During the mid-1960s, a proposed delta-wing modification to X-15-3 might have kept the program flying until 1972 or 1973. Unlike many proposals, such as the "orbital X-15," the delta wing was a real project and was the subject of a great deal of research and engineering.
The delta-wing X-15 grew out of hypersonic cruise research vehicle studies conducted during the early 1960s. A "hypersonic cruise" vehicle would spend minutes or tens of minutes at hypersonic velocities, in contrast to the original X-15 that spent only a few tens of seconds at that velocity. The delta-wing X-15 configuration used the third airplane with the MH-96 and the basic modifications made to X-15A-2. Proponents of the concept, particularly John Becker at Langley, found the idea very attractive. Becker opined that "the highly swept delta wing has emerged from studies of the past decade as the form most likely to be utilized on future hypersonic flight vehicles in which high lift/drag ratio is a prime requirement i. e., hypersonic transports and military hypersonic cruise vehicles, and certain recoverable boost vehicles as well."[287]
Researchers held a meeting at the FRC on 9-10 December 1964 to determine exactly what research could be undertaken with a delta-wing hypersonic-cruise X-15. Attendees included researchers from Ames and Langley, and of course groups from the AFFTC and FRC. Not surprisingly, Ames and Langley did not necessarily agree on the exact nature of the research, and NASA Headquarters asked each center to submit a position paper outlining its preferences.
The Langley paper included an evaluation of possible aerodynamic and heat-transfer experiments, in-flight engine-inlet tests, and various structural recommendations that might be applicable to the delta-wing X-15. The entire paper was remarkably short-only 11 pages, or about the same size as the original 1954 paper that had been the genesis of the X-15 program.*288
John Becker and David E. Fetterman, Jr. led the Langley group that defined the aerodynamic and heat-transfer experiments primarily concerned with evaluating the differences between data gathered during full-scale flight tests and the results of wind-tunnel and analytical data. They noted that "[s]ince air-breathing hypersonic cruise vehicles will fly at such large Reynolds numbers that turbulent conditions will occur over the entire wing, it is obviously of great importance to establish the turbulent heat-transfer characteristics of delta wings. The lack of any rigorous theory to turbulent heat transfer places great emphasis on experimental determinations.
It has proved impossible, however, to achieve natural turbulent boundary layers on delta wing models in hypersonic ground facilities except over the rearward regions." Becker and Fetterman used similar logic to justify investigations into areas such as turbulent skin friction and Reynolds analogy, turbulent boundary-layer profile surveys, interference heating, and pressure distributions.-128^
The discussion of engine-inlet testing led to a rather surprising conclusion: "an inlet flight test program on the X-15 is not recommended." J. R. Henry believed that ground facilities such as the 20-inch hypersonic tunnel at Langley and the 3.5-foot hypersonic tunnel at Ames were more than adequate for research into inlet configurations up to Mach 8. Henry’s case was convincing, and despite the ongoing interest in the HRE experiment, Langley dropped engine-inlet testing from further consideration for the delta wing.[290]
Structural considerations were not so much possible experiments, but rather recommendations prepared by J. C. Robinson representing the views of the Structures Research Division at Langley. The primary recommendation was to manufacture the main wing structure from one of the nickel – or cobalt-base "superalloys" using simple construction methods such as "corrugated webs welded to machined cap members with a machined waffle plate skin between the cap members and welded or riveted to them." It was also recommended that the leading-edge material "should be refurbishable, fabricated of thoria-dispersed nickel or a refractory metal, radiation cooled, and should have expansion joints to accommodate differences in thermal expansion between it and the main structure."[291]
The Ames position paper submitted by J. Lloyd Jones was more extensive, consisting of 18 pages using much smaller typeface. The paper also levied some criticism of the existing X-15 program.[292]
