The political, technical and financial fiasco that would become ELDO grew from an act of political cowardice by the British Government. In an attempt to deflect some of the criticism that he knew would come its way after the Blue Streak cancellation, Watkinson had announced that development would continue as a satellite launcher. This was a disastrous move from several points of view.
Firstly, it deflected very little criticism. Very few people were interested in Blue Streak as a satellite launcher, but they were interested in the effect the cancellation might have on the Government’s defence policy. Secondly, the popular enthusiasm for a satellite launcher was small to non-existent. Thirdly, even civilian development was going to cost a great deal of money, and fourthly, there was no demand for a satellite launcher. It looked very much as though it might become a white elephant before it was even built.
One way round the problem was to try and find partners: Thorneycroft had tried the Commonwealth but had received little concrete help. The French, on the other hand, were very interested, as this note from Selwyn Lloyd, then Foreign Secretary, shows:
The French Ambassador raised with me on the 8th of July the question of Anglo-
French co-operation in the development of Blue Streak as a space project. He said
that the reply to the French aide-memoire had been communicated to the French
Government and that he himself had spoken about the matter to the French Minister
of Defence when he had been in Paris.1
Thorneycroft was anxious to find partners for the launcher, and so a draft document was quickly put together as the basis of an offer to the French:
1. All firings to be done at Woomera.
2. Offer to divide satellites for initial programme equally between partners, each paying their share of the cost.
3. The French to make the third stage boost.
4. French technicians to be associated with the completion of BLUE STREAK and
BLACK KNIGHT, and to be given all design information and know-how in a return for a payment of £X for five years.2
Not everyone was happy with a bilateral deal with the French; Edward Heath, then Lord Privy Seal, wrote to the Minister of Aviation thus:
Although I realise that the French are more likely than anyone else in Europe to make a useful technical and financial contribution to the development of a European launcher, I do not feel it is politically possible now, having made an approach to so many European countries to turn round and tell the Europeans that we propose to enter into an exclusive bilateral scheme with the French…
The French may of course try to steer us towards a bilateral scheme: if so, we should have to think again, and very hard: for I see substantial political objections to some exclusive Anglo-French scheme.. .3
Despite Heath’s objection, a party of French engineers visited London on 29 September, moving on to Farnborough on 30, September followed by a much longer four day visit in November, when the itinerary included Hatfield, Ansty, RPE, Spadeadam, Cowes and London.
Thorneycroft summarised the results of the visits in a note to the Prime Minister:
The French have replied on Blue Streak. Essentially they have said 4 things –
(a) That they will join us in an approach to other countries in Europe.
(b) That they remain uncommitted at this stage.
(c) That they want to make a good slice of the composite rocket themselves.
(d) That it will all take a long time to arrange.
(a) is excellent, (b) and (c) are understandable and (d) must be avoided at all costs.4
Then it was the turn of the British to go to Paris in January 1961. The record of the meeting begins with the sentence: ‘M. Pierratt opened the discussion by stating that the French had received instructions from top level on Wednesday last to work at a joint solution with the British for a European space launcher’ (‘top level’ being interpreted by the British in this context as meaning General de Gaulle himself).
The meeting then went on to discuss the details of the design. The French, at this stage, were leaning towards the idea of a solid fuel second stage deriving from their military programme. The British technical representative, Dr Lyons from RAE, was
… disappointed… not so much that the payload was less, but because it was less flexible in terms of a change in diameter. A 1.5 meter second stage would not produce a good three stage build-up if in later years a Hydrogen third stage was considered. The solid fuel motor would have been a cheaper option, since it was already being developed for the military. The liquid fuelled proposal would use
UDMH and N2O4, although the French admitted when asked what experience they had with these propellants: ‘… very little indeed. They had fired some engines of a research size for very short durations only’.
The most surprising point about the technical exchanges is how seemingly ill- prepared the French were. The first contacts had taken place more than six months ago, the first technical visits more than three months before, yet obviously no detailed consideration had been given to the design at all. If even such a basic point as whether to go for a solid or liquid fuelled design had not been considered in any depth, then there was a great deal of work still to be done. There was an interesting coda to the meeting. To quote:
French said they would try to work out these costs this evening and on Saturday morning. They would have to go carefully into the savings to be made on the military investment and the question of British help in this field was of major importance.
