In early 1957, just as North American was preparing to begin modifications on the B-36, the X – 15 Joint Operations Committee began considering replacements for the B-36 for various reasons. There were some concerns that the research airplane would not be as stable as desired during launch because of the relatively slow speed of the B-36. Another reason was that as the weight of the X-15 and its subsystems grew, the Air Force and NACA began to look for ways to recover some of the lost performance; a faster carrier would compensate somewhat for the increased X – 15 weight. Perhaps most vocally, personnel at Edwards believed that the 10-engine B-36 would quickly become a maintenance nightmare since the Air Force was already phasing it out of the inventory. A lack of spare parts and depot maintenance capabilities for the B-29 and B-50 carrier aircraft had already delayed the X-1 and X-2 programs on several occasions.1871
A survey by North American identified the Boeing B-52 Stratofortress, Convair B-58 Hustler, and
Boeing KC-135 Stratotanker as possible B-36 replacements. It is interesting to note that Douglas had apparently chosen the B-52 for their model 671 study four years earlier.-88
The supersonic B-58 was attractive from a performance perspective, but looked less attractive from the maintenance and availability standpoint. Nevertheless, on 22 January 1957, future X-15 pilot Neil Armstrong traveled to the Convair plant in Fort Worth to discuss the possibility of using a B-58 to launch the research airplane. The first problem was that the 22-foot wingspan and 18- foot tail-span of the X-15 both intersected the plane of the rearward-retracting main gear on the B-58. This would have necessitated moving the entire X-15 forward of the desired location. Convair engineers believed that this might be possible, but it would require designing a new nose gear for the B-58 since the X-15 would block the normal nose gear. Another possibility was to beef up the X-15 nose gear and use it while the pair was on the ground. The inboard engine nacelles on the B-58 would likely need to be "toed" outward or simply moved further out on the wing, and either would have necessitated major structural changes. Engineers would need to design a way to fold the X-15 vertical stabilizer because they could not make room for it within the B-58 fuselage without severing a main wing spar. The design of the B-58 included a weapons/fuel pod that weighed 30,000 pounds, only slightly less than the X-15. However, the baseline mission included using the fuel in the pod prior to dropping the pod, and the maximum drop weight was only 16,000 pounds. This would necessitate a new series of tests to validate that a heavier object would separate cleanly, especially at supersonic speeds. However unfortunately, the B-58 was obviously not going to work.-89
The landing-gear configuration on the KC-135 and B-52 precluded carrying the X-15 under the fuselage, as had been the practice in all earlier research programs. Although the performance and availability of the KC-135 made it attractive, nobody could figure out where to carry the research airplane since the Stratotanker had a low-mounted wing and relatively short landing gear. Engineers quickly dropped the KC-135 from consideration.-1901
The B-52 also offered an excellent performance increment over the B-36, and since the Boeing bomber was still in production, the availability of spare parts and support should not become an issue. There was a large space on the wing between the fuselage and inboard engine nacelle that could be adapted to carry a pylon, and investigations were already under way to install similar pylons on later B-52s to carry air-to-surface missiles. In May 1957, NASA directed North American to perform an initial feasibility study on using the B-52 as an X-15 carrier. The study lasted several weeks and the results were favorable. At a meeting on 18-19 June 1957, the program officially adopted the B-52 as a carrier aircraft. Representatives from the FRC discussed concerns about maintenance and availability issues, and NASA recommended procuring two carrier aircraft to ensure that the flight program would proceed smoothly. The Air Force subsequently authorized North American to modify two B-52s in lieu of the single B-36.-91
The North American investigations showed that the X-15, as designed, would fit under the wing between the fuselage and inboard engine pylon at an 18% semi-span location. The wing structure in this location was capable of supporting up to 50,000 pounds, so the 31,275-pound research airplane did not represent a problem. Nevertheless, this was not the ideal solution. The X-15 pilot would have to be in the research airplane prior to takeoff, and the large weight transition when the B-52 released the X-15 would present some interesting control challenges.-921