Ames agreed with Langley that the primary area of research should be turbulent boundary layers "because of the difficulty of providing turbulent boundary layer flow on models in wind tunnel tests at hypersonic speeds." Ames noted that the existing X-15 had already validated wind-tunnel results up to Mach 5, and the Mach 8 data would be a natural extension. Ames also pointed out that the delta-wing X-15 "is more representative of hypersonic cruise aircraft configurations" and would therefore yield more useful data. Ames also believed that "knowledge that will accrue of the handling qualities of a delta winged vehicle representative of current concepts of airbreathing cruise configuration will certainly be of value."[293]
The researchers at Ames seemed to want to take the lead on the delta-wing configuration, much as Langley had done on the original X-15, and their list of potential research areas was a good deal longer. Besides turbulent-boundary-layer research, Ames wanted to look at skin-friction surveys, pressure distributions and local flow fields, boundary-layer-transition definitions, ablative studies, panel-flutter studies, and low-speed and hypersonic-handling qualities. To accompany these experiments, Ames believed that "an increased program of ground based research relating to hypersonic cruise aircraft technology should be initiated."[294]
Although Ames acknowledged that "the X-15 program to date unquestionably has been very successful" and had turned into "a research facility with which to conduct studies never envisioned at its inception," it believed the program was open to some criticism. "For example, measurement of heat transfer was one of the major research experiments conducted on the airplane, but design inflexibility resulted in the acquisition of heat transfer data in an environment which compromised their value to the extent that they cannot be fully explained nor understood."[295]
To overcome this fault on the new airplane, Ames indicated, "the key to the potential benefits…
for a delta wing X-15 program lies in the design of the airplane to accomplish well defined experimental tasks as primary objectives." To this end, Ames made several recommendations for the vehicle configuration:12961
1. Provision for removable test panels in the areas selected for measurements… to provide for heat transfer, boundary layer and structural tests on both experimental and prototype panels. Design of the test panels and supporting structure should be guided by the requirement to avoid localized heat sinks that withdraw heat away from the boundary layer in a non-uniform manner.
2. Provide a smooth primary test area along the bottom centerline of the airplane free of all protuberances. This consideration may well lead to the requirement for a low-wing configuration to insure a test region with a definable uniform flow field.
3. A removable fuselage nose section ahead of the wheel well with an instrument compartment and a removable tip. This feature would provide for replacement nose sections having different geometry.
4. An instrumentation bullet located at the wing-fin juncture may be advantageous.
Ames went on to describe an elaborate research program that began with wind-tunnel studies, followed by flights using X-15A-2, and finally tests with the delta-wing aircraft. The program would concentrate most of the theoretical and wind-tunnel work at Ames. Based on the scope of the work described, it probably would have been expensive, although the report did not include a cost estimate.
After reviewing the papers submitted by Ames and Langley, with additional input from the Air Force and FRC, NASA defined two primary objectives for the delta-wing X-15 program:12921
1. Aerodynamic research-The flight tests would provide realistic aerodynamic data under fully developed turbulent flow conditions to supplement ground-based research where such conditions cannot be achieved. Answers would be obtained to key questions relating to hypersonic aerodynamics of delta wings, large-scale behaviors of flap-type controls, tip-fin interference effects, and handling qualities of a configuration typical of present thinking for a future hypersonic air-breathing vehicle. Aerodynamic research on this vehicle would be unclouded by propulsion effects, inasmuch as most of the data would be taken under gliding conditions.
2. Structural research-The delta-wing proposal would permit the evaluation in a practical flight application of a hot radiation-cooled structure designed for repeated flights at temperatures between 1,500 degrees and 2,200 degrees Fahrenheit. It would also focus technical effort on a refurbishable, hot-wing leading edge design.