Twinn said we fully recognised this, and in order to be as helpful as possible we would like the French to define in more detail than previously just how we could help with the military programme.5
The items were listed in a separate table:
MILITARY INFORMATION EXCHANGE ITEMS
Refrigeration and cooling
Re-Entry Head Stabilisation, orientation
Rate of spin, methods of spin control
Heat flux
Materials
Equipments concerned with operating the bomb
These are exactly the questions one might expect, although if the French were intending to produce a solid fuelled missile, some of the items such as sloshing would become redundant. It is unlikely that Britain could have given much help on large solid motors. Some of the other items were ones which had given particular difficulty to the British only two or three years before – inertial guidance and re-entry in particular.
Sir Steuart Mitchell’s comment on the re-entry head read as follows:
The design of re-entry head which we finally ended up with for Blue Streak is:-
(a) Of British origin.
(b) It is now joint UK/US information.
(c) It is agreed by the US to be much better than their designs as regards invulnerability and US has now copied it.
(d) As regards invulnerability it is so advanced that neither the US nor ourselves can conceive a counter to it.6
Writing to Solly Zuckermann in a memo entitled ‘Possible Transfer to French Government of Military Technical Information on Blue Streak’, he also notes that:
Re-entry head.
Radar Echo. Information on this is mostly Top Secret and would be of great value to the French. The most advanced work in this field is British and is acknowledged by the US to be ahead of their work. It is thought that future US warheads may be based on this British work.
Release of this information would be contrary to I and II of para 3 in that it could provide an enemy with a ballistic weapon against which we see no defence and it would prejudice American weapons. It is desired to draw particular attention to this point and it is recommended that this information should not be released.
To provide a line of defence on which any technical conversations might be conducted it is suggested that we take the line that –
Details of shape, weight, dimensions, etc. of the Blue Streak re-entry head cannot be discussed as they contain “atomic” information.
Decoys. Information on these would contravene I and II of para 3 above. This is a sensitive Top Secret field in which we are well ahead of the USA who accordingly would be apprehensive if we released information to the French.7
He also made the point that ‘… the re-entry head design is highly specific to the weapon parameters.’
It is clear, however, that the French regarded the military information as something of a quid pro quo:
… they wished to make a political point of associating the exchange of military information with the cost for the space launcher, and they wished to make the interdependence clear at Ministerial level by presenting both cost and military exchange papers to Mr Thorneycroft at Strasbourg.8
The British delegation was less than happy with this idea: ‘The representation at Strasbourg was not the channel at which we would prefer to deal with this.’ Mitchell wrote a minute (‘French Proposals for 2nd and 3rd Stage’) for the Minister, summing up the position to date. An interesting comment was that
‘since August [1960] no approach to UK firms to start design of the second and third stages has been permitted, partly to avoid compromising our negotiating position in Europe’. Using a French second stage would increase development time, and CGWL felt that this ‘now gives enough time to develop a liquid hydrogen 3rd stage’.
He also had these comments to make on the French proposals:
… if the French chose a liquid motor for the 2nd stage, and if they followed their present lines of development, the performance of their 2nd stage would again be appreciably lower than that of Black Knight.
This is due to the fact that the French have not developed high performance turbo pump fuel systems on UK or USA lines and, for their weapon development, are not prepared to face up to their technical complexities. They intend to use the cruder method of gas pressurisation of the fuel tanks as a means of pumping the fuel. The resultant penalty in tankage weight is considerable.
As a result of the above, the conclusions as to French 2nd stage performance are as follows:
The French agree that there would be a loss of performance, but argue that it would not be great… We, with much more experience, consider that the penalty would be considerable.9
There was a way round this performance loss: replacing the planned HTP/kerosene third stage with one using liquid hydrogen. His suggestion was:
Participation by other European countries in the Space Club is essential. Hence I suggest that development of the liquid hydrogen 3rd Stage should be offered to a consortium of European countries with some UK technical participation in the development teams.