Lawrence P. Greene, the North American chief aerodynamicist wrote, "One item which caused considerable concern in the early evaluation was the fact that in this installation, the pilot could not enter the airplane in flight as had been possible in the B-36. This limitation was of concern from both the fatigue and safety aspects; however, the time from take-off of the B-52 to launching the X-15 is about 1.5 hours, and considerable effort has been expended in plans for making the pilot comfortable during this time. In the event of an emergency, the configuration permits the pilot to eject safely while the X-15 and B-52 are still connected.’4931
Further analysis and wind-tunnel tests indicated that the potential problems were solvable, and that the increase in speed and altitude capabilities was desirable. Researchers conducted additional wind-tunnel tests of a 1/40-scale model in the Langley 7 by 10-foot tunnel and the University of Washington wind tunnel to explore possible flutter problems, but did not discover any critical issues. Researchers installed six-component strain-gage balances in both the B-52 and X-15 models, and the B-52 model had additional strain gages and a pressure gage located in the horizontal stabilizer to obtain measurements of possible tail buffet created by the X-15 installation.-1941
Initially the X-15 was to be carried under the left wing of the B-52. It was moved to the right wing to "permit easier servicing of the X-15 when installed on the B-52," although exactly what was easier to service was not described. Researchers had conducted most of the wind-tunnel tests with models of the X-15 under the left wing. However, since both aircraft were largely symmetrical, researchers decided that the test results were equally as valid for the right-wing configuration. The initial design also had an anti-buffet fairing that partially shielded the pylon from the airflow, but wind-tunnel tests showed that the fairing did not significantly help anything, and the engineers subsequently deleted it.1951
Originally, the Air Force indicated that it could make the two prototype B-52s (the XB-52 and YB – 52) available to the X-15 program. Personnel at Edwards feared that the use of these two nonstandard aircraft would result in the same maintenance and parts availability problems they were attempting to avoid. By August 1957 the Strategic Air Command agreed to make an early- production B-52A available, and the Air Force subsequently assigned serial number 52-003 to the program in October 1957. In May 1958 the Air Force also assigned an early RB-52B (52-008) to the X-15 program. Both aircraft had been involved in isolating problems with the B-52 defensive fire control system, and Boeing delivered each aircraft to North American after the completion of their test programs.-1961
On 29 November 1957 the B-52A arrived at Air Force Plant 42 in Palmdale, California, after a flight from the Boeing plant in Seattle. North American placed the aircraft into storage pending modifications. On 4 February 1958, technicians moved the aircraft to the North American hangar and began modifying it to support the X-15 program. The aircraft, now designated NB-52A, flew to Edwards on 14 November 1958 and was subsequently named "The High and Mighty One." The RB-52B arrived in Palmdale for similar modifications on 5 January 1959, and, as an NB-52B, flew to Edwards on 8 June 1959; the airplane briefly wore the name "The Challenger.’4271
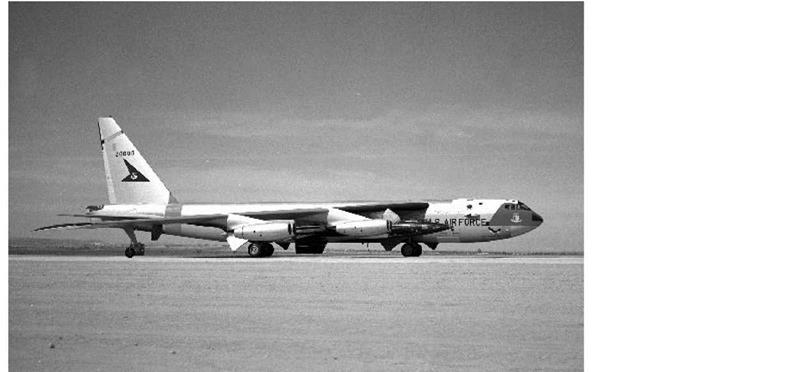
|
The Air Force initially contributed the third production B-52A (serial number 52-003) to the X-15 program. This airplane had been used in initial B-52 testing at Boeing in Seattle, and came to Edwards when its testing duties were completed. The airplane was modified by North American to support carrying and launching the X-15. The aircraft, now designated NB-52A, flew to Edwards on 14 November 1958 and was subsequently named The High and Mighty One. (NASA)
The major modifications to the two NB-52s included the following:^981
1. The no. 3 right main wing fuel cell was removed to allow the installation of pylon tie fittings and supports in the front and rear wing spars.
2. The inboard flap mechanism on both wings was disconnected, and the flaps were bolted to the flap tracks. A cutout through the right inboard flap provided clearance for the X-15 vertical stabilizer.
3. A pylon was installed between the right inboard engine nacelle and the fuselage. The pylon contained a primary hydraulic and a secondary, pneumatic-release mechanism for the research airplane.
4. Changes to the NB-52 avionics included the addition of an AN/APN-81 Doppler radar system to provide ground-speed and drift-angle information to the stable platform in the X-15, an auxiliary UHF communications system to provide additional communications channels, and a change in the AN/AIC-10 interphone system to provide an AUX UHF position.
5. The fuselage static ports were removed from the right side of the NB-52 to allow installation of the forward television camera. The airspeed system was recalibrated to use only the left static ports. This worked surprisingly well, even during sideslip maneuvers, with "no measurable difference" noted.