Paul Bikle concluded that "[i]n general, a delta-wing X-15 program could establish a baseline of confidence and technology from which decisions regarding the feasibility and design of advanced air-breathing vehicles could be realistically made. The proposed time for the delta X-15 fits well with that for an overall hypersonic research vehicle program and the cost does not appear to be unreasonable."12981
Things seemed to be progressing rapidly. In January 1965 the FRC drafted a statement of work for North American to conduct a detailed study of the delta-wing concept. This document indicated that "NASA is considering a hypersonic cruise vehicle research program which involves a modification of the basic X-15 configuration for study of various aerodynamic, structural, and flight control problems. The program will also include limited investigations of flight to altitudes extending to about 180,000 feet." Extreme high-altitude research was not a requirement.12991
NASA suggested that an existing "X-15 airplane would be modified to incorporate a representative slender hypersonic wing substituted for the present wing and horizontal tail. The wing structure would be designed for sustained hypersonic flight at a Mach number of 7, but would also be capable of flight to Mach number 8 for limited time periods. The basic X-15 fuselage structure, rocket engine, flight control and other systems would be retained with minimum modification, and the present B-52 launch system and high range facility would be utilized."13001
The work statement went on to indicate that the airplane should have a load limit of 5 g and a
2,0- psf design dynamic pressure. Potential "improvements" included relocating the wing to be flush with the bottom of the fuselage, increasing the dynamic pressure to 2,500 psi and the load factor to 7.33 g, including external propellant tank(s), and relocating the nose landing gear. Other possibilities included the addition of a permanent thermal-protection system (in lieu of ablative coatings) over the fuselage to prevent contamination of the wing with ablative products.-13011
The delta wing seemed to languish at the FRC for the remainder of the year while engineers put together a project development plan. By the end of the year, the FRC had released the second draft of the plan for internal review, providing more detail on how things might progress. The opening paragraph provided the justification for the program:13021
Three of the most probable uses for hypersonic airbreathing aircraft are transport over long ranges, military reconnaissance, and as maneuverable reusable first-stage boosters. There are currently no military or civilian requirements of over-riding importance for any one of these. Their potential, however, constitutes a clear justification to proceed with comprehensive programs to develop the required hypersonic technology.
Unfortunately, the justification also included a rationale for not supporting the program, given the budget crunch NASA was experiencing as it continued the Apollo program to the detriment of the aeronautics budget. Nevertheless, the FRC pressed on with detailed plans. The FRC considered the delta-wing project an extension of the X-15 program, and assumed that all existing agreements between the Air Force and NASA would continue. Researchers believed that the manpower requirements for the program could be satisfied "with the present complements of the Langley, Ames, and Flight Research Center."13031
Researchers at the FRC estimated the program would cost $29,750,000 spread between FY67 and FY73. Of this, the airframe contractor would receive $24,600,000 to build the flight vehicle, while the other $5,150,000 would be "in-house" expenses. The second year represented the largest annual expenditure: $14,500,000 to the contractor and a little over $1,000,000 in-house. The planners warned, however, that "if the military withdraws their operational support from the general X-15 program, this project would be responsible for additional expenses over the 4-1/2 year operational period. These expenses could amount to as much as 17 million dollars." The preliminary schedule showed a request for proposals in August 1966, a contract award in March 1967, modifications to X-15-3 between December 1967 and October 1968, and a first flight in January 1969. The 37-flight research program continued until December 19 72.13041
In the project plan, the FRC had expected the X-15 Project Office at Wright-Patterson AFB to handle the procurement of the modifications, although NASA would pay the bills. Although it would seem logical for North American to perform the modifications, several other contractors (Lockheed, Northrop, and Republic) had expressed interest in the program, so the FRC proposed to make it a competitive process.13051
The Air Force was not totally in favor of this since they saw their involvement with the X-15 winding down, and had little apparent interest in the delta-wing program. Despite negotiations between the Air Force and NASA at various levels, the X-15 Project Office declined to participate in the expected procurement of the delta-wing airplane; however, it did agree to transfer the X – 15-3 airframe to NASA for the modification at the end of its flight program.