His final conclusion was that
We are in favour of proceeding with a French 2nd stage and a European 3rd stage, recognising that by so doing the completion date for the European launcher will be delayed by perhaps Ш years and that the total costs may rise by perhaps 10-15%.
There followed some very rapid writing of proposals which would be put to other European countries. The end result was a long brochure, describing the vehicle and its missions in considerable detail10. The introduction provides a useful summary of the history of the project to that date:
After the British Prime Minister’s Statement in May 1959 that an investigation would be made of the adaptation of British rockets for satellite launching, extensive studies of the capabilities of Blue Streak, in combination with other rocket stages, have been made by the United Kingdom Ministry of Aviation at the Royal Aircraft Establishment, Farnborough.
The later proposal that a satellite launching vehicle system based on a Blue Streak as a first stage should be developed as a joint European and Commonwealth effort, has recently caused these studies to be extended by joint Anglo-French investigations into a design incorporating a French second stage.
The original British proposals were put to representatives of European nations at Church House, Westminster, London on the 9th and 10th January, 1961. At Strasbourg, during the week of 30th January to 3rd February, a preliminary description of a joint Anglo-French proposal was presented for the consideration of representatives of a number of European nations.
One of the guiding principles of the United Kingdom studies was the minimisation of cost, particularly capital cost, and thus the greatest possible use should be made of existing equipment and facilities, including the rocket ground testing and development facilities at Hatfield and Spadeadam, in England, and also the launching and other range facilities at the Weapons Research Establishment, Woomera, Australia.
France, on her side, has undertaken an extensive national programme of basic studies and development of ballistic missiles. The French proposal for a second stage, later to be described, is closely related to this programme in order, again, to minimise cost, delay and technical uncertainty.
This brochure contains outlines of the jointly proposed satellite launching vehicle and its systems as they stand at February, 1961. The opportunity has been taken since the Strasbourg meeting to bring the proposals into accord with the latest technical information. The assessment work which will lead to a full design study is by no means complete, depending as it does considerably on the parts of the work to be undertaken by the European nations involved. All aspects of the combination of the French second stage with Blue Streak have not yet been completely examined. The brochure, therefore, contains the joint Anglo-French proposals as far as they have gone, and where the necessary work has not been completed, the parallel work done on the original British configuration has been referred to. In the absence so far of an alternative proposal for the third stage, the third stage described is the original UK proposal.
The brochure went on to describe the capabilities of the launcher:
(i) A large satellite weighing between one and two thousand pounds in a near circular, near earth, orbit. This satellite would be space-stabilised with a primary purpose of making astronomical observations above the earth’s atmosphere.
(ii) A smaller satellite of several hundred pounds weight, moving in an eccentric orbit out to two or three earth radii, for the investigation of the earth’s gravitational, magnetic, and radiation fields, and the constitution of the earth’s outer atmosphere.
(iii) A satellite of the order of one hundred pounds weight, in a highly eccentric orbit reaching out to about 100,000 miles, to carry instruments for the study of the sun’s atmosphere.
These aims have been subsequently extended to cover the possible launching needs for Satellite Communication Systems and this has led to the consideration, in addition, of circular orbits at several thousand miles altitude.
-BREAK UP CHARGES. CHARGES DE DESTRUCTION
KEROSENE TANK. RESERVOIR DE KEROSENE
-RATE GYROS. GYROMETRES
Figure 62. The Anglo-French proposal. This is effectively the Black Prince design with a French second stage.
The first three objectives are taken from the Saunders Roe brochure for Black Prince, published a year previously. It does highlight an absurdity of the programme: £60 million for three satellites does seem excessive. The communications requirement is new, and the Saunders Roe liquid hydrogen stage was optimised for just such a role. The main problem was that even 5,000-6,000 miles was still too low an orbit for communication satellites. RAE and others tried looking at 8-hour or 12-hour orbits, but it is only the geostationary orbit which is of any practical use.