6. Two television cameras were installed in streamline fairings on the right side of the NB-52. The rear camera pointed generally forward and was equipped with the zoom lens to allow the launch operator to focus on areas of interest on the rear of the X-15. The forward camera used a fixed-length lens pointed outward and slightly rearward to allow a view of the X-15 forward fuselage. Two monitors were located at the launch operator position, and either could show the view from either camera. Four floodlights and three 16-mm motion picture
cameras were also installed. Two of these were Millikan DBM-5 high-speed units located in a window on the right side of the fuselage at station 374 and in an astrodome at station 1217. The third was an Urban GSAP gun camera mounted in the pylon pointed downward to show X-15 separation.
7. The NB-52 forward-body fuel cell was removed to provide space for inspecting and maintaining various fluid and gas lines installed in the wing. The mid-body fuel cell was removed and the fuselage area above the bomb bay was reworked to provide space for 15 nitrogen and nine helium storage cylinders. Early during the flight program, a separate liquid-nitrogen supply was added to the pylon to cool the stable platform on the X-15.
8. Two stainless-steel liquid-oxygen tanks (a 1,000-gallon "climb" tank and a 500-gallon "cruise" tank) were installed in the bomb bay. The tanks were not jettisonable, although the contents could be vented through a streamlined jettison line protruding from the forward left side of the bomb bay. Liquid oxygen would be sucked into the right rear landing gear well if the doors were opened while liquids were being jettisoned; this was procedurally restricted.
9. A launch operator station replaced the normal eCm compartment located on the upper rear flight deck. After the first flew flights with X-15-1, an astrodome-type viewing window was added to the NB-52 above the forward television camera in case the video system failed, and a duplicate set of controls for the liquid-oxygen top-off system were located above the window to allow the launch operator to top off the X-15 while looking out the window. A defrosting system was provided for the window, and two steel straps across the window provided safety for the launch operator in case the window blew out.
10. Changes to the NB-52 flight deck included the addition of a master launch panel on the lower left side of the main instrument panel, launch-indicating lights in the pilot’s direct field of vision, a normal launch switch on the left console, and an emergency launch handle below and to the left of the master launch panel. Changes were also made to the B-52 fuel control panel in both aircraft to reflect the removal of the fuel cells and eliminate the external tank position.
11. Breathing oxygen was made available to the NB-52 crewmembers at all times. In addition, oxygen was tapped from the NB-52 oxygen system to supply the X-15 research pilot with breathing oxygen until flight release.
12. A high-speed wheel, tire, and braking system was installed on the NB-52 because the original landing gear was only rated to 174 knots. The new system incorporated an adequate margin for no-flap takeoffs and landings at heavy weights, and was rated to 218 knots.
13. All military systems, including the tail turret and defensive fire-control system, were removed. The modifications to the rear fuselage to delete the tail turret differed between the two aircraft. The ability to carry the reconnaissance pod on the RB-52B was also deleted.
14. Later in the flight program, additional instrumentation was added to the launch operator position to allow monitoring of the MH-96 adaptive flight control system and X-20 inertial flight data system. A "stable platform control and monitoring unit" was also added to the NB-52B to allow the launch operator to monitor and control the stable platform during captive-carries of the pod-mounted system used for post-maintenance validation.
These changes differed somewhat from those initially proposed for the NB-52. For instance, the original design had a pressurized compartment in the bomb bay for an observer. When North American deleted this from the design, engineers moved the liquid-oxygen top-off tank there instead. The launch operator position was moved from the left side of the aircraft to the right side to permit "continuous observation of the research vehicle" after the X-15 itself was moved to the right side. This also allowed the launch operator to remain in his ejection seat for the entire launch process (previously he had to stand up occasionally to visually check the X-15).[99]
The change from a B-36 to a B-52 did not come cheaply. Although the basic aircraft was provided
at no charge to the program, North American submitted a bill for an additional $2,130,929.06 for the modification of the first B-52. The second airplane cost somewhat less since it did not require wind-tunnel testing and the basic engineering was already complete.