After nearly two years of delay, on 13 May 1967 the delta-wing program had progressed far enough for the FRC to issue a request for proposals (PR-7-174) for a formal conceptual design study. The primary objectives of the study were to 1) develop a preliminary design for evaluating the modification of X-15-3 to a delta-wing configuration, and 2) formulate an accurate estimate of performance, weight, cost, and schedule for such modification. A secondary objective was to analyze alternate approaches, such as unsegmented leading edges; eliminate the use of ablatives; and incorporate a fly-by-wire control system, multiplane airfoils, symmetrical tip fins, and different propulsion systems.-1306
There appears have been only a single respondent to the request for proposals. North American submitted a two-volume, 500-page proposal containing detailed engineering concepts and cost data-and that was just the proposal to do the study! By this time, North American had already been testing the delta-wing X-15 in wind tunnels for over a year. The North American low-speed and hypersonic tunnels and the Langley 20-inch hypersonic tunnel had tested 1/15-scale and 1/50-scale models at Mach numbers between 0.2 and 6.9 and Reynolds numbers up to 10,000,000 (equivalent, based on model length).-307
The proposed North American delta-wing X-15-3 was not a simple conversion. The 603-square – foot delta-wing planform had a 76-degree leading-edge sweep, but the span was the same as that of the original X-15 to ensure that there would be no clearance issues with the NB-52 carrier aircraft. Elevons (30.8 square feet each) at the trailing edge provided longitudinal and roll control by deflecting up to 4.5 degrees up or 5.0 degrees down. The existing dorsal and ventral stabilizers provided directional stability with the addition of wing-tip fins, and the existing dorsal rudder provided directional control. Engineers could adjust the removable tip fins on the ground for cant and tow-in, which allowed them to change the relative levels of directional and lateral stability to investigate the handling qualities of the vehicle. The tip fins compensated for the blanking of the normal centerline vertical stabilizers by the fuselage at hypersonic speeds and large angles of attack.308
The position of the wing was the subject of a great deal of study since the HRE was expected to be carried on the ventral stabilizer (as the dummy was on X-15A-2), and the aircraft also had to be stable in flight without the 1,000-pound engine. It proved to be a difficult problem. The final answer before NASA terminated the program was to position the wing in the best location to compensate for the HRE. On flights without the engine, as much research equipment or ballast as possible would be located in a new aft experiment compartment. Likewise, the shape of the wing leading edge was of some concern, but North American noted that "the effect of leading edge radius on the low-speed aerodynamic characteristics of highly swept delta wings is not well understood." Engineers did not think the effect on the leading-edge shape at supersonic speeds would be significant, because positive pressure on the wing lower surface would produce most of the lift. Nevertheless, since the leading-edge shape significantly influenced the landing characteristics, North American investigated various configurations in its low-speed wind tunnel. The company had not found a satisfactory answer, and was awaiting further data from NASA wind-tunnel tests, when the program ended.309
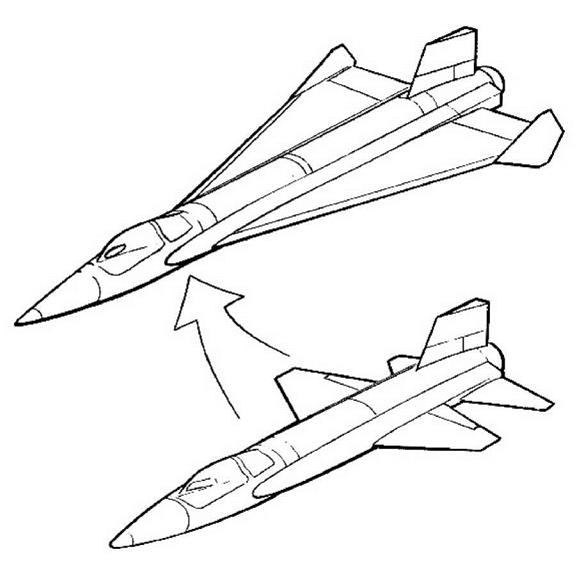
|
During the mid-1960s, a proposed delta-wing modification to X-15-3 might have kept the program flying until 1972 or 1973. Unlike many proposals, such as the "orbital X-15," the delta wing was a real project and was the subject of a great deal of research and engineering. Despite endorsements from the Flight Research Center and John Becker at Langley, support remained lukewarm within the Air Force and NASA. The FRC was still evaluating the proposals for the deltawing study on 15 November 1967 when the crash of the X-15-3 effectively ended all thought of such a modification. (NASA)
North American was also somewhat uncertain about the leading-edge material, mainly because of the expected 2,200°F temperatures encountered on the design mission. North American built a segmented leading edge made from columbium alloy that successfully passed tests at 2,400°F. This appeared satisfactory, at least for initial use. The company expected that no available material would prove satisfactory for the lower surface of the wing, and that some form of thermal protection system would have to be developed. Unsurprisingly, many of the North American ideas looked similar to concepts the company was investigating for the space shuttle. One of the most promising ideas was to use metallic heat shields supported by standoff clips with a layer of low – density insulation sandwiched between the shield and the wing skin. Only an area about 2 feet wide just behind the leading edge needed this type of protection since the airflow further aft smoothed out sufficiently to keep temperatures within the ability of alloys such as TD nickel to
Г3101