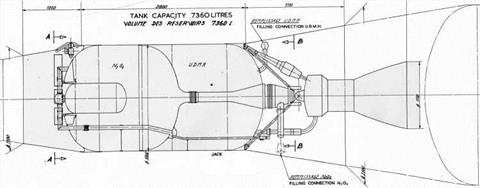
Figure 63. The French proposal for the second stage (the final version would be very similar, except that the one large chamber would be replaced by four smaller ones).
|
The brochure then went on to describe the vehicle in more detail:
The original British proposal for the second stage was to use a modified form of the ballistic research vehicle Black Knight. This has now been replaced by a proposed French second stage making use of techniques currently under development in that country. This stage will be propelled by a liquid propellant engine using Nitrogen Tetroxide and UDMH with, a sea level thrust of 25 tons (32 tons vacuum) and vacuum Specific Impulse of 276 seconds. The vehicle tanks contain approximately 7 tons of propellants and are pressurised by means of a solid propellant gas generator. The single thrust chamber is gimbal mounted for control in pitch and yaw. Roll control is achieved by means of auxiliary jets mounted at the top of the vehicle…
Studies indicate that it is possible to inject a satellite into orbit using the proposed two stage combination but this would necessitate a long coasting period after perhaps 90% of the second stage propellants had been burnt, followed by a relight of the second stage engine to inject both satellite and empty second stage into orbit. This approach introduces problems of relighting the engines under zero acceleration as well as the necessity for ensuring correct orientation of the second stage at engine relight.
Though such problems have been solved in other satellite launchings, the two stage vehicle would give considerably reduced payloads and would be unable to put any payload into higher orbits. The preferred approach is therefore to introduce a small third stage rocket. This is sometimes referred to as a vernier stage. The engine of this stage, working at a relatively low thrust level of between 1000 lb and 2000 lb would be started during separation from the second stage and would continue to burn through what would otherwise be the coasting period, cutting off when orbital altitude and velocity had been achieved. The low weight of the third stage structure and engines, compared with that of the relit second stage, affords considerable improvement in payload weight into low orbits and makes possible the injection of payloads into very high orbits.
The British proposal for a third stage engine is a four chamber design, each chamber pivoted about one axis for steering. It would use hydrogen peroxide and kerosene. With low thrust and four chambers, very high nozzle expansion ratios, of 1000 : 1, are possible without undue chamber size and length…
It is possible to meet the several orbital requirements by exchanging satellite payload weight for propellent weight in the third stage whilst maintaining constant the overall weight of the third stage plus satellite payload at some 5000 lb; that is, the third stage incremental velocity can be increased at the expense of payload. The tank volume is altered to suit the orbital mission allowing the remainder of the third stage, including the engine, and all equipment, to remain sensibly unchanged.
For the configuration just described, with a take-off thrust of 300,000 lb weight a satellite of 2,160 lb may be put into a 300 mile circular polar orbit.
Corresponding payloads for elliptical polar orbits, both with perigee heights of 300 miles, and apogee height of 7000 and 100,000 miles, are respectively 910 lb and 320 lb.
For a typical high altitude equatorial orbit (launched near the equator) at, say, 5000 miles altitude; a payload weight of 700 lb is calculated.
These are ‘nominal’ payloads making some allowances for weight growth of the launching vehicle. It would be prudent, however, to assume that actual payloads would be perhaps 200 lb less than these nominal values to allow for unforeseen contingencies.
The negotiations were not easy. Enthusiasm for the project in Europe was very limited. Indeed, in May 1961, Thorneycroft asked Mitchell what needed to be done to go ahead with an all-British launcher, and received a reply saying that it would be quite straightforward with the original HTP design, with or without the liquid hydrogen stage. Even Australia seemed to be making difficulties, and Thorneycroft took the unusual step of writing to Mitchell to ask whether it was feasible to launch Blue Streak from Spadeadam!
The conclusion to his hastily written paper (the full version can be found in Appendix A):
Spadeadam is technically both feasible and attractive. From the cost point of view, it is approximately the same as Woomera, and is much cheaper than any alternative.