The Air Force named Captain Edward C. Gahl as the project pilot for the NB-52 carrier aircraft in 1957. Gahl was well up to the task. He was a graduate of the Experimental Test Pilot School and had been involved in flight-testing the B-52 and KC-135 prior to joining the carrier program. Unfortunately, Gahl perished in a mid-air collision on 16 June 1958, long before the NB-52A had completed its modifications. Captain Charles C. Bock, Jr., replaced him as the chief carrier pilot.™
After the modifications to the NB-52A were completed, engineers from the Air Force, Boeing, NASA, and North American conducted a ground vibration test on the pylon using the X-15-1. The tests built on data already accumulated by Boeing-Wichita while the B-52F was being integrated with the North American GAM-77 Hound Dog missile.-11011 Technicians constructed a structural steel frame to make the NB-52 wing as rigid as possible, effectively preventing any movement by the NB-52 wing, pylon, horizontal stabilizer, or fuselage. The X-15 was excited by electromagnetic shakers and sensors mounted on the X-15 fuselage, wing, horizontal stabilizer, and vertical stabilizers measured the amplitude of motion for various frequencies. Researchers used these data to determine the natural vibration frequencies of the pylon to verify data obtained from a series of flutter model tests of the NB-52/X-15 combination conducted by Boeing in a low-speed wind tunnel. The results from these two tests demonstrated that the flutter speed of the NB-52 when carrying the X-15 was well above the required launch conditions.-11021
However, there was some concern about the jet exhaust from engine nos. 5 and 6 of the NB-52 impinging on the X-15 empennage. Specifically, the engineers worried that the engine acoustics would detrimentally affect the X-15’s structural fatigue life. To mitigate this concern, at least initially, the engineers decided the NB-52 pilots would restrict engine nos. 5 and 6 to 50% thrust while carrying the X-15. The engineers and pilots believed this was an acceptable compromise between protecting the X-15 and the need to provide adequate power and control of the NB-52 during takeoff. At 50% power on these two engines, the tip of the X-15 horizontal stabilizer was exposed to 158 decibels and the sides of the vertical stabilizers were exposed to 144 decibels; at 100% power each value was about 10 decibels greater.-103
Although it appeared feasible to operate the carrier aircraft engines at reduced power, it was not desirable, so North American began redesigning some parts of the X-15 to increase their fatigue life. The modifications to the vertical stabilizers consisted of increasing the rivet diameter, using dimpled-skin construction instead of countersunk rivets, and increasing the gage of the corrugated ribs along the edge where they flanged over to attach to the cap strip. The horizontal stabilizer used larger rivets and dimpled construction.104
To verify the effectiveness of the modifications, researchers conducted several acoustic tests to establish the structural fatigue life of both the original and modified aft X-15 structures. A static ground test was run on a simulated X-15 empennage to determine the sound levels beneath the pylon (the hastily-constructed structure could not be attached to the pylon) with the B-52 engines operating at 85% rpm (equivalent to 50% thrust). Both the original and modified test panels withstood 20 hours of operation with no failure. Subsequent analysis indicated that the original panels would be adequate for operation at 50% power, and the new panels would allow operation at 100% power. North American decided to retrofit all three X-15s with the new structure, which would take several months.-103
Following completion of these tests, Captain Bock and Captain John E. "Jack" Allavie tested the NB-52A along with launch panel operator, William "Bill" Berkowitz from North American. To eliminate possible interference with the X-15, the engineers decided to bolt the inboard flaps in the closed position, meaning that the NB-52 pilots would have to fly the airplane without flaps. Therefore, the pilots dedicated the initial flights to developing techniques for no-flap operations and measuring various performance parameters of the modified NB-52. The takeoffs were conducted using 50% power on engine nos. 5 and 6 since it appeared that initial flights would be restricted to this power setting until all three X-15s were modified. The NB-52 also accomplished qualitative stability tests over the speed and altitude ranges anticipated for the X-15 program.-11061
There was very little no-flap, takeoff-and-landing experience with the B-52 available to draw on, so Bock and Allavie conducted the initial tests using predicted information and recommendations from Boeing personnel. Engineers based the anticipated takeoff speeds and distances on a lift coefficient of 0.75, meaning that the NB-52 had to be rotated about the aft main gear to an attitude that would produce the correct amount of lift. This was contrary to normal B-52 takeoffs where all four main gear lift at the same time. The pilots also realized that the 10% chord elevator used on the B-52 would have limited authority and that the horizontal-stabilizer trim setting would be important if reasonable takeoff distances were to be attained.-1071
The flight tests involved a fair amount of trial and error. For instance, on the first test at a gross weight of 315,000 pounds (the maximum predicted weight for an actual X-15 flight), Bock set the stabilizer trim 0.5 degrees more than the normal recommended trim of 0 degrees. The pilots ran engine nos. 5 and 6 at 50% power, and fuel loading simulated the weight (but not the drag) of the X-15 on the right wing. The predicted takeoff distance was 10,500 feet at a speed of 176 knots. However, the NB-52 would not rotate, even with the control columns pulled all the way back.