Originally, North American had envisioned using upswept wing tips to replace the directional stability lost by the removal of the ventral rudder from the delta-wing configuration. Although the X-15 program seldom used the ventral rudder, this was because most missions flew at high angles of attack, where the lower rudder was detrimental to stability. The delta-wing program, on the other hand, wanted to fly sustained high-speed cruise missions that would require little high – angle-of-attack work. The initial round of tests in the North American hypersonic tunnel revealed that the upswept wing tips were inadequate above Mach 6. Researchers tested various configurations in both the North American hypersonic tunnel and the 20-inch Langley hypersonic tunnel until they found a set of tip fins that extended both above and below the wing centerline to be adequate. Nevertheless, engineers decided to make it easy to replace the fins just in case the wind-tunnel tests proved to be inaccurate.13111
The large-angle-of-attack capability of the basic X-15s was no longer required since researchers did not intend the mission to go to high altitudes. Given that the maximum angle of attack envisioned for the new airplane was less than 15 degrees, engineers decided to use a fixed-flow direction sensor to sense the angle of attack and sideslip. A hemispherical nose with five pressure taps could provide an air-data computer with sufficient information to derive the necessary angles without the complexity and weight of the ball nose. Conceptually, this was identical to the fixed alpha nose flown during six of the last X-15-1 flights.13121
North American proposed to stretch the fuselage 10 feet to 62.43 feet overall, and to manufacture what was essentially a new fuselage from the cockpit rearward. The company would stretch the propellant tank section 91 inches and provide new mounting provisions for the delta wing. North American manufactured test specimens from Rene 41 and Inconel 718 to determine which would be the best material for this area; these tests were in progress when NASA canceled the program. The space between the liquid-oxygen and ammonia tanks accommodated the standard center-of – gravity instrumentation compartment, and North American added a new 29-inch-long compartment behind the fuel tank but ahead of the engine to hold fuel and gases for the HRE. Designers also wanted to replace the existing ogive forward fuselage (in front of the canopy) with a 20-degree, included-angle-cone section. This semi-monocoque structure would use Rene 41 outer skin and Inconel X (or Inconel 718) frames, and titanium would be used for the inner skin of the equipment compartment.13131
North American investigated several different powerplants for the airplane, with the leading challenger being an Aerojet YLR91-AJ-15 from the second stage of a Titan II ICBM. This engine used unsymmetrical dimethylhydrazine and nitrogen tetroxide as propellants, and had already been man-rated for the NASA Gemini program. When equipped with a 25:1 nozzle, this engine completed the reference mission without the use of external propellant tanks. In fact, at a launch weight of 52,485 pounds and a burnout weight of 18,985 pounds, the YLR91 would have allowed a maximum velocity of 8,745 fps, well in excess of the 7,600 fps required by NASA. The effect of carrying the 1,000-pound HRE would have reduced this by about 400 fps.13141
North American briefly investigated the idea of using a separate "sustainer" engine to provide thrust to overcome drag during hypersonic cruise. Although the integration issues involved with incorporating a second engine and its propellants into the airframe eventually convinced all concerned that it would be too difficult, the particular engines investigated show how a program could come full circle. One of the engines investigated was the Bell YLR81-BA-11, a variation of the one of the engines proposed to power the X-15 in 1954. North American also investigated several variants of the Reaction Motors LR11 family that had been used for the initial X-15 flights,
along with the Aerojet LR52 (AJ-10).-1315
The engine that was ultimately selected was a modified XLR99 that provided 83,000 Ibf at 100,000 feet and was throttleable down to 8,000 lbf for sustained cruise. This was the version of the XLR99 that used a single thrust chamber and nozzle, not the Reaction Motors concept that used a second, remotely located alternate chamber. The increased internal fuel would permit sustained flights at Mach 6.5 using the low-thrust "sustainer" capability of the modified XLR99 to overcome drag but not produce any acceleration. The addition of a single centerline external tank would allow Mach 8 flights.-316
The main landing gear would be a version of the gear developed for the X-15A-2, appropriately strengthened for the almost 19,000-pound normal landing weight of the delta-wing design. As on the X-15-A-2, North American proposed to use both short and long versions of the rear shock struts; the long ones would provide clearance for the HRE under the ventral, while flights that did not carry the HRE would use the short ones. The nose gear would be moved to the instrument compartment behind the pilot, and the recorders and other research instrumentation normally carried there would be moved to a new compartment in front of the pilot where the original nose gear well was.-1317!