It must be accepted, however, that some cut-downs on to UK territory would inevitably occur if we fire from Spadeadam. The chance of serious damage to life and property from such cut-downs are numerically small.
The risk of damage to foreign countries, or to shipping, is negligible.
The crucial point is the political acceptability of the risk in the UK Hitherto this has been regarded as unacceptable, and it would be no less now than when previously considered. My advice is that the risk is appreciable and should not be accepted.11
As Mitchell says, the crucial point is political acceptability. The thought of launching a rocket as large as Europa from an inland site in Britain is one which should fill any politician with horror. The repercussions from an accident would be horrendous.
There is also another technical point. Mitchell describes the launch direction as ‘North 15 East’, or 015° in modern parlance. To be restricted in launch direction in this fashion very much reduces the value of the site (and this also applied to Woomera). Different satellites fulfilling different roles need different orbits. It certainly would be useless for communication satellites.
Fortunately, agreement was reached with the Australians, and Woomera would indeed become the launch site for the first ten launches.
Although several European countries sent delegates, most of Thorneycroft’s efforts were devoted to persuading the German and Italian Governments to join the project. Both countries were reluctant; the Italians wanting to reserve their money for their own national programme. Belgium and the Netherlands were willing to participate, but their contributions would be small. Denmark had taken part in the discussions but decided in the end not to join, but again any Danish contribution would not have been very significant.
After further protracted negotiations, Germany agreed to join, and would build the third stage; the Italians would provide the satellite fairings and the Satellite Test Vehicle (STV). Thus the final membership of ELDO consisted of the UK, France, Germany, Italy, Belgium and the Netherlands, with Australia making the seventh member.
The cost of the programme was split thus
|
Britain:
|
38.8%
|
France:
|
23.9%
|
West Germany:
|
22.0%
|
Italy:
|
9.8%
|
Belgium:
|
2.9%
|
Netherlands:
|
2.6%
|
Australia would make no direct contribution, but would instead develop the Woomera launch site.
ELDO came into formal being in March 1962 by a Convention which was signed by the seven Governments and which came into force on 29 February 1964 after ratification by the signatory states. The headquarters were in Paris, and it was governed by a Council that had two representatives for each member state. The Council was assisted by an International Secretariat under the direction of a Secretary General, with two Deputy Secretaries General, one in charge of technical affairs and the other of administrative affairs. The staff of the Secretariat amounted to around 180 people in 1965.
But while design work for the new launcher had started, ELDO itself was already running into serious political trouble. Indeed, it would spend most of its existence staggering from crisis to crisis, either technical, financial or political.
By 1964, the design of the vehicle had finally been decided12, and work was beginning on the design and construction of the upper stages. The French then dropped something of a bombshell by stating ELDO A was inadequate, that it should be dropped, and that the organisation’s efforts should be directed towards a new launcher, ELDO B.
There were immediate objections from the other member states, mainly on the grounds that an entirely new upper stage would be technically demanding and take several more years to develop, whilst in the meantime, nothing else would be happening. Blue Streak had already been successfully tested, and work was proceeding on F4, which was Blue Streak with dummy upper stages. Under the French proposal, there would be no further launches for some years until the new upper stages had been designed and developed. To be fair to the French, if ever there was a time to go for a design that was far more capable, this was it, but given that it had already taken four years to get to the point of beginning work on ELDO A,
the reluctance of the other countries was understandable.
But the French took their objection to ELDO A one step further: they refused to provide any further funding. This did produce quite a serious crisis: without an agreed budget, all work would grind to a halt by the middle of 1965. Negotiations with the French proved difficult: the British representative referred to what he called ‘decisions handed down from Mount Olympus’ – in other words, a decision taken on high, and presumably a reference to General de Gaulle, which the French ELDO representatives could do little about. One junior minister, Austen Albu, described the situation thus: ‘Whatever the merits of the case we are in fact being blackmailed by the French.’13
The British Government had by now become actively hostile to ELDO, and there were hopes that French intransigence might bring about the collapse of the organisation.