After the airplane passed the 10,000-foot marker on the runway, the pilots went to full power on engine nos. 5 and 6, and the aircraft broke ground at 12,650 feet at 195 knots. Engineers later calculated the actual lift coefficient for this takeoff at 0.639. During a normal B-52 takeoff with the flaps down, all four main gear leave the ground simultaneously and the lift coefficient is approximately 0.55.1081
Subsequent takeoff tests established that a trim setting of 2 degrees nose up was the optimum setting (this represented one-half of the available trim). This setting produced reasonable takeoff distances and a rapid but controllable rotation just prior to liftoff, with the pilot holding the column all the way back. The maximum lift coefficients were later determined to be approximately
0.71.11091
Landings also proved challenging. Again, the airplane needed higher than normal lift coefficients during landing in order to produce reasonable touchdown speeds and landing distances. Unlike the traditional B-52 landing on all four main gear at once, the NB-52s landed on their two aft main gear. The problem was that the designers had not intended the B-52 to do this. Very little control could be achieved as the aircraft rotated to a level attitude, and the forward main gear usually hit with a noticeable impact. Accelerometers installed in the pylon after the initial landing tests measured impact loads of 1.5-1.8 g. The engineers considered these annoying but acceptable.-11101
After the front main gear touched down, the pilots fully extended the NB-52 air brakes and the drag chute deployed at 140 knots. When landing at heavier weights, such as when returning with the X-15 still attached, the pilots used moderate braking. When these techniques were used with a 300,000-pound airplane, the touchdown speed was 172 knots and the landing roll took 10,800 feet. At 250,000 pounds, touchdown occurred at 154 knots and light braking used only 9,300
feet of runway. The importance of the drag chute was telling: one landing at 267,000 pounds with a failed drag chute required over 12,000 feet to stop even with heavy braking, and resulted in one brake being severely warped, necessitating its replacement.111
The NB-52 pilots now felt confident that they could control their airplane with the X-15 attached, so the first captive flight was attempted. The right wing sat on its outrigger wheel during the initial takeoff roll in order to keep spoiler extension and the associated drag at a minimum. The engineers did not expect the additional drag of the X-15 to result in any serious degradation of low-speed performance; however, there existed some concerns about the possible impingement of the X-15 wake on the right horizontal stabilizer of the NB-52.1121
Despite the concerns about exhaust impingement from engine nos. 5 and 6, the X-15 program had not taken a firm stand on what power levels to use. Bock and Allavie therefore decided to use full power on all eight engines for the flight on 10 March 1959. The takeoff gross weight was 258,000 pounds and the center of gravity was located at 26.5% mean aerodynamic chord (MAC). The actual takeoff distance was 6,085 feet and liftoff occurred at 172 knots. The lift coefficient developed on this takeoff was 0.66 since the pilots did not attempt to achieve maximum performance. Bock just wanted to demonstrate that the mated pair would actually fly as predicted, which it did for 1 hour and 8 minutes. The second flight (which was supposed to result in an X – 15 glide flight, but did not due to a radio failure) produced largely similar results. On the third flight (another unsuccessful attempt at a glide flight) engine nos. 5 and 6 were set to 50% thrust until an indicated airspeed of 130 knots was reached, and then they were advanced to full power. This procedure extended the takeoff distance to 7,100 feet at the same gross weight and similar atmospheric conditions.-1113!
Following takeoff, engine nos. 5 and 6 were set to 50% thrust at 5,000 feet altitude and the mated pair continued to climb using a circular pattern around Rogers Dry Lake. This kept Scott Crossfield in the X-15 within gliding distance of a suitable lake in the event of a possible emergency jettison. The NB-52 pilots flew all of these early tests to an altitude of 45,000 feet and Mach 0.85, which was pretty much the maximum performance of the mated pair. Bock and Allavie flew simulated launch patterns and practiced emergency and aborted launch procedures, and Crossfield accomplished X-15 propellant jettison tests using a water-alcohol mixture that included red dye. Before each flight, technicians covered the underside of the right horizontal stabilizer of the NB-52 with a powdery substance so that the impingement would be easy to identify.-1141
Since the X-15 horizontal and vertical stabilizers used for these initial carry flights were the original design, the engineers decided to inspect them after the third flight. The inspection revealed several structural failures in the upper vertical stabilizer. For the most part, the corrugated ribs had failed where they flanged over to attach to the cap strip, but the most extensive failure was an 18-inch separation of the rib from the flange on the side away from the NB-52 engines. Subsequent investigation showed that the failures were largely a result of a previously unsuspected source: the turbulent airflow created by the X-15 pylon and the B-52 wing cutout. Researchers made pressure measurements to determine the exact environment around the wing cutout. Fortunately, the subsequent analysis indicated an acceptable fatigue life for the modified X-15 structures, even though the engineers had not factored this particular environment into the design. After this round of tests and analysis was completed, the pilots made most subsequent takeoffs with all eight B-52 engines operating at 100% power.-1151
at Edwards during the summer were conducted in the early morning in any case, and if the takeoff roll was computed to be too long, one of the lakebeds could always be used (although this only happened once during actual flight operations). The NB-52B eliminated this particular deficiency. Unlike the A-model, the NB-52B was quipped with water injection for its engines. Bock and Allavie tested the NB-52B using water injection on just the outer four engines, and on all engines except nos. 5 and 6, with promising results. Bock noted that the use of water injection "appreciably increases take-off performance and is considered mandatory for take-off from the paved runway at a weight of 300,000 pounds when the ambient temperature exceeds 90 degrees Fahrenheit.’,[116]
Takeoffs were initially made using runway 04 at Edwards because that runway had several miles of lakebed overrun available. This allowed the pilots to fly a better pattern during climb-out, but more importantly, it avoided the use of heavy braking in case of an aborted takeoff. Engineers considered the use of maximum braking "undesirable" because of potential damage to the X-15 if one of the NB-52 tires failed. The other direction, runway 22, has a road at the end of it instead of lakebed.-1117!