Although it was not part of the delta-wing baseline, North American was investigating the use of a fly-by-wire control system on the delta-wing X-15. Engineers believed that this would reduce the overall system size, weight, and volume, and provide better overall performance. This system would have used an analog flight-control system, not a digital one. The MH-96 adaptive control system was capable of accepting electrical inputs that were equivalent to flying in a fly-by-wire mode, and Honeywell designed the MH-96 to interface to the fly-by-wire flight-control system in the Dyna-Soar. In X-15-3 these were paralleled with mechanical linkages, and the delta wing could eliminate these mechanical linkages altogether. Given the facts that a fly-by-wire system had never flown, and the delta-wing airplane was flying in a new performance envelope anyway, NASA was not supportive of this effort.316
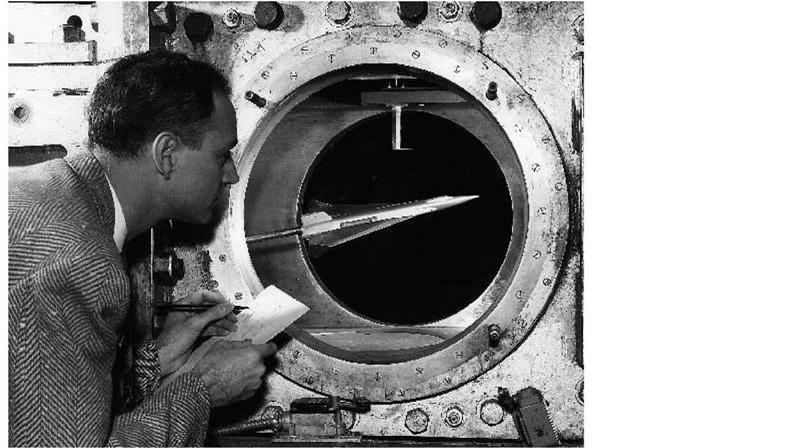
|
The final delta-wing design spent a considerable amount of time in this NASA Langley wind tunnel before the program was cancelled. (NASA)
Although the delta-wing airplane was generally described as a modification of X-15-3, about the only structure from the original airplane that would remain would be the cockpit and the aft thrust structure. Most of the electronics (i. e., the inertial system and MH-96) would also remain.
However, at least by weight, the majority of the aircraft would be new. Since the North American study had not been completed when X-15-3 was lost, the company had not estimated the final cost, but the amount would probably have been substantial.
Although no formal contracting arrangement existed, North American pressed on with a great deal of research into the delta-wing configuration. By March 1967, wind-tunnel models had accumulated over 300 hours of testing, with a 1/50-scale model used for high-speed tests and a 1/15-scale model used for low-speed tests. According to a North American news release, "the four year research program has also enabled North American to check out the integrity of components using new super alloys that will be required at hypersonic speeds. Tanks, wing sections, and other components have been fabricated of such materials and put through exhaustive thermal and structural tests."[319]
Despite endorsements from the FRC and John Becker at Langley, support remained lukewarm within the Air Force and NASA. The FRC was still evaluating the proposals for the delta-wing study on 15 November 1967 when the crash of the X-15-3 effectively ended all thought of such a modification. Since the general concept depended upon the use of the electronic systems that were unique to X-15-3, most researchers did not consider it readily possible to convert one of the other airframes; besides, the accident effectively sealed the fate of the entire X-15 program.-132^