From the economic point of view, the safest course would still appear to be to decline any further financial obligations beyond our share of the original £70 million on ELDO A, to which we are already committed. It has certainly not been demonstrated that a firm stand on these lines will involve serious dangers to those policies on which it is really important that we should have our neighbours’ support [referring to other members of ELDO]. Such action might indeed gain us enhanced respect in the more responsible sections of our neighbours’ administrations…
If however the feeling of Minister’s colleagues is against such risk of friction to neighbourly relations as a firm stand might involve, the next best course would be to take the line that on present evidence Britain
is not prepared to depart from ELDO A as originally conceived,
is unwilling to proceed to completion of the ELDO A programme until more
adequately costed,
as regards ELDO B no commitment could be considered until much more information was available.
There are many who consider that if Britain takes a position along these lines ELDO will die a natural death, without Britain having to plunge the dagger. First Secretary, however, will appreciate that such a happy outcome cannot be guaranteed and that the more moderate course must carry the risk of a lingering British involvement in these unrewarding activities.14
There were attempts at a compromise. One was to proceed with what was called ELDO A(1+3), to keep the programme going whilst work began on ELDO B. This was a proposal to put the German third stage on top of Blue Streak – hence the (1+3) designation. This, it was thought, could put 300 kg into a 500 km orbit. Use of an apogee motor would enable payloads to be put into highly elliptical orbits, which might suit some of the proposed European Space Research Organisation (ESRO) requirements. Given that the German stage was the least well developed part of Europa, this too was somewhat optimistic.
An ELDO document15 described the proposal thus:
The 1+3 programme would provide for development of basic techniques, establishment of facilities, and experience by personnel as a foundation for the ELDO B programme including proof of the first stage and engines; development of throttled engines, live-stage separation; instrumentation, safety, nose-fairing and STV separation, and inertial guidance. This is work which can only be carried out in a vehicle based on Blue Streak.
The studies so far undertaken, necessarily limited by time, give the Secretariat good grounds of assurance that the programme is technically feasible.
The payload performance of the 1+3 vehicle is strongly dependent on the 3rd stage performance and empty mass. Its round to round variation will be somewhat smaller than that of the original three-stage vehicle. For a 300 km orbit, the upper limit of payload performance is about 500 kg…
This payload performance would have application to:
a) missions requiring light satellites, e. g. for navigation, meteorology or geodesy,
b) ESRO requirements for the launch of small satellites, i. e. those within the launching capacity of Thor Delta.
It was a proposal that died together with ELDO B. A 500 kg payload is quite respectable, but whether it would be worth using a launcher as expensive as the (1+3) scheme is debatable. A sketch of the proposed vehicle is shown on the left.
The (1+3) programme was intended to run in parallel with the ELDO B development, but ELDO B was abandoned as a result of the Intergovernmental Conference in July 1966. Instead, a new five year programme was drawn up, starting in January 1967 at an estimated cost of 331 MMU. (1 MMU was effectively the same as 1 US dollar, so at the then rate of exchange this was a little less than £120 million.) 10 MMU were set aside for ‘studies and experimental’ work – ELDO B was not entirely dead yet.
On the other hand, the rejection of ELDO B left the organisation with a vehicle that had very little purpose. In order to salvage something from the wreck, the Perigee Apogee System (PAS) was put forward. This consisted of two solid fuel motors and a communications satellite. The system would be put into orbit by Europa, then the first solid fuel motor
would be fired to put the satellite into a highly elliptical geosynchronous transfer orbit. The apogee motor would convert the elliptical orbit into a circular orbit.
A geosynchronous orbit required a launch site close to the equator – and Woomera was too far south. The launch corridors from Woomera were very restricted by the centres of population below the flight path. ELDO set about finding an alternative site, and the two main contenders were Kourou or Darwin, and, as we shall see, Kourou was chosen.
So a new launch site for Blue Streak was built in the depths of the South American jungle. The last launch of Europa from Woomera was F9, after which Australia left the organisation. A non-flight model Blue Streak, known as DG, was taken out to Kourou to test the facilities. F11 (there was no F10) would be the first launch from South America, the first with the PAS operational, carrying a communications satellite for France, and the last ever launch of Blue Streak and Europa.