Pilots found the lateral and directional control systems of the carrier aircraft capable of trimming out the unbalance of the NB-52/X-15 combination. Most of the pilots noted that lateral control became sensitive above Mach 0.8, but believed that launches were possible up to Mach 0.85 with no particular problems. The evaluations did not reveal any buffeting in level flight. It was possible to induce a minor airframe buffet in maneuvering flight at 1.6 g (80% of the pylon load limit), but only at speeds well below the normal operating range. It was discovered that the specific range deterioration of the NB-52 was about 7% with an empty pylon; with the X-15 attached, the specific range decreased by approximately 16%. Given that researchers never planned to launch the X-15 from a distance of more than 500 miles, and the B-52 was an intercontinental bomber, nobody considered this decrease in range significant. Nevertheless, a nonstop flight in May 1962 demonstrated that the pair could fly 1,625 miles from Edwards to Eglin AFB, Florida.118!
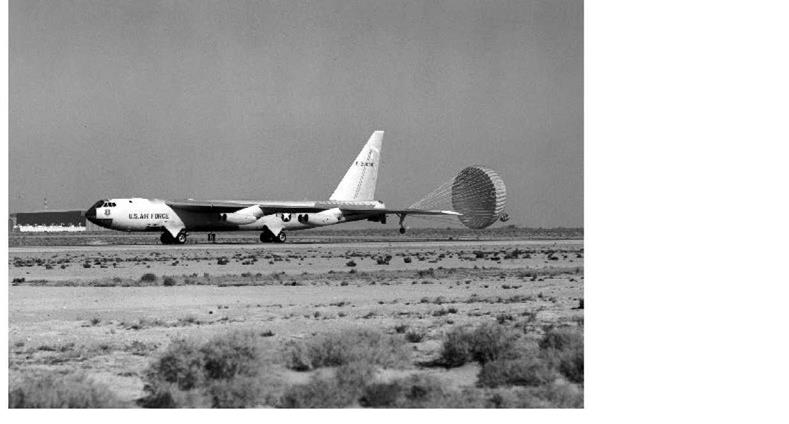
|
The Air Force also provided the second production RB-52B (the fifth B-model) to the X-15 program. The RB-52B (52-008) arrived in Palmdale for similar modifications on 5 January 1959, and as an NB-52B, flew to Edwards on 8 June 1959; the airplane briefly wore the name The Challenger. The NB-52B went on to a long career at the Flight Research Center before being retired in 2005. (U. S. Air Force)
The engineers and pilots predicted that launching the X-15 would result in an instantaneous rearward shift of the NB-52 center of gravity, coupled with a tendency for the carrier aircraft to roll to the left. The X-15 glide flight (i. e., with no fuel) was expected to result in a 4.5% shift in the center of gravity, while full-fuel flights would result in a 9% shift (which rose to about 12% on the later X-15A-2 flights). Engineers calculated that the rolling tendency and pitch-up were well within the capabilities of the NB-52 to counter, and in fact actual operations revealed no particular problems. Under "normal" conditions, the center of gravity actually shifted approximately 7% and required a 40-pound push force on the control column to compensate, but the resulting pulse usually dampened in one cycle.[119]
Some other minor problems were discovered during the NB-52 flight tests. For instance, the aft alternator cooling air duct on the right-wing leading edge and the air ducts on the right side of the NB-52 fuselage ingested hydrogen peroxide residue during pre-launch operation of the X-15 nose ballistic control system. Engineers did not consider the residue hazardous since it was composed primarily of water. Interestingly, while the X-15 was attached to the NB-52, operation of the X-15 ballistic control system had no noticeable effect on the bomber. Operation of the X – 15 aerodynamic flight control also had no appreciable effect on the NB-52; however, a slight airframe buffet was noted when the X-15 speed brakes were extended. A flap extension on the X-15 caused a small nose-down trim change, and extension of the X-15 main landing skids was not even apparent in the bomber. Initially, extension of the X-15 nose gear resulted in a "thump" that was felt and heard in the NB-52, but later changes to the X-15 extension mechanism eliminated the event.-1120
