight, the fixed nose did not return the same absolute data as the ball nose. This was not surprising since the wing-mounted device and the nose-mounted unit operated in different flow fields. Several factors affected the performance of the wing – mounted device, including 1) flow disturbances and shock-wave impingement from the forebody of the X-15, 2) rotational flow about the lifting-wing surface (the latter effect was particularly noticeable during approach and landing), and 3) suspected small deflections (bending and twisting) of the wing that created a variable offset between the normal – and fixed-ball-nose devices. Nevertheless, the fixed-ball-nose data showed the same trends as the ball-nose data. Researchers concluded that the fixed ball nose was a feasible alternative to the ball nose.-1200
Confidence was high enough that NASA manufactured a "fixed alpha nose" and installed it on a wing-tip pod for six of the last seven X-15-1 flights. Again, the data did not precisely match those obtained with the ball nose, but were repeatable enough that researchers could make consistent correlations. A conceptually similar system was used on the Apollo launch escape system to provide limited air data to the astronauts in case of an abort forced them to separate the capsule from the Saturn booster. NASA designed and installed a similar system, using ports in the nose cone, on the Space Shuttle Columbia as the Shuttle Entry Air Data System (SEADS) experiment between 1986 and 1991.-1200