On the other side of the equation, the NB-52 had some effects on the X-15. For instance, the NB – 52 fuselage and wing created noticeable upwash and sidewash on the X-15. Because of the NB – 52 wing sweep, the right wing of the X-15 was nearer to the B-52 wing leading edge and, consequently, flow over the X-15 right wing was deflected downward more than over its left wing. This difference in effective angle of attack of the right and left wings resulted in a right rolling moment. There were also some concerns that the X-15 might strike the carrier aircraft during separation. Because there was only two feet of clearance between the X-15 dorsal stabilizer and the cutout in the NB-52 wing, the X-15 could potentially strike the cutout if the X-15 bank angle exceeded 20 degrees before the airplane dropped below the NB-52 fuselage level (about 2.5 feet vertically). It was decided that all X-15 controls should be in the neutral position when the airplane was dropped, allowing the automatic dampers to take care of correcting the attitude. The first few X-15 launches experimented with the settings needed for the dampers to do this, but Scott Crossfield soon developed a consistent set of settings.-121
Scott Crossfield unexpectedly demonstrated the effects of not using the dampers on the third flight (2-3-6) when the roll damper failed at launch. The X-15 rolling velocity increased rapidly to a peak value of 47 degrees per second and a peak bank angle of 40 degrees. The X-15 dorsal stabilizer dropped below the NB-52 wing cutout within 0.5 second, with the tail barely clearing the cutout. Crossfield finally managed to get the X-15’s wings level about 7 seconds after launch.121
The most obvious modification was a large pylon under the right wing to carry the X-15. This was in contrast to all earlier X-planes, which had been carried partially submerged in the bomb bay of the carrier aircraft, something that was not possible given the B-52 configuration. The pylon worked satisfactorily and allowed the NB-52s to carry other research airplanes, such as the lifting bodies, later in their careers. (NASA)
The damper generally applied a left-aileron input of 6-8 degrees, reducing the peak right-roll velocity to about 25 degrees per second. The pilot could do the same if the damper failed. Aileron inputs of only 2 degrees, however, resulted in peak roll velocities in excess of 50 degrees per second, with corresponding bank angles of over 40 degrees. This risked a tail strike during launch. As the X-15 cleared the NB-52 flow field, it tended to roll left, so the damper and/or pilot had to be prepared to correct this sudden opposite movement. It took approximately 0.8 second for the X-15 to drop 10 feet below the NB-52.-1123
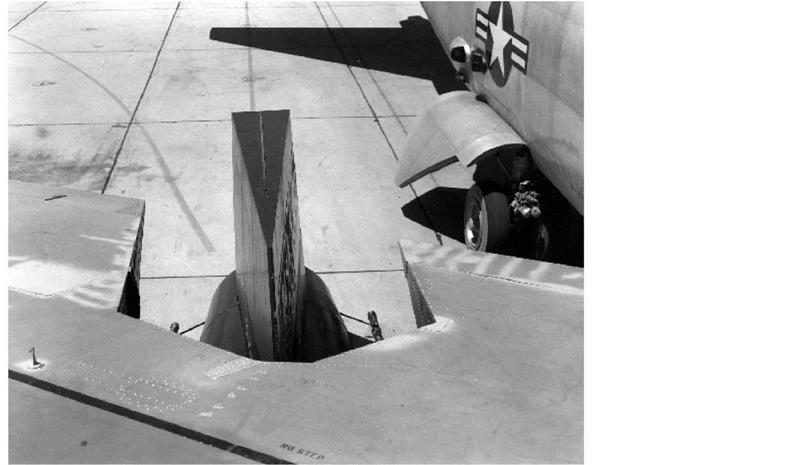
|
Another modification to the two NB-52s was a notch in the right wing to accommodate the X-15 vertical stabilizer. Because there was only 2 feet of clearance between the X-15 dorsal stabilizer and the cutout in the NB-52 wing, the X-15 could potentially strike the cutout if the X-15 bank angle exceeded 20 degrees before the airplane dropped below the NB-52 fuselage level (about
2.5 feet vertically). Fortunately, this was never an issue during the flight program. (U. S. Air Force)
The first few seconds were quite a ride, at least during the first time for each pilot. However, it quickly became routine. Bob White described it as "what might be expected and, after the very first experience, is of no concern to the pilot as normal 1.0-g flight is regained within 2 seconds. The rolloff at launch stops as the X-15 emerges from the B-52 flow field. Since the bank-angle change is small, it is easily and quickly corrected. Launch has been made by using either the center or side aerodynamic control stick with equal satisfaction in both cases."[124]
During initial planning, the engineers set the X-15 launch parameters at Mach 0.78 and 38,000 feet. However, before the first flight, North American decided to raise the launch altitude to 40,000 feet to provide additional performance and increased safety margins. During early launches from 40,000 feet, the X-15 generally needed about 3,000 feet to recover before beginning its climb. After the first few flights, researchers decided to increase the launch parameters yet again, this time to Mach 0.80 and 45,000 feet, just below the previously determined buffet boundary for the NB-52/X-15 combination. Interestingly, when researchers raised the launch altitude to 45,000 feet, the research airplane needed between 4,000 and 9,000 feet to recover, negating much of the value of the higher launch altitude.-1125
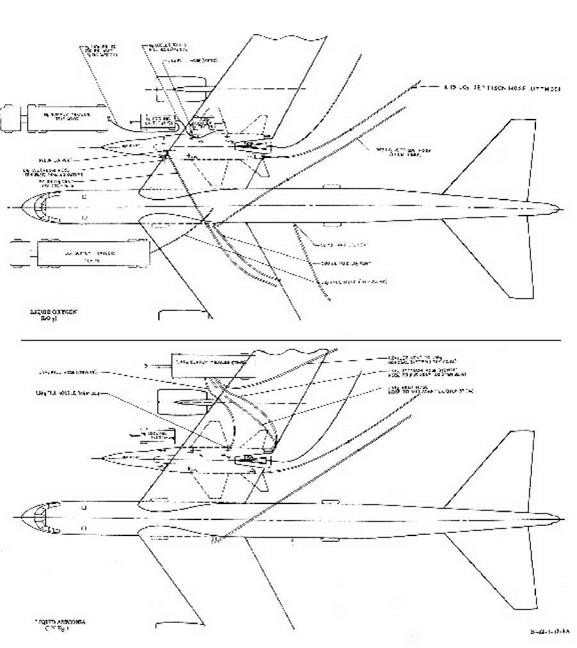
|
Although simplistic by modern standards, preparation of the X-15 for flight was still a complicated procedure involving many people and pieces of ground – support equipment. These drawings show the relative placement of tank trucks and other equipment during the loading of liquid oxygen and anhydrous ammonia prior to flight. (NASA)
In June 1960 the Air Force installed an AN/APN-41 radar transponder in the NB-52A that allowed the High Range to track the carrier aircraft more accurately. This beacon was similar to the one installed in the X-15. The problem had been that the B-52 fuselage was often located between the X-15 beacon and the radar site before launch and acted as an effective shield. Installing a beacon on the B-52 avoided the problem. A series of test flights that made simulated launches from Silver Lake (the NB-52 did not carry the X-15 for the tests) showed that using the beacon to position the B-52 resulted in a more accurate launch location than had previously been attained. This provided an extra margin of safety should the X-15 pilot have to make an emergency landing, and also allowed flight profiles to be repeated more accurately, helping post-flight analysis. The NB-52B received a similar beacon during July 1960. Flight 1-9-17 on 4 August 1960 was the first flight to use the new beacon.-1126
In June 1965 the FRC estimated that the full-up weight of the X-15A-2 with a real ramjet and fuel had grown to 56,000 pounds. This was more than 1,000 pounds greater than the most recent analysis showed the NB-52 wing/pylon could safely tolerate. In January and February 1966 the Air Force modified the NB-52A to increase the allowable pylon weight to 65,000 pounds, allowing for the heaviest expected X-15A-2 flight with some reserve for gusts or other contingencies. The modifications consisted primarily of installing doublers and additional fasteners on various parts of the wing and pylon structure. Although the modifications allowed the NB-52 to carry the X – 15A-2 safely, performance suffered. For instance, the maximum launch altitude was 1,500 feet lower and the maximum launch speed was restricted to about Mach 0.8 when the research airplane carried the external tanks and ramjet. The Air force installed the same modifications on the NB-52B during its next major maintenance period.-